El amoníaco se utiliza en el proceso de recocido principalmente porque puede disociarse en una mezcla gaseosa de 75% de hidrógeno y 25% de nitrógeno, lo que ofrece varias ventajas. El hidrógeno, componente clave de esta mezcla, tiene un alto coeficiente de transferencia de calor, lo que hace que el proceso de recocido sea más eficiente y eficaz. Además, el hidrógeno del amoníaco disociado evita la oxidación, garantizando la integridad de los materiales tratados. El uso de amoníaco disociado también es rentable en comparación con el hidrógeno puro, lo que lo convierte en una opción práctica para aplicaciones industriales. Esta combinación de eficacia, protección y rentabilidad hace del amoníaco un recurso valioso en los procesos de recocido.
Explicación de los puntos clave:
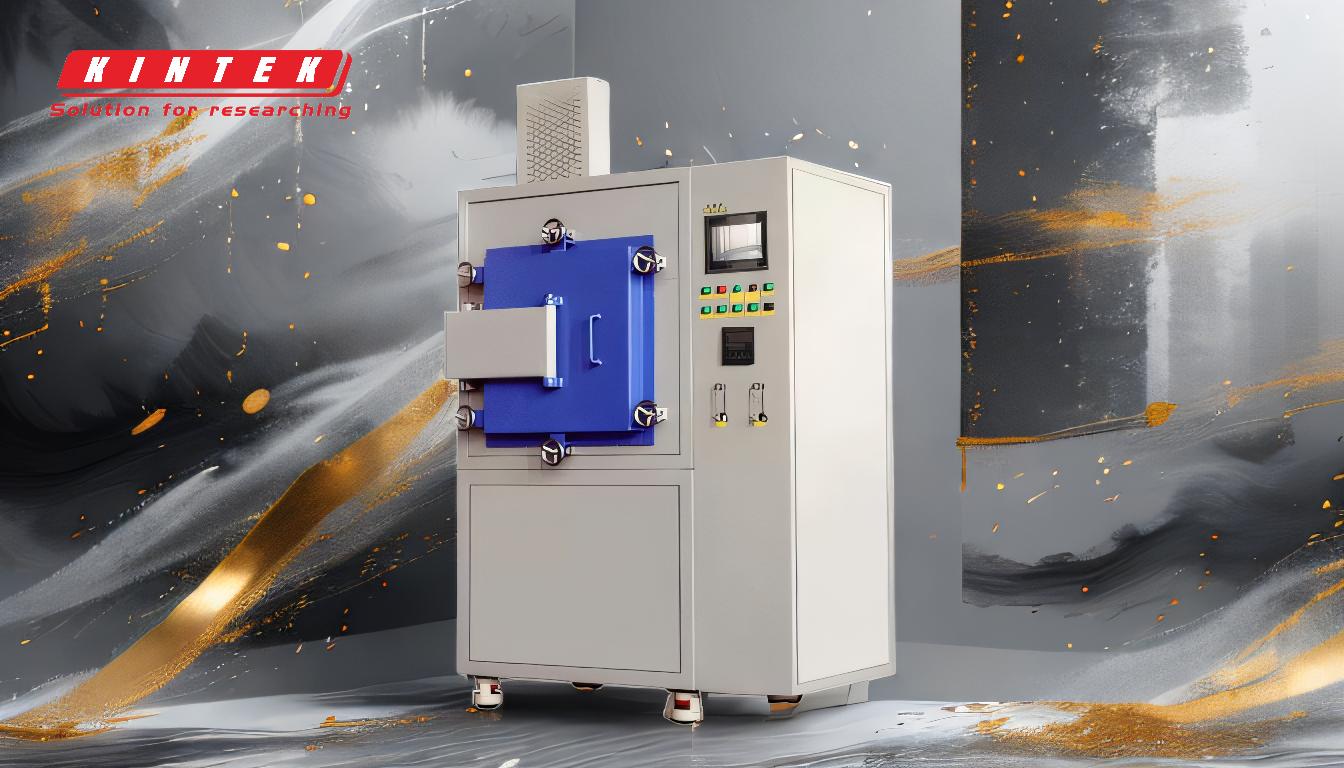
-
Disociación del amoníaco:
- El amoníaco puede disociarse (craquearse) en una mezcla gaseosa que contiene un 75% de hidrógeno y un 25% de nitrógeno.
- Este proceso de disociación convierte al amoníaco en una fuente versátil tanto de hidrógeno como de nitrógeno, que son esenciales en diversos procesos de tratamiento térmico, incluido el recocido.
-
Papel del hidrógeno en el recocido:
- El hidrógeno, componente principal del amoníaco disociado, tiene un elevado coeficiente de transferencia de calor, lo que aumenta la eficacia del proceso de recocido.
- Una transferencia de calor eficaz garantiza el calentamiento y enfriamiento uniformes de los materiales, lo que es crucial para conseguir las propiedades mecánicas deseadas y reducir las tensiones internas.
-
Prevención de la oxidación:
- El hidrógeno del amoníaco disociado actúa como agente reductor, evitando la oxidación de los materiales durante el proceso de recocido.
- La oxidación puede provocar defectos superficiales y la degradación de las propiedades del material, por lo que la atmósfera protectora que proporciona el hidrógeno es fundamental para mantener la integridad del material.
-
Relación coste-eficacia:
- El amoníaco disociado ofrece muchas de las ventajas del hidrógeno puro, pero a un coste menor.
- Esta ventaja de costes la convierte en una opción atractiva para aplicaciones industriales en las que se requieren grandes volúmenes de gas.
-
Versatilidad y practicidad:
- El amoníaco puede producirse y almacenarse en distintas formas (gas generado, gas embotellado o gas almacenado a granel), lo que lo convierte en una opción flexible y práctica para distintas instalaciones industriales.
- Su capacidad para servir a dos propósitos (como fuente de nitrógeno para la nitruración y de hidrógeno para la reducción) aumenta su versatilidad en los procesos de tratamiento térmico.
-
Aplicación en el tratamiento térmico de componentes fundidos y soldados:
- El uso de amoníaco disociado es especialmente beneficioso en el tratamiento térmico de componentes fundidos y soldados, donde la transferencia de calor eficaz y la prevención de la oxidación son cruciales.
- Estos componentes suelen requerir un tratamiento térmico preciso para conseguir las propiedades mecánicas y la integridad estructural deseadas.
Aprovechando las propiedades del amoníaco disociado, las industrias pueden conseguir procesos de recocido eficientes, eficaces y económicos, garantizando resultados de alta calidad para los materiales tratados.
Cuadro recapitulativo:
Beneficio clave | Explicación |
---|---|
Disociación del amoníaco | El amoníaco se disocia en un 75% de hidrógeno y un 25% de nitrógeno, ideal para el tratamiento térmico. |
Transferencia de calor eficiente | El elevado coeficiente de transferencia de calor del hidrógeno garantiza un calentamiento y enfriamiento uniformes. |
Prevención de la oxidación | El hidrógeno actúa como agente reductor, protegiendo los materiales de la oxidación. |
Relación coste-eficacia | El amoníaco disociado es más económico que el hidrógeno puro para uso industrial. |
Versatilidad | El amoníaco tiene una doble función: hidrógeno para la reducción y nitrógeno para la nitruración. |
Aplicaciones industriales | Ideal para el tratamiento térmico de componentes fundidos y soldados, garantizando la integridad del material. |
Optimice su proceso de recocido con amoníaco disociado- contacte con nosotros para saber más