El proceso de evaporación por haz electrónico es una sofisticada técnica de deposición física en fase vapor (PVD) utilizada para crear revestimientos finos de gran pureza sobre sustratos. Consiste en utilizar un haz de electrones de alta energía para calentar y evaporar un material fuente, que luego se condensa sobre un sustrato en una cámara de vacío. Este método es especialmente eficaz para materiales con puntos de fusión elevados, como metales y aleaciones, y permite controlar con precisión el grosor del revestimiento, que suele oscilar entre 5 y 250 nanómetros. El proceso se utiliza ampliamente en industrias que requieren revestimientos uniformes de gran pureza, como la de los semiconductores, la óptica y la aeroespacial.
Explicación de los puntos clave:
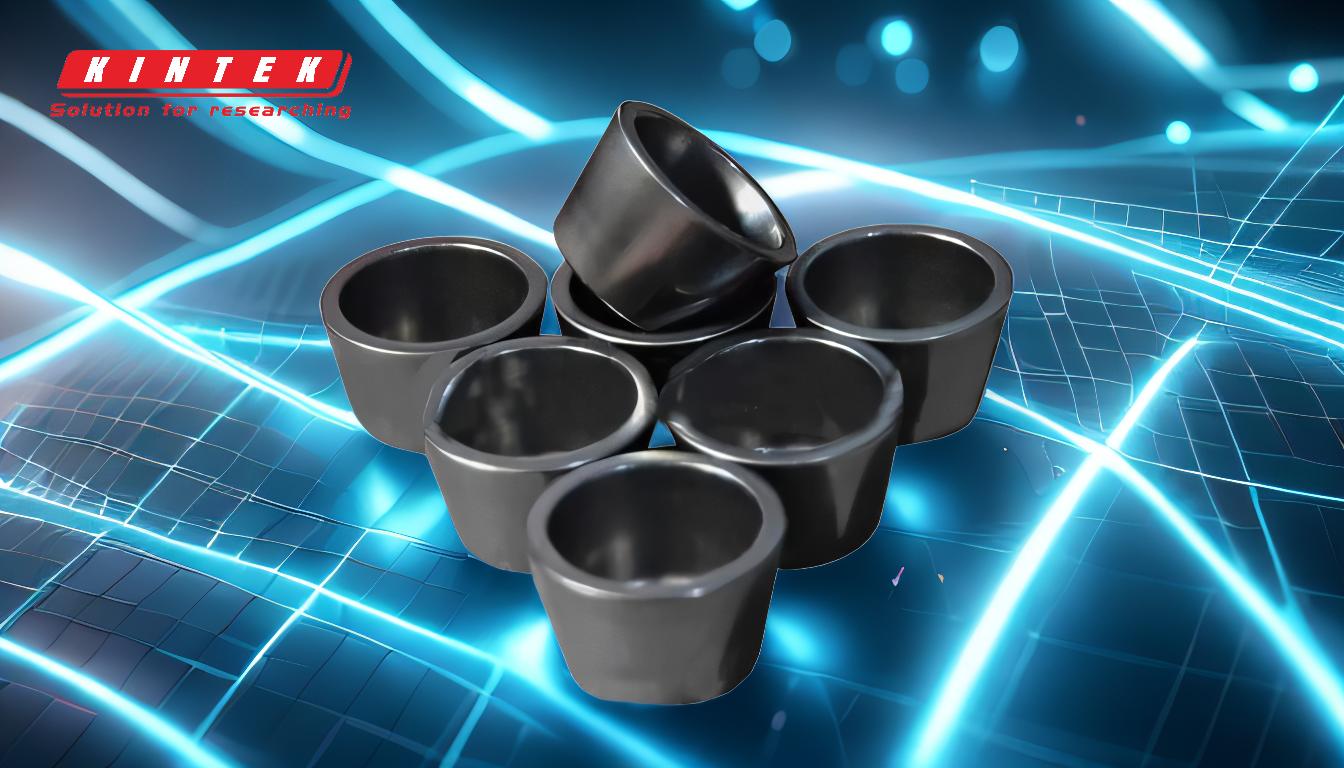
-
Generación y aceleración de haces de electrones:
- El proceso comienza con la generación de electrones mediante un filamento de tungsteno. Al pasar corriente por el filamento, éste se calienta y emite electrones por emisión termoiónica.
- A continuación, estos electrones se aceleran hacia el material fuente mediante un campo eléctrico de alta tensión, normalmente de varios kilovoltios. El alto voltaje garantiza que los electrones adquieran la energía suficiente para calentar eficazmente el material fuente.
-
Enfoque del haz de electrones:
- Se utiliza un campo magnético para concentrar los electrones acelerados en un haz estrecho y concentrado. Este haz concentrado se dirige a la superficie del material fuente contenido en un crisol o en un hogar de cobre refrigerado por agua.
- La focalización del haz de electrones es crucial para conseguir una alta densidad de energía, necesaria para evaporar materiales con puntos de fusión elevados.
-
Calentamiento y evaporación del material de partida:
- Cuando el haz de electrones de alta energía incide en el material fuente, transfiere una cantidad significativa de energía, provocando un rápido calentamiento del material. Dependiendo del material, esta transferencia de energía puede provocar la evaporación o la sublimación.
- El material fuente suele colocarse en un crisol, que puede estar refrigerado por agua para evitar la contaminación por impurezas o reacciones no deseadas con el material del crisol.
-
Entorno de vacío:
- Todo el proceso tiene lugar en una cámara de vacío para garantizar que las partículas evaporadas se desplacen sin obstáculos hasta el sustrato. El entorno de vacío minimiza las colisiones entre las partículas evaporadas y las moléculas de gas residuales, que de otro modo podrían degradar la calidad del revestimiento.
- El vacío también evita la oxidación o contaminación del material de partida y de la fina película resultante.
-
Deposición sobre el sustrato:
- Las partículas evaporadas se desplazan hacia arriba en la cámara de vacío y se depositan sobre el sustrato, que se coloca por encima del material de partida. El sustrato suele mantenerse a una temperatura controlada para garantizar una adhesión y una calidad de película adecuadas.
- El proceso de deposición da como resultado un revestimiento fino de gran pureza que puede alterar las propiedades del sustrato, como la conductividad eléctrica, la reflectividad o la resistencia a la corrosión, sin afectar a su precisión dimensional.
-
Control del espesor del revestimiento:
- El grosor de la película depositada se controla cuidadosamente mediante microbalanzas de cristal de cuarzo. Estos dispositivos controlan la velocidad de deposición en tiempo real midiendo el cambio de masa a medida que la película crece sobre el sustrato.
- Ajustando parámetros como la corriente del haz de electrones, el voltaje de aceleración y el tiempo de deposición, se puede conseguir con gran precisión el grosor de recubrimiento deseado, normalmente entre 5 y 250 nanómetros.
-
Ventajas de la evaporación E-Beam:
- Alta pureza: El proceso produce revestimientos de muy alta pureza, ya que el entorno de vacío y el calentamiento controlado minimizan la contaminación.
- Materiales de alto punto de fusión: La evaporación por haz electrónico es especialmente adecuada para materiales con puntos de fusión elevados, como el oro, el platino y los metales refractarios, que son difíciles de evaporar con los métodos térmicos tradicionales.
- Recubrimientos uniformes: El haz de electrones focalizado permite un calentamiento y una evaporación uniformes, lo que se traduce en un grosor y una calidad uniformes de la película en todo el sustrato.
- Recubrimientos multicapa: Muchos sistemas de haz electrónico están equipados con múltiples crisoles, lo que permite la deposición de revestimientos multicapa o la codeposición de diferentes materiales sin romper el vacío.
-
Aplicaciones:
- Semiconductores: La evaporación por haz electrónico se utiliza ampliamente en la industria de semiconductores para depositar películas finas de metales y aleaciones para interconexiones, contactos y otros componentes críticos.
- Óptica: El proceso se utiliza para crear revestimientos de alta reflectividad para espejos, lentes y otros componentes ópticos.
- Aeroespacial: La evaporación por haz de electrones se emplea para producir revestimientos protectores que mejoran la durabilidad y el rendimiento de los componentes aeroespaciales.
- Investigación y desarrollo: La técnica también se utiliza en I+D para desarrollar nuevos materiales y revestimientos con propiedades a medida.
En resumen, el proceso de evaporación por haz electrónico es un método muy controlado y versátil para depositar revestimientos finos de gran pureza sobre sustratos. Su capacidad para manipular materiales de alto punto de fusión, producir revestimientos uniformes y operar en un entorno de vacío lo hace indispensable en diversas industrias de alta tecnología.
Cuadro recapitulativo:
Aspecto clave | Detalles |
---|---|
Resumen del proceso | Utiliza un haz de electrones de alta energía para evaporar y depositar materiales en el vacío. |
Componentes clave | Filamento de tungsteno, campo magnético, crisol, cámara de vacío, sustrato. |
Espesor del revestimiento | 5 a 250 nanómetros, controlados con microbalanzas de cristal de cuarzo. |
Ventajas | Alta pureza, revestimientos uniformes, maneja materiales de alto punto de fusión. |
Aplicaciones | Semiconductores, óptica, aeroespacial, I+D. |
¿Le interesan los revestimientos de gran pureza para su industria? Póngase en contacto con nosotros para obtener más información sobre las soluciones de evaporación por haz electrónico