La sinterización por plasma de chispa (SPS) es una técnica de sinterización avanzada que ofrece ventajas significativas sobre los métodos tradicionales, especialmente para polímeros y otros materiales.Combina la activación por plasma, el prensado en caliente y el calentamiento por resistencia para lograr una sinterización rápida a temperaturas más bajas, preservando la microestructura y mejorando las propiedades del material.Este método ahorra energía y tiempo y produce materiales con granos uniformes, alta densidad y excelentes propiedades mecánicas.El SPS se utiliza ampliamente para sinterizar metales, cerámicas y materiales compuestos, lo que lo convierte en una valiosa herramienta en la investigación y producción de materiales avanzados.
Explicación de los puntos clave:
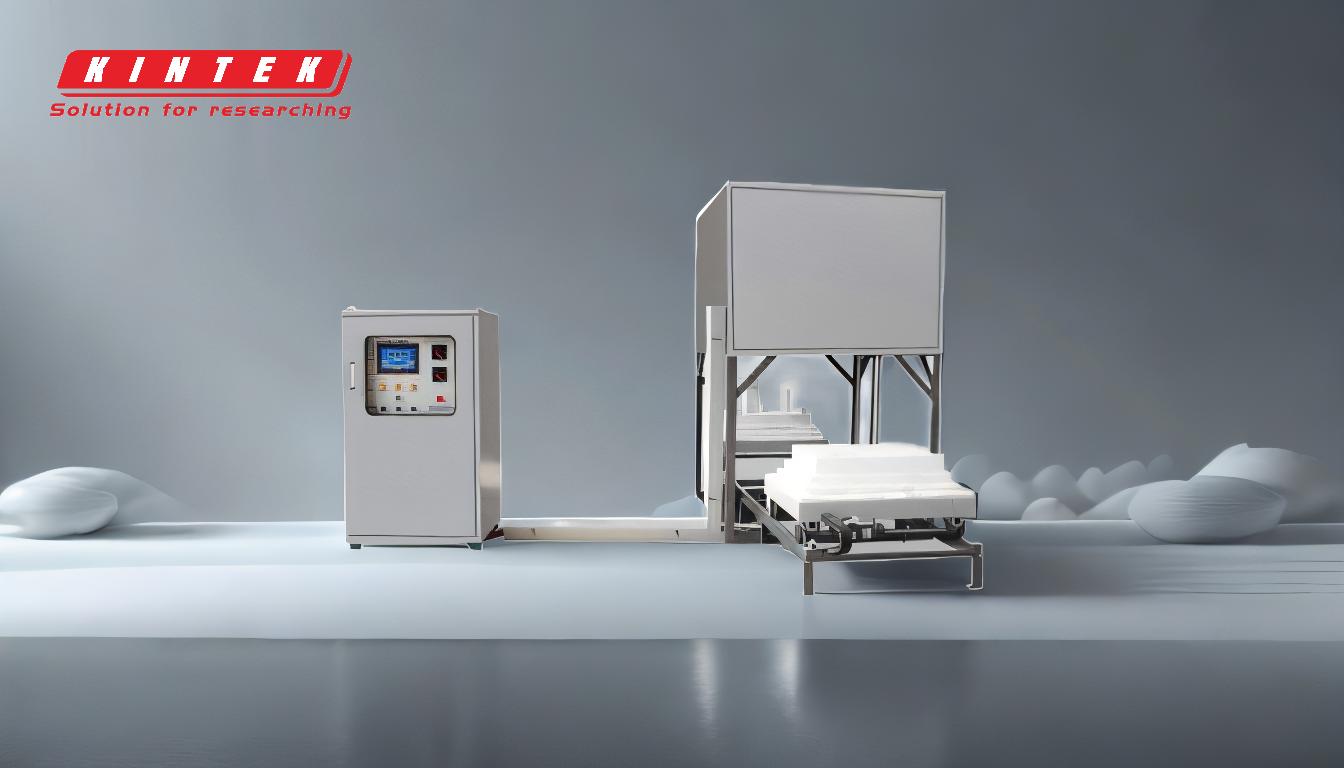
-
¿Qué es el Spark Plasma Sintering (SPS)?
- El SPS es una técnica moderna de sinterización que integra la activación por plasma, el prensado en caliente y el calentamiento por resistencia.Utiliza un voltaje de impulsos de CC para generar calor Joule, provocando la deformación plástica y la descarga entre las partículas de polvo.Esta combinación única de mecanismos permite una sinterización rápida a temperaturas más bajas en comparación con los métodos tradicionales.
-
Ventajas del SPS para polímeros y otros materiales:
- Rápida velocidad de calentamiento: SPS consigue un calentamiento rápido, reduciendo significativamente el tiempo necesario para la sinterización.
- Menor temperatura de sinterización: El proceso funciona a temperaturas más bajas, lo que resulta especialmente beneficioso para materiales sensibles al calor como los polímeros.
- Calentamiento uniforme: Garantiza propiedades uniformes del material en todo el cuerpo sinterizado.
- Eficiencia energética: SPS consume menos energía debido a sus tiempos de procesamiento más cortos y temperaturas más bajas.
- Mejores propiedades de los materiales: Los materiales sinterizados resultantes tienen estructuras de grano fino y uniforme, alta densidad y propiedades mecánicas mejoradas.
-
Mecanismos implicados en el SPS:
- Calentamiento Joule: La principal fuente de calor en SPS, generada por la resistencia del material a la corriente eléctrica.
- Deformación plástica: La presión aplicada durante la sinterización hace que las partículas se deformen y se adhieran más eficazmente.
- Descarga entre partículas: La descarga eléctrica entre partículas ayuda a activar sus superficies, favoreciendo una mejor unión y densificación.
-
Aplicaciones del SPS:
- Metales y Cerámica: El SPS se utiliza ampliamente para sinterizar estos materiales, produciendo productos de alta densidad y grano fino.
- Materiales compuestos: Eficaz para crear materiales compuestos con propiedades mejoradas.
- Nanomateriales: El SPS es especialmente útil para preparar nanomateriales, preservando sus refinadas microestructuras.
- Aleaciones amorfas a granel y materiales funcionales gradientes: Estos materiales avanzados se benefician del control preciso y el procesamiento rápido de SPS.
-
Ventajas para el sinterizado de polímeros:
- Preservación de la microestructura: El SPS permite la consolidación de polvos poliméricos a temperaturas más bajas y tiempos más cortos, manteniendo la microestructura conseguida mediante procesos como el fresado criogénico.
- Propiedades mecánicas mejoradas: La estructura de grano uniforme y la alta densidad conseguidas mediante SPS dan como resultado polímeros con una resistencia mecánica y una durabilidad mejoradas.
-
Comparación con los métodos de sinterización tradicionales:
- Eficiencia en el tiempo: El SPS reduce significativamente el tiempo de sinterización, haciéndolo más eficiente para la producción a gran escala.
- Ahorro de energía: Las temperaturas de funcionamiento más bajas y los tiempos de procesamiento más cortos permiten reducir el consumo de energía.
- Calidad del material: La estructura de grano fino y uniforme y la alta densidad de los materiales sinterizados por SPS a menudo superan a los producidos por métodos tradicionales.
En resumen, el sinterizado por plasma de chispa es un método muy eficiente y eficaz para sinterizar polímeros y otros materiales, que ofrece numerosas ventajas sobre las técnicas tradicionales.Su capacidad para producir materiales de alta calidad con propiedades mejoradas lo convierte en una herramienta valiosa en la ciencia de los materiales y las aplicaciones industriales.
Cuadro sinóptico:
Aspecto | Detalles |
---|---|
¿Qué es SPS? | Combina la activación por plasma, el prensado en caliente y el calentamiento por resistencia para una sinterización rápida. |
Ventajas | Calentamiento rápido, temperaturas más bajas, calentamiento uniforme, eficiencia energética, mejora de las propiedades. |
Mecanismos | Calentamiento Joule, deformación plástica, descarga entre partículas. |
Aplicaciones | Metales, cerámicas, compuestos, nanomateriales, aleaciones amorfas a granel. |
Beneficios de los polímeros | Preserva la microestructura, mejora las propiedades mecánicas. |
frente a los métodos tradicionales | Más rápido, más eficiente energéticamente, material de calidad superior. |
Descubra cómo el sinterizado por plasma puede revolucionar su producción de materiales. contáctenos hoy ¡!