Para conseguir un buen proceso de soldadura fuerte, hay que tener en cuenta varios factores críticos, como la elección del método de calentamiento, el control de la temperatura, la limpieza del metal base, el diseño de la unión y las propiedades del metal de aportación.La transferencia eficaz del calor, la aleación adecuada y la acción humectante son esenciales para garantizar unas uniones fuertes y duraderas.Además, la geometría de la unión, la limpieza de las superficies y el procesamiento mecánico preciso desempeñan un papel importante en la obtención de resultados de alta calidad.A continuación, desglosamos estas consideraciones en puntos clave prácticos.
Explicación de los puntos clave:
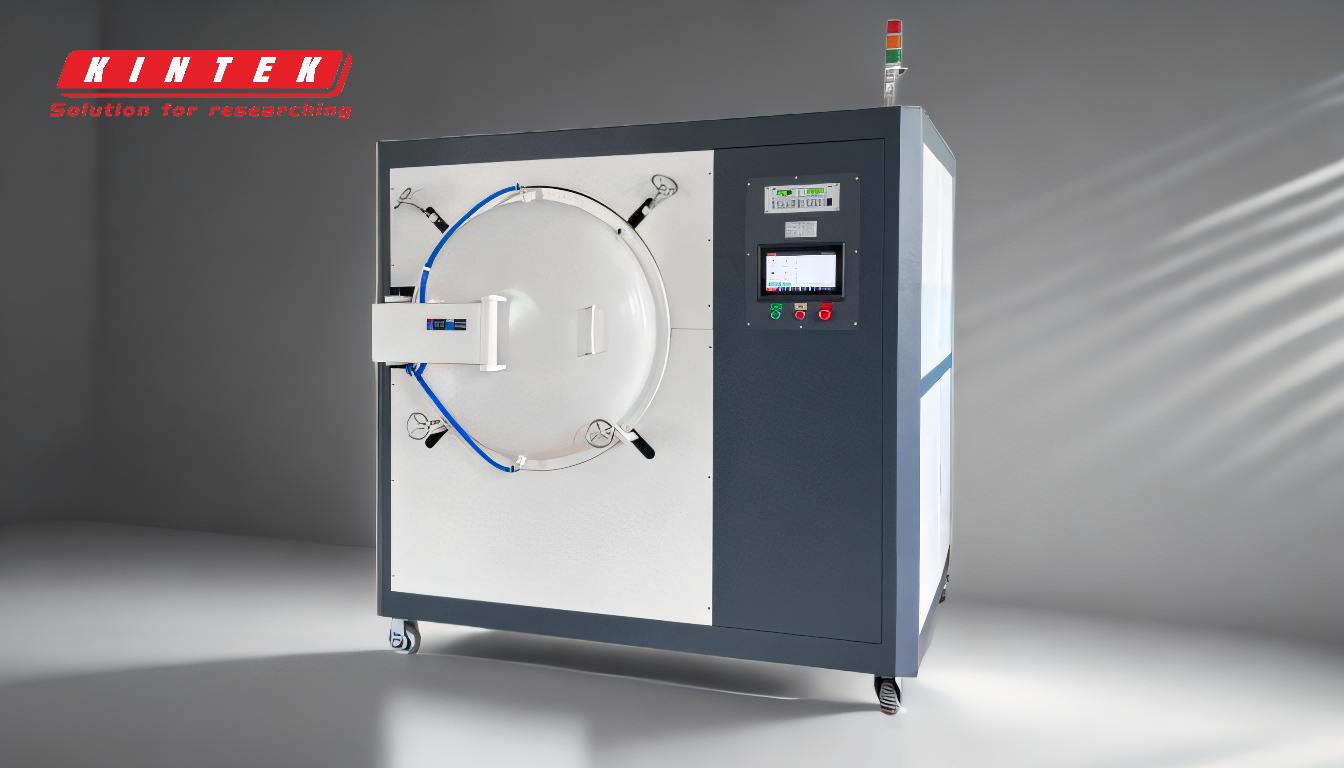
-
Selección del método de calentamiento
- El método de calentamiento debe garantizar una transferencia de calor eficaz por toda la junta para conseguir un calentamiento y enfriamiento uniformes.
- Debe mantenerse dentro de la capacidad térmica de los metales base para evitar distorsiones o daños.
- La geometría de la unión soldada influye en la elección del método de calentamiento, ya que las formas complejas pueden requerir técnicas de calentamiento localizadas o especializadas.
- La velocidad de producción y los requisitos de volumen también determinan el método de calentamiento, y los procesos de gran volumen suelen favorecer los sistemas de calentamiento automatizados o continuos.
-
Control de la temperatura y el tiempo
- La temperatura de soldadura fuerte debe superar el punto de fusión del metal de aportación para garantizar una aleación y una acción humectante adecuadas.
- Un calentamiento excesivo puede dañar los metales base, mientras que un calor insuficiente puede provocar una unión incompleta.
- El tiempo de permanencia a la temperatura de soldadura fuerte debe controlarse cuidadosamente para permitir una humectación y extensión adecuadas del metal de aportación sin una difusión excesiva en los metales base.
-
Limpieza del metal base
- Las superficies de las juntas deben estar libres de contaminantes como aceites, grasas, óxidos o suciedad para asegurar una correcta humectación y adherencia.
- En función de los metales base y los contaminantes, puede ser necesario utilizar métodos de limpieza como el desengrasado, el decapado o la limpieza abrasiva.
- Mantener la limpieza durante el proceso de soldadura fuerte es igualmente importante para evitar la recontaminación.
-
Diseño de la unión y dimensiones de la separación
- El diseño de la junta debe permitir una acción capilar adecuada, que es fundamental para que el metal de aportación fluya y rellene la cavidad de la junta.
- Se requiere un procesamiento mecánico preciso para lograr las dimensiones correctas de la separación, ya que las separaciones demasiado anchas o demasiado estrechas pueden comprometer la resistencia de la unión.
- El diseño también debe tener en cuenta la dilatación y contracción térmicas para minimizar la tensión durante el calentamiento y el enfriamiento.
-
Propiedades del metal de aportación
- El metal de aportación debe tener una temperatura de fusión significativamente inferior a la de los metales base para evitar dañarlos durante la soldadura fuerte.
- Debe presentar buenas características de humectabilidad, extensión y adherencia para formar una unión resistente.
- Las propiedades mecánicas del metal de aportación, como la solidez y la resistencia a la corrosión, deben ajustarse a los requisitos de la aplicación.
-
Consideraciones sobre la producción
- El ritmo y el volumen de producción influyen en la elección del equipo de soldadura fuerte y los parámetros del proceso.
- La producción de gran volumen puede requerir sistemas automatizados para obtener una calidad y eficacia constantes.
- Las aplicaciones de bajo volumen o personalizadas pueden beneficiarse de procesos manuales o semiautomatizados para una mayor flexibilidad.
Si aborda estos factores sistemáticamente, podrá garantizar un proceso de soldadura fuerte y fiable que produzca uniones de alta calidad adaptadas a su aplicación específica.
Tabla resumen:
Factor clave | Consideraciones clave |
---|---|
Selección del método de calentamiento | - Transferencia de calor eficiente, calentamiento y enfriamiento uniformes |
- Evitar distorsiones o daños en los metales base | |
- Tenga en cuenta la geometría de la unión y el volumen de producción | |
Control de temperatura y tiempo | - Superar el punto de fusión del metal de aportación, evitar el sobrecalentamiento o el calor insuficiente |
- Controlar el tiempo para una correcta humectación y extensión | |
Limpieza del metal base | - Eliminar contaminantes (aceites, óxidos, suciedad) |
- Utilizar desengrase, decapado o limpieza abrasiva | |
Diseño de la junta y dimensiones de la separación | - Garantizar una acción capilar adecuada para el flujo del metal de aportación |
- Dimensiones precisas de los huecos y consideraciones de expansión térmica | |
Propiedades del metal de aportación | - Temperatura de fusión inferior a la de los metales comunes |
- Buenas características de humectabilidad, extensión y adherencia | |
Consideraciones sobre la producción | - Adaptar el equipo y el proceso a la velocidad y el volumen de producción |
Optimice su proceso de soldadura para obtener resultados de alta calidad. póngase en contacto con nuestros expertos para obtener soluciones a medida.