La temperatura de sinterización de la cerámica, sobre todo en aplicaciones dentales, suele oscilar entre 1.200 °C y 1.400 °C.Esta alta temperatura es esencial para facilitar la difusión atómica a través de los límites de las partículas, lo que permite que éstas se fusionen sin alcanzar el punto de fusión del material.El proceso consta de varias etapas: preparación del polvo, calentamiento, fusión de las partículas y solidificación.En el caso de materiales como el óxido de circonio, la temperatura de sinterización suele superar entre los 1100 °C y los 1200 °C, y algunos hornos funcionan a temperaturas cercanas a los 1500 °C para lograr la máxima densidad.La temperatura exacta depende de las propiedades del material y del resultado deseado, garantizando una densidad y una integridad estructural óptimas.
Explicación de los puntos clave:
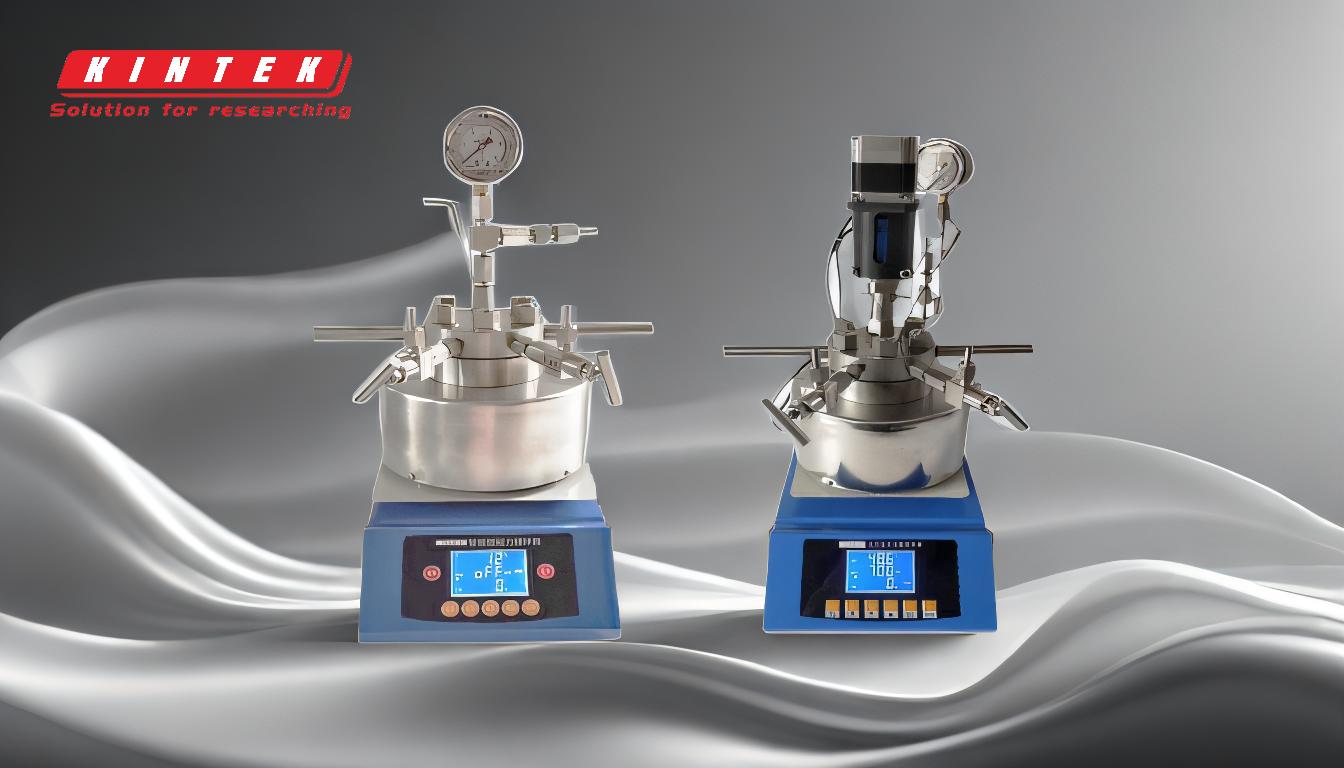
-
Gama de temperaturas para sinterizar cerámica:
- El proceso de sinterización suele requerir temperaturas entre 1200°C y 1400°C para la cerámica, especialmente en aplicaciones dentales.
- Este rango es crítico porque permite que los átomos se difundan y las partículas se fusionen sin licuar el material.
- En el caso de la circonia, la transformación de los estados cristalinos monoclínico a politetragonal se produce en torno a los 1100°C a 1200°C pero a temperaturas más altas (hasta 1500°C ) para alcanzar una densidad máxima cercana a la teórica.
-
Papel de la temperatura en la sinterización:
- La temperatura es un factor clave en la sinterización, ya que debe ser lo suficientemente alta para permitir la difusión atómica y la unión de las partículas, pero inferior al punto de fusión del material para evitar la licuefacción.
- El horno de sinterización debe mantener un control preciso de la temperatura para garantizar que el material alcance la densidad y las propiedades estructurales deseadas.
-
Etapas del proceso de sinterización:
- Preparación del polvo:La materia prima se prepara en una forma compacta utilizando métodos como la soldadura en frío, la impresión 3D o el prensado.
- Calentamiento y consolidación:El compacto se calienta justo por debajo de su punto de fusión, lo que activa las microestructuras cristalinas e inicia la unión de las partículas.
- Fusión de partículas:Las partículas se densifican y se fusionan, un proceso que puede acelerarse mediante técnicas como la sinterización en fase líquida (LPS).
- Solidificación:El material se enfría y solidifica en una estructura unificada y densa.
-
Consideraciones específicas del material:
- En el caso de la circonia, la temperatura de sinterización es fundamental para lograr la transformación cristalina y la densidad deseadas.
- Los hornos de sinterización suelen funcionar a temperaturas más elevadas (por ejemplo, 1500°C) para garantizar la máxima densidad, que puede alcanzar hasta el 99% del máximo teórico .
-
Importancia de un control preciso de la temperatura:
- Los hornos de sinterización deben mantener temperaturas por debajo del punto de fusión del material para evitar la licuefacción y garantizar al mismo tiempo el calor suficiente para la fusión de las partículas.
- Esta precisión es crucial para conseguir las propiedades mecánicas y estructurales deseadas en el producto final.
-
Aplicaciones e implicaciones:
- En aplicaciones dentales, la sinterización se utiliza para crear restauraciones cerámicas de alta resistencia, como coronas y puentes.
- La capacidad de controlar la temperatura de sinterización influye directamente en la calidad, durabilidad y rendimiento del producto final.
Para obtener más información sobre los hornos de sinterización, puede consultar esta guía detallada: horno de sinterización .
Cuadro recapitulativo :
Aspecto | Detalles |
---|---|
Gama de temperaturas | 1200°C-1400°C (hasta 1500°C para el óxido de circonio) |
Papel clave de la temperatura | Permite la difusión atómica y la unión de partículas sin licuefacción |
Etapas de la sinterización | Preparación del polvo, calentamiento, fusión de partículas, solidificación |
Factores específicos del material | La circonia requiere 1100°C-1200°C para la transformación cristalina |
Importancia de la precisión | Garantiza una densidad, integridad estructural y propiedades mecánicas óptimas |
Aplicaciones | Restauraciones dentales (coronas, puentes) y componentes cerámicos de alta resistencia |
¿Necesita soluciones de sinterización precisas para su cerámica? Póngase en contacto con nuestros expertos para obtener más información.