El ciclo de sinterización en pulvimetalurgia es un proceso crítico que transforma los polvos metálicos en un producto final cohesivo y duradero.Aunque las referencias varían ligeramente en sus descripciones, los pasos fundamentales pueden destilarse en tres etapas principales: compactación del polvo , sinterización (calentamiento) y refrigeración .Estas etapas garantizan que el material alcance la densidad, resistencia e integridad estructural deseadas.A continuación, exploramos estos pasos en detalle, centrándonos en su propósito, mecanismos y resultados.
Explicación de los puntos clave:
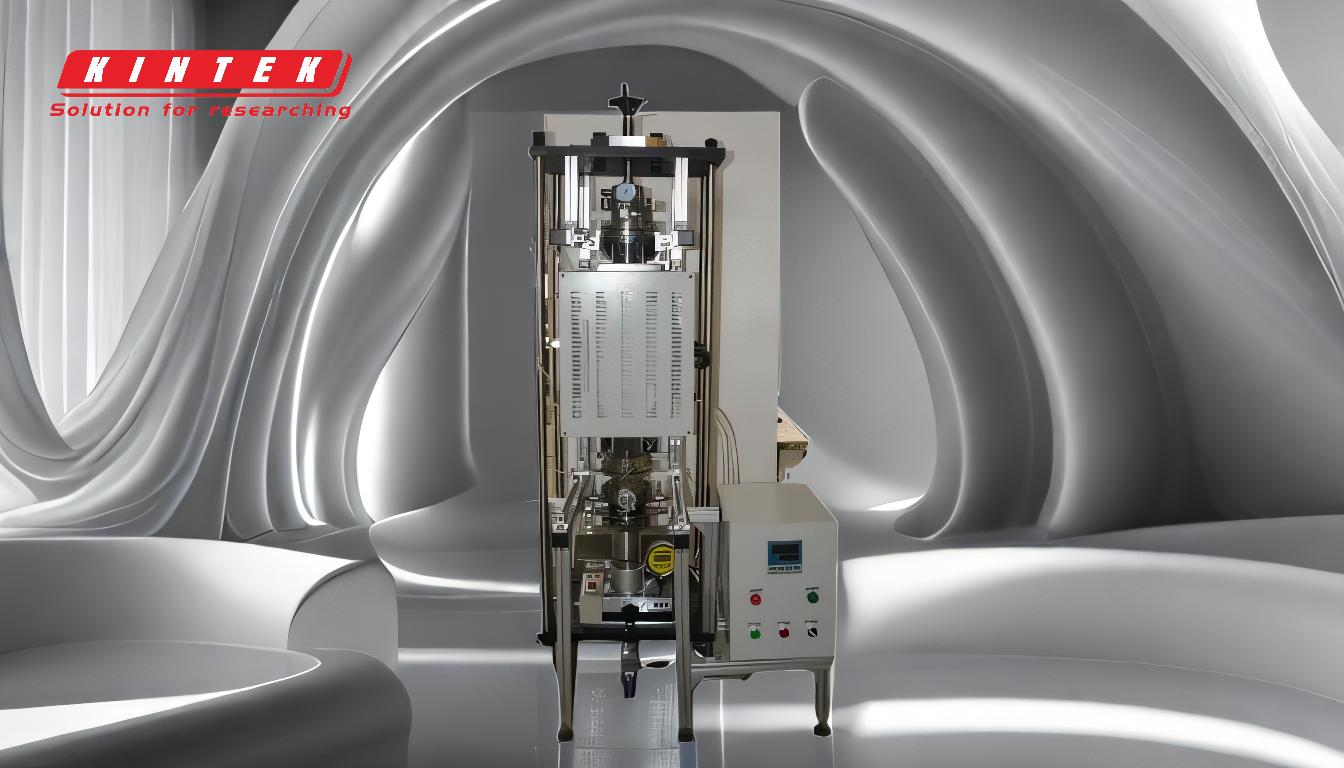
-
Compactación del polvo
- Propósito:Transformar el polvo metálico en una forma preliminar (pieza verde) con resistencia suficiente para su manipulación y sinterización.
-
Proceso:
- Los polvos metálicos se colocan en una matriz y se someten a alta presión, normalmente mediante una prensa hidráulica o mecánica.
- La presión compacta el polvo, reduciendo los huecos y aumentando el contacto entre partículas.
- La "pieza verde" resultante tiene una estructura porosa, pero es lo suficientemente cohesiva como para mantener su forma.
-
Consideraciones:
- La elección de la composición del polvo (por ejemplo, el tipo de aleación o el tamaño de las partículas) afecta directamente al proceso de compactación y a las propiedades del producto final.
- Una compactación adecuada garantiza una densidad uniforme, lo que es fundamental para obtener unos resultados de sinterización uniformes.
-
Sinterización (calentamiento)
- Objetivo:Para unir las partículas de polvo compactado en una estructura sólida y densa mediante un calentamiento controlado.
-
Proceso:
- La pieza verde se calienta en un horno de sinterización a una temperatura justo por debajo del punto de fusión del metal.
- Durante el calentamiento, se produce una difusión atómica que hace que las partículas se unan en sus puntos de contacto (formación de cuellos).
- El material se densifica al reducirse los poros y fusionarse las partículas.
-
Mecanismos:
- Fase inicial:Las partículas comienzan a unirse y la difusión superficial reduce la porosidad.
- Etapa intermedia:Aumenta la densidad de las partículas y se forman los límites de grano.
- Etapa final:La estructura se vuelve mayoritariamente sólida, con una porosidad mínima y una elevada resistencia mecánica.
-
Consideraciones:
- La temperatura y el tiempo se controlan cuidadosamente para evitar la fusión o la deformación.
- La atmósfera de sinterización (por ejemplo, hidrógeno, nitrógeno o vacío) es fundamental para evitar la oxidación y garantizar una unión adecuada.
-
Enfriamiento
- Propósito:Solidificar el material sinterizado en su forma final manteniendo la integridad estructural.
-
Proceso:
- La pieza sinterizada se enfría gradualmente en un entorno controlado para evitar tensiones térmicas o grietas.
- Las velocidades de enfriamiento varían en función del material y de las propiedades deseadas (por ejemplo, un enfriamiento más rápido para una mayor dureza).
-
Resultado:
- El producto final alcanza las propiedades mecánicas previstas, como resistencia, dureza y estabilidad dimensional.
- Se minimiza cualquier porosidad restante y el material está listo para los procesos de acabado, si es necesario.
-
Consideraciones:
- El enfriamiento debe ser uniforme para evitar distorsiones o tensiones residuales.
- Pueden aplicarse tratamientos posteriores a la sinterización (por ejemplo, tratamiento térmico, acabado superficial) para mejorar el rendimiento.
Resumen del ciclo de sinterización:
- Compactación del polvo:Los polvos metálicos se prensan en una forma preliminar, creando una pieza verde con suficiente cohesión.
- Sinterización (calentamiento):La parte verde se calienta para unir las partículas, reducir la porosidad y lograr la densificación.
- Enfriamiento:La pieza sinterizada se enfría para solidificar su estructura y finalizar sus propiedades mecánicas.
Cada etapa es interdependiente, y el control cuidadoso de los parámetros (por ejemplo, presión, temperatura, velocidad de enfriamiento) garantiza la producción de componentes sinterizados de alta calidad.Comprender estas etapas es esencial para optimizar el proceso de sinterización y conseguir las propiedades deseadas del material.
Tabla resumen:
Etapa | Objetivo | Procesos clave |
---|---|---|
Compactación de polvo | Dar al polvo metálico una forma preliminar (parte verde) para su manipulación. | Compactación a alta presión mediante prensa hidráulica/mecánica; reduce los huecos, aumenta el contacto de las partículas. |
Sinterización (calentamiento) | Unir partículas en una estructura sólida y densa mediante calentamiento controlado. | Calentamiento por debajo del punto de fusión; difusión atómica, formación de cuellos y densificación. |
Enfriamiento | Solidificar el material sinterizado manteniendo la integridad estructural. | Enfriamiento gradual en un entorno controlado; minimiza la porosidad y el estrés térmico. |
Optimice su proceso de sinterización con el asesoramiento de expertos. póngase en contacto con nosotros ¡!