El calentamiento por inducción es un proceso que utiliza la inducción electromagnética para generar calor dentro de un material conductor.La temperatura alcanzada durante el calentamiento por inducción puede variar mucho en función de varios factores, como las propiedades del material, la frecuencia de la corriente alterna y los requisitos específicos de la aplicación.En general, el calentamiento por inducción puede alcanzar temperaturas que oscilan entre unos pocos cientos de grados centígrados y más de 2.000 °C, lo que lo hace adecuado para una gran variedad de aplicaciones industriales como el endurecimiento, la soldadura fuerte y la fusión de metales.
Explicación de los puntos clave:
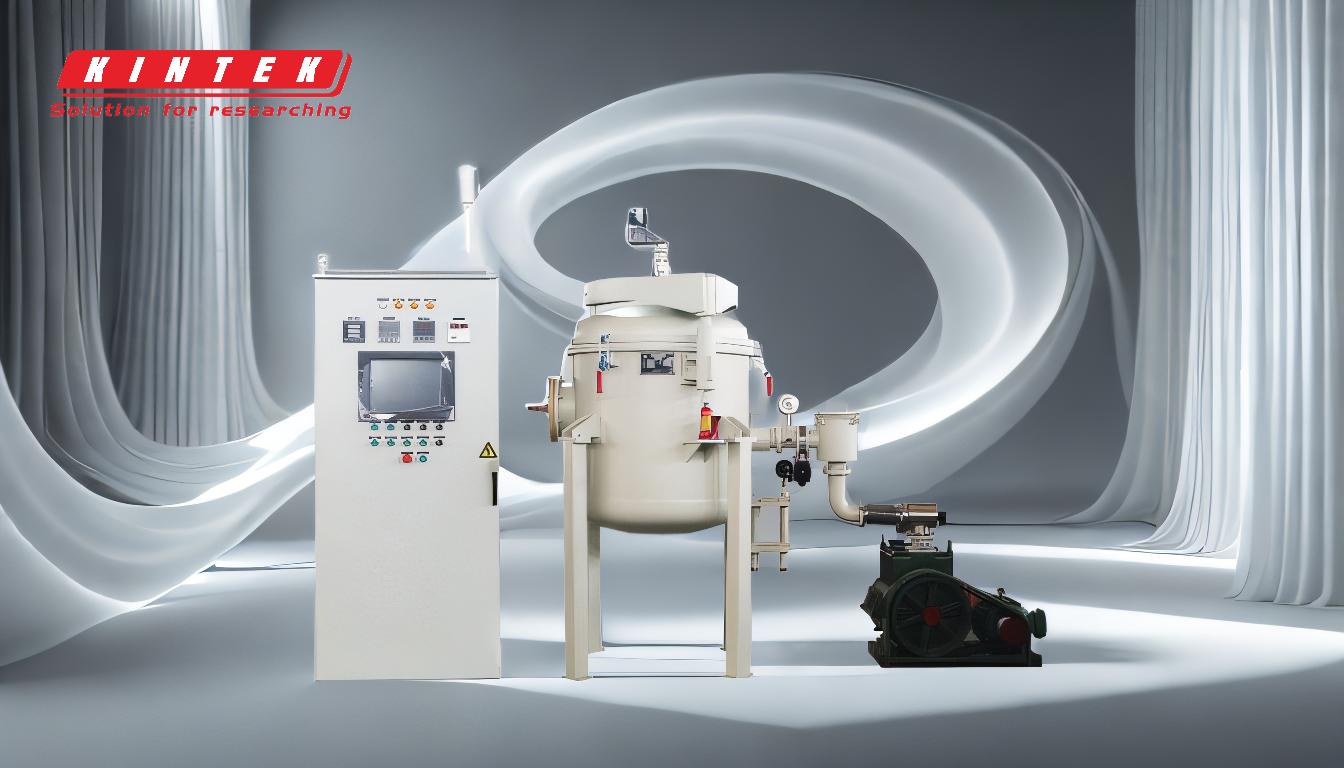
-
Las Propiedades del Material Influyen en la Temperatura de Calentamiento:
- Conductividad y Resistividad: Los materiales con mayor conductividad eléctrica, como el cobre y el aluminio, se calientan más eficazmente debido a su menor resistencia al flujo de corrientes parásitas.Por el contrario, los materiales con mayor resistividad, como ciertos aceros, pueden calentarse más rápidamente pero necesitan más energía para alcanzar la misma temperatura.
- Propiedades magnéticas: Los materiales magnéticos, como el hierro y algunos aceros, generan calor mediante corrientes de Foucault y efectos de histéresis.Este doble mecanismo permite que estos materiales se calienten más rápidamente que los no magnéticos.
- Tamaño y grosor: Los materiales más pequeños y delgados se calientan más rápidamente porque las corrientes inducidas tienen menos material que penetrar.Esto es especialmente importante en aplicaciones que requieren un calentamiento rápido, como el endurecimiento de superficies.
-
Frecuencia de la corriente alterna:
- Frecuencia más alta: Las corrientes alternas de mayor frecuencia dan lugar a una menor penetración en profundidad del calentamiento, lo que resulta ideal para aplicaciones de calentamiento superficial como el cementado.El efecto piel hace que la corriente se concentre cerca de la superficie, lo que provoca un rápido calentamiento superficial.
- Frecuencia más baja: Las frecuencias más bajas se utilizan para una penetración más profunda, necesaria para aplicaciones de calentamiento pasante como la forja o la fusión.La elección de la frecuencia es crucial para determinar el perfil de calentamiento y la distribución final de la temperatura en el material.
-
Requisitos de temperatura específicos de la aplicación:
- Endurecimiento de metales: En procesos como el temple por inducción, la temperatura suele elevarse hasta el rango de austenitización (en torno a 750-900°C para el acero) para permitir la transformación de la microestructura, seguida de un enfriamiento rápido para alcanzar la dureza deseada.
- Soldadura fuerte y blanda: Estos procesos requieren temperaturas más bajas, normalmente entre 450°C y 800°C, dependiendo del material de aportación utilizado.La temperatura exacta es fundamental para garantizar el flujo y la unión adecuados del material de relleno sin dañar el material base.
- Fusión: En la fusión por inducción, las temperaturas pueden superar los 2000°C, especialmente cuando se funden metales refractarios como el wolframio o el molibdeno.Las altas temperaturas son necesarias para superar el elevado punto de fusión del material y alcanzar un estado fundido.
-
Consideraciones sobre el tratamiento térmico al vacío:
- Requisitos técnicos y de rendimiento: En el tratamiento térmico al vacío, la temperatura de calentamiento se selecciona cuidadosamente en función de los requisitos técnicos, las condiciones de servicio y las necesidades de rendimiento de la pieza.El objetivo es minimizar la deformación al tiempo que se consiguen las propiedades deseadas del material.
- Minimizar la deformación: Bajar la temperatura de calentamiento puede reducir el riesgo de deformación, especialmente en componentes complejos o de paredes finas.Sin embargo, la temperatura debe seguir siendo lo suficientemente alta para lograr las transformaciones metalúrgicas necesarias.
-
Características del horno de inducción:
- Arranque a voltaje cero: Los hornos de inducción modernos suelen contar con un arranque a tensión cero, que inicia el proceso de calentamiento suavemente y con una alta potencia inicial.Esto minimiza el impacto en la red eléctrica y permite un control preciso del proceso de calentamiento.
- Eficiencia energética: La capacidad de controlar la frecuencia y la potencia del proceso de calentamiento por inducción contribuye a la eficiencia energética, ya que el calor se genera directamente dentro del material en lugar de transferirse desde una fuente externa.
En resumen, la temperatura del proceso de calentamiento por inducción es muy variable y depende del material que se calienta, la frecuencia de la corriente alterna y los requisitos específicos de la aplicación.Comprender estos factores es crucial para optimizar el proceso de calentamiento por inducción y lograr los resultados deseados de forma eficiente y eficaz.
Tabla resumen:
Factor | Impacto en la temperatura |
---|---|
Propiedades de los materiales | - Conductividad:Mayor conductividad = calentamiento eficaz. |
- Propiedades magnéticas:Los materiales magnéticos se calientan más rápido debido a las corrientes parásitas y la histéresis. | |
- Tamaño y grosor:Los materiales más pequeños o más finos se calientan más rápido. | |
Frecuencia de la corriente alterna | - Frecuencia más alta:Mejor para calentamiento superficial (por ejemplo, cementación). |
- Frecuencia más baja:Mejor para calentamiento profundo (por ejemplo, fusión). | |
Requisitos de aplicación | - Temple de metales: 750-900°C. |
- Soldadura fuerte/soldadura blanda:450-800°C. | |
- Fusión:Hasta 2000°C+ para metales refractarios. |
Optimice hoy mismo su proceso de calentamiento por inducción contacte con nuestros expertos para soluciones a medida.