La sinterización es un proceso de fabricación que consiste en compactar y formar una masa sólida de material aplicando calor y presión sin alcanzar el punto de fusión del material.Este proceso es crucial en industrias como la metalurgia, la cerámica y la pulvimetalurgia, donde transforma materiales en polvo en componentes densos y resistentes.El proceso de sinterización se desarrolla normalmente en tres etapas: conformación de la mezcla de polvos, eliminación del agente aglutinante y fusión de las partículas a altas temperaturas.Las técnicas avanzadas de sinterización, como la sinterización en vacío o la sinterización en prensa caliente, mejoran aún más la calidad y el rendimiento del producto final al evitar la oxidación y la contaminación.El proceso se utiliza ampliamente en aplicaciones que van desde la producción de acero hasta la creación de cerámicas avanzadas.
Explicación de los puntos clave:
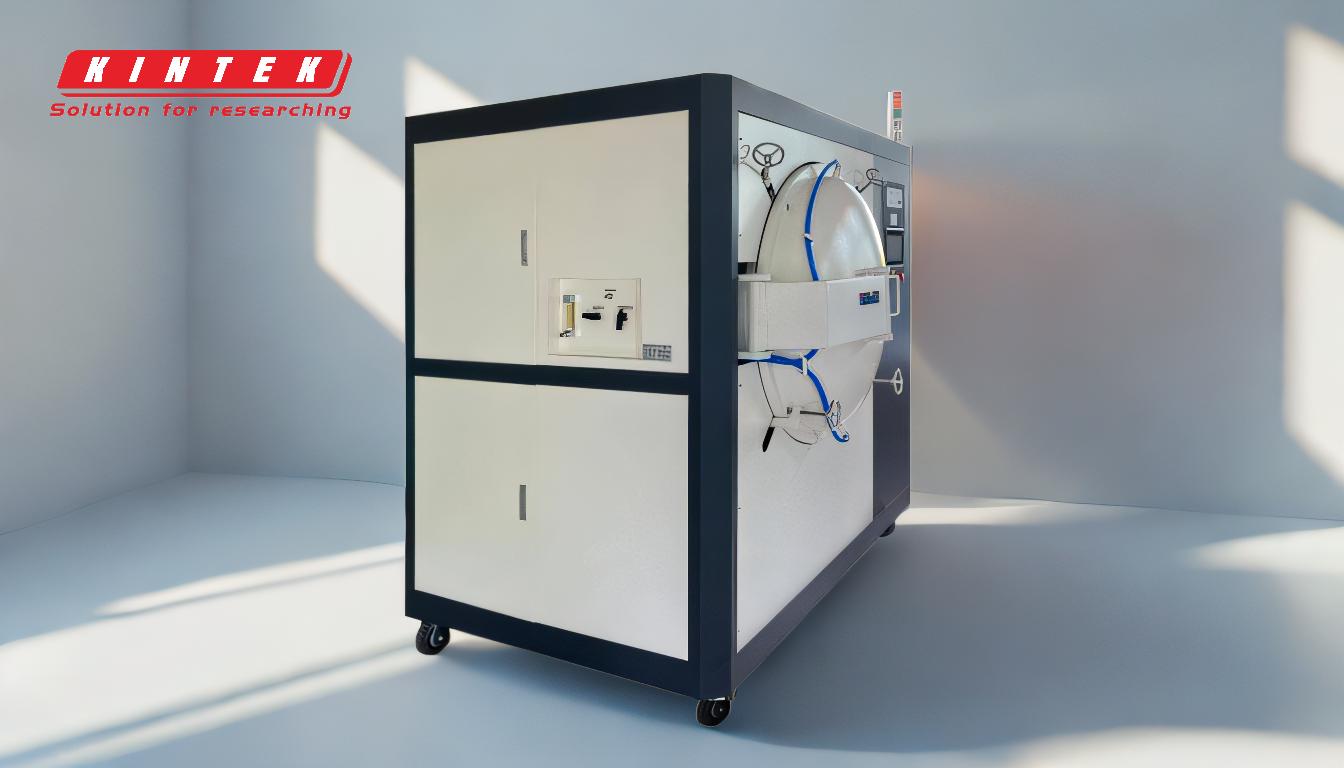
-
Definición y finalidad de la sinterización:
- La sinterización es un proceso que utiliza calor y presión para compactar materiales en polvo y convertirlos en una masa sólida sin fundirlos.Esto reduce la porosidad y aumenta la resistencia y densidad del material.
- Se utiliza ampliamente en industrias como la metalurgia, la cerámica y la pulvimetalurgia para crear componentes con formas y propiedades precisas.
-
Etapas del proceso de sinterización:
-
Etapa 1: Dar forma a la mezcla de polvos:
- Se mezcla una mezcla primaria de polvo con un agente aglutinante (por ejemplo, agua, cera o polímero) y se le da la forma deseada.
- El agente aglutinante mantiene unidas las partículas de polvo durante las etapas iniciales.
-
Etapa 2: Eliminación del agente adhesivo:
- La "pieza verde" moldeada se calienta, lo que hace que el agente adhesivo se evapore o se queme.
- Este paso prepara el material para la fusión de partículas.
-
Etapa 3: Fusión de partículas:
- La temperatura aumenta hasta un punto en el que las partículas primarias comienzan a fundirse en sus superficies, fusionándose.
- En algunos casos, un agente de unión intermedio (por ejemplo, bronce) funde y une las partículas sin alterar el material primario.
-
Etapa 1: Dar forma a la mezcla de polvos:
-
Tipos de hornos de sinterización:
-
Horno de sinterización al vacío:
- Este horno crea un entorno de vacío para evitar la oxidación y la contaminación, mejorando la calidad del producto sinterizado.
- El proceso consiste en cargar el material, evacuar el aire, calentar y enfriar en condiciones controladas.Más información sobre horno de sinterización .
-
Horno de sinterización con prensa caliente:
- Combina alta temperatura y presión en un entorno de vacío para fundir polvos cerámicos en materiales sólidos.
- El horno incluye un cuerpo, un calentador, un sistema de presión y un sistema de vacío para un control preciso.
-
Horno de sinterización al vacío:
-
Aplicaciones de la sinterización:
-
Producción de acero:
- La sinterización se utiliza para crear terrones de hierro a partir de mineral de hierro en polvo y coque, que luego se procesan en altos hornos para producir acero.
-
Cerámica y materiales avanzados:
- La sinterización es esencial para crear cerámicas de alto rendimiento y componentes con formas complejas.
-
Producción de acero:
-
El papel del agua en la sinterización:
- El agua enfría la pieza sinterizada después del tratamiento en estado líquido.
- Como vapor, se combina con los agentes de prensado y aceites evaporados para formar subproductos inocuos como CO o CO2, evitando la liberación de hidrocarburos nocivos.
-
Fase de acabado:
- Tras la sinterización, las piezas pueden someterse a tratamientos adicionales, como la calibración, para cumplir especificaciones precisas.
- El calibrado consiste en ajustar la pieza mediante una matriz de calibrado para garantizar que cumple las tolerancias y normas de calidad requeridas.
-
Ventajas de la sinterización:
- Produce componentes de gran resistencia, densidad y precisión.
- Reduce el desperdicio de material y el consumo de energía en comparación con los procesos de fusión tradicionales.
- Permite la creación de formas complejas y materiales avanzados.
Al comprender estos puntos clave, los compradores de equipos y consumibles pueden tomar decisiones informadas sobre los procesos de sinterización y los hornos o materiales adecuados que requieren sus aplicaciones específicas.
Tabla resumen:
Aspecto clave | Detalles |
---|---|
Definición | Proceso de compactación de materiales en polvo mediante calor y presión. |
Propósito | Reduce la porosidad, aumenta la resistencia y crea formas precisas. |
Etapas |
1.Dar forma a la mezcla de polvos
2.Eliminación del agente adhesivo 3.Fusión de partículas |
Tipos de hornos de sinterización |
- Horno de sinterización en vacío
- Horno de sinterización de prensa caliente |
Aplicaciones | Producción de acero, cerámica y materiales avanzados. |
Ventajas | Alta resistencia, reducción de residuos y capacidad para crear formas complejas. |
Descubra cómo el sinterizado puede beneficiar a su industria póngase en contacto con nuestros expertos para obtener soluciones a medida.