El endurecimiento es un proceso que se utiliza para aumentar la dureza y resistencia de los materiales, generalmente metales, mediante tratamiento térmico u otros métodos. Si bien ofrece importantes ventajas, como una mayor resistencia al desgaste y durabilidad, también presenta varias desventajas. Estos incluyen mayor fragilidad, ductilidad reducida, potencial de agrietamiento y limitaciones en la selección de materiales. Además, el proceso puede ser costoso, llevar mucho tiempo y puede introducir tensiones residuales que afecten el rendimiento del material. Comprender estos inconvenientes es crucial para tomar decisiones informadas en la selección y aplicación de materiales.
Puntos clave explicados:
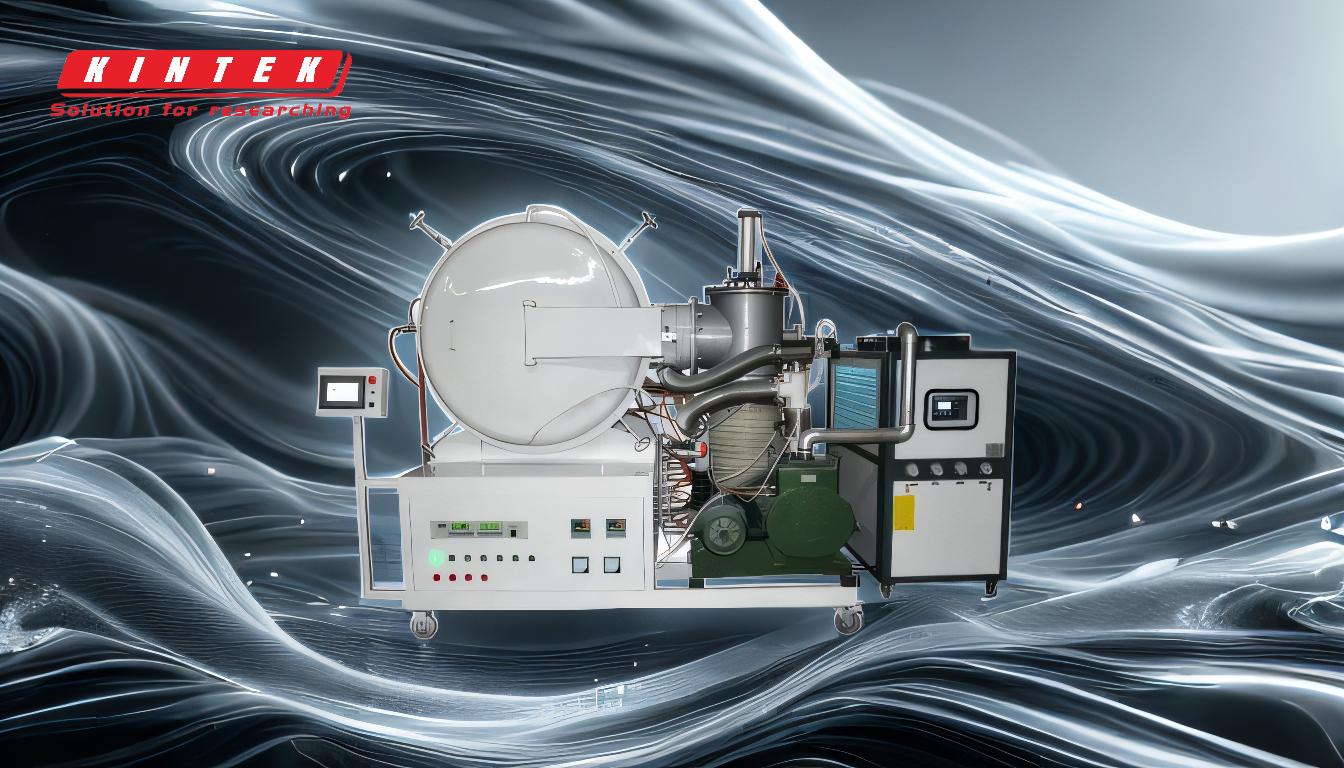
-
Mayor fragilidad:
- El endurecimiento a menudo conduce a un aumento significativo de la fragilidad, lo que hace que el material sea más propenso a fallar repentinamente bajo impacto o tensión.
- Esto es particularmente problemático en aplicaciones donde el material está sujeto a cargas dinámicas o impactos.
-
Ductilidad reducida:
- El proceso de endurecimiento generalmente reduce la ductilidad del material, lo que significa que se vuelve menos capaz de sufrir deformación plástica sin romperse.
- Esta reducción de la ductilidad puede limitar la capacidad del material para absorber energía, haciéndolo inadecuado para aplicaciones que requieren flexibilidad.
-
Potencial de agrietamiento:
- Durante el proceso de endurecimiento, especialmente en métodos de enfriamiento rápido como el temple, existe un alto riesgo de agrietamiento debido a tensiones térmicas.
- Las grietas pueden comprometer la integridad estructural del material y provocar fallas prematuras.
-
Tensiones residuales:
- El endurecimiento puede introducir tensiones residuales dentro del material, lo que puede provocar distorsión o deformación.
- Estas tensiones también pueden reducir la vida útil del material, haciéndolo más susceptible a fallar bajo cargas cíclicas.
-
Limitaciones de materiales:
- No todos los materiales son aptos para endurecer. Es posible que algunas aleaciones y metales no respondan bien al proceso, lo que limita la variedad de materiales que pueden endurecerse de manera efectiva.
- Esto puede restringir las opciones de diseño y requerir el uso de materiales o tratamientos alternativos.
-
Consideraciones de costo y tiempo:
- El proceso de endurecimiento puede ser costoso y requerir equipos especializados y entornos controlados.
- También requiere mucho tiempo, lo que puede aumentar los plazos de producción y los costos generales.
-
Dureza superficial versus propiedades del núcleo:
- El endurecimiento a menudo da como resultado una superficie mucho más dura que el núcleo del material. Esta discrepancia puede provocar problemas como delaminación o desconchado en determinadas condiciones.
- Equilibrar la dureza de la superficie con las propiedades del núcleo es una consideración crítica en el diseño y aplicación de materiales endurecidos.
-
Preocupaciones ambientales y de seguridad:
- El proceso de endurecimiento, particularmente aquellos que involucran altas temperaturas y tratamientos químicos, pueden presentar riesgos ambientales y de seguridad.
- El manejo y eliminación adecuados de los productos químicos, así como el cumplimiento de los protocolos de seguridad, son esenciales para mitigar estos riesgos.
En resumen, si bien el endurecimiento ofrece importantes beneficios en términos de resistencia del material y resistencia al desgaste, es esencial considerar cuidadosamente sus desventajas. Estos incluyen mayor fragilidad, ductilidad reducida, potencial de agrietamiento, tensiones residuales, limitaciones de materiales, consideraciones de costo y tiempo, discrepancias en las propiedades de la superficie del núcleo y preocupaciones ambientales y de seguridad. Comprender estos inconvenientes permite tomar mejores decisiones en la selección y aplicación de materiales, asegurando que se maximicen los beneficios del endurecimiento y minimizando sus impactos negativos.
Tabla resumen:
Desventaja | Descripción |
---|---|
Mayor fragilidad | Mayor riesgo de falla repentina bajo estrés o impacto. |
Ductilidad reducida | Disminución de la capacidad de deformarse sin romperse, lo que limita la flexibilidad. |
Potencial de agrietamiento | Alto riesgo de grietas debido a tensiones térmicas durante un enfriamiento rápido. |
Tensiones residuales | Introduce tensiones internas que provocan distorsión o reducción de la vida útil. |
Limitaciones de materiales | No todos los materiales se pueden endurecer, lo que restringe las opciones de diseño. |
Consideraciones de costo y tiempo | Proceso costoso y que requiere mucho tiempo y requiere equipo especializado. |
Discrepancia superficie-núcleo | Superficie más dura en comparación con el núcleo, con riesgo de delaminación o desconchado. |
Riesgos ambientales y de seguridad | Las altas temperaturas y los productos químicos plantean problemas de seguridad y medioambientales. |
¿Necesita ayuda para seleccionar el material o proceso adecuado? Póngase en contacto con nuestros expertos hoy ¡Para soluciones personalizadas!