El diseño del inductor en el calentamiento por inducción es un proceso crítico que influye directamente en la eficiencia, eficacia y practicidad del sistema de calentamiento.Un inductor bien diseñado garantiza patrones de calentamiento óptimos, maximiza la eficiencia energética y se adapta a los requisitos de la pieza de trabajo.Los factores clave que hay que tener en cuenta son la selección de la banda de frecuencia, las propiedades del material de la pieza de trabajo, la geometría del inductor, los mecanismos de refrigeración y la compatibilidad de la fuente de alimentación.Cada uno de estos factores debe evaluarse cuidadosamente para lograr el efecto de calentamiento deseado, equilibrando al mismo tiempo el coste y la eficacia operativa.
Explicación de los puntos clave:
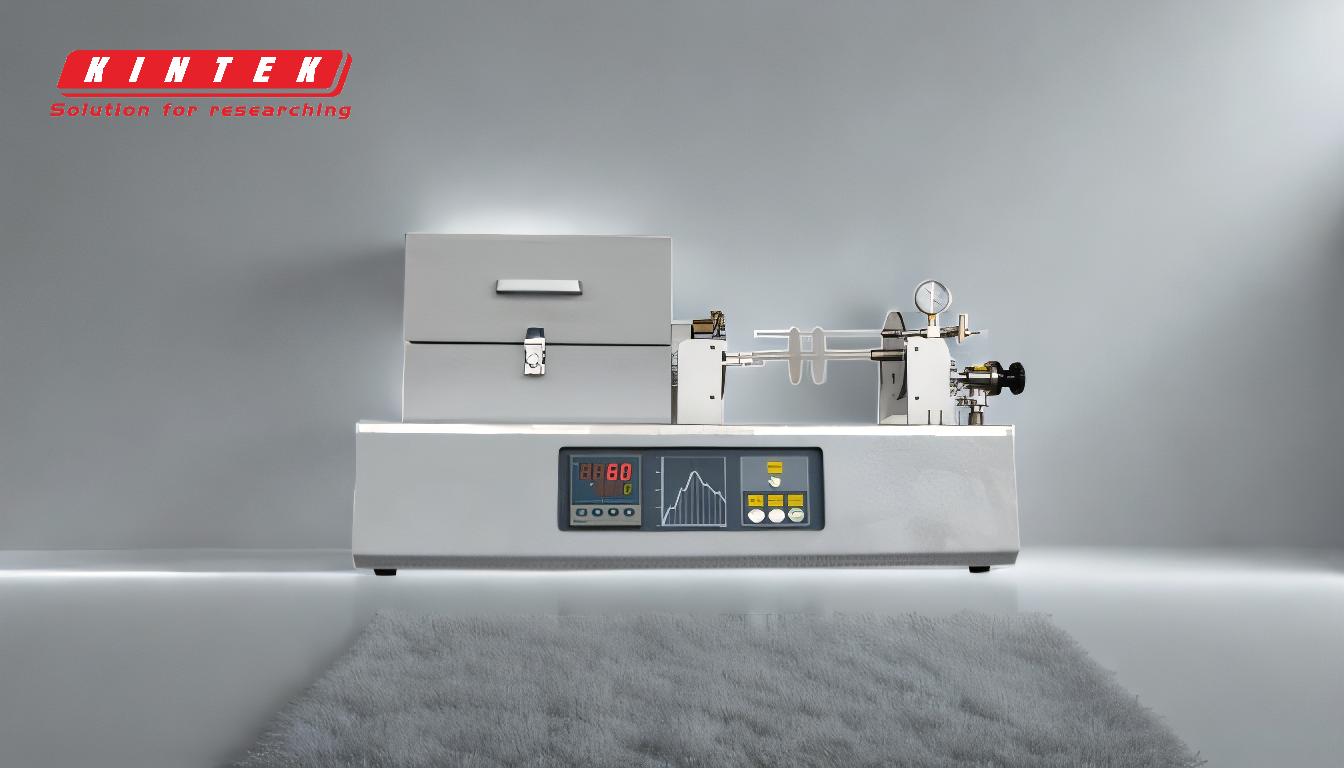
-
Selección de la banda de frecuencia
- La frecuencia de la corriente alterna utilizada en el calentamiento por inducción influye significativamente en el patrón y la profundidad del calentamiento.
- Las frecuencias más bajas (por ejemplo, de 50 Hz a 10 kHz) son adecuadas para una penetración más profunda en piezas más grandes, mientras que las frecuencias más altas (por ejemplo, de 10 kHz a 1 MHz) son ideales para el calentamiento superficial o de componentes más pequeños.
- La elección de la frecuencia debe alinearse con el material de la pieza de trabajo, el tamaño y el efecto de calentamiento deseado, teniendo en cuenta también el coste y la disponibilidad del equipo.
-
Propiedades del material de la pieza
- La conductividad eléctrica y la permeabilidad magnética del material de la pieza determinan la eficacia de su calentamiento.
- Los materiales con alta conductividad eléctrica (por ejemplo, cobre, aluminio) y permeabilidad magnética (por ejemplo, hierro, acero) responden mejor al calentamiento por inducción.
- Los materiales no conductores o poco conductores pueden requerir técnicas o revestimientos especiales para permitir un calentamiento eficaz.
-
Geometría y diseño del inductor
- La forma y el tamaño de la bobina inductora deben coincidir con la geometría de la pieza para garantizar un calentamiento uniforme.
- Entre los diseños de inductores más comunes se encuentran las bobinas helicoidales, las bobinas de panqueque y las bobinas de canal, cada una de ellas adecuada para aplicaciones específicas.
- El número de espiras, la separación entre espiras y el diámetro de la bobina influyen en la distribución del campo magnético y en la eficacia del calentamiento.
-
Mecanismos de refrigeración
- Las bobinas de inducción generan calor durante su funcionamiento y requieren una refrigeración eficaz para evitar el sobrecalentamiento y mantener el rendimiento.
- La refrigeración por agua es el método más común, con refrigerante que fluye a través de canales en el inductor o alrededor de la bobina.
- Un diseño de refrigeración adecuado garantiza la longevidad y el funcionamiento constante del inductor.
-
Compatibilidad de la fuente de alimentación
- El inductor debe ser compatible con la fuente de alimentación del calentamiento por inducción en términos de tensión, corriente y frecuencia.
- La adaptación de impedancias entre el inductor y la fuente de alimentación es esencial para maximizar la transferencia de energía y minimizar las pérdidas.
- Es posible que se necesiten inductores a medida para aplicaciones especializadas con el fin de lograr un rendimiento óptimo.
-
Consideraciones operativas
- El diseño del inductor debe facilitar la carga y descarga de la pieza para agilizar el proceso de calentamiento.
- Deben tenerse en cuenta los requisitos de durabilidad y mantenimiento para minimizar el tiempo de inactividad y los costes operativos.
- Las características de seguridad, como el aislamiento y el blindaje, protegen a los operarios y al equipo de los riesgos eléctricos y térmicos.
Al tener en cuenta estos factores, un inductor bien diseñado puede mejorar significativamente el rendimiento y la eficacia de un sistema de calentamiento por inducción, garantizando un funcionamiento fiable y rentable.
Tabla resumen:
Factor | Consideraciones clave |
---|---|
Selección de la banda de frecuencia | - Frecuencias más bajas para penetración profunda; frecuencias más altas para calentamiento superficial. |
Material de la pieza | - Los materiales de alta conductividad y permeabilidad (por ejemplo, acero, cobre) se calientan eficazmente. |
Geometría del inductor | - Adapte la forma de la bobina a la pieza de trabajo; diseños helicoidales, de panqueque o de canal. |
Mecanismos de refrigeración | - La refrigeración por agua es habitual; garantiza la longevidad y un rendimiento constante. |
Compatibilidad de las fuentes de alimentación | - La adaptación de impedancias es fundamental para la eficiencia energética. |
Consideraciones operativas | - Garantice la facilidad de carga y descarga, la durabilidad y las características de seguridad. |
¿Está listo para optimizar su sistema de calentamiento por inducción? Póngase en contacto con nuestros expertos para obtener soluciones de diseño de inductores a medida.