La pulvimetalurgia es un proceso de fabricación versátil utilizado para producir piezas sinterizadas con formas intrincadas y dimensiones precisas.El proceso suele constar de tres pasos principales: selección del polvo, compactación y sinterización.Sin embargo, técnicas avanzadas como el moldeo por inyección de metal (MIM), el prensado isostático en caliente (HIP), la fabricación aditiva y el sinterizado por plasma de chispa (SPS) han ampliado las capacidades de la pulvimetalurgia.Estos métodos permiten la producción de componentes complejos para industrias como la automovilística, la aeroespacial y la de herramientas de corte.La elección del método depende de las propiedades deseadas del producto final, como la resistencia, la dureza y la precisión dimensional.
Explicación de los puntos clave:
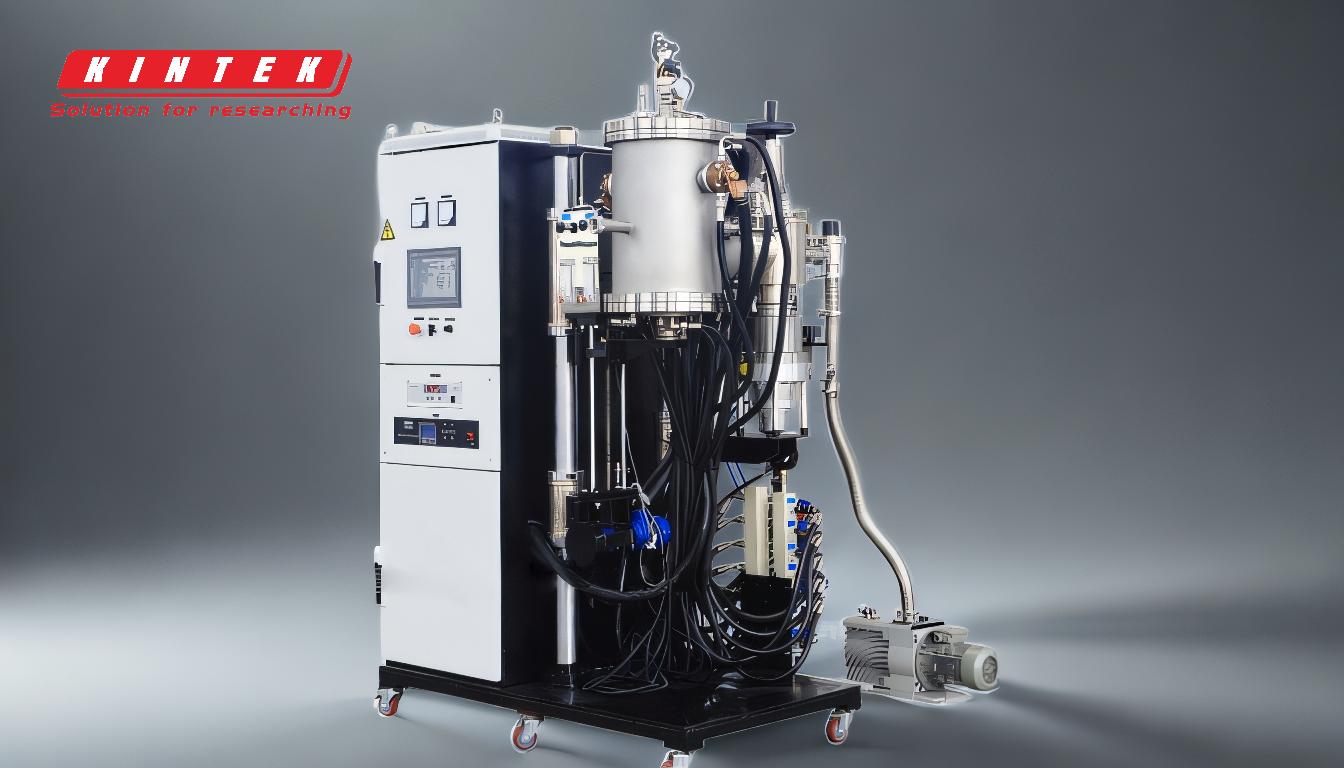
-
Pulvimetalurgia tradicional (prensado y sinterizado)
- Selección de polvos:El proceso comienza con la selección de polvos metálicos, como hierro, níquel, molibdeno o cobre, a menudo mezclados con lubricantes para mejorar el flujo y la compactación.
- Compactación:El polvo se prensa en una matriz a temperatura ambiente para formar una pieza "verde" con una resistencia inicial.Este paso determina la forma y la densidad de la pieza.
- Sinterización:La pieza verde se calienta en un horno a temperaturas justo por debajo del punto de fusión del metal.De este modo, las partículas se unen entre sí, lo que aumenta su resistencia y dureza sin licuar el material.A menudo se utilizan condiciones atmosféricas controladas para evitar la oxidación.
-
Moldeo por inyección de metal (MIM)
- Mezcla de polvos:Los polvos metálicos finos se mezclan con un aglutinante termoplástico para crear una materia prima.
- Moldeo por inyección:La materia prima se inyecta en un molde a alta presión para formar una pieza verde.
- Desmoldeo:El aglutinante se elimina mediante procesos térmicos o químicos.
- Sinterización:La pieza se sinteriza para conseguir una densidad y unas propiedades mecánicas completas.El MIM es ideal para fabricar piezas pequeñas y complejas de gran precisión.
-
Prensado isostático en caliente (HIP)
- Compactación del polvo:Los polvos metálicos se colocan en un molde y se someten simultáneamente a alta presión y temperatura.
- Sinterización:La combinación de calor y presión densifica el polvo, lo que da como resultado una pieza con forma casi de red y una porosidad mínima.El HIP se utiliza para componentes de alto rendimiento que requieren propiedades mecánicas superiores.
-
Fabricación aditiva (impresión 3D)
- Fusión de lecho de polvo:Los polvos metálicos se funden selectivamente mediante un láser o un haz de electrones para construir piezas capa a capa.
- Chorro de ligante:Se deposita selectivamente un aglutinante líquido sobre un lecho de polvo para crear una pieza verde, que posteriormente se sinteriza.
- Deposición directa de energía:El polvo metálico se introduce en un baño de fusión creado por un láser o un haz de electrones, lo que permite reparar o añadir material a piezas existentes.La fabricación aditiva es ideal para la creación de prototipos y la producción de geometrías complejas.
-
Sinterización por plasma de chispa (SPS)
- Preparación del polvo:Los polvos metálicos se colocan en una matriz de grafito.
- Sinterización:Se aplica una corriente eléctrica pulsada que genera un plasma que calienta rápidamente el polvo.La aplicación simultánea de presión produce una rápida densificación.El SPS se utiliza para materiales avanzados, incluidos los cerámicos y los compuestos, debido a su capacidad para alcanzar altas densidades a temperaturas más bajas.
-
Procesos de postratamiento
- Mecanizado:Las piezas sinterizadas pueden requerir un mecanizado adicional para conseguir dimensiones o acabados superficiales precisos.Las herramientas de diamante o el mecanizado por ultrasonidos suelen utilizarse para materiales duros como la cerámica.
- Montaje:En el caso de las piezas cerámicas, se utilizan la metalización y la soldadura fuerte para unir los componentes.Esto es habitual en aplicaciones que requieren conductividad eléctrica o sellado hermético.
- Tratamiento térmico:Pueden aplicarse tratamientos térmicos adicionales, como el revenido o la cementación en caja, para mejorar las propiedades mecánicas.
-
Aplicaciones de las piezas sinterizadas
- Industria del automóvil:Las piezas sinterizadas se utilizan ampliamente en engranajes, árboles de levas y asientos de válvulas debido a su solidez y resistencia al desgaste.
- Herramientas de corte:Las herramientas de carburo sinterizado son conocidas por su dureza y durabilidad.
- Filtros:Los filtros metálicos sinterizados se utilizan en aplicaciones que requieren una filtración precisa, como en las industrias química y farmacéutica.
Al conocer estos métodos, los fabricantes pueden seleccionar la técnica más adecuada para producir piezas sinterizadas que cumplan los requisitos específicos de rendimiento y las consideraciones de coste.
Tabla resumen:
Método | Pasos clave | Aplicaciones |
---|---|---|
Pulvimetalurgia tradicional | Selección de polvos, compactación, sinterización | Engranajes de automoción, árboles de levas, asientos de válvulas |
Moldeo por inyección de metales (MIM) | Mezcla de polvos, moldeo por inyección, desbobinado, sinterización | Piezas pequeñas y complejas de alta precisión |
Prensado isostático en caliente (HIP) | Compactación del polvo, sinterización a alta presión y temperatura | Componentes de alto rendimiento con porosidad mínima |
Fabricación aditiva | Fusión de lecho de polvo, inyección de aglutinante, deposición directa de energía | Prototipos, geometrías complejas |
Sinterización por plasma de chispa (SPS) | Preparación de polvos, sinterización rápida con corriente eléctrica pulsada y presión | Materiales avanzados como cerámicas y compuestos |
Procesos de postratamiento | Mecanizado, montaje, tratamiento térmico | Mejora de las propiedades mecánicas y los acabados superficiales |
Descubra la mejor solución pulvimetalúrgica para sus necesidades. contacte hoy mismo con nuestros expertos ¡!