La deposición en vacío es una técnica versátil utilizada para depositar películas finas o revestimientos sobre superficies en un entorno controlado, normalmente en condiciones de vacío. El grosor de la capa depositada puede variar significativamente, desde una sola capa atómica (nanómetros) hasta varios milímetros, dependiendo del proceso específico, los materiales y los parámetros implicados. Factores como la duración del proceso, los niveles de energía, las propiedades de los materiales y las condiciones ambientales (por ejemplo, la presión de vacío o la temperatura) desempeñan un papel fundamental a la hora de determinar el grosor final y la calidad de la película depositada. Esta técnica se utiliza ampliamente en industrias que requieren un control preciso de las propiedades de las películas, como la electrónica, la óptica y los revestimientos.
Explicación de los puntos clave:
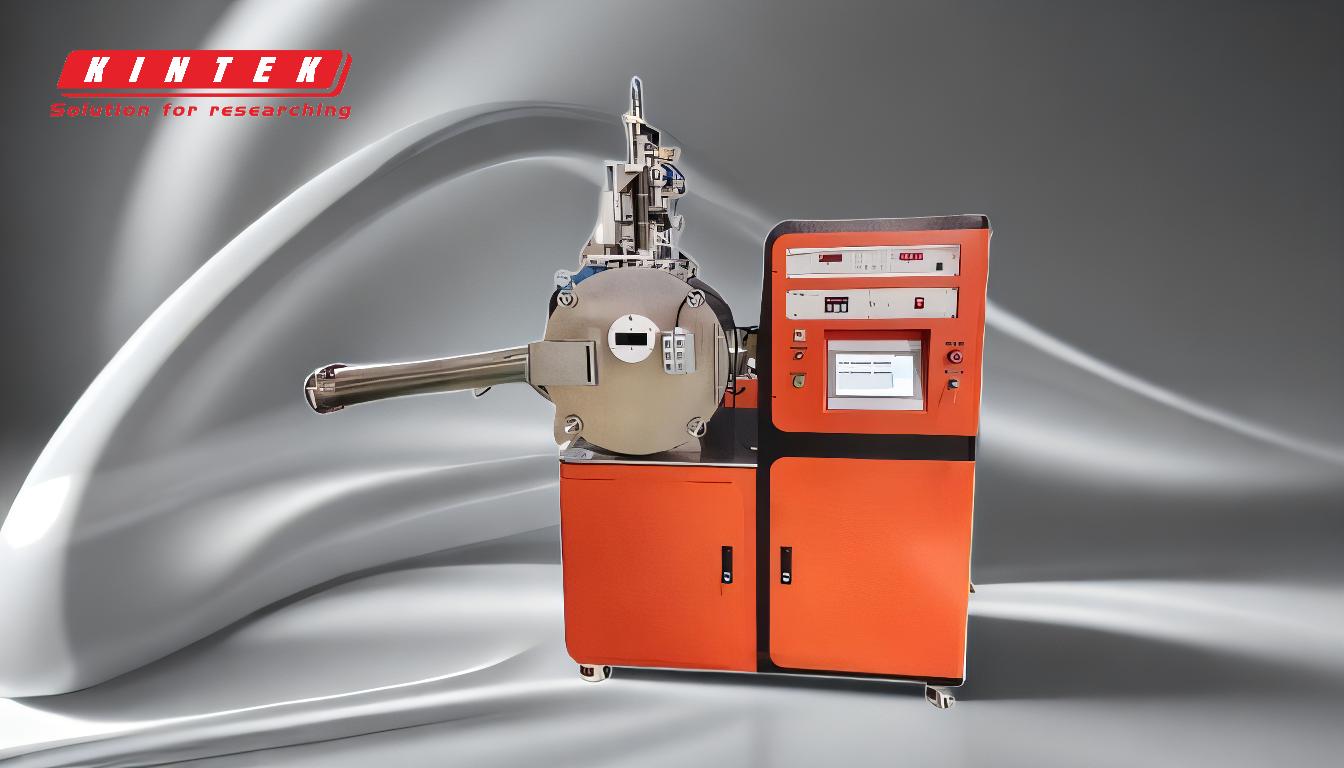
-
Gama de espesores en la deposición al vacío:
- La deposición al vacío puede producir películas con espesores que van desde una sola capa atómica (escala nanométrica) hasta varios milímetros.
-
Por ejemplo:
- Escala atómica/molecular: En procesos como la deposición física de vapor (PVD) o la deposición química de vapor a baja presión (LPCVD), las capas se depositan átomo a átomo o molécula a molécula, lo que da lugar a películas extremadamente finas (nanómetros).
- Escala macroscópica: En algunas aplicaciones, como los revestimientos protectores o los acabados decorativos, pueden depositarse capas más gruesas (de micrómetros a milímetros).
-
Factores que influyen en el grosor:
-
El grosor de la película depositada depende de varios factores clave:
- Duración del proceso: Los tiempos de deposición más largos suelen dar lugar a películas más gruesas.
- Niveles de energía: Los niveles de energía más elevados de las partículas de revestimiento (por ejemplo, de decenas a miles de electronvoltios en la pulverización catódica) pueden aumentar la velocidad de deposición y afectar al espesor.
- Propiedades de los materiales: La masa y el peso molecular del material de partida influyen en la rapidez con que se evapora o chisporrotea, lo que repercute en el espesor.
- Presión de vacío: Un mayor grado de vacío mejora el camino libre de las moléculas del material fuente, lo que conduce a una deposición más uniforme y controlada.
- Preparación del sustrato: La rugosidad de la superficie y la limpieza del sustrato pueden afectar a la uniformidad y adherencia de la película depositada.
-
El grosor de la película depositada depende de varios factores clave:
-
Consideraciones específicas del proceso:
- Pulverización catódica: El espesor del metal depositado en sputtering depende de la duración del ciclo y de la potencia aplicada al blanco. A mayor potencia y ciclos más largos se obtienen películas más gruesas.
- Evaporación térmica: En este proceso, la velocidad de evaporación del material de partida, junto con la presión de vacío y la velocidad de rotación del sustrato, determinan el grosor y la uniformidad de la película.
- Deposición química en fase vapor (CVD): En el LPCVD, la velocidad de deposición y el espesor están influidos por las reacciones químicas que se producen en la superficie del sustrato, así como por las condiciones de temperatura y presión.
-
Calidad y rendimiento de las películas finas:
-
La calidad de la película depositada es fundamental para su rendimiento en las aplicaciones. Los factores clave que afectan a la calidad son:
- Pureza del material original: Las impurezas pueden provocar defectos en la película.
- Temperatura y presión de deposición: Un control adecuado garantiza películas uniformes y de alta calidad.
- Preparación de la superficie del sustrato: Una superficie de sustrato lisa y limpia favorece una deposición uniforme y una fuerte adherencia.
-
La calidad de la película depositada es fundamental para su rendimiento en las aplicaciones. Los factores clave que afectan a la calidad son:
-
Aplicaciones e implicaciones:
-
La deposición en vacío se utiliza en una amplia gama de industrias, entre ellas:
- Electrónica: Para crear transistores de película fina, dispositivos semiconductores y capas conductoras.
- Óptica: Para revestimientos antirreflectantes, espejos y filtros ópticos.
- Revestimientos: Para acabados resistentes al desgaste, a la corrosión y decorativos.
- La capacidad de controlar el grosor de la película a nivel atómico hace de la deposición al vacío una tecnología fundamental para la fabricación y la investigación avanzadas.
-
La deposición en vacío se utiliza en una amplia gama de industrias, entre ellas:
Al comprender estos puntos clave, los compradores de equipos y consumibles pueden tomar decisiones informadas sobre los materiales y procesos necesarios para conseguir espesores de película y propiedades específicas para sus aplicaciones.
Cuadro recapitulativo:
Aspecto | Detalles |
---|---|
Gama de espesores | De nanómetros (escala atómica) a milímetros (escala macroscópica) |
Factores clave | Duración del proceso, niveles de energía, propiedades del material, presión de vacío, preparación del sustrato |
Ejemplos de procesos | Pulverización catódica, evaporación térmica, depósito químico en fase vapor (CVD) |
Aplicaciones | Electrónica (transistores, semiconductores), Óptica (espejos, filtros), Recubrimientos (antidesgaste, decorativos) |
¿Necesita soluciones precisas de deposición en vacío? Contacte hoy mismo con nuestros expertos para hablar de sus necesidades