La evaporación por haz de electrones y los sistemas de pulverización iónica son técnicas de deposición física en fase vapor (PVD) utilizadas para crear películas finas, pero difieren significativamente en sus mecanismos, parámetros operativos y aplicaciones.La evaporación por haz de electrones utiliza un haz de electrones focalizado para calentar y vaporizar materiales a alta temperatura, lo que se traduce en una elevada tasa de deposición y la idoneidad para aplicaciones como paneles solares y vidrio.La pulverización catódica, por su parte, consiste en bombardear un material con iones energéticos para expulsar átomos que se depositan en un sustrato.La pulverización catódica funciona a temperaturas más bajas, mejora la adherencia y la homogeneidad de la película y es ideal para sustratos complejos y películas finas de gran pureza.Cada método presenta ventajas distintas en función de los requisitos específicos del proyecto.
Explicación de los puntos clave:
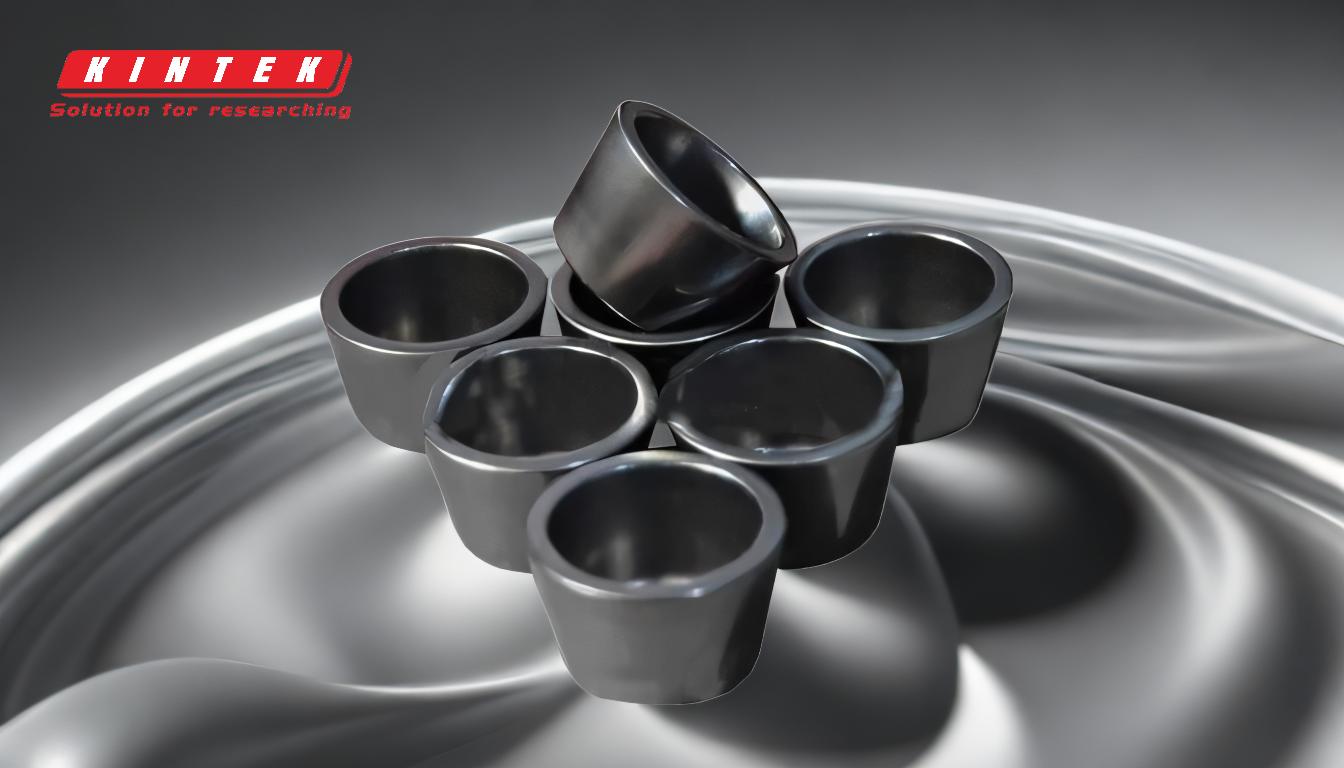
-
Mecanismo de deposición:
- Evaporación por haz de electrones:Utiliza un haz de electrones focalizado para calentar y vaporizar el material fuente.El material vaporizado se condensa en el sustrato para formar una fina película.
- Pulverización iónica:Consiste en bombardear un material objetivo con iones energéticos (normalmente argón) en un entorno de plasma.La colisión expulsa átomos del objetivo, que se depositan en el sustrato.
-
Entorno operativo:
- Evaporación por haz de electrones:Requiere un entorno de alto vacío para minimizar la contaminación y garantizar una vaporización eficaz.
- Pulverización iónica:Funciona en un entorno de bajo vacío y a menudo dentro de un campo magnético cerrado para mejorar la ionización y la eficacia de la deposición.
-
Velocidad de deposición:
- Evaporación por haz de electrones:Ofrece una mayor velocidad de deposición, por lo que es adecuado para aplicaciones que requieren una rápida formación de la película.
- Pulverización iónica:Generalmente tiene una tasa de deposición más baja, especialmente para materiales dieléctricos, pero proporciona un mejor control sobre las propiedades de la película.
-
Adhesión y calidad de la película:
- Evaporación por haz de electrones:Produce películas con menor adherencia y homogeneidad, que pueden requerir tratamientos posteriores a la deposición.
- Pulverización iónica:Proporciona mejor adherencia, mayor homogeneidad de la película y tamaños de grano más pequeños, lo que da como resultado películas finas de mayor calidad.
-
Requisitos de temperatura:
- Evaporación por haz de electrones:Requiere altas temperaturas para vaporizar el material fuente, lo que puede limitar su uso con sustratos sensibles a la temperatura.
- Pulverización iónica:Funciona a temperaturas más bajas, lo que la hace adecuada para materiales sensibles a la temperatura y sustratos complejos.
-
Escalabilidad y automatización:
- Evaporación por haz de electrones:Menos escalable y más difícil de automatizar debido a su dependencia del alto vacío y del control preciso del haz de electrones.
- Pulverización iónica:Más escalable y fácil de automatizar, por lo que resulta ideal para aplicaciones industriales y de producción a gran escala.
-
Aplicaciones:
- Evaporación por haz de electrones:Comúnmente utilizado en aplicaciones como paneles solares, revestimientos de vidrio y películas ópticas debido a su alta tasa de deposición.
- Pulverización iónica:Preferido para la producción eléctrica y óptica, películas finas de gran pureza y revestimientos sobre sustratos complejos debido a su calidad de película y adherencia superiores.
-
Energía de las especies depositadas:
- Evaporación por haz de electrones:Produce especies de vapor de menor energía, lo que puede dar lugar a películas menos densas.
- Pulverización iónica:Expulsa átomos de mayor energía, dando lugar a películas más densas y adherentes.
-
Absorción de gases:
- Evaporación por haz de electrones:Menos propenso a la absorción de gases debido al entorno de alto vacío.
- Pulverización iónica:Más propenso a absorber gases, lo que puede afectar a las propiedades de la película, pero también permite el sputtering reactivo para crear películas compuestas.
-
Direccionalidad de las partículas atomizadas:
- Evaporación por haz de electrones:Produce una corriente de vapor más dispersa, que puede dar lugar a una deposición menos direccional.
- Pulverización iónica:Expulsa las partículas de forma más direccional, mejorando la cobertura en geometrías complejas.
En resumen, la elección entre la evaporación por haz de electrones y el pulverizado iónico depende de los requisitos específicos del proyecto, como la velocidad de deposición, la calidad de la película, la complejidad del sustrato y la escalabilidad.Cada método tiene sus propias ventajas y limitaciones, lo que los hace adecuados para diferentes aplicaciones en la deposición de películas finas.
Cuadro sinóptico:
Aspecto | Evaporación por haz de electrones | Pulverización iónica |
---|---|---|
Mecanismo | El haz de electrones focalizado calienta y vaporiza los materiales. | Los iones energéticos bombardean el material objetivo para expulsar los átomos. |
Entorno operativo | Se requiere alto vacío. | Menor vacío, a menudo con un campo magnético. |
Tasa de deposición | Mayor tasa de deposición. | Menor tasa de deposición, mejor control de las propiedades de la película. |
Adhesión y calidad de la película | Menor adherencia, menor homogeneidad. | Mejor adherencia, mayor homogeneidad, menor tamaño de grano. |
Temperatura | Altas temperaturas requeridas, menos adecuado para sustratos sensibles. | Temperaturas más bajas, ideales para materiales sensibles y sustratos complejos. |
Escalabilidad | Menos escalable, más difícil de automatizar. | Más escalable, más fácil de automatizar para la producción a gran escala. |
Aplicaciones | Paneles solares, revestimientos de vidrio, películas ópticas. | Producción eléctrica/óptica, películas de gran pureza, sustratos complejos. |
Energía de los átomos depositados | Especies de vapor de menor energía, películas menos densas. | Átomos de mayor energía, películas más densas y adherentes. |
Absorción de gases | Menos propenso a la absorción de gases. | Más propenso a absorber gases, lo que permite el sputtering reactivo. |
Direccionalidad | Corriente de vapor dispersa, menos direccional. | Más direccional, mejor cobertura en geometrías complejas. |
¿Necesita ayuda para elegir la técnica de PVD adecuada para su proyecto? Póngase en contacto con nuestros expertos para recibir asesoramiento personalizado.