La soldadura por inducción, aunque eficaz y precisa, tiene varias limitaciones que pueden afectar a su eficacia en determinadas aplicaciones.Estas limitaciones incluyen la necesidad de materiales limpios y sin óxido, la posible pérdida de elementos de aleación debido a la oxidación y las dificultades con materiales como el aluminio, que forman capas de óxido estables.Además, el control preciso de la temperatura y la distribución térmica homogénea son fundamentales, especialmente cuando se trabaja con materiales que tienen rangos de fusión muy parecidos.Comprender estas limitaciones es esencial para seleccionar el método de soldadura fuerte adecuado y garantizar unos resultados de alta calidad.
Explicación de los puntos clave:
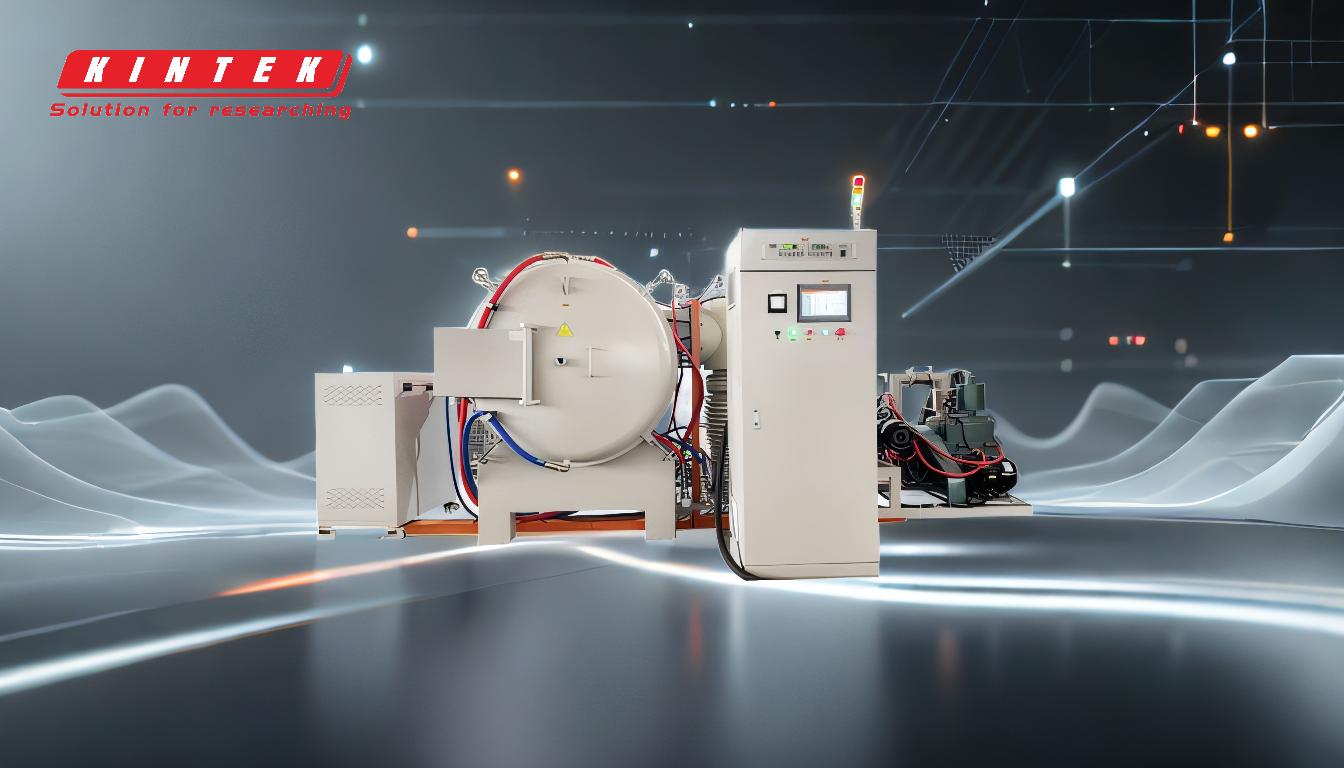
-
Falta de capacidad de refinado:
- La soldadura por inducción requiere que los materiales de carga estén libres de óxidos y tengan una composición conocida.Esto significa que cualquier impureza u óxido presente en los materiales puede afectar negativamente al proceso de soldadura fuerte.
- El proceso no tiene la capacidad de refinar o purificar los materiales durante la soldadura fuerte, lo que puede ser un inconveniente importante cuando se trabaja con materiales propensos a la oxidación o la contaminación.
-
Oxidación y pérdida de elementos de aleación:
- Durante el proceso de soldadura por inducción, algunos elementos de aleación pueden perderse debido a la oxidación.Esto hace necesario volver a añadir estos elementos a la masa fundida para conseguir la composición deseada.
- La pérdida de elementos de aleación puede dar lugar a incoherencias en el producto final, lo que requiere una cuidadosa supervisión y ajuste durante el proceso de soldadura fuerte.
-
Desafíos con el aluminio y otros materiales oxidables:
- El aluminio, en particular, es muy oxidable y forma una capa estable de óxido de aluminio (Al2O3) que puede impedir que los metales de aportación humedezcan la superficie.Esta capa de óxido debe suprimirse antes de la soldadura fuerte e impedir que vuelva a formarse hasta que se solidifique el metal de aportación.
- La necesidad de gestionar esta capa de óxido añade complejidad al proceso de soldadura fuerte, lo que requiere pasos y precauciones adicionales para garantizar una unión satisfactoria.
-
Control preciso de la temperatura y distribución térmica homogénea:
- La soldadura por inducción requiere un control preciso de la temperatura, especialmente cuando los intervalos de fusión de los metales base y de aportación están muy próximos.Cualquier desviación de la temperatura puede provocar una soldadura incompleta o dañar los materiales.
- Conseguir una distribución térmica homogénea también es fundamental para garantizar que toda la unión alcance la temperatura necesaria de manera uniforme.Un calentamiento incoherente puede dar lugar a uniones débiles o a un sobrecalentamiento localizado, lo que puede comprometer la integridad del conjunto soldado.
-
Compatibilidad de materiales:
- No todos los materiales son adecuados para la soldadura fuerte por inducción.Los materiales muy reactivos o de composición compleja pueden requerir métodos de soldadura alternativos para obtener los resultados deseados.
- La compatibilidad de los metales base y de aportación debe considerarse cuidadosamente para garantizar que puedan formar una unión fuerte y duradera sin reacciones adversas.
-
Complejidad del equipo y del proceso:
- Los equipos de soldadura por inducción pueden ser complejos y caros, y requieren operarios cualificados para gestionar el proceso con eficacia.
- El proceso en sí puede ser más complejo que otros métodos de soldadura fuerte, lo que exige un conocimiento profundo de los materiales, equipos y técnicas implicados.
En resumen, aunque la soldadura por inducción ofrece muchas ventajas, como un calentamiento rápido y un control preciso, también tiene varias limitaciones que deben controlarse cuidadosamente.Entre ellas, la necesidad de materiales limpios y sin óxido, la posible pérdida de elementos de aleación, los problemas con materiales oxidables como el aluminio y el requisito de un control preciso de la temperatura y una distribución térmica homogénea.Comprender estas limitaciones es crucial para seleccionar el método de soldadura fuerte adecuado y garantizar resultados de alta calidad.
Cuadro sinóptico:
Limitación | Principales retos |
---|---|
Falta de capacidad de refinado | Requiere materiales limpios y sin óxido; no hay refinado durante la soldadura fuerte. |
Oxidación y pérdida de elementos de aleación | Los elementos de aleación pueden oxidarse, lo que requiere una nueva adición y un control cuidadoso. |
Desafíos del aluminio | La capa de óxido de aluminio debe suprimirse y controlarse para que la soldadura fuerte tenga éxito. |
Control preciso de la temperatura | Crítico para materiales con rangos de fusión muy próximos. |
Compatibilidad de materiales | No todos los materiales son adecuados; los metales base y de aportación deben ser compatibles. |
Complejidad del equipo y del proceso | Requiere operarios cualificados y equipos complejos y caros. |
¿Necesita ayuda para superar los retos de la soldadura por inducción? Póngase en contacto con nuestros expertos para obtener soluciones a medida.