Los hornos de inducción, si bien son muy eficientes y versátiles para fundir metales, presentan varias desventajas notables. Uno de los principales inconvenientes es su falta de capacidad de refinación, lo que significa que los materiales de carga ya deben estar libres de óxidos y tener una composición conocida. Además, ciertos elementos de aleación pueden perderse debido a la oxidación durante el proceso de fusión, lo que requiere su readición. Estas limitaciones pueden aumentar la complejidad operativa y los costos. A continuación, exploramos estas y otras desventajas en detalle.
Puntos clave explicados:
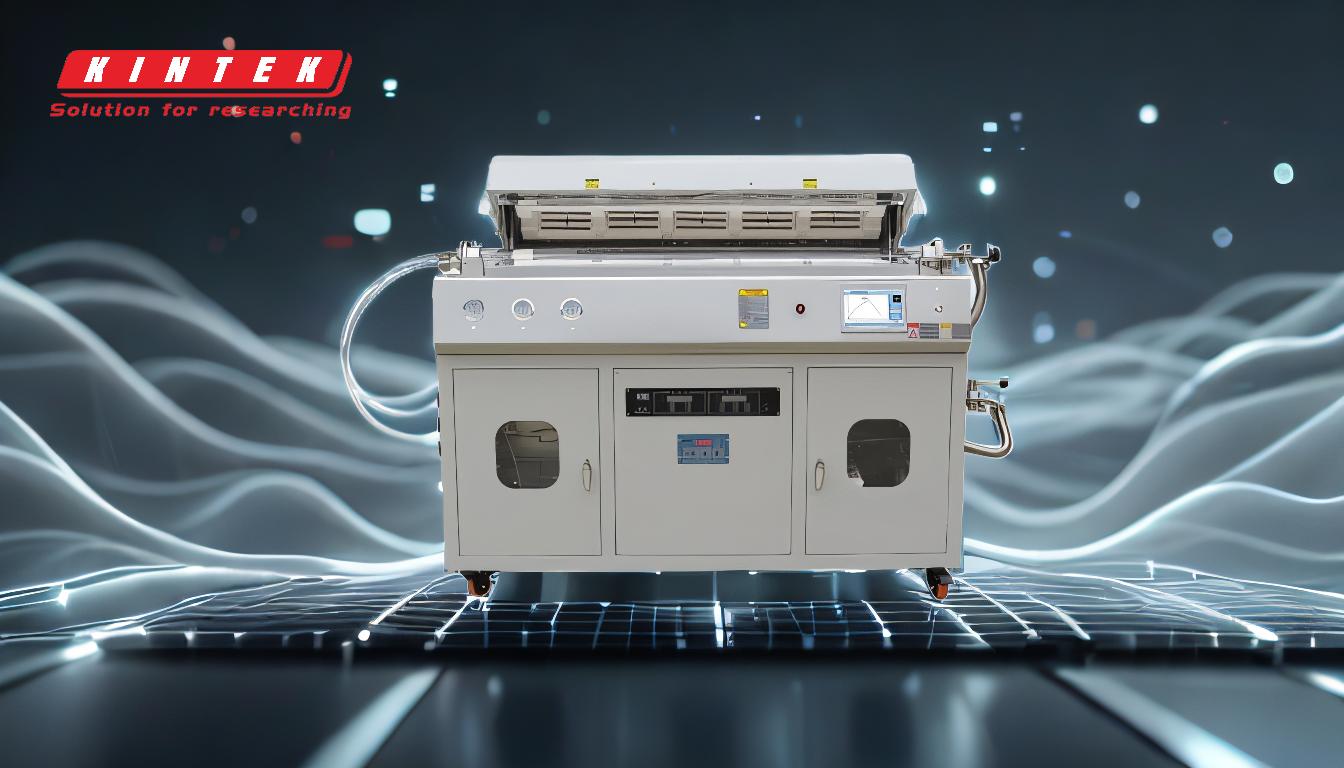
-
Falta de capacidad de refinación
- Los hornos de inducción no tienen la capacidad de refinar el metal durante el proceso de fusión. Esto significa que los materiales de carga deben estar limpios, libres de óxidos y de composición conocida antes de ser introducidos en el horno.
- Para las industrias que requieren metales de alta pureza, esta limitación puede ser un inconveniente importante, ya que requiere pasos de preprocesamiento adicionales para garantizar la calidad de los materiales de carga.
-
Oxidación y pérdida de elementos de aleación.
- Durante el proceso de fusión, ciertos elementos de aleación, como el magnesio, el aluminio y el silicio, pueden oxidarse y perderse de la masa fundida.
- Esto requiere que los operadores controlen cuidadosamente la composición de la masa fundida y vuelvan a agregar estos elementos, lo que puede aumentar tanto los costos de material como el tiempo de procesamiento.
-
Dependencia de la calidad del material de carga
- Dado que los hornos de inducción dependen de la calidad de los materiales de carga, cualquier impureza o inconsistencia en la materia prima puede afectar directamente el producto final.
- Esto dificulta el uso de desechos o materiales reciclados sin una clasificación y preparación minuciosas, lo que puede aumentar los costos operativos.
-
Altos costos operativos y de inversión inicial
- Hornos de inducción, particularmente aquellos que utilizan tecnologías avanzadas como Hornos de inducción IGBT , requieren una importante inversión inicial.
- Además, los costos operativos, incluido el consumo de electricidad y el mantenimiento, pueden ser mayores en comparación con otros tipos de hornos.
-
Capacidad limitada para la producción a gran escala
- Los hornos de inducción suelen ser más adecuados para operaciones a pequeña escala o producción por lotes. Para la producción continua a gran escala, otros tipos de hornos, como los hornos de arco, pueden ser más eficientes.
- Esta limitación puede hacer que los hornos de inducción sean menos adecuados para industrias que requieren un gran volumen de producción.
-
Complejidad en el control de temperatura
- Si bien los hornos de inducción ofrecen un control preciso de la temperatura, mantener temperaturas constantes en toda la masa fundida puede resultar un desafío, especialmente en hornos más grandes.
- Las variaciones de temperatura pueden provocar inconsistencias en el producto final, lo que requiere un seguimiento y ajuste cuidadosos.
-
Susceptibilidad a problemas de suministro de energía
- Los hornos de inducción dependen en gran medida de un suministro de energía estable y fiable. Cualquier fluctuación o interrupción en la energía puede interrumpir el proceso de fusión y potencialmente dañar el horno.
- Esto los hace menos adecuados para áreas con infraestructura eléctrica poco confiable.
-
Flexibilidad limitada para ciertos metales
- Si bien los hornos de inducción son versátiles, es posible que no sean ideales para fundir ciertos metales o aleaciones que requieren atmósferas o procesos de refinación específicos.
- Por ejemplo, los metales que requieren ambientes de vacío o gas inerte pueden no ser adecuados para hornos de inducción estándar.
-
Mantenimiento y Desgaste de Componentes
- Los componentes de un horno de inducción, como el crisol y las bobinas, están sujetos a desgaste con el tiempo.
- Se requiere un mantenimiento regular para garantizar un rendimiento óptimo y reemplazar estos componentes puede resultar costoso.
-
Preocupaciones ambientales y de seguridad
- Los hornos de inducción generan campos electromagnéticos que pueden representar riesgos de seguridad para los operadores si no están protegidos adecuadamente.
- Además, el proceso de fusión puede producir humos y emisiones, lo que requiere ventilación y controles ambientales adecuados.
En resumen, si bien los hornos de inducción ofrecen muchas ventajas, como eficiencia energética y control preciso de la temperatura, sus desventajas (incluida la falta de capacidad de refinación, la oxidación de elementos de aleación y los altos costos operativos) deben considerarse cuidadosamente al seleccionar un horno para aplicaciones específicas. . Para industrias que requieren metales de alta pureza o producción a gran escala, los tipos de hornos alternativos pueden ser más adecuados.
Tabla resumen:
Desventaja | Descripción |
---|---|
Falta de capacidad de refinación | No puede refinar metales; requiere materiales de carga limpios y libres de óxido. |
Oxidación de elementos de aleación | Pérdida de elementos como magnesio, aluminio y silicio durante la fusión. |
Dependencia de la calidad de la carga | Las impurezas en la materia prima afectan la calidad del producto final. |
Altos costos iniciales y operativos | Inversión significativa y mayores costos de electricidad/mantenimiento. |
Capacidad limitada a gran escala | Más adecuado para la producción a pequeña escala o por lotes, no a la producción continua a gran escala. |
Control de temperatura complejo | Es difícil mantener temperaturas constantes en hornos más grandes. |
Sensibilidad de la fuente de alimentación | Requiere energía estable; las interrupciones pueden alterar las operaciones. |
Flexibilidad limitada del metal | No es ideal para metales que requieren refinamiento específico o atmósferas controladas. |
Desgaste y mantenimiento de componentes | Se necesita mantenimiento regular y reemplazos costosos de componentes. |
Riesgos ambientales y de seguridad | Los campos electromagnéticos y los humos requieren protección y ventilación adecuadas. |
¿Necesita ayuda para elegir el horno adecuado para sus necesidades? Póngase en contacto con nuestros expertos hoy para asesoramiento personalizado!