Sí, un calentador de inducción puede fundir aluminio.El calentamiento por inducción es un método muy eficiente y eficaz para fundir materiales conductores como el aluminio.El proceso se basa en la inducción electromagnética para generar calor dentro del propio aluminio, lo que garantiza un calentamiento y una fusión uniformes.A continuación se explica detalladamente cómo funcionan los calentadores de inducción con el aluminio, sus ventajas y los factores clave que intervienen en el proceso.
Explicación de los puntos clave:
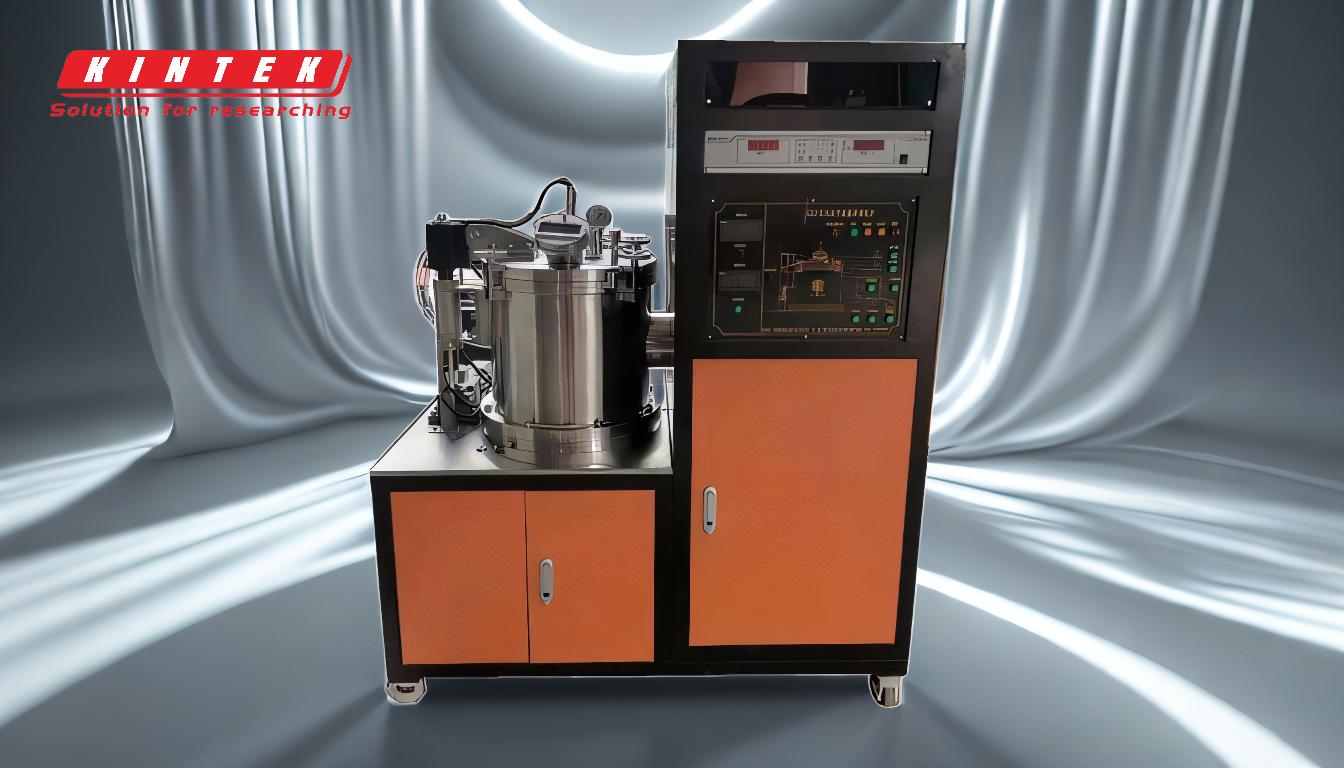
-
Cómo funciona el calentamiento por inducción del aluminio
- El calentamiento por inducción utiliza corriente alterna (CA) que pasa a través de una bobina de inducción para crear un campo magnético que cambia rápidamente.
- Cuando el aluminio (un material conductor) se coloca dentro de este campo magnético, la Ley de Faraday induce corrientes de Foucault dentro del aluminio.
- La resistencia del aluminio a estas corrientes de Foucault genera calor, un fenómeno conocido como calentamiento Joule.
- Este calor se genera internamente en el aluminio, lo que garantiza un calentamiento rápido y uniforme.
- El campo magnético también provoca una agitación inductiva, que ayuda a mezclar el aluminio fundido y garantiza una temperatura y composición uniformes.
-
Ventajas del calentamiento por inducción para la fusión del aluminio
- Eficiencia energética:Los hornos de inducción son muy eficientes desde el punto de vista energético, lo que los hace ideales para fundir aluminio, que es un proceso que consume mucha energía.
- Calentamiento uniforme:El efecto de agitación electromagnética garantiza una distribución uniforme de la temperatura, reduciendo el riesgo de puntos calientes y de fusión desigual.
- Impurezas reducidas:La acción de agitación ayuda a que las impurezas suban a la superficie, donde pueden eliminarse fácilmente, lo que da como resultado un aluminio más puro.
- Menos oxidación y pérdidas por combustión:El calentamiento por inducción minimiza la exposición al oxígeno, reduciendo la oxidación y la pérdida de material durante la fusión.
- Precisión y control:Los hornos de inducción permiten un control preciso de la temperatura y la velocidad de calentamiento, lo que es fundamental para producir aleaciones de aluminio de alta calidad.
-
Factores que influyen en la fusión del aluminio en los hornos de inducción
- Frecuencia de la corriente alterna:La frecuencia de la corriente alterna utilizada en la bobina de inducción afecta a la profundidad de penetración del calor en el aluminio.Las frecuencias más altas suelen utilizarse para piezas más pequeñas o secciones finas, mientras que las frecuencias más bajas son mejores para volúmenes más grandes.
- Conductividad del material:La alta conductividad eléctrica del aluminio lo hace idóneo para el calentamiento por inducción, ya que genera calor de forma eficiente mediante corrientes parásitas.
- Diseño del crisol:El crisol utilizado en el horno de inducción debe ser compatible con el aluminio y soportar las altas temperaturas necesarias para la fusión.
- Intensidad del campo magnético:La intensidad del campo magnético determina la intensidad de las corrientes parásitas y, en consecuencia, la velocidad de calentamiento.
-
Aplicaciones del calentamiento por inducción para el aluminio
- Producción de aluminio primario:Los hornos de inducción se utilizan para convertir la alúmina en aluminio puro y después en aleaciones de aluminio.
- Reciclaje:El calentamiento por inducción es ideal para reciclar chatarra de aluminio, ya que garantiza una fusión y purificación eficaces.
- Producción de aleaciones:El control preciso y el calentamiento uniforme que proporcionan los hornos de inducción los hacen adecuados para producir aleaciones de aluminio de alta calidad con propiedades específicas.
- Fundición y moldeo:El aluminio fundido de los hornos de inducción puede utilizarse directamente para procesos de fundición y moldeo.
-
Retos y consideraciones
- Coste inicial:Los hornos de inducción pueden tener un coste inicial más elevado en comparación con los métodos de fusión tradicionales, pero su eficiencia energética y sus ventajas operativas suelen compensarlo con el tiempo.
- Mantenimiento:La bobina de inducción y el crisol requieren un mantenimiento regular para garantizar un rendimiento óptimo y una larga vida útil.
- Compatibilidad de materiales:Aunque el aluminio es muy adecuado para el calentamiento por inducción, el proceso puede no ser tan eficaz para materiales no conductores o con baja conductividad eléctrica.
En resumen, los calentadores de inducción no sólo son capaces de fundir aluminio, sino que también son muy eficientes y eficaces para este fin.Ofrecen numerosas ventajas, como la eficiencia energética, el calentamiento uniforme y la reducción de impurezas, lo que los convierte en la opción preferida para fundir aluminio en diversas aplicaciones industriales.
Cuadro sinóptico:
Aspecto | Detalles |
---|---|
Cómo funciona | Utiliza la inducción electromagnética para generar calor interno en el aluminio. |
Principales ventajas | Eficiencia energética, calentamiento uniforme, reducción de impurezas, control preciso. |
Factores que influyen | Frecuencia de CA, conductividad del material, diseño del crisol, intensidad del campo magnético. |
Aplicaciones | Producción de aluminio primario, reciclaje, producción de aleaciones, fundición y moldeo. |
Desafíos | Mayor coste inicial, requisitos de mantenimiento, compatibilidad de materiales. |
¿Está listo para explorar el calentamiento por inducción para sus necesidades de fusión de aluminio? Póngase en contacto con nosotros para obtener asesoramiento experto y soluciones.