La sinterización es un proceso crítico en la pulvimetalurgia y la fabricación de cerámica, en el que los materiales en polvo se transforman en cuerpos densos y sólidos mediante la aplicación de calor y presión, normalmente por debajo del punto de fusión del material.Este proceso implica varias etapas, incluida la formación de una pieza verde, la eliminación del agente aglutinante y la sinterización propiamente dicha, en la que las partículas se fusionan.La máquina de sinterización desempeña un papel fundamental en el control de la temperatura, la atmósfera y la presión para garantizar que se consiguen las propiedades deseadas del material.Los componentes clave del proceso de sinterización incluyen materias primas como polvos que contienen hierro, agentes fundentes y combustible, que deben cumplir criterios específicos para una sinterización eficaz.
Explicación de los puntos clave:
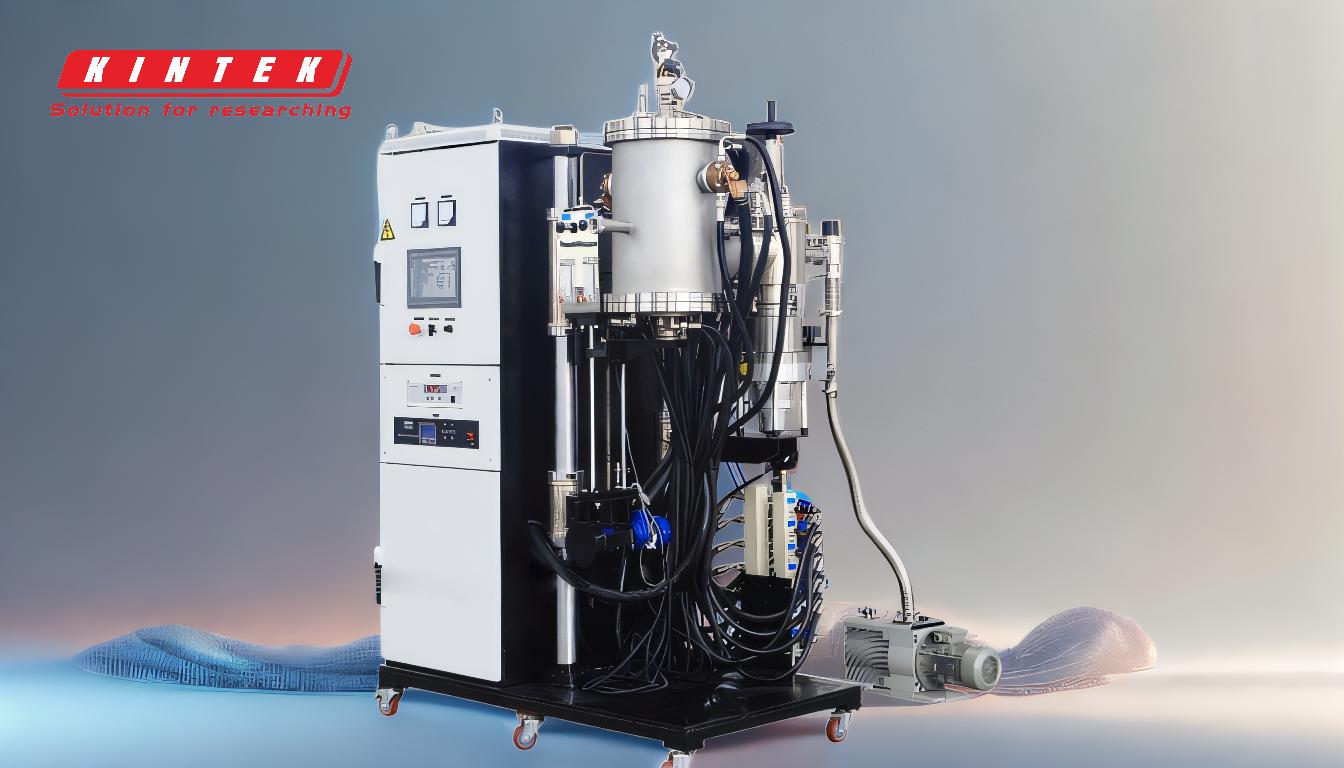
-
Definición y finalidad de la sinterización:
- La sinterización es un proceso que compacta y forma una masa sólida de material aplicando calor o presión sin alcanzar el punto de fusión del material.
- Se utiliza para crear materiales densos y de alta resistencia a partir de formas pulverulentas, normalmente en pulvimetalurgia y fabricación de cerámica.
-
Etapas del proceso de sinterización:
- Formación de la pieza verde: Se da la forma deseada a una mezcla de polvo primario y un agente adhesivo (como cera o polímero).
- Eliminación del agente adhesivo: Durante el calentamiento, el agente adhesivo se evapora o se quema.
- Sinterización: La temperatura se incrementa hasta un punto en el que las partículas comienzan a fusionarse en sus superficies, ya sea por fusión parcial o a través de un agente de unión intermedio.
-
Componentes de las materias primas de sinterización
- Materias primas que contienen hierro: Incluyen polvo de mineral con alto contenido en hierro, concentrado de hierro y otros materiales ricos en hierro.
- Agentes fundentes: Deben tener un alto contenido de CaO válido, pocas impurezas y un contenido de agua y tamaño de partícula específicos.
- Combustible: Típicamente incluye polvo de coque y carbón sin humo, que debe tener un alto contenido de carbono fijo, baja ceniza y bajo contenido de azufre.
-
Pasos clave en la operación de sinterización:
- Colocación: Consiste en colocar el fondo y mezclar los materiales en la máquina de sinterización.
- Ignición: La superficie del compartimento del carro se enciende y se mantiene a una temperatura elevada adecuada.
- Sinterización: Requiere un control preciso del volumen de aire, el vacío, el grosor de la capa, la velocidad y el punto final de sinterización para garantizar unos resultados óptimos.
-
Horno de sinterización por atmósfera:
- Este tipo de horno controla la atmósfera (como nitrógeno o argón) para optimizar el entorno de sinterización.
- Incluye dispositivos de calentamiento, mecanismos de presión, cámaras de sinterización y sistemas de control de gases.
- La atmósfera controlada permite la migración del material, el movimiento de los límites de grano, la eliminación de poros y la contracción, lo que da como resultado un cuerpo cerámico denso con propiedades de resistencia específicas.
-
Ventajas de la sinterización:
- Produce materiales con propiedades mecánicas mejoradas, como una mayor resistencia y durabilidad.
- Permite crear formas y estructuras complejas que serían difíciles de conseguir mediante los procesos tradicionales de fusión y fundición.
- Adecuado para materiales con puntos de fusión extremadamente altos, como el wolframio y el molibdeno.
Comprendiendo estos puntos clave, se puede apreciar la complejidad y precisión requeridas en el proceso de sinterización, así como el papel crítico que desempeñan las máquinas de sinterización en la consecución de las propiedades deseadas del material.
Cuadro sinóptico:
Aspecto | Detalles |
---|---|
Definición | Compactación de materiales en polvo utilizando calor/presión por debajo del punto de fusión. |
Etapas | Formación de la pieza verde, eliminación del agente adhesivo y fusión de las partículas. |
Componentes clave | Polvos que contienen hierro, agentes de fusión y combustible. |
Operación de sinterización | Paño, ignición y control preciso del aire, el vacío y la temperatura. |
Sinterización en atmósfera | Entorno controlado para la migración del material, la eliminación de poros y la contracción. |
Ventajas | Mayor resistencia, formas complejas e idoneidad para materiales de alta fusión. |
Descubra cómo el sinterizado puede transformar su proceso de fabricación. contacte con nuestros expertos hoy mismo ¡!