La forja en caliente es un proceso de fabricación en el que el metal se calienta a alta temperatura y luego se le da forma utilizando fuerzas de compresión.Esta técnica se utiliza mucho en diversos sectores por su capacidad para producir componentes metálicos resistentes, duraderos y de alta calidad.El proceso es especialmente beneficioso para crear piezas que requieren gran resistencia, precisión y resistencia al desgaste.La forja en caliente se utiliza habitualmente en los sectores de automoción, aeroespacial, construcción y maquinaria pesada, entre otros.Es ideal para producir formas complejas y componentes de gran tamaño que serían difíciles o imposibles de conseguir mediante otros métodos de fabricación.
Explicación de los puntos clave:
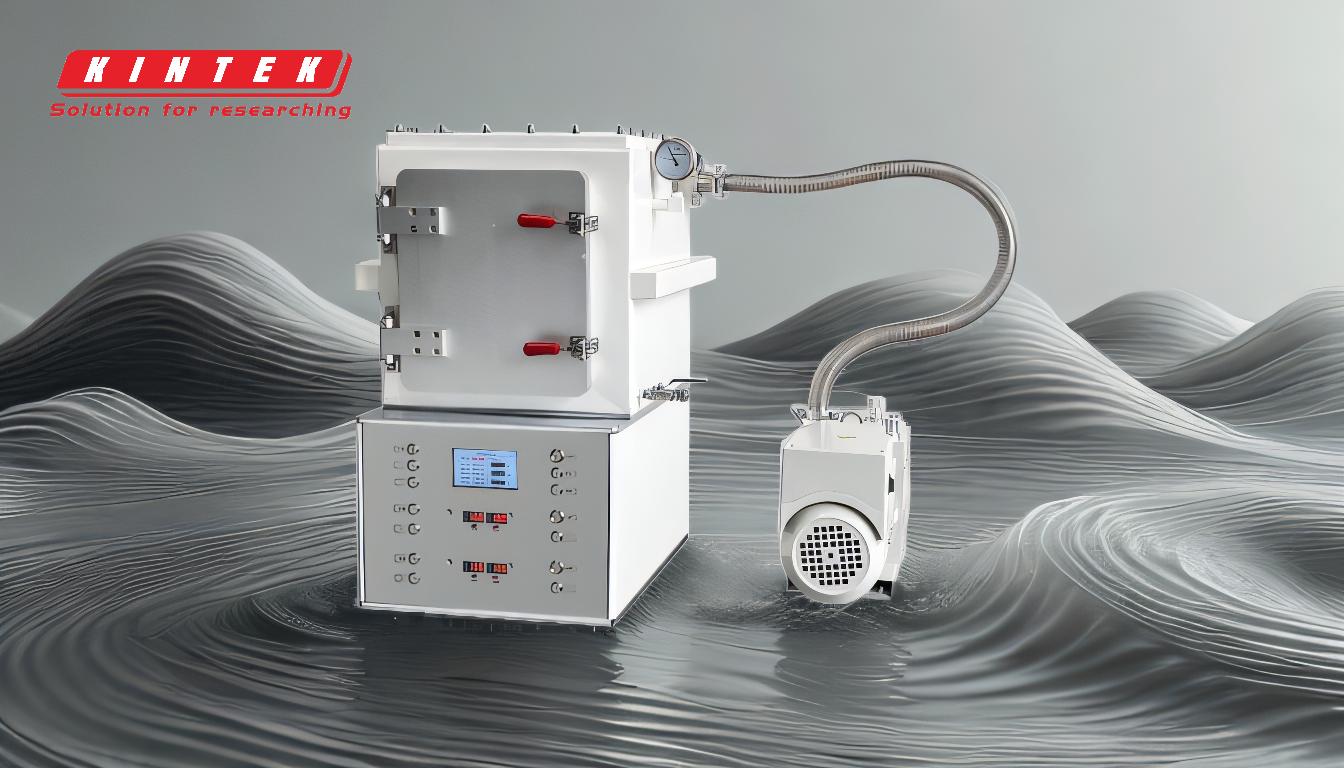
-
Definición y proceso de forja en caliente:
- La forja en caliente consiste en calentar el metal a una temperatura superior a su punto de recristalización, normalmente entre 950°C y 1250°C, según el material.
- Una vez calentado, el metal se coloca en una matriz y se somete a fuerzas de compresión, ya sea mediante martilleo o prensado, para darle la forma deseada.
- La alta temperatura hace que el metal sea más maleable, lo que permite darle forma con menos fuerza y reduce el riesgo de grietas u otros defectos.
-
Ventajas de la forja en caliente:
- Propiedades mecánicas mejoradas:La forja en caliente mejora la estructura del grano del metal, lo que se traduce en una mayor resistencia, tenacidad y resistencia a la fatiga.
- Formas complejas:El proceso permite crear formas complejas e intrincadas que serían difíciles de conseguir con forja en frío o mecanizado.
- Eficacia del material:La forja en caliente minimiza el desperdicio de material, ya que el metal sobrante a menudo puede reciclarse o reutilizarse.
- Rentable para piezas grandes:Para piezas de gran tamaño, la forja en caliente suele ser más rentable que otros métodos, ya que reduce la necesidad de un mecanizado exhaustivo.
-
Aplicaciones habituales de la forja en caliente:
- Automoción:La forja en caliente se utiliza para fabricar componentes críticos como cigüeñales, bielas, engranajes y vigas de ejes.Estas piezas requieren una gran resistencia y durabilidad para soportar las tensiones del funcionamiento del vehículo.
- Industria aeroespacial:El sector aeroespacial recurre a la forja en caliente para fabricar componentes de alta resistencia, como álabes de turbina, piezas del tren de aterrizaje y elementos estructurales.El proceso garantiza que estas piezas puedan soportar condiciones y tensiones extremas.
- Maquinaria pesada y de construcción:La forja en caliente se utiliza para crear piezas grandes y duraderas, como pernos, tuercas y componentes estructurales para edificios, puentes y maquinaria pesada.
- Industria del petróleo y el gas:Componentes como válvulas, bridas y accesorios utilizados en la industria del petróleo y el gas se fabrican a menudo mediante forja en caliente debido a su necesidad de alta resistencia y resistencia a la corrosión.
-
Materiales adecuados para la forja en caliente:
- Aceros y aceros aleados:Son los materiales más forjados por su resistencia y versatilidad.El forjado en caliente mejora sus propiedades mecánicas, lo que los hace adecuados para aplicaciones de alta resistencia.
- Aleaciones de aluminio:Aunque el aluminio tiene una temperatura de forja inferior a la del acero, la forja en caliente se sigue utilizando para fabricar componentes ligeros y de alta resistencia.
- Aleaciones de titanio:Conocidas por su elevada relación resistencia/peso y su resistencia a la corrosión, las aleaciones de titanio suelen forjarse en caliente para aplicaciones aeroespaciales y médicas.
- Cobre y latón:Estos materiales se forjan en caliente para fabricar componentes que requieren una buena conductividad eléctrica y resistencia a la corrosión.
-
Comparación con la forja en frío:
- Temperatura:La forja en frío se realiza a temperatura ambiente o cercana, mientras que la forja en caliente requiere calentar el metal a altas temperaturas.
- Propiedades del material:La forja en caliente mejora la ductilidad y la trabajabilidad del metal, facilitando la conformación de piezas complejas.Por otro lado, la forja en frío puede aumentar la resistencia y la dureza del metal mediante el endurecimiento por deformación.
- Acabado superficial:La forja en frío suele dar como resultado un mejor acabado superficial y tolerancias más ajustadas, mientras que la forja en caliente puede requerir procesos de acabado adicionales.
- Coste y complejidad:La forja en caliente suele ser más rentable para piezas grandes y complejas, mientras que la forja en frío es más adecuada para componentes más pequeños y sencillos.
-
Tendencias futuras de la forja en caliente:
- Automatización y robótica:La integración de la automatización y la robótica en los procesos de forja en caliente está aumentando la eficacia, reduciendo los costes de mano de obra y mejorando la uniformidad de la calidad de las piezas.
- Materiales avanzados:El desarrollo de nuevas aleaciones y materiales con propiedades mejoradas está ampliando las aplicaciones de la forja en caliente en sectores como el aeroespacial y el de las energías renovables.
- Sostenibilidad:Se están haciendo esfuerzos para reducir el impacto medioambiental de la forja en caliente mejorando la eficiencia energética, reciclando materiales y minimizando los residuos.
La forja en caliente sigue siendo un proceso vital en la fabricación moderna, ya que ofrece una combinación de resistencia, precisión y versatilidad inigualable por otros métodos.Sus aplicaciones en diversas industrias ponen de relieve su importancia en la producción de componentes de alto rendimiento que cumplen los exigentes requisitos de la tecnología y las infraestructuras actuales.
Cuadro sinóptico:
Aspecto | Detalles |
---|---|
Definición | Calentar el metal por encima de su punto de recristalización y darle forma con fuerzas de compresión. |
Temperatura | 950°C a 1250°C, dependiendo del material. |
Ventajas | Mayor resistencia, formas complejas, eficacia del material, rentabilidad. |
Aplicaciones | Automoción (cigüeñales, engranajes), aeroespacial (álabes de turbina), construcción (pernos, tuercas). |
Materiales | Acero, aleaciones de aluminio, aleaciones de titanio, cobre y latón. |
Comparación con la forja en frío | La forja en caliente es mejor para piezas grandes y complejas; la forja en frío es adecuada para componentes más pequeños y sencillos. |
Tendencias futuras | Automatización, materiales avanzados y mejoras de la sostenibilidad. |
¿Está interesado en la forja en caliente para su industria? Póngase en contacto con nosotros para obtener más información.