La sinterización, también conocida como "fritado", es un proceso de fabricación que utiliza calor y presión para formar una masa sólida de material sin llegar al punto de licuefacción.Este proceso se basa en la difusión atómica a través de los límites de las partículas, lo que provoca su fusión en una estructura cohesiva.La sinterización se utiliza ampliamente en industrias como la metalurgia, la cerámica y la pulvimetalurgia para crear componentes duraderos y complejos.El proceso se facilita con equipos especializados como un horno de sinterización que emplea métodos de calentamiento como elementos cerámicos (por ejemplo, disiliciuro de molibdeno o carburo de silicio) o microondas para lograr los resultados deseados.
Explicación de los puntos clave:
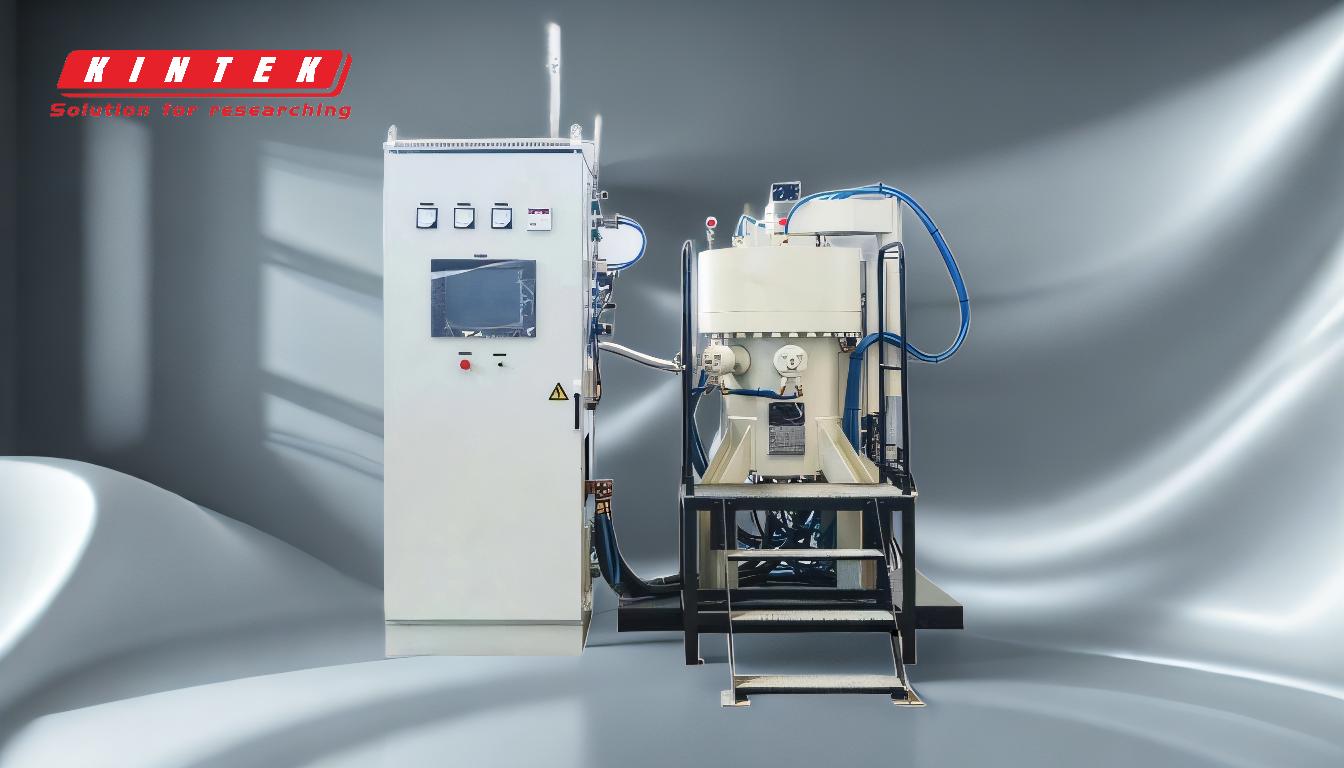
-
Definición de sinterización:
- La sinterización, o "fritado", es un proceso que une partículas mediante calor y presión sin fundir completamente el material.Esto permite crear estructuras sólidas con mejores propiedades mecánicas, como resistencia y densidad.
-
Mecanismo de sinterización:
- El proceso implica la difusión atómica, en la que los átomos se mueven a través de los límites de las partículas y se fusionan.El resultado es la reducción de la porosidad y la formación de un material denso y cohesivo.
-
Aplicaciones de la sinterización:
-
El sinterizado se utiliza en diversas industrias, entre ellas:
- Metalurgia:Para fabricar piezas metálicas de gran resistencia y durabilidad.
- Cerámica:Para crear formas y estructuras complejas con propiedades mejoradas.
- Pulvimetalurgia:Para fabricar componentes a partir de polvos metálicos, como engranajes y cojinetes.
-
El sinterizado se utiliza en diversas industrias, entre ellas:
-
Función de un horno de sinterización:
- A horno de sinterización es esencial para el proceso de sinterización.Proporciona el entorno controlado necesario para aplicar calor y presión de forma eficaz.El horno garantiza un calentamiento uniforme y un control preciso de la temperatura, que son fundamentales para lograr resultados uniformes.
-
Métodos de calentamiento en la sinterización:
-
Los hornos de sinterización emplean dos métodos de calentamiento principales:
- Elementos cerámicos:Fabricados con materiales como el disiliciuro de molibdeno (MoSi2) o el carburo de silicio (SiC), estos elementos son muy utilizados por su estabilidad a altas temperaturas y su eficacia.
- Sinterización por microondas:Una tecnología más reciente que utiliza la energía de microondas para calentar materiales de manera uniforme y rápida.Este método está ganando popularidad por su eficiencia energética y su capacidad para producir microestructuras de grano fino.
-
Los hornos de sinterización emplean dos métodos de calentamiento principales:
-
Ventajas de la sinterización:
-
El proceso de sinterización ofrece varias ventajas, entre ellas:
- La capacidad de producir formas complejas con gran precisión.
- Mejora de las propiedades del material, como mayor resistencia y menor porosidad.
- Rentabilidad en la fabricación, especialmente para la producción a gran escala.
-
El proceso de sinterización ofrece varias ventajas, entre ellas:
Comprendiendo los principios y las aplicaciones de la sinterización, así como la función de un horno de sinterización los fabricantes pueden optimizar sus procesos para crear componentes de alta calidad de forma eficiente.
Cuadro sinóptico:
Aspecto | Detalles |
---|---|
Definición | La sinterización o "fritado" une partículas mediante calor y presión sin fundirlas. |
Mecanismo | La difusión atómica fusiona las partículas, reduciendo la porosidad y formando estructuras densas. |
Aplicaciones | Utilizado en metalurgia, cerámica y pulvimetalurgia para componentes duraderos. |
Función del horno de sinterización | Proporciona calor y presión controlados para un calentamiento uniforme y unos resultados precisos. |
Métodos de calentamiento | Elementos cerámicos (por ejemplo, MoSi2, SiC) o sinterización por microondas para mayor eficacia. |
Ventajas | Produce formas complejas, mejora la resistencia y reduce los costes de fabricación. |
¿Está listo para optimizar su proceso de sinterización? Póngase en contacto con nuestros expertos para obtener más información.