La porosidad de los productos cerámicos depende de varios factores, como la porosidad inicial del compacto verde, la temperatura de sinterización, la duración del proceso de sinterización y la aplicación de presión durante la sinterización.Las cerámicas de óxido puro, en particular, requieren temperaturas más altas y tiempos de sinterización más largos debido a la difusión de partículas en estado sólido.Comprender estos factores es crucial para controlar la porosidad final de los productos cerámicos, que repercute directamente en sus propiedades mecánicas, térmicas y eléctricas.
Explicación de los puntos clave:
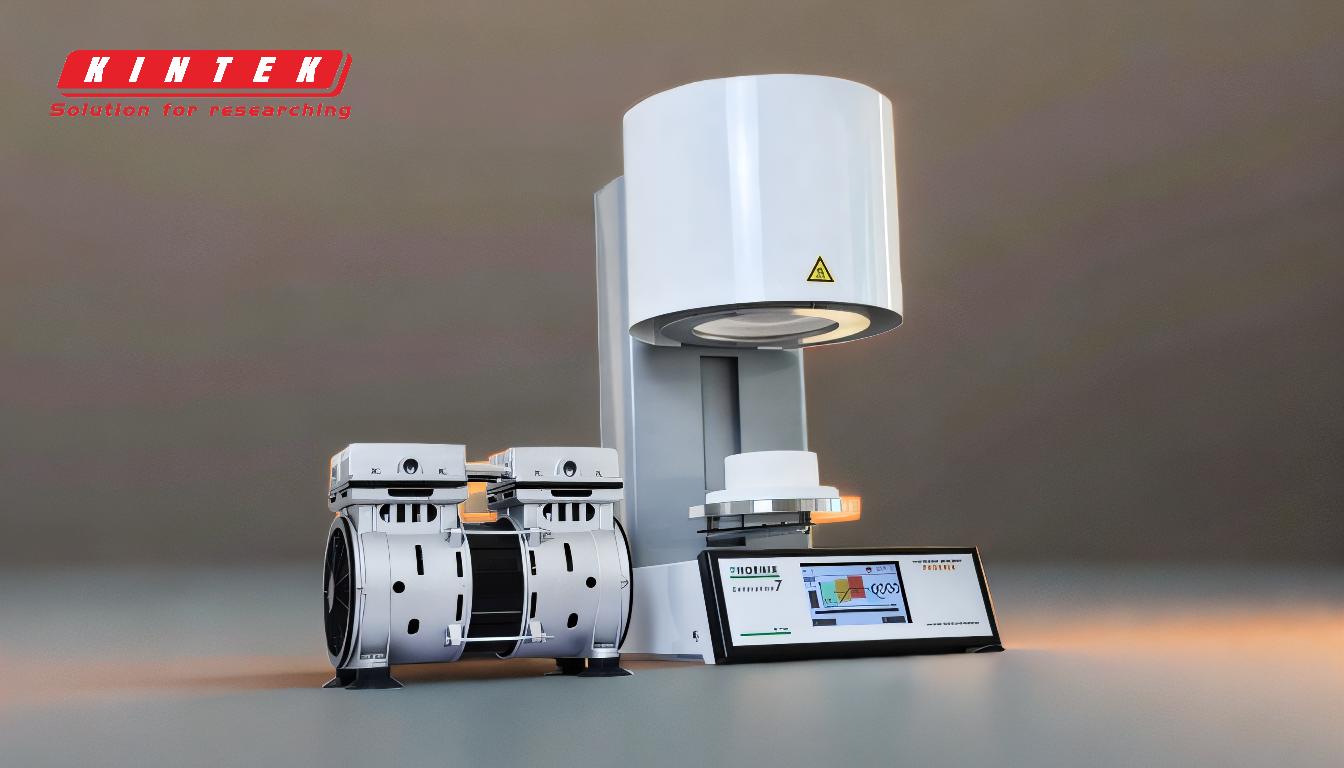
-
Porosidad inicial del Pacto Verde:
- El compacto verde se refiere al material cerámico antes de someterse a la sinterización.La porosidad inicial de este compacto desempeña un papel importante en la determinación de la porosidad final de la cerámica sinterizada.
- Una mayor porosidad inicial conduce generalmente a una mayor porosidad final, a menos que el proceso de sinterización la reduzca eficazmente.
- La densidad y la uniformidad del compacto verde son fundamentales.Un compacto verde más denso y con menos huecos dará como resultado una menor porosidad final tras la sinterización.
-
Temperatura de sinterización:
- La temperatura de sinterización es un factor crítico para reducir la porosidad.Las temperaturas más altas facilitan la difusión de las partículas, lo que da lugar a estructuras cerámicas más densas.
- En el caso de las cerámicas de óxido puro, se necesitan temperaturas de sinterización más elevadas porque la difusión de las partículas se produce en estado sólido, que es más lento en comparación con la sinterización en fase líquida.
- Sin embargo, las temperaturas excesivamente altas pueden provocar efectos indeseables como el crecimiento de grano, que podría afectar negativamente a las propiedades mecánicas de la cerámica.
-
Duración del proceso de sinterización:
- La duración del proceso de sinterización también afecta a la porosidad final.Los tiempos de sinterización más largos permiten una difusión y densificación más completas de las partículas.
- En el caso de las cerámicas de óxido puro, se requieren tiempos de sinterización más largos para lograr la reducción deseada de la porosidad debido a la difusión más lenta en estado sólido.
- Equilibrar el tiempo de sinterización con la temperatura es esencial para lograr una porosidad óptima sin provocar un crecimiento excesivo del grano u otros defectos.
-
Aplicación de presión:
- La aplicación de presión durante el proceso de sinterización puede reducir significativamente tanto el tiempo de sinterización como la porosidad final.Esta técnica se conoce como sinterización asistida por presión o prensado en caliente.
- La presión ayuda a cerrar los poros y favorece la reorganización de las partículas, lo que da lugar a una estructura cerámica más densa.
- Este método es especialmente útil para materiales difíciles de sinterizar en condiciones normales, como ciertas cerámicas de óxido puro.
-
Composición del material:
- El tipo de material cerámico también influye en la porosidad.Las cerámicas de óxido puro, por ejemplo, tienen un comportamiento de sinterización diferente al de las cerámicas compuestas.
- Pueden utilizarse aditivos o dopantes para modificar el comportamiento de sinterización y reducir la porosidad.Estos aditivos pueden reducir la temperatura de sinterización o mejorar las velocidades de difusión.
-
Tamaño y distribución de partículas:
- El tamaño y la distribución de las partículas cerámicas en el compacto verde afectan al proceso de sinterización y a la porosidad final.
- Las partículas más pequeñas tienen una mayor relación superficie/volumen, lo que favorece una sinterización y densificación más rápidas.
- Una distribución uniforme del tamaño de las partículas ayuda a conseguir una microestructura más homogénea con una porosidad controlada.
Controlando cuidadosamente estos factores, los fabricantes pueden adaptar la porosidad de los materiales cerámicos a los requisitos específicos de cada aplicación, ya sean componentes estructurales, aislantes térmicos o sustratos electrónicos.
Tabla resumen:
Factor | Impacto en la porosidad |
---|---|
Porosidad inicial del compacto verde | Una mayor porosidad inicial conduce a una mayor porosidad final a menos que la sinterización la reduzca. |
Temperatura de sinterización | Las temperaturas más altas reducen la porosidad, pero un calor excesivo puede provocar el crecimiento del grano. |
Duración de la sinterización | Los tiempos de sinterización más largos reducen la porosidad, especialmente en las cerámicas de óxido puro. |
Aplicación de presión | La sinterización asistida por presión reduce la porosidad y el tiempo de sinterización. |
Composición del material | Las cerámicas de óxido puro requieren temperaturas más elevadas y tiempos de sinterización más largos. |
Tamaño y distribución de partículas | Las partículas más pequeñas y uniformes favorecen una sinterización más rápida y una porosidad controlada. |
¿Necesita ayuda para optimizar la porosidad cerámica de su proyecto? Póngase en contacto con nuestros expertos hoy mismo ¡!