La soldadura fuerte, aunque es un método de unión versátil y eficaz, presenta varios inconvenientes y limitaciones que deben tenerse en cuenta, sobre todo para los compradores de equipos y consumibles.Entre ellas se incluyen la necesidad de una gran limpieza del metal base, un diseño cuidadoso y consideraciones de fabricación, la necesidad de ajustes estrechos para facilitar la acción capilar y el posible recocido de los componentes durante el proceso.Estos factores pueden aumentar la complejidad, el coste y el tiempo de producción, por lo que es esencial evaluar si la soldadura fuerte es el método más adecuado para una aplicación determinada.
Explicación de los puntos clave:
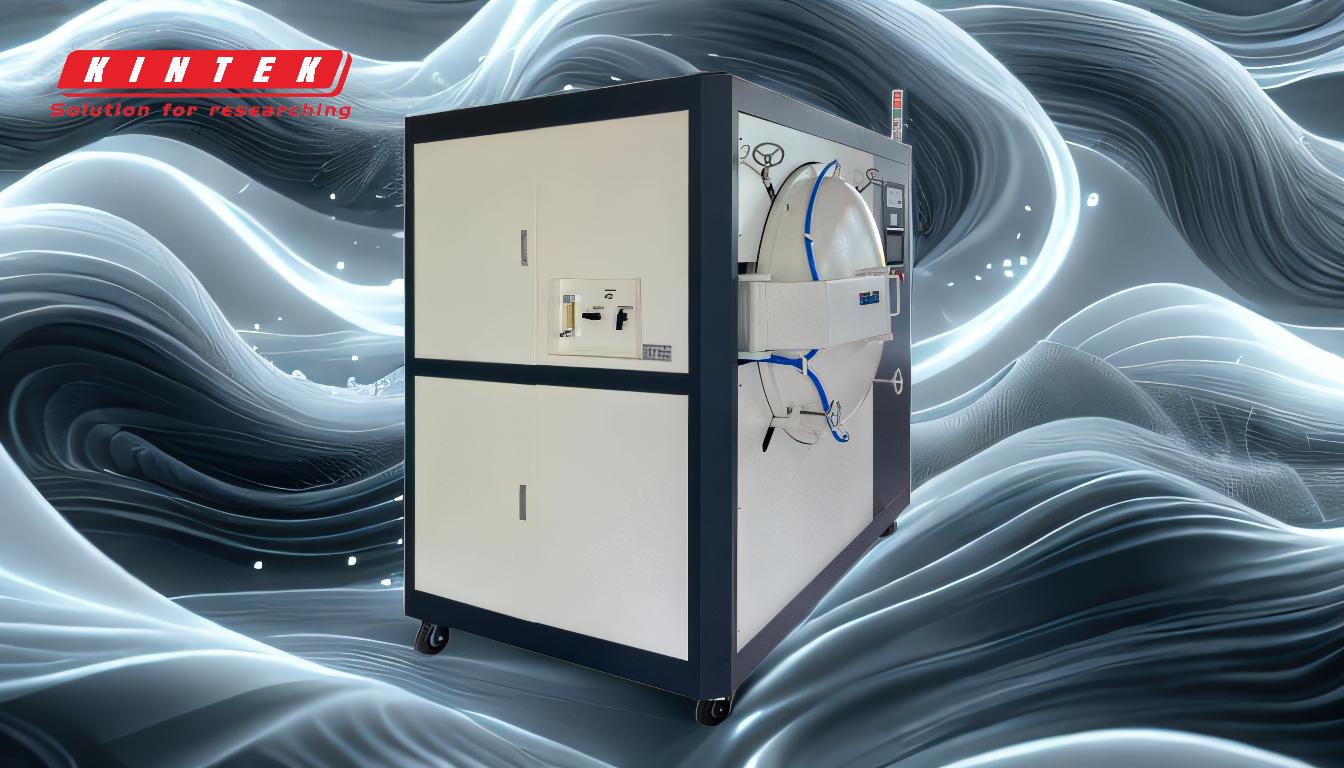
-
Alto grado de limpieza del metal base:
- La soldadura fuerte requiere que los metales base estén excepcionalmente limpios para garantizar una adhesión y un flujo adecuados del material de aportación.Contaminantes como aceites, óxidos o suciedad pueden perjudicar considerablemente el proceso de soldadura fuerte, provocando uniones débiles o defectos.
- Esto requiere pasos adicionales de limpieza previa, como la limpieza química o los procesos abrasivos, que pueden aumentar el tiempo y los costes de producción.Para los compradores, esto significa invertir en equipos de limpieza o consumibles, lo que aumenta el gasto total.
-
Consideraciones sobre diseño y fabricación:
- La soldadura fuerte exige una planificación meticulosa del diseño y la fabricación.Los componentes deben diseñarse para adaptarse al proceso de soldadura fuerte, incluida la colocación del material de relleno y la creación de juntas que faciliten la acción capilar.
- Esto requiere a menudo una estrecha colaboración entre los ingenieros de diseño y los equipos de fabricación, lo que puede ralentizar los plazos de producción.Los compradores deben tener en cuenta estas limitaciones de diseño al seleccionar la soldadura fuerte como método de unión.
-
Ajustes estrechos por capilaridad:
- La soldadura fuerte se basa en la acción capilar para introducir el material de relleno en la unión.Esto requiere tolerancias extremadamente estrechas entre las piezas que se unen, lo que puede ser difícil de conseguir de forma consistente.
- Conseguir estos ajustes tan estrechos puede requerir un mecanizado de precisión o herramientas especializadas, lo que aumenta aún más los costes y la complejidad.Para los compradores, esto significa asegurarse de que sus proveedores pueden cumplir estas estrechas tolerancias, lo que puede limitar el grupo de proveedores disponibles.
-
Recocido de componentes:
- Las altas temperaturas utilizadas en la soldadura fuerte pueden provocar el recocido de los componentes, sobre todo si están fabricados con materiales sensibles al calor.El recocido puede alterar las propiedades mecánicas del metal base, como reducir su dureza o resistencia.
- Esto puede requerir tratamientos térmicos posteriores a la soldadura fuerte para restaurar las propiedades deseadas, lo que añade otro paso al proceso de fabricación.Los compradores deben considerar si los materiales de base pueden soportar el proceso de soldadura fuerte sin comprometer sus prestaciones.
-
Limitaciones de los materiales:
- No todos los materiales son adecuados para la soldadura fuerte.Algunos metales, como ciertas aleaciones de alta temperatura o aquellos con alta conductividad térmica, pueden no formar uniones fuertes con los materiales de aportación convencionales para la soldadura fuerte.
- Esto limita la aplicabilidad de la soldadura fuerte en determinadas industrias o para componentes específicos.Los compradores deben evaluar cuidadosamente la compatibilidad de sus materiales con el proceso de soldadura fuerte.
-
Costes y plazos:
- Los pasos adicionales necesarios para la limpieza, el mecanizado de precisión y los posibles tratamientos posteriores a la soldadura fuerte pueden aumentar significativamente tanto el coste como el tiempo necesario para la producción.
- Para los compradores, esto significa mayores costes iniciales y plazos de entrega potencialmente más largos, que deben sopesarse con las ventajas de la soldadura fuerte, como juntas fuertes y estancas.
-
Accesibilidad de las juntas:
- La soldadura fuerte requiere acceso a la zona de unión para aplicar calor y material de relleno.En ensamblajes o componentes complejos con accesibilidad limitada, esto puede suponer un reto importante.
- Esto puede hacer necesario el uso de equipos o técnicas especializadas, como la soldadura por inducción o la soldadura al vacío, que pueden aumentar aún más los costes y la complejidad.
-
Consideraciones medioambientales y de seguridad:
- El proceso de soldadura fuerte implica a menudo el uso de fundentes u otros productos químicos para favorecer la humectación y el flujo del material de aportación.Estas sustancias pueden suponer riesgos para el medio ambiente y la seguridad, y requieren una manipulación, almacenamiento y eliminación adecuados.
- Los compradores deben asegurarse de que sus instalaciones están equipadas para manipular estos materiales de forma segura, lo que puede requerir inversiones adicionales en equipos de seguridad o formación.
En conclusión, aunque la soldadura fuerte ofrece varias ventajas, como la capacidad de unir metales distintos y crear uniones fuertes y duraderas, también tiene desventajas y limitaciones importantes.Entre ellas, la necesidad de una gran limpieza del metal base, consideraciones de diseño y fabricación cuidadosas, ajustes estrechos para la acción capilar, posible recocido de los componentes, limitaciones de material, implicaciones de coste y tiempo, problemas de accesibilidad a las uniones y consideraciones medioambientales y de seguridad.Los compradores deben sopesar cuidadosamente estos factores frente a las ventajas de la soldadura fuerte para determinar si es el método de unión más adecuado para su aplicación específica.
Cuadro sinóptico:
Desventaja | Descripción |
---|---|
Alta limpieza del metal base | Requiere una limpieza excepcional para garantizar la correcta adhesión y fluidez de la masilla. |
Diseño y fabricación | Exige una planificación y colaboración meticulosas, lo que puede ralentizar la producción. |
Ajustes estrechos para la acción capilar | Requiere tolerancias estrechas, lo que aumenta los costes de mecanizado y la complejidad. |
Recocido de componentes | Las altas temperaturas pueden alterar las propiedades mecánicas, lo que requiere un tratamiento posterior. |
Limitaciones de los materiales | No todos los materiales son aptos para la soldadura fuerte, lo que limita su aplicabilidad. |
Costes y plazos | Los pasos adicionales aumentan el tiempo y los costes de producción. |
Accesibilidad a las juntas | El acceso limitado a las juntas puede complicar el proceso. |
Preocupaciones medioambientales y de seguridad | El uso de fundentes y productos químicos requiere una manipulación adecuada y medidas de seguridad. |
¿Necesita ayuda para decidir si la soldadura fuerte es adecuada para su aplicación? Póngase en contacto con nuestros expertos hoy mismo ¡!