Los hornos de inducción sin núcleo y con núcleo se utilizan para fundir metales, pero difieren significativamente en su diseño, funcionamiento y aplicación.Los hornos de inducción sin núcleo se basan en una bobina de cobre refrigerada por agua para inducir corrientes directamente en la carga metálica, lo que ofrece un control preciso de la temperatura, una distribución uniforme del calor y flexibilidad para los cambios de aleación.Sin embargo, su eficiencia energética es menor (en torno al 75%) y pueden requerir frecuentes sustituciones del revestimiento refractario.Los hornos de inducción con núcleo, por su parte, utilizan un núcleo magnético para mejorar la eficiencia y son más adecuados para operaciones continuas con menos cambios de aleación.La elección entre uno y otro depende de las necesidades operativas específicas, como la eficiencia energética, la flexibilidad de la aleación y los requisitos de mantenimiento.
Explicación de los puntos clave:
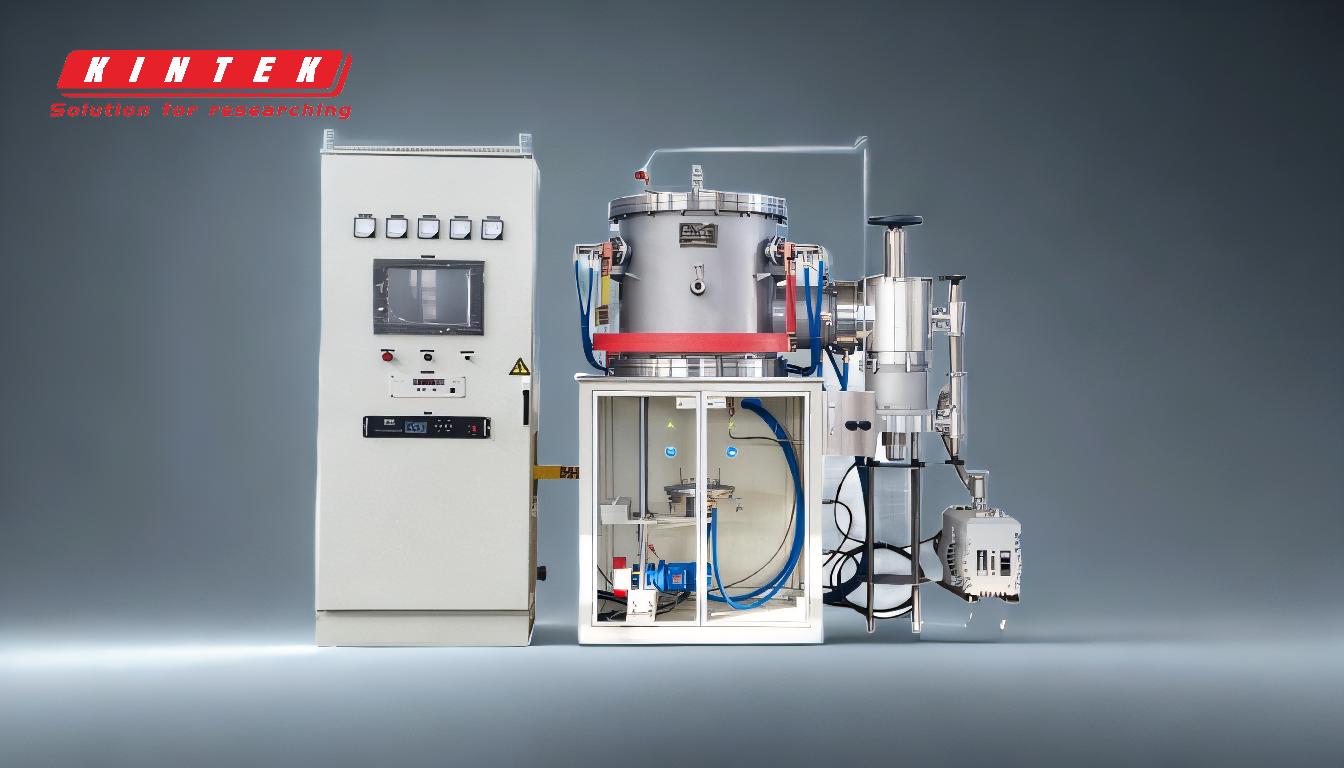
-
Diseño y construcción:
-
Horno de inducción sin núcleo:
- El componente primario es una bobina de cobre refrigerada por agua y enrollada en forma helicoidal, alojada dentro de una carcasa de acero.
- La bobina induce corrientes directamente en la carga metálica, lo que elimina la necesidad de una bobina secundaria o un núcleo magnético.
- La carcasa de acero está blindada magnéticamente para evitar el calentamiento y se apoya en muñones para facilitar el vertido.
-
Horno de inducción con núcleo:
- Incorpora un núcleo magnético (normalmente de hierro) que aumenta el flujo magnético y mejora la eficiencia energética.
- El núcleo actúa como circuito secundario, lo que permite una mayor eficiencia energética en comparación con los diseños sin núcleo.
- El diseño es más complejo y adecuado para operaciones continuas con menos cambios de aleación.
-
Horno de inducción sin núcleo:
-
Funcionamiento y eficiencia:
-
Horno de inducción sin núcleo:
- Funciona por acción transformadora sin bobina secundaria, induciendo corrientes directamente en la carga metálica.
- Ofrece un control preciso de la temperatura y la composición química del metal, por lo que resulta ideal para fundir diversos grados de acero, hierro y aleaciones no ferrosas.
- Menor eficiencia energética (aproximadamente 75%) debido a la ausencia de núcleo magnético.
- Puede apagarse y arrancarse en frío, lo que simplifica los cambios de aleación pero reduce la vida útil del revestimiento refractario.
-
Horno de inducción con núcleo:
- Utiliza un núcleo magnético para mejorar la eficiencia, logrando una mayor eficiencia energética en comparación con los hornos sin núcleo.
- Más adecuado para operaciones continuas con menos cambios de aleación, ya que los cambios frecuentes pueden dañar el núcleo.
- Menos flexible para los cambios de aleación, pero más eficiente energéticamente para series de producción constantes.
-
Horno de inducción sin núcleo:
-
Aplicaciones y flexibilidad:
-
Horno de inducción sin núcleo:
- Ideal para aplicaciones que requieren cambios frecuentes de aleación, como las fundiciones que producen pequeños lotes de aleaciones diferentes.
- Proporciona una distribución uniforme del calor y un control preciso de la temperatura, lo que la hace adecuada para procesos de refundición y refinado.
- Se utiliza habitualmente para fundir acero, hierro y aleaciones no ferrosas.
-
Horno de inducción con núcleo:
- Más adecuado para operaciones continuas con menos cambios de aleación, como la producción a gran escala de una sola aleación.
- Su mayor eficacia la hace rentable para la producción constante de grandes volúmenes.
- Menor flexibilidad para cambios de aleación, pero más eficiente para aplicaciones específicas a largo plazo.
-
Horno de inducción sin núcleo:
-
Mantenimiento y vida útil:
-
Horno de inducción sin núcleo:
- Los cambios frecuentes de aleación y los ciclos térmicos pueden reducir la vida útil del revestimiento refractario.
- Requiere un mantenimiento regular para sustituir el revestimiento refractario y garantizar la correcta refrigeración del serpentín.
- Su menor eficiencia energética puede conllevar mayores costes operativos con el tiempo.
-
Horno de inducción con núcleo:
- El menor número de cambios de aleación y el funcionamiento continuo reducen el desgaste del revestimiento refractario y del núcleo.
- La mayor eficiencia energética reduce los costes operativos, pero el núcleo magnético puede requerir un mantenimiento periódico.
- Mayor vida útil de los revestimientos refractarios y los núcleos en situaciones de funcionamiento continuo.
-
Horno de inducción sin núcleo:
-
Gama de frecuencias y control:
-
Horno de inducción sin núcleo:
- Funciona en una amplia gama de frecuencias (de 50 Hz a 10 kHz), lo que permite fundir con flexibilidad diferentes metales y aleaciones.
- Proporciona un control preciso sobre la temperatura y la química del metal, lo que lo hace adecuado para aplicaciones especializadas.
-
Horno de inducción con núcleo:
- Normalmente funciona a frecuencias más bajas, optimizadas para aleaciones específicas y producción continua.
- Menos flexible en cuanto a la gama de frecuencias, pero más eficiente para aplicaciones específicas.
-
Horno de inducción sin núcleo:
En resumen, la elección entre hornos de inducción con o sin núcleo depende de las necesidades operativas específicas, como la frecuencia de los cambios de aleación, la eficiencia energética requerida y las consideraciones de mantenimiento.Los hornos sin núcleo ofrecen mayor flexibilidad y control, mientras que los hornos con núcleo proporcionan mayor eficiencia y son más adecuados para operaciones continuas.
Tabla resumen:
Característica | Horno de inducción sin núcleo | Horno de inducción con núcleo |
---|---|---|
Diseño | Bobina de cobre refrigerada por agua, sin núcleo magnético | Núcleo magnético para mejorar la eficiencia |
Eficiencia | ~75% de eficiencia energética | Mayor eficiencia energética |
Aplicaciones | Cambios frecuentes de aleación, lotes pequeños | Operaciones continuas, aleación única |
Mantenimiento | Sustitución frecuente del revestimiento refractario | Mantenimiento menos frecuente, mayor vida útil |
Gama de frecuencias | 50 Hz a 10 kHz | Frecuencias más bajas, optimizadas para aleaciones específicas |
¿Aún no sabe qué horno de inducción es el más adecuado para su empresa? Póngase en contacto con nuestros expertos para un asesoramiento personalizado.