La porosidad en la soldadura fuerte es un defecto común que puede debilitar significativamente la unión y comprometer su integridad. Se produce cuando queda atrapado gas o aire dentro de la unión soldada, formando huecos o burbujas. Las causas de la porosidad son múltiples y pueden atribuirse a factores como una preparación incorrecta de la superficie, una limpieza inadecuada, un flujo deficiente del material de aportación, una velocidad de calentamiento incorrecta y un tiempo o temperatura de permanencia insuficientes. Comprender estas causas es esencial para optimizar el proceso de soldadura fuerte y garantizar uniones duraderas y de alta calidad.
Explicación de los puntos clave:
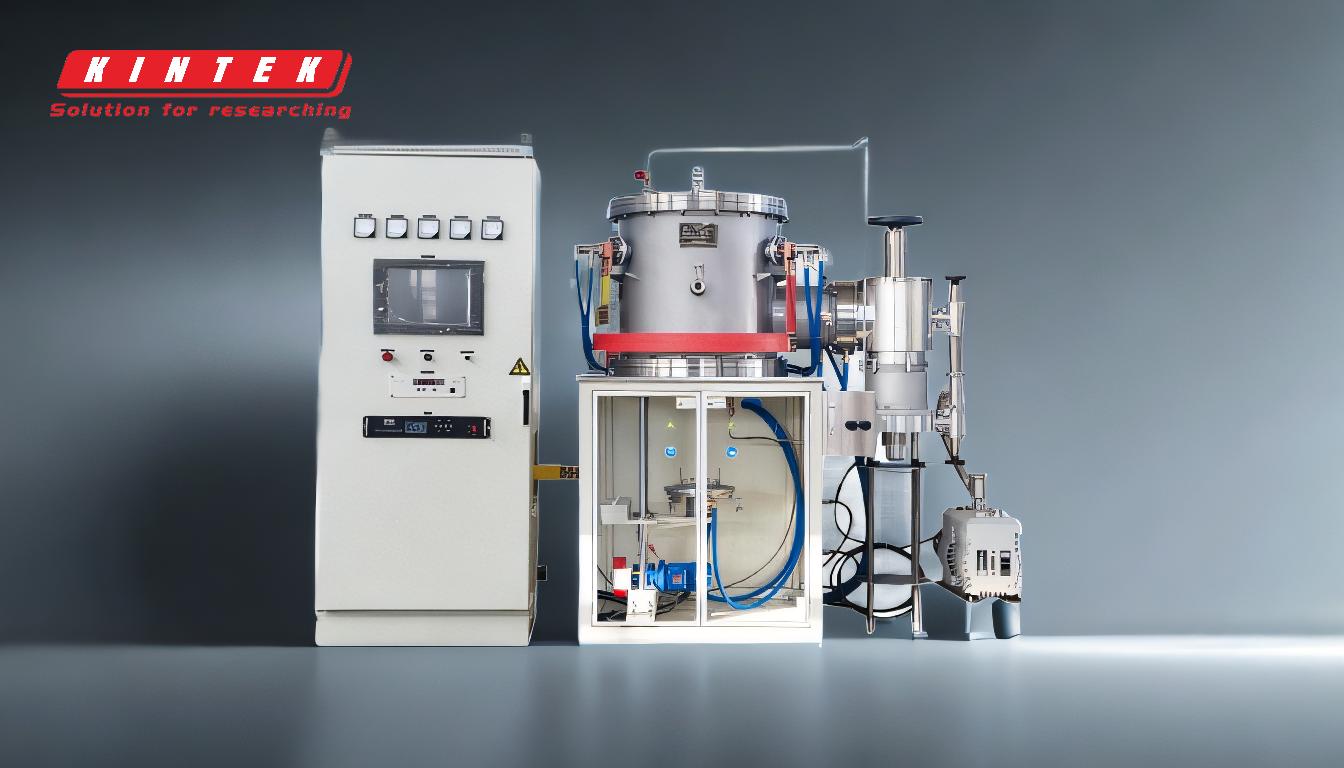
-
Preparación inadecuada de la superficie:
- La preparación de la superficie es fundamental para conseguir uniones fuertes. Si las superficies que se van a unir no son planas, lisas o están libres de contaminantes, la acción capilar y el flujo del material de aportación pueden verse obstaculizados. Esto puede provocar una humectación incompleta y la formación de huecos.
- Las películas de óxido, aceite, grasa u otros residuos en la superficie pueden impedir una adhesión adecuada, atrapando gases y provocando porosidad.
- Solución : Antes de proceder a la soldadura fuerte, limpie y prepare la superficie a fondo, eliminando las capas de óxido y los contaminantes.
-
Limpieza inadecuada:
- La eficacia de la limpieza depende del material, las condiciones atmosféricas y la manipulación. Si el material no se limpia correctamente o queda expuesto a contaminantes después de la limpieza, puede producirse porosidad.
- Solución : Limpiar los materiales inmediatamente antes de la soldadura fuerte y minimizar la manipulación para evitar la recontaminación.
-
Flujo deficiente del material de relleno:
- El material de relleno debe fluir uniforme y completamente en la junta para formar una unión fuerte. Si el material de relleno no humedece bien las superficies o si hay huecos en la junta, puede quedar atrapado gas, lo que provocaría porosidad.
- Solución : Optimizar los parámetros de soldadura fuerte, como la temperatura, el tiempo de permanencia y la velocidad de calentamiento, para garantizar un flujo adecuado del material de aportación.
-
Velocidad de calentamiento incorrecta:
- Un calentamiento demasiado rápido o irregular puede provocar un sobrecalentamiento localizado o un calentamiento insuficiente, lo que provocaría una fusión incompleta del material de relleno o gases atrapados.
- Solución : Controle la velocidad de calentamiento para garantizar una distribución uniforme de la temperatura y una fusión adecuada del material de relleno.
-
Tiempo de permanencia o temperatura insuficientes:
- La temperatura y el tiempo de permanencia son fundamentales para conseguir una soldadura fuerte completa. Si la temperatura es demasiado baja o el tiempo de permanencia demasiado corto, es posible que el material de aportación no se funda o fluya completamente, lo que produciría huecos.
- Solución : Siga las directrices de temperatura y tiempo de permanencia recomendadas para los materiales específicos y la aleación de relleno que se está utilizando.
-
Nivel de vacío y atmósfera:
- En la soldadura fuerte al vacío, el nivel de vacío debe ser suficiente para eliminar los gases de la zona de unión. Si el nivel de vacío es demasiado bajo, los gases residuales pueden causar porosidad.
- Solución : Asegúrese de que el nivel de vacío es adecuado para los materiales y el proceso de soldadura fuerte que se está utilizando.
-
Factores específicos del material:
- El tipo de metal base y de aleación de relleno puede influir en la porosidad. Por ejemplo, las aleaciones de aluminio son propensas a la formación de óxido, que puede atrapar gases si no se elimina adecuadamente.
- Solución : Seleccione materiales compatibles y utilice técnicas de limpieza y soldadura adecuadas para la aleación específica.
-
Diseño y geometría de las juntas:
- La forma y el tamaño de las piezas que se unen pueden afectar al flujo del material de relleno y al atrapamiento de gas. Las geometrías complejas o los huecos estrechos pueden aumentar el riesgo de porosidad.
- Solución : Diseñe las juntas con el espacio libre y la accesibilidad adecuados para el flujo del material de relleno.
-
Tasa de enfriamiento:
- Un enfriamiento rápido puede atrapar gases dentro de la junta, mientras que un enfriamiento lento permite que los gases escapen. Un ritmo de enfriamiento inadecuado puede contribuir a la porosidad.
- Solución : Controle la velocidad de enfriamiento para permitir la salida de gases sin comprometer la resistencia de la junta.
Si se tienen en cuenta estos factores y se optimiza el proceso de soldadura fuerte, se puede minimizar la porosidad, lo que da lugar a uniones más fuertes y fiables.
Cuadro recapitulativo:
Causa de la porosidad | Solución |
---|---|
Preparación inadecuada de la superficie | Limpiar y preparar a fondo las superficies, eliminando óxidos y contaminantes. |
Limpieza inadecuada | Limpiar los materiales inmediatamente antes de la soldadura fuerte y minimizar la manipulación. |
Flujo deficiente del material de relleno | Optimizar los parámetros de soldadura fuerte (temperatura, tiempo de permanencia, velocidad de calentamiento). |
Velocidad de calentamiento incorrecta | Control de la velocidad de calentamiento para una distribución uniforme de la temperatura. |
Tiempo de permanencia/Temperatura insuficiente | Siga las directrices recomendadas de temperatura y tiempo de permanencia. |
Nivel de vacío y atmósfera | Garantizar un nivel de vacío adecuado para los materiales y el proceso. |
Factores específicos del material | Seleccione materiales compatibles y utilice técnicas de limpieza/soldadura adecuadas. |
Diseño y geometría de juntas | Diseñe las juntas con el espacio libre y la accesibilidad adecuados para el flujo de relleno. |
Tasa de enfriamiento | Controlar la velocidad de enfriamiento para permitir la salida de gases sin debilitar la junta. |
¿Necesita ayuda para minimizar la porosidad en su proceso de soldadura fuerte? Contacte hoy mismo con nuestros expertos soluciones a medida