El sputtering, una técnica moderna de deposición en vacío, ofrece varias ventajas sobre métodos más antiguos como la evaporación térmica o la evaporación por haz de electrones.Entre las principales ventajas se encuentran la capacidad de depositar una amplia gama de materiales (incluidos los que tienen puntos de fusión elevados), el control preciso de la composición y las propiedades de la película, una mejor adherencia gracias a la mayor energía cinética de los átomos pulverizados y la compatibilidad con gases reactivos para procesos avanzados.Además, el sputtering es más reproducible, fácil de automatizar y adecuado para aplicaciones de vacío ultraalto.También permite una precisión a nivel molecular, posibilitando la creación de interfaces prístinas y películas uniformes con altas densidades de empaquetamiento, incluso a bajas temperaturas.
Explicación de los puntos clave:
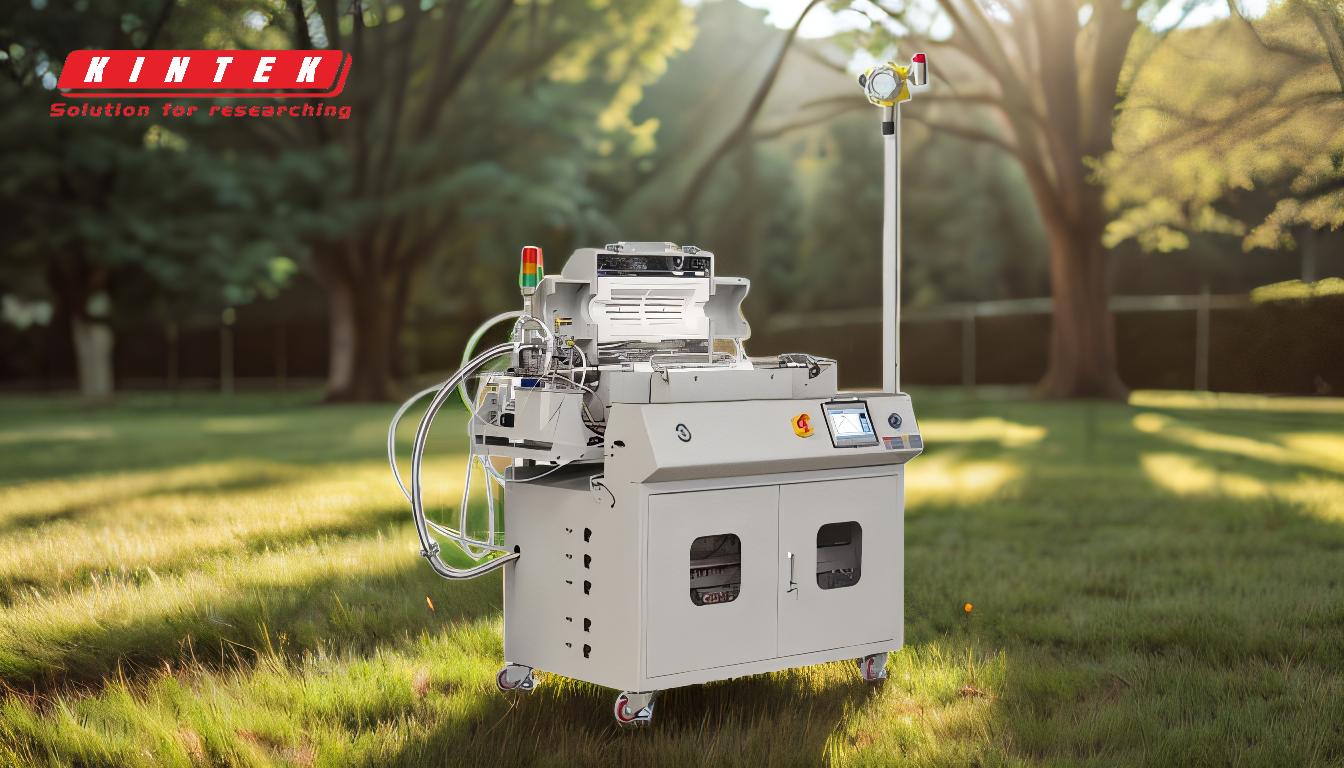
-
Deposición de una amplia gama de materiales:
- El sputtering puede depositar materiales con puntos de fusión muy altos, que son difíciles o imposibles de evaporar utilizando métodos más antiguos como la evaporación térmica.
- Funciona bien con diversos materiales, como metales, aleaciones, compuestos, plásticos, orgánicos y vidrio, por lo que es más versátil que las técnicas tradicionales de deposición en vacío.
-
Mejor adherencia y calidad de la película:
- Los átomos expulsados por pulverización catódica tienen una energía cinética significativamente superior a la de los materiales evaporados, lo que se traduce en una mejor adhesión a los sustratos.
- Las películas producidas por pulverización catódica son más uniformes, tienen mayores densidades de empaquetamiento y presentan una mejor adherencia a la superficie, incluso a bajas temperaturas.
-
Precisión y control:
- La pulverización catódica ofrece precisión a nivel molecular, lo que permite la creación de interfaces prístinas entre materiales.
- Las propiedades de la película pueden ajustarse con precisión controlando los parámetros del proceso, como la composición del gas, la presión y la potencia.
-
Reproducibilidad y automatización:
- La deposición por pulverización catódica es altamente reproducible y más fácil de automatizar que otros métodos más antiguos, como el haz de electrones o la evaporación térmica.
- El blanco de pulverización catódica proporciona una fuente de vaporización estable y de larga duración, lo que garantiza resultados constantes a lo largo del tiempo.
-
Deposición reactiva y procesos avanzados:
- La deposición reactiva se consigue fácilmente utilizando especies gaseosas reactivas activadas en plasma, lo que permite la formación de películas de óxido o nitruro con las composiciones deseadas.
- El sputtering es compatible con procesos avanzados como el crecimiento epitaxial y puede realizarse en condiciones de vacío ultraalto.
-
Rentabilidad y mantenimiento:
- La deposición por pulverización catódica es relativamente barata en comparación con otros procesos de deposición.
- El proceso no requiere mantenimiento, lo que reduce los costes operativos y el tiempo de inactividad.
-
Instalación compacta y flexible:
- La cámara de deposición por pulverización catódica puede tener un volumen reducido, y la fuente y el sustrato pueden estar muy próximos entre sí, lo que minimiza el calor radiante y simplifica la configuración.
- El blanco para sputtering puede tener forma (por ejemplo, línea, varilla o cilindro) para adaptarse a aplicaciones específicas.
-
Amplia compatibilidad de materiales:
- El sputtering funciona bien con una gama más amplia de materiales, incluidas mezclas y aleaciones, en comparación con métodos como la evaporación térmica.
- Es adecuado para depositar películas ópticas mediante la oxidación o nitruración de iones metálicos pulverizados para conseguir las composiciones de película deseadas.
Al aprovechar estas ventajas, el sputtering se ha convertido en el método preferido para la deposición en vacío moderna, ya que ofrece un rendimiento, una flexibilidad y una rentabilidad superiores en comparación con las técnicas más antiguas.
Tabla resumen:
Ventaja | Descripción |
---|---|
Amplia gama de materiales | Deposita materiales con altos puntos de fusión, metales, aleaciones, compuestos y más. |
Mejor adherencia y calidad de la película | Una mayor energía cinética garantiza películas uniformes con una excelente adherencia. |
Precisión y control | Precisión a nivel molecular para conseguir interfaces prístinas y propiedades de película sintonizables. |
Reproducibilidad y automatización | Altamente reproducible, fácil de automatizar y constante en el tiempo. |
Deposición reactiva | Compatible con gases reactivos para películas de óxido/nitruro y procesos avanzados. |
Rentabilidad | Relativamente económica y sin mantenimiento. |
Configuración compacta y flexible | Cámara de tamaño reducido, calor radiante mínimo y formas de objetivos personalizables. |
Amplia compatibilidad de materiales | Funciona con mezclas, aleaciones y películas ópticas para diversas aplicaciones. |
¿Listo para mejorar su proceso de deposición? Póngase en contacto con nosotros para obtener más información sobre las soluciones para sputtering.