La carburación líquida y la carburación con gas son dos métodos distintos de endurecimiento de superficies que se utilizan para mejorar la resistencia al desgaste y la durabilidad de los componentes de acero. La cementación líquida implica sumergir piezas de acero en un baño de sales fundidas que contiene compuestos ricos en carbono, mientras que la cementación con gas utiliza una atmósfera gaseosa rica en carbono para difundir el carbono en la superficie del acero. Ambos procesos tienen como objetivo aumentar el contenido de carbono en la superficie, pero difieren en sus mecanismos, requisitos de equipos y control del proceso. La cementación líquida suele preferirse para piezas más pequeñas y ofrece velocidades de calentamiento más rápidas, mientras que la cementación con gas es más adecuada para componentes más grandes y proporciona mejor uniformidad y control del proceso.
Puntos clave explicados:
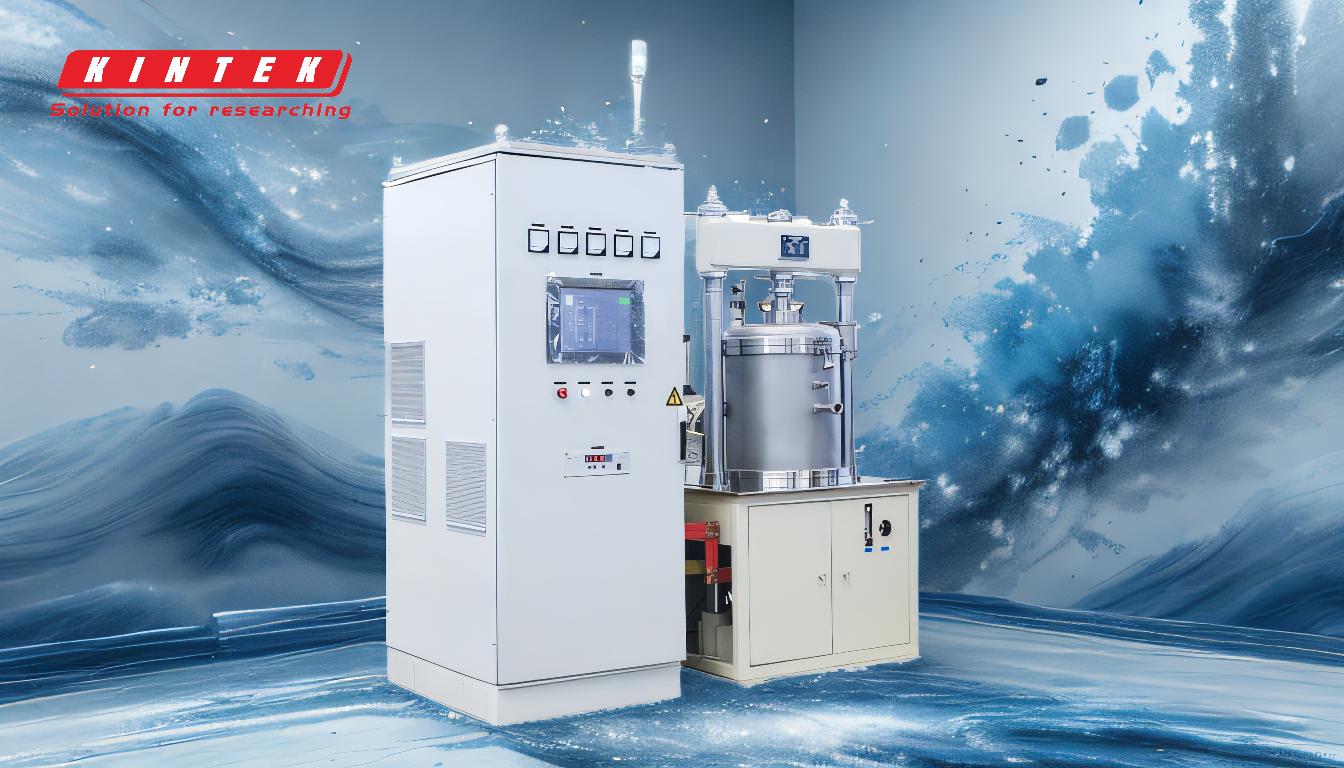
-
Mecanismo de proceso:
- Carburación líquida: Las piezas de acero se sumergen en un baño de sales fundidas que contiene compuestos ricos en carbono, como cianuro de sodio o cianuro de potasio. El carbono se difunde en la superficie del acero a altas temperaturas (normalmente entre 850 y 950 °C).
- Carburación de gas: Las piezas de acero se calientan en un horno con una atmósfera de gas rica en carbono, normalmente compuesta de metano, propano o gas natural. Los átomos de carbono se difunden en la superficie del acero a temperaturas típicamente entre 900 y 950 °C.
-
Equipo y configuración:
- Carburación líquida: Requiere un horno de baño de sal, que es relativamente simple y compacto. La sal fundida debe mantenerse cuidadosamente para garantizar un contenido de carbono y una temperatura constantes.
- Carburación de gas: Requiere una configuración de horno más compleja con sistemas de inyección de gas y control atmosférico preciso. El horno debe estar equipado con sensores para monitorear y regular el potencial de carbono de la atmósfera de gas.
-
Control y uniformidad de procesos:
- Carburación líquida: Ofrece velocidades de calentamiento más rápidas debido al contacto directo con la sal fundida, pero puede resultar complicado lograr una difusión uniforme del carbono, especialmente para geometrías complejas.
- Carburación de gas: Proporciona un mejor control sobre el potencial de carbono y permite una difusión más uniforme del carbono en la superficie de las piezas, incluso para formas complejas.
-
Idoneidad de la aplicación:
- Carburación líquida: Ideal para piezas de tamaño pequeño a mediano, como engranajes, cojinetes y sujetadores, donde se requiere un procesamiento rápido. También es adecuado para piezas que requieren una capa superficial fina y dura.
- Carburación de gas: Más adecuado para componentes más grandes y producción en masa, donde el endurecimiento de la superficie consistente y uniforme es fundamental. A menudo se utiliza en las industrias automotriz y aeroespacial para piezas como cigüeñales, árboles de levas y componentes de transmisión.
-
Consideraciones ambientales y de seguridad:
- Carburación líquida: Implica el uso de productos químicos peligrosos como el cianuro, que requieren un manejo y eliminación cuidadosos. El proceso también puede producir humos tóxicos, lo que requiere una ventilación adecuada y medidas de seguridad.
- Carburación de gas: Generalmente se considera más seguro y respetuoso con el medio ambiente, ya que no contiene productos químicos tóxicos. Sin embargo, todavía requiere un manejo adecuado de los gases inflamables y un seguimiento de las emisiones de los hornos.
-
Costo y mantenimiento:
- Carburación líquida: Menores costos iniciales de equipo pero mayor mantenimiento continuo debido a la necesidad de reponer y eliminar periódicamente el baño de sal. El proceso también puede requerir una limpieza de piezas más frecuente para eliminar los residuos de sal.
- Carburación de gas: Mayor inversión inicial en equipos de hornos y sistemas de control de gas, pero menores costos de mantenimiento con el tiempo. El proceso también es más eficiente desde el punto de vista energético, lo que conlleva posibles ahorros de costes a largo plazo.
-
Acabado superficial y posprocesamiento:
- Carburación líquida: Normalmente da como resultado un acabado superficial más suave debido al efecto de pulido de la sal fundida. Sin embargo, es posible que las piezas requieran una limpieza adicional para eliminar la sal residual.
- Carburación de gas: Puede producir un acabado superficial ligeramente más rugoso, pero esto se puede mitigar con un control adecuado del proceso. Las piezas generalmente requieren menos posprocesamiento en comparación con la cementación líquida.
En resumen, la elección entre cementación líquida y gaseosa depende de los requisitos específicos de la aplicación, incluido el tamaño de la pieza, el volumen de producción, las propiedades superficiales deseadas y las consideraciones ambientales. Ambos métodos ofrecen ventajas y desafíos únicos, lo que los hace adecuados para diferentes necesidades industriales.
Tabla resumen:
Aspecto | Carburación líquida | Carburación de gas |
---|---|---|
Mecanismo de proceso | Inmersión en baño de sales fundidas (850-950°C) | Calentamiento en atmósfera de gas rico en carbono (900-950°C) |
Equipo | Horno de baño de sal (simple, compacto) | Horno complejo con inyección de gas y control de atmósfera. |
Control de procesos | Calentamiento más rápido, difusión menos uniforme. | Mejor control, difusión más uniforme |
Idoneidad de la aplicación | Piezas pequeñas y medianas (engranajes, rodamientos) | Componentes más grandes, producción en masa (automotriz, aeroespacial) |
Impacto ambiental | Productos químicos peligrosos (cianuro), vapores tóxicos | Más seguro, sin productos químicos tóxicos, pero sí gases inflamables. |
Costo y mantenimiento | Menor coste inicial, mayor mantenimiento (reposición de sal, limpieza) | Mayor costo inicial, menor mantenimiento, eficiencia energética |
Acabado superficial | Acabado más suave, pero requiere limpieza. | Ligeramente más rugoso, menos posprocesamiento |
¿Necesita ayuda para decidir entre carburación líquida y gaseosa para su aplicación? Póngase en contacto con nuestros expertos hoy ¡Para asesoramiento personalizado!