Entendiendo el prensado en caliente
Tabla de contenido
- Entendiendo el prensado en caliente
- Tipos de calentamiento en prensado en caliente
- Introducción a tres tipos de calentamiento: calentamiento por inducción, calentamiento por resistencia indirecta y técnica de sinterización asistida en campo (FAST)/prensado directo en caliente.
- Calentamiento inductivo
- Calentamiento por resistencia indirecta
- Técnica de sinterización asistida en campo (FAST) / Prensado directo en caliente
- Calentamiento inductivo
- Calentamiento por resistencia indirecta
- Técnica de sinterización asistida en campo (FAST) / Prensado directo en caliente
- Aplicaciones del prensado en caliente
- Fabricación de artículos críticos como objetivos de pulverización catódica y componentes cerámicos de alto rendimiento.
- Beneficios de usar polvo metálico
- Idoneidad del proceso para altas velocidades de calentamiento.
- Papel del prensado directo en caliente en la industria de materiales de fricción.
- Aplicaciones de pastillas de freno y discos de embrague sinterizados
Definición y proceso de prensado en caliente.
El prensado en caliente es un proceso de pulvimetalurgia de alta presión y baja tasa de deformación que se utiliza para formar polvo o polvo compacto a altas temperaturas para inducir procesos de sinterización y fluencia. Implica la aplicación simultánea de calor y presión para fabricar materiales duros y quebradizos.
Uso y aplicación principal
El prensado en caliente se utiliza principalmente en la consolidación de herramientas de corte compuestas de metal y diamante, cerámicas técnicas y otros materiales duros y quebradizos. Funciona mediante reordenamiento de partículas y flujo plástico en los contactos de las partículas. El polvo suelto o la pieza precompactada se introduce en un molde de grafito, lo que permite el calentamiento por inducción o resistencia hasta temperaturas típicas de 2400 °C (4350 °F). Se pueden aplicar presiones de hasta 50 MPa (7300 psi). El prensado en caliente también se utiliza en el prensado de diferentes tipos de polímeros.
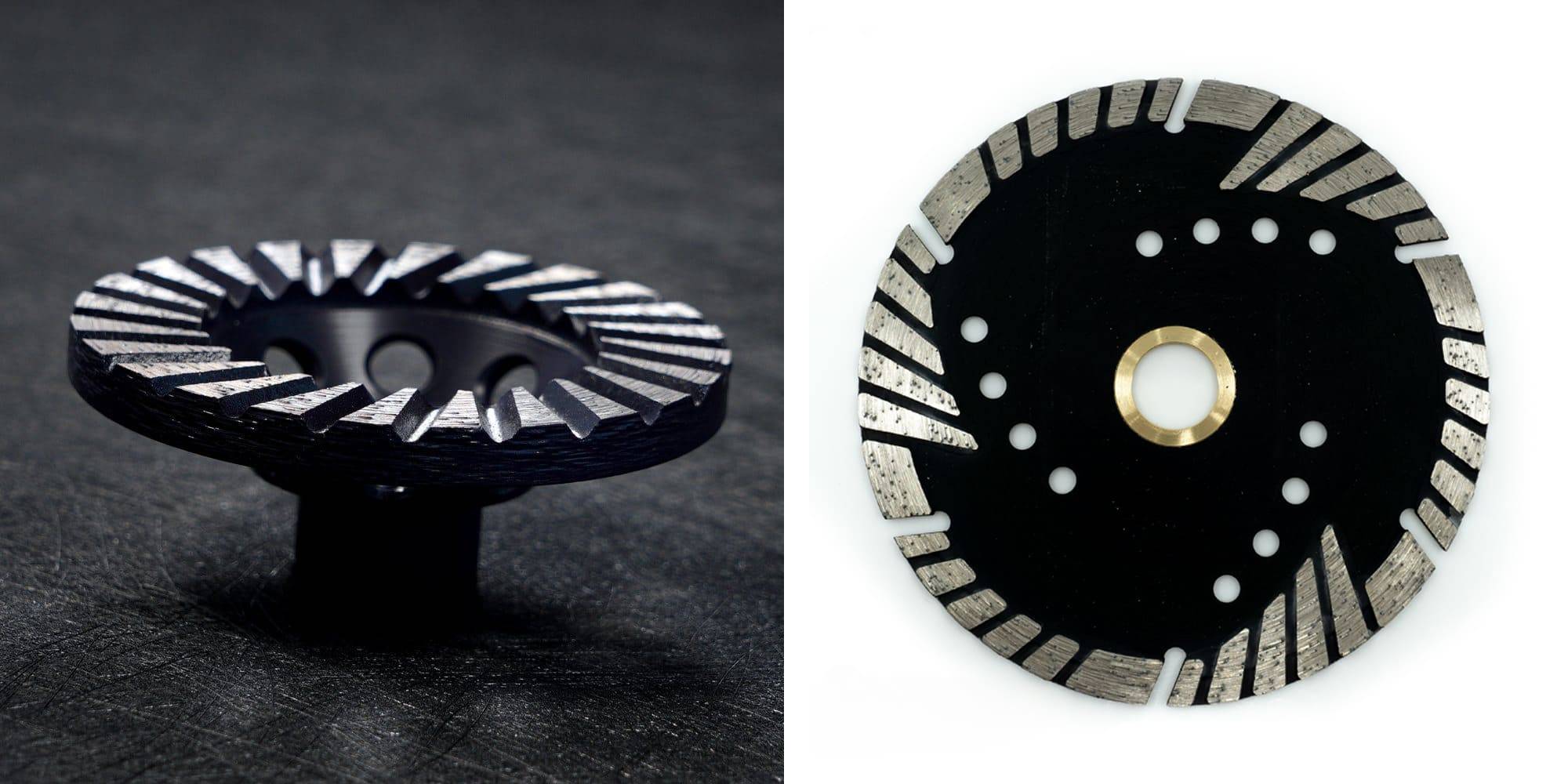
Diamantes prensados en caliente
Densificación mediante reordenamiento de partículas y flujo plástico.
El proceso de densificación en el prensado en caliente se produce mediante la reordenación de las partículas y el flujo plástico en los contactos de las partículas. La presión externa aplicada durante el prensado en caliente provoca la destrucción de los defectos y poros internos, lo que hace que las superficies internas entren en contacto entre sí. Luego, el material sufre fluencia a alta temperatura, lo que permite la penetración mutua y la unión por difusión, eliminando por completo los defectos y la porosidad.
Uso del molde de grafito y temperaturas de calentamiento.
En el prensado en caliente se suele utilizar un molde de grafito para contener el polvo suelto o la pieza precompactada. El molde de grafito permite un calentamiento eficiente mediante calentamiento por inducción o resistencia. Las temperaturas utilizadas en el prensado en caliente pueden alcanzar hasta 2400 °C (4350 °F), asegurando los procesos de sinterización y fluencia necesarios para la densificación.
Presiones involucradas en el proceso.
El prensado en caliente implica la aplicación de altas presiones para lograr la densificación. Se pueden aplicar presiones de hasta 50 MPa (7300 psi) durante el proceso de prensado en caliente. La alta presión ayuda a la reorganización de las partículas y al flujo plástico, lo que da como resultado un producto final compacto y denso.
Prensado en caliente en la industria de los polímeros.
El prensado en caliente también se utiliza ampliamente en la industria de los polímeros. Al utilizar la técnica de prensado en caliente, los fabricantes pueden eliminar la necesidad de aglutinantes en su proceso de fabricación y, en su lugar, utilizar la combinación de fuerza y temperatura para unir sus piezas por completo. Esto permite la producción de productos poliméricos de alta calidad con propiedades mecánicas y precisión dimensional mejoradas.
En resumen, el prensado en caliente es un proceso de pulvimetalurgia que se utiliza para fabricar materiales duros y quebradizos. Implica la aplicación de calor y presión para inducir procesos de sinterización y fluencia, lo que da como resultado la densificación. El prensado en caliente se utiliza ampliamente en diversas industrias, incluida la aeroespacial, la cerámica y la fabricación de polímeros. El proceso utiliza un molde de grafito y puede alcanzar altas temperaturas y presiones para lograr los resultados deseados.
Tipos de calentamiento en prensado en caliente
Introducción a tres tipos de calentamiento: calentamiento por inducción, calentamiento por resistencia indirecta y técnica de sinterización asistida en campo (FAST)/prensado directo en caliente.
El prensado en caliente es una técnica ampliamente utilizada en la industria manufacturera para crear uniones duraderas y estrechas entre materiales. Implica la combinación de fuerza añadida durante la sinterización de materiales a alta temperatura, ya sea en vacío o bajo presión positiva de gas inerte. Esta presión ayuda a aumentar la densificación del material, lo que da como resultado un tocho de material con densidades cercanas a las teóricas.
Hay dos tipos principales de hornos de prensado en caliente: los que utilizan varillas frías y calientes para aplicar presión y los que utilizan punzones y matrices de grafito o placas de presión para ejercer la fuerza durante la unión por difusión. Estos hornos eliminan la necesidad de aglutinantes en el proceso de fabricación, lo que los hace muy eficientes.
Dentro de la tecnología de prensado en caliente, se utilizan tres tipos distintos de métodos de calentamiento: calentamiento por inducción, calentamiento por resistencia indirecta y técnica de sinterización asistida en campo (FAST)/prensado en caliente directo.
Calentamiento inductivo
El calentamiento inductivo es un método comúnmente utilizado para la sinterización de polvo de compuestos intermetálicos de metal, cerámica y algunos metales refractarios. Implica el uso de inducción electromagnética para generar calor dentro del material.
En este proceso, se hace pasar una corriente alterna a través de una bobina, creando un campo magnético. Este campo magnético induce corrientes parásitas dentro del material, que a su vez generan calor. Luego se utiliza el calor para sinterizar el material y crear la unión deseada.
El calentamiento inductivo es conocido por su eficiencia y precisión. Permite velocidades de calentamiento rápidas y un control preciso sobre la distribución de la temperatura, lo que da como resultado uniones de alta calidad. Es particularmente adecuado para materiales que tienen alta conductividad eléctrica.
Calentamiento por resistencia indirecta
El calentamiento por resistencia indirecta es otro método comúnmente utilizado en el prensado en caliente. Implica el uso de resistencia eléctrica para generar calor dentro del material.
En este proceso, una corriente eléctrica pasa a través del material, provocando resistencia y generando calor. Luego se utiliza el calor para sinterizar el material y crear la unión deseada.
El calentamiento por resistencia indirecta es conocido por su simplicidad y versatilidad. Se puede utilizar con una amplia gama de materiales y es especialmente adecuado para materiales que tienen baja conductividad eléctrica. Permite un control preciso de la temperatura y puede alcanzar altas tasas de calentamiento.
Técnica de sinterización asistida en campo (FAST) / Prensado directo en caliente
La técnica de sinterización asistida en campo (FAST), también conocida como prensado directo en caliente, es un método relativamente nuevo utilizado en el prensado en caliente. Implica el uso de un campo eléctrico para ayudar en el proceso de sinterización.
En este proceso, una corriente eléctrica pasa a través del material, creando un campo eléctrico. Este campo eléctrico mejora la movilidad de los átomos dentro del material, permitiendo una sinterización y densificación aceleradas.
El prensado en caliente RÁPIDO/directo es conocido por su capacidad para producir materiales muy densos y uniformes. Permite velocidades de sinterización rápidas y puede alcanzar altas densidades cercanas a las teóricas. Es particularmente adecuado para materiales que tienen baja difusividad y alta conductividad eléctrica.
En conclusión, el prensado en caliente es una técnica valiosa en la industria manufacturera para crear uniones duraderas y estrechas entre materiales. Dentro de la tecnología de prensado en caliente, se utilizan comúnmente tres tipos de métodos de calentamiento: calentamiento por inducción, calentamiento por resistencia indirecta y técnica de sinterización asistida en campo (FAST)/prensado en caliente directo. Cada método tiene sus propias ventajas y es adecuado para diferentes materiales y aplicaciones.
Calentamiento inductivo
Proceso y funcionamiento del calentamiento inductivo.
El calentamiento inductivo es el proceso de calentar materiales eléctricamente conductores, como metales o semiconductores, mediante inducción electromagnética. Esto se logra haciendo pasar una corriente alterna de alta frecuencia a través de un electroimán, creando un campo magnético que alterna rápidamente. Este campo magnético induce corrientes parásitas dentro del material, que fluyen a través de su resistencia y generan calor mediante calentamiento Joule. En materiales ferromagnéticos y ferrimagnéticos, el calor también se genera por pérdidas por histéresis magnética. La frecuencia de la corriente eléctrica utilizada depende de factores como el tamaño y material del objeto, el acoplamiento entre la bobina de trabajo y el objeto y la profundidad de penetración.
Este método de calentamiento se usa comúnmente para fundir metales y fabricar aleaciones. La fusión por inducción al vacío, que combina una atmósfera controlada y un control preciso del proceso de fusión, es una aplicación popular del calentamiento inductivo. Los hornos de inducción pueden alcanzar temperaturas de 1800ºC o más y normalmente constan de un enfriador, una unidad de potencia y una unidad de vacío.
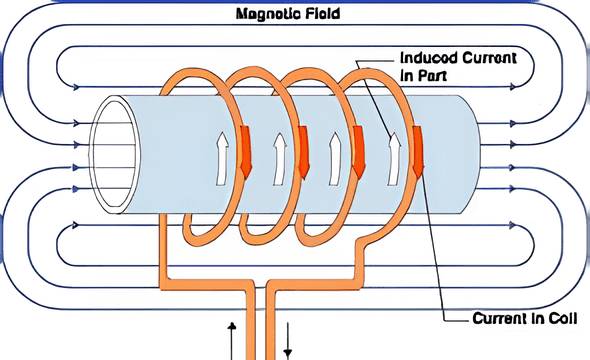
Ventajas y desventajas del calentamiento inductivo.
El calentamiento inductivo ofrece varias ventajas sobre otros métodos de calentamiento. Es un proceso más rápido en comparación con el calentamiento eléctrico o de gas, gracias a su principio de inducción. Los hornos de inducción también tienen un tiempo de arranque rápido, ya que no requieren un ciclo de calentamiento o enfriamiento. La alimentación por inducción crea una fuerte acción de agitación, lo que da como resultado mezclas homogéneas de metal líquido. Además, los hornos de inducción requieren menos materiales refractarios en comparación con las unidades alimentadas por combustible. Son más eficientes energéticamente y capaces de reducir el consumo de energía para fundir metales. Los hornos de inducción también son de tamaño compacto, lo que permite una instalación más sencilla y tasas de producción más altas debido a tiempos de fusión más cortos.
Sin embargo, también hay algunas desventajas a considerar. Es posible que la potencia nominal de los hornos de inducción no siempre refleje su potencia de trabajo real, lo que lleva a una reducción de la eficiencia de fusión. Es importante asegurarse de que el proveedor cuente con tecnología de placa de potencia de inducción de desarrollo propio y pueda proporcionar soluciones personalizadas flexibles. Además, el calentamiento por inducción puede plantear desafíos en la distribución del calor y la velocidad de calentamiento, lo que requiere una consideración cuidadosa de la aplicación específica y del material que se está calentando.
Problemas con la distribución del calor y la velocidad de calefacción.
El calentamiento por inducción puede producir densidades de alta potencia, lo que permite tiempos de interacción cortos para alcanzar la temperatura requerida. Esto da como resultado un control estricto del patrón de calentamiento, siguiendo de cerca el campo magnético aplicado. Este control preciso ayuda a reducir la distorsión térmica y el daño al material que se está calentando.
Sin embargo, la distribución del calor y la velocidad de calentamiento pueden ser problemas potenciales en el calentamiento por inducción. Puede ocurrir una distribución desigual del calor si la bobina de inducción no tiene un contacto adecuado con el material o si el material tiene una forma o composición irregular. Es importante asegurar un acoplamiento adecuado entre la bobina de trabajo y el objeto a calentar para lograr un calentamiento uniforme.
La velocidad de calentamiento también puede verse influenciada por factores como el tamaño y el material del objeto, así como la profundidad de penetración del campo electromagnético. Comprender estos factores y su impacto en el proceso de calentamiento es crucial para lograr los resultados deseados en las aplicaciones de calentamiento por inducción.
En general, el calentamiento inductivo es un método versátil y eficiente para calentar materiales eléctricamente conductores. Sus ventajas en términos de velocidad, eficiencia energética y controlabilidad lo convierten en una opción popular en diversas industrias, incluida la metalurgia, la fabricación de semiconductores y la fundición de oro. Al considerar los requisitos y desafíos específicos de cada aplicación, las empresas pueden tomar decisiones informadas al utilizar la tecnología de calentamiento inductivo.
Calentamiento por resistencia indirecta
El calentamiento por resistencia indirecta es una tecnología utilizada en hornos eléctricos que implica calentar un molde o una carga utilizando elementos calefactores de grafito. El calor se genera haciendo pasar una corriente eléctrica a través de estos elementos, que luego transfieren el calor al molde mediante convección. Este proceso se conoce como calentamiento por resistencia indirecta.
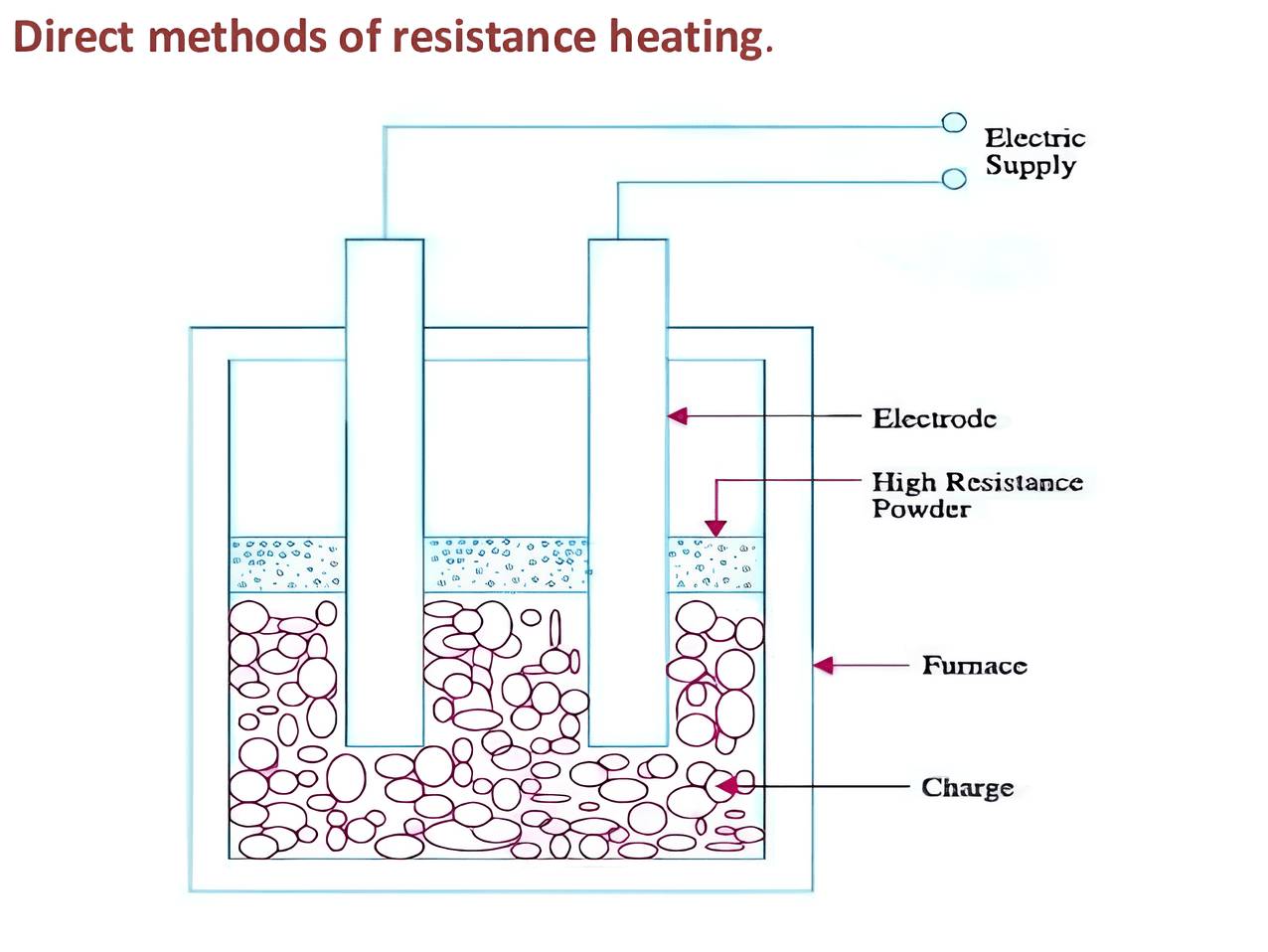
Proceso y funcionamiento del calentamiento por resistencia indirecta.
En el calentamiento por resistencia indirecta, el molde se coloca en una cámara de calentamiento donde se ubican los elementos calefactores de grafito. Estos elementos se calientan mediante la corriente eléctrica que los atraviesa. El calor generado por los elementos calefactores se transfiere luego al molde mediante convección, lo que da como resultado el calentamiento del molde.
Ventajas y desventajas del calentamiento por resistencia indirecta
Una de las ventajas del calentamiento por resistencia indirecta es la capacidad de alcanzar altas temperaturas. La temperatura alcanzada es independiente de la conductividad del molde y no se ve afectada por el calor ni la presión. Sin embargo, una de las principales desventajas del calentamiento por resistencia indirecta es el tiempo que lleva calentar el molde. La transferencia de calor desde la atmósfera del horno a la superficie del molde y a lo largo de toda la sección transversal del molde es relativamente lenta.
Historia e interés actual en el calentamiento por resistencia
El calentamiento por resistencia se ha utilizado durante muchos años en diversas aplicaciones. Se utiliza comúnmente en electrodomésticos como cocinas eléctricas y tostadoras. En los últimos años, ha habido un interés creciente en el calentamiento por resistencia para aplicaciones industriales, como la tecnología de prensado en caliente. El calentamiento por inducción y la técnica de sinterización asistida en campo (FAST)/prensado directo en caliente son otros métodos de calentamiento que se utilizan junto con el calentamiento por resistencia.
Los elementos calefactores de resistencia, como cables o cintas de resistencia, se utilizan comúnmente en diversos dispositivos calefactores y hornos industriales. Estos elementos convierten la energía eléctrica en calor mediante calentamiento Joule. La resistencia encontrada por la corriente eléctrica que pasa a través del elemento da como resultado el calentamiento del elemento.
En conclusión, el calentamiento por resistencia indirecta es una tecnología que utiliza elementos calefactores de grafito para calentar un molde o una carga mediante convección. Ofrece ventajas como altas temperaturas alcanzables, independientemente de la conductividad del molde y del calor/presión. Sin embargo, tiene el inconveniente de una transferencia de calor relativamente lenta. Los elementos calefactores de resistencia, como los cables de resistencia, se utilizan comúnmente en diversos dispositivos calefactores y hornos industriales.
Técnica de sinterización asistida en campo (FAST) / Prensado directo en caliente
Concepto y ejecución de FAST
La tecnología de sinterización asistida en campo/sinterización por plasma por chispa (FAST/SPS) utiliza una corriente eléctrica de CC para calentar directamente el molde y/o la muestra mediante calentamiento Joule. Este calentamiento directo permite lograr altas velocidades de calentamiento y bajos tiempos de ciclo de procesamiento. También permite la consolidación de una amplia gama de materiales metálicos, cerámicos y funcionales. FAST/SPS ofrece nuevas posibilidades para fabricar materiales con características potencialmente extraordinarias. También puede procesar compuestos de múltiples materiales, materiales de grado funcional y de unión por difusión.
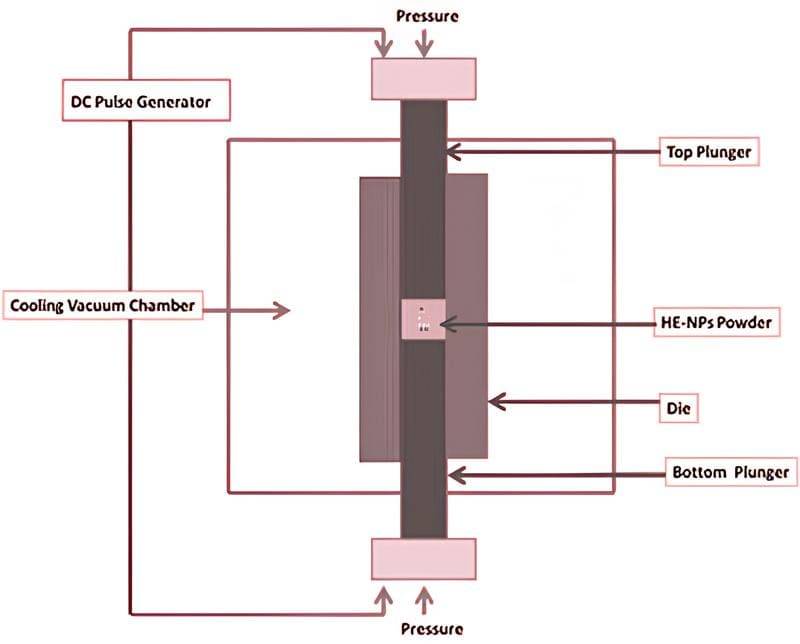
Razones para acortar el tiempo del ciclo
La razón de peso para acortar el tiempo del ciclo en el prensado directo en caliente es evitar el crecimiento del grano y ahorrar energía. En el prensado directo en caliente, el molde se conecta directamente a la energía eléctrica, generando calor en el molde a través de la resistividad del molde y la parte del polvo. Esto da como resultado velocidades de calentamiento muy altas y aumenta significativamente la actividad de sinterización de agregados de polvo metálico fino. Se hacen posibles tiempos de ciclo cortos de unos pocos minutos y el proceso reduce el umbral de temperatura y presión de sinterización en comparación con las técnicas de sinterización convencionales. El calentamiento por resistencia directa garantiza que el calor se genere donde se necesita.
Beneficios del prensado directo en caliente
El prensado directo en caliente ofrece varios beneficios en comparación con las técnicas de sinterización de pulvimetalurgia convencionales. Permite la producción de propiedades únicas mediante el uso de temperaturas de procesamiento más bajas y/o tiempos de procesamiento más cortos. Permite la sinterización por prensado en caliente de polvos metálicos y cerámicos, la preparación de compuestos cerámicos/metálicos y compuestos intermetálicos, y la investigación y el desarrollo de procesos de soldadura por difusión. También facilita la sinterización por densificación en caliente de compuestos de oxígeno/nitrógeno/boro/carbono y sus mezclas.
Diferencias entre sinterizar con corriente pulsada o no pulsada
Las últimas investigaciones sugieren que no existe una diferencia básica entre la sinterización con corriente pulsada o no pulsada (SPS o FAST). En principio, todas las técnicas de prensado directo en caliente pueden lograr mejores resultados de sinterización en comparación con el prensado en caliente convencional si la mejora se debe únicamente al calentamiento in situ del polvo. Sin embargo, si están presentes efectos físicos adicionales asociados con la propia densidad de corriente eléctrica, una corriente pulsada frecuentemente tiene efectos beneficiosos adicionales. Esto se debe a que durante cada pulso, la densidad de corriente eléctrica alcanza un máximo de un valor significativamente más alto que una corriente continua con una potencia de calentamiento comparable.
En resumen, la técnica de sinterización asistida en campo (FAST) o prensado directo en caliente utilizando una corriente eléctrica directa ofrece numerosas ventajas en términos de tiempos de ciclo de procesamiento más cortos, temperaturas y presiones más bajas y la capacidad de producir propiedades únicas en una amplia gama de materiales. Ya sea que se utilice corriente pulsada o no pulsada, la técnica de prensado directo en caliente puede lograr mejores resultados de sinterización en comparación con los métodos convencionales.
Aplicaciones del prensado en caliente
Fabricación de artículos críticos como objetivos de pulverización catódica y componentes cerámicos de alto rendimiento.
La tecnología de prensado en caliente se ha utilizado con éxito en la fabricación de artículos críticos, como objetivos de pulverización catódica y componentes cerámicos de alto rendimiento. Mediante este proceso se han obtenido materiales como carburo de boro, diboruro de titanio y sialón. Al utilizar polvo metálico, la conductividad del molde permite un calentamiento rápido de la pieza de trabajo. Este método es especialmente adecuado para aplicaciones que requieren altas velocidades de calentamiento, lo que lo hace ideal para materiales que solo pueden mantenerse a altas temperaturas brevemente o para procesos que requieren velocidades de calentamiento rápidas para una alta productividad.
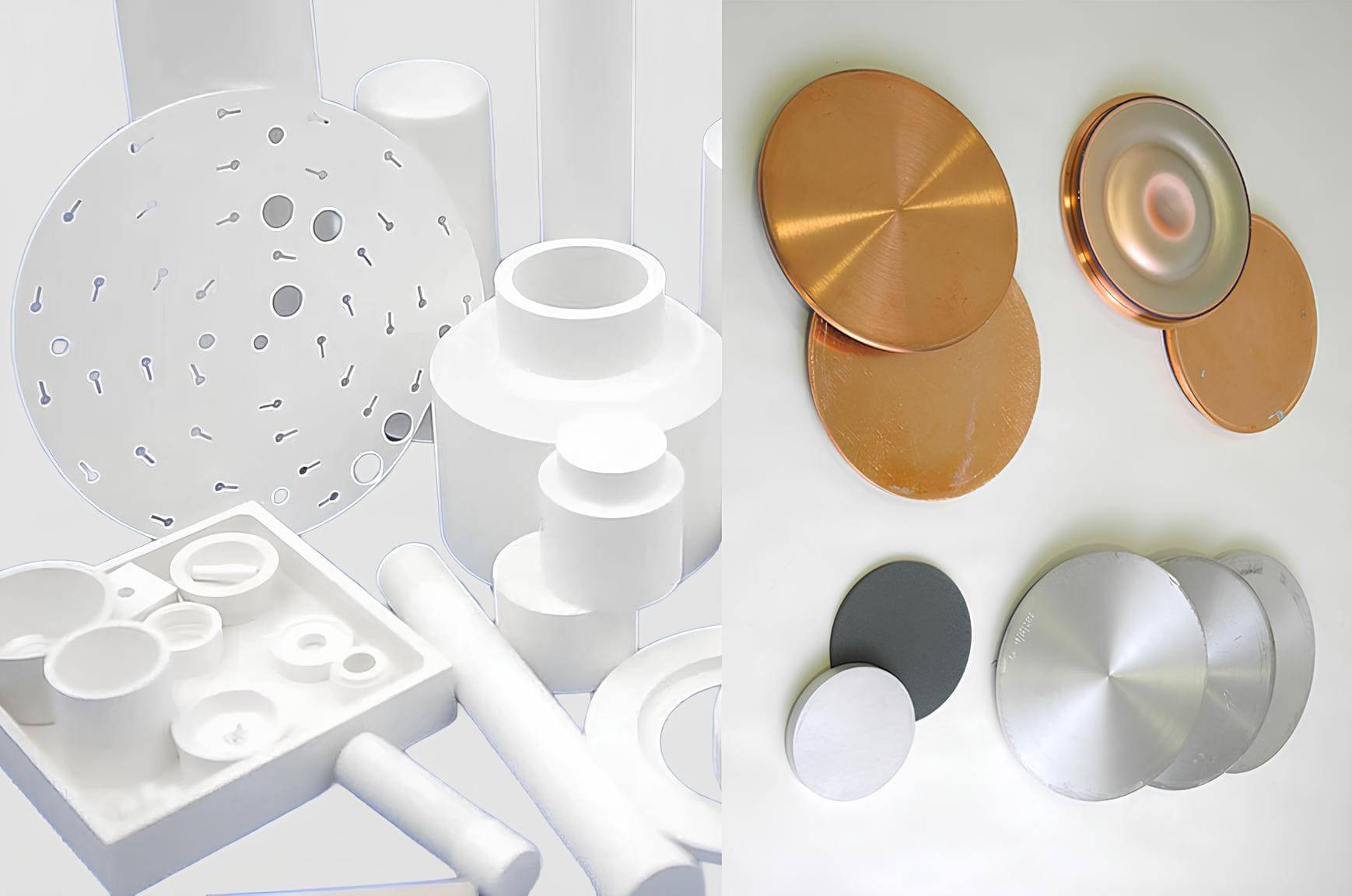
Beneficios de usar polvo metálico
Una de las ventajas de utilizar polvo metálico en el proceso de prensado en caliente es que permite un calentamiento rápido de la pieza de trabajo. Los moldes con un diámetro grande y una altura relativamente pequeña se pueden calentar rápidamente, lo que aumenta la eficiencia y la productividad. Además, el uso de polvo metálico elimina la necesidad de aglutinantes en el proceso de fabricación, lo que permite una unión completa de las piezas mediante una combinación de fuerza y temperatura.
Idoneidad del proceso para altas velocidades de calentamiento.
El proceso de prensado en caliente es particularmente adecuado para aplicaciones que requieren altas velocidades de calentamiento. Esto es beneficioso para materiales que solo pueden mantenerse brevemente a altas temperaturas o para procesos que requieren velocidades de calentamiento rápidas para lograr una alta productividad. La combinación de fuerza y temperatura en el prensado en caliente permite una unión rápida y eficiente de las piezas.
Papel del prensado directo en caliente en la industria de materiales de fricción.
La tecnología de prensado directo en caliente juega un papel importante en la industria de materiales de fricción. Permite sinterizar materiales hasta su densidad final, logrando un alto nivel de precisión casi neta. Esta precisión a menudo elimina la necesidad de reelaboración mecánica de materiales que son difíciles de procesar. El prensado directo en caliente es particularmente útil para materiales que requieren un alto nivel de densidad y precisión en su forma final.
Aplicaciones de pastillas de freno y discos de embrague sinterizados
El prensado en caliente se utiliza habitualmente en la producción de pastillas de freno y discos de embrague sinterizados. El proceso permite la creación de materiales densos y de alto rendimiento que ofrecen capacidades superiores de frenado y embrague. Las pastillas de freno y los discos de embrague sinterizados son conocidos por su durabilidad, resistencia al calor y rendimiento constante, lo que los hace muy valorados en la industria automotriz.
En conclusión, el prensado en caliente es un proceso versátil y valioso que encuentra aplicaciones en diversas industrias. Es particularmente útil en la fabricación de artículos críticos como objetivos de pulverización catódica y componentes cerámicos de alto rendimiento. El uso de polvo metálico en prensado en caliente ofrece beneficios como calentamiento rápido y eliminación de aglutinantes. El proceso es adecuado para altas velocidades de calentamiento y desempeña un papel importante en la industria de materiales de fricción. Además, el prensado en caliente se utiliza ampliamente en la producción de pastillas de freno y discos de embrague sinterizados, lo que proporciona un rendimiento y una durabilidad superiores en aplicaciones automotrices.
CONTÁCTANOS PARA UNA CONSULTA GRATUITA
Los productos y servicios de KINTEK LAB SOLUTION han sido reconocidos por clientes de todo el mundo. Nuestro personal estará encantado de ayudarle con cualquier consulta que pueda tener. ¡Contáctenos para una consulta gratuita y hable con un especialista del producto para encontrar la solución más adecuada para sus necesidades de aplicación!