Una atmósfera inerte para el recocido hace referencia a un entorno controlado en el que los gases reactivos como el oxígeno se sustituyen por gases no reactivos (inertes) como el nitrógeno o el argón. Este entorno evita la oxidación, la descarburación y la contaminación de la superficie del metal durante el proceso de recocido, garantizando unos resultados de alta calidad. Las atmósferas inertes son especialmente cruciales para el recocido de aceros inoxidables y metales no férreos, ya que protegen el material de reacciones químicas que podrían comprometer sus propiedades. El uso de gases inertes de gran pureza (por ejemplo, 99,99% de pureza) y de sistemas de control precisos en los hornos mejora aún más la eficacia del proceso de recocido.
Explicación de los puntos clave:
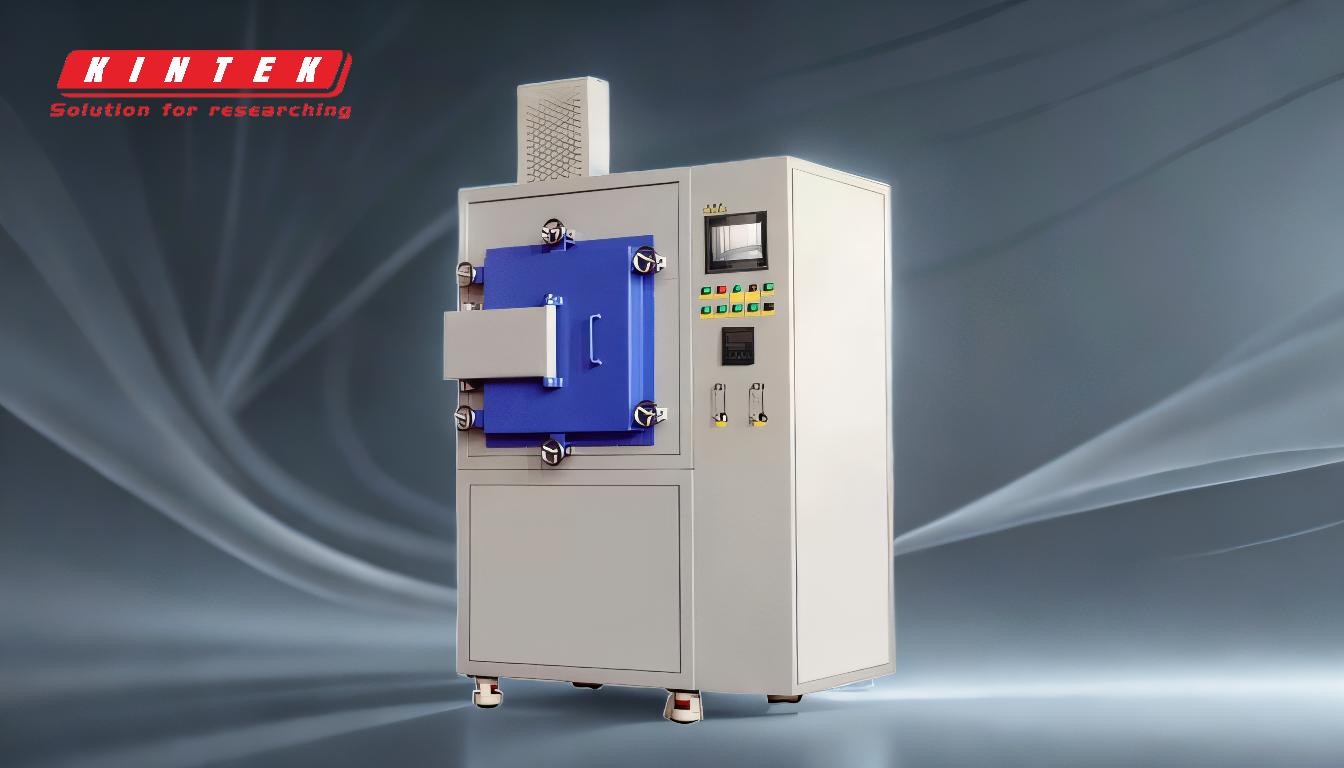
-
Definición de atmósfera inerte:
- Una atmósfera inerte es un entorno controlado en el que los gases reactivos (por ejemplo, el oxígeno) se sustituyen por gases no reactivos como el nitrógeno o el argón.
- Este entorno está diseñado para evitar reacciones químicas no deseadas, como la oxidación o la descarburación, durante procesos de tratamiento térmico como el recocido.
-
Finalidad del uso de una atmósfera inerte en el recocido:
- Prevención de la oxidación: La oxidación se produce cuando los metales reaccionan con el oxígeno, dando lugar a la formación de incrustaciones en la superficie. Una atmósfera inerte elimina el oxígeno, impidiendo esta reacción.
- Evitar la descarburación: La descarburación es la pérdida de carbono de la superficie del acero, que puede debilitar el material. Los gases inertes lo evitan creando un entorno no reactivo.
- Reducir la contaminación: Las atmósferas inertes minimizan el riesgo de contaminación por impurezas, garantizando que el metal conserve las propiedades deseadas.
- Mejorar la reproducibilidad: Al mantener un entorno constante, las atmósferas inertes garantizan resultados de recocido fiables y repetibles.
-
Tipos de gases inertes utilizados:
- Nitrógeno: Es el gas inerte más utilizado debido a su rentabilidad y a que no reacciona con el acero. Está ampliamente disponible y ofrece una excelente protección contra la oxidación.
- Argón: Otra opción popular, especialmente para aplicaciones que requieren una mayor pureza o cuando el nitrógeno puede reaccionar con determinados materiales. El argón es más denso que el nitrógeno, por lo que ofrece mejor protección en algunos casos.
- Hidrógeno: Ocasionalmente se utiliza en combinación con argón para aplicaciones específicas, como el recocido de aceros inoxidables, para mejorar la limpieza de la superficie y reducir la formación de óxido.
-
Aplicaciones de las atmósferas inertes en el recocido:
- Aceros inoxidables: Las atmósferas inertes son esenciales para el recocido de los aceros inoxidables a fin de evitar la formación de óxido de cromo, que puede degradar la resistencia a la corrosión.
- Metales no ferrosos: Metales como el cobre, el aluminio y el titanio se benefician de atmósferas inertes para evitar la oxidación y mantener la calidad de la superficie.
- Tratamientos térmicos especializados: Las atmósferas inertes se utilizan en procesos como el pegado, el curado y el tratamiento térmico para garantizar un control preciso de las propiedades de los materiales.
-
Equipos y sistemas de control:
- Hornos de atmósfera de gas inerte: Estos hornos están diseñados con controles de temperatura de precisión basados en microprocesadores y aislamiento de bajo consumo para mantener unas condiciones constantes.
- Gases de gran pureza: Se utilizan gases inertes con una pureza superior al 99,99% para garantizar una contaminación mínima y un rendimiento óptimo.
- Control de la presión: La presión del gas inerte suele mantenerse dentro de un rango específico (por ejemplo, de 0,05 a 0,07 MPa) para lograr el entorno de protección deseado.
-
Ventajas de utilizar una atmósfera inerte:
- Mejora de la calidad de la superficie: Previene la formación de incrustaciones y mantiene una superficie limpia y libre de óxido.
- Propiedades mejoradas de los materiales: Conserva el contenido de carbono y otros elementos críticos, garantizando la resistencia y durabilidad del material.
- Seguridad: Reduce el riesgo de incendios y explosiones al eliminar los gases reactivos.
- Ahorro de costes: Los hornos energéticamente eficientes y los precisos sistemas de control optimizan el uso de los recursos, reduciendo los costes operativos.
-
Retos y consideraciones:
- Coste de los gases inertes: Los gases de gran pureza, como el argón, pueden ser caros, lo que repercute en el coste global del proceso de recocido.
- Mantenimiento de equipos: Los hornos de atmósfera de gas inerte requieren un mantenimiento regular para garantizar un rendimiento constante y evitar fugas.
- Compatibilidad de materiales: No todos los materiales requieren atmósferas inertes, por lo que es esencial evaluar las necesidades específicas del material que se va a recocer.
Al comprender estos puntos clave, los compradores de equipos y consumibles pueden tomar decisiones informadas sobre la implantación de atmósferas inertes en sus procesos de recocido, garantizando resultados de alta calidad y operaciones rentables.
Cuadro recapitulativo:
Aspecto | Detalles |
---|---|
Definición | Entorno controlado con gases no reactivos (por ejemplo, nitrógeno, argón). |
Propósito | Evita la oxidación, la descarburación y la contaminación, y garantiza la reproducibilidad. |
Gases inertes utilizados | Nitrógeno (económico), Argón (alta pureza), Hidrógeno (especializado). |
Aplicaciones | Aceros inoxidables, metales no ferrosos, tratamientos térmicos especializados. |
Equipamiento | Hornos de gas inerte con controles de precisión y gases de gran pureza. |
Beneficios | Mejora de la calidad de la superficie, mejora de las propiedades del material, seguridad y ahorro de costes. |
Desafíos | Coste de los gases inertes, mantenimiento de los equipos, compatibilidad de los materiales. |
¿Necesita ayuda para crear una atmósfera inerte para el recocido? Contacte hoy mismo con nuestros expertos soluciones a medida