Tanto los hornos de resistencia como los de inducción se utilizan ampliamente en los procesos industriales de calentamiento y fusión, pero difieren significativamente en sus principios de funcionamiento, eficacia y aplicaciones.Los hornos de resistencia se basan en elementos calefactores externos para generar calor, que luego se transfiere al material, mientras que los hornos de inducción generan calor directamente dentro del material mediante inducción electromagnética.Esta diferencia fundamental da lugar a variaciones en la eficiencia energética, los niveles de contaminación y las capacidades operativas.A continuación se explican en detalle las diferencias clave.
Explicación de los puntos clave:
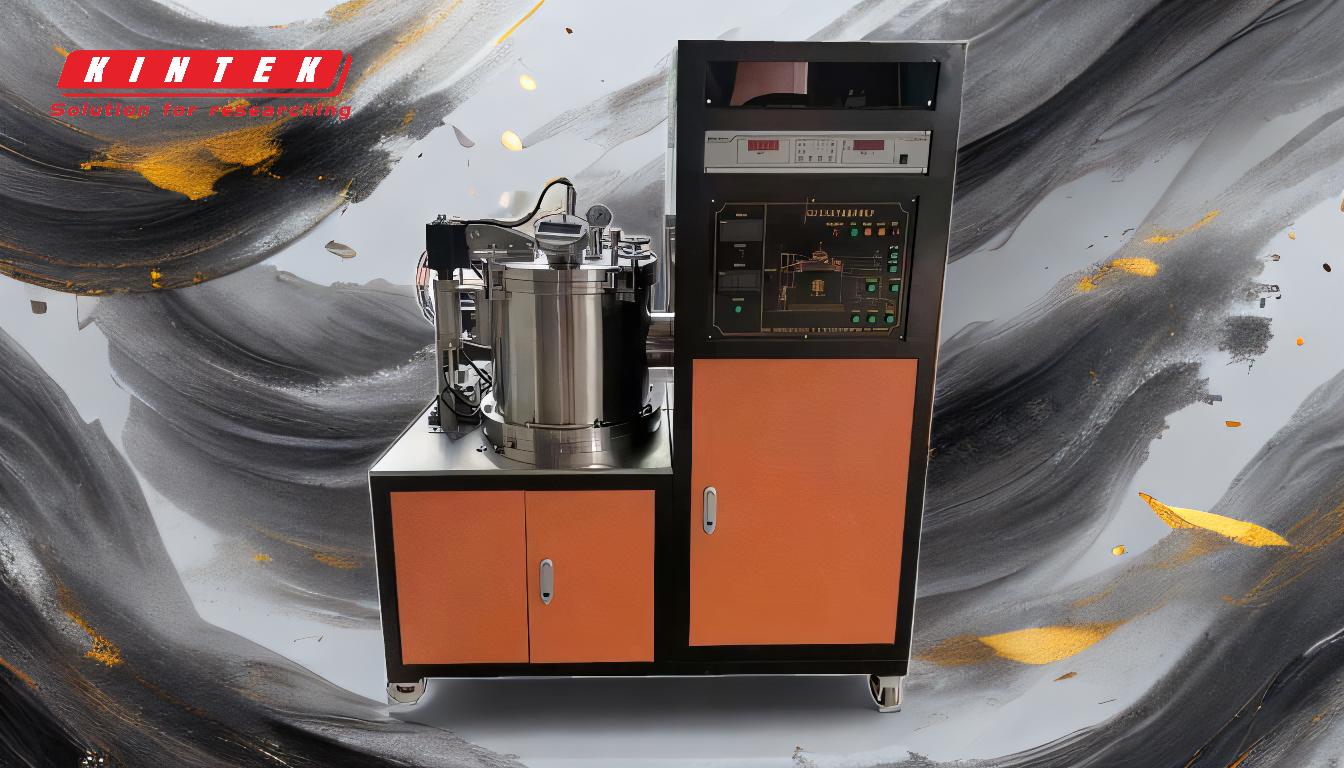
-
Mecanismo de calentamiento:
-
Horno de resistencia:
- Utiliza elementos calefactores externos (por ejemplo, elementos refractarios o bobinas) para generar calor.
- El calor se transfiere al material por conducción, convección o radiación.
- Adecuado para procesos en los que se requiere un calentamiento uniforme, pero la fuente de calor es externa al material.
-
Horno de inducción:
- Genera calor directamente en el material mediante inducción electromagnética.
- La corriente alterna crea un campo magnético alterno, induciendo corrientes parásitas en el material, que producen calor debido a la resistencia.
- Garantiza un calentamiento uniforme y minimiza la contaminación, ya que no interviene ninguna fuente de calor externa.
-
Horno de resistencia:
-
Eficiencia y consumo energético:
-
Horno de resistencia:
- Menos eficiente energéticamente debido a la pérdida de calor durante la transferencia de la fuente externa al material.
- Requiere más energía para mantener altas temperaturas, especialmente en operaciones a gran escala.
-
Horno de inducción:
- Mayor eficiencia energética, ya que el calor se genera directamente dentro del material, lo que reduce las pérdidas de calor.
- Alcanza velocidades de calentamiento más rápidas y una mayor eficiencia térmica, por lo que es ideal para aplicaciones de alta temperatura.
-
Horno de resistencia:
-
Temperatura y densidad de potencia:
-
Horno de resistencia:
- Funciona con densidades de potencia inferiores a las de los hornos de inducción.
- Adecuado para aplicaciones que requieren temperaturas moderadas (por ejemplo, recocido, revenido).
-
Horno de inducción:
- Capaz de funcionar a temperaturas y densidades de potencia más elevadas.
- Puede alcanzar temperaturas de forja de hasta 1250°C y de fusión de hasta 1650°C, lo que la hace adecuada para la fusión y el procesamiento a alta temperatura.
-
Horno de resistencia:
-
Contaminación y pureza:
-
Horno de resistencia:
- Mayor riesgo de contaminación debido al uso de elementos calefactores externos, que pueden introducir impurezas.
- Requiere una cuidadosa selección de los elementos calefactores y de los revestimientos del horno para minimizar la contaminación.
-
Horno de inducción:
- Contaminación mínima, ya que el calor se genera dentro del propio material.
- Ideal para aplicaciones que requieren materiales de gran pureza, como en las industrias de semiconductores o aeroespacial.
-
Horno de resistencia:
-
Control y automatización:
-
Horno de resistencia:
- Normalmente se basa en sistemas de control manuales o semiautomáticos.
- Limitado por la complejidad de mantener un calentamiento uniforme en grandes volúmenes.
-
Horno de inducción:
- Equipado con avanzados sistemas de control, que incluyen barrido automático de frecuencias, control de potencia constante y mecanismos de protección integral.
- Ofrece un control preciso de la temperatura y un funcionamiento suave, reduciendo la necesidad de intervención manual.
-
Horno de resistencia:
-
Aplicaciones:
-
Horno de resistencia:
- Comúnmente utilizado para procesos de tratamiento térmico como recocido, temple y revenido.
- Adecuado para el procesamiento por lotes de materiales que no requieren temperaturas extremadamente altas.
-
Horno de inducción:
- Ampliamente utilizado en aplicaciones de fusión y forja, especialmente para metales como el acero, el aluminio y el cobre.
- Se prefieren para procesos continuos y operaciones a alta temperatura en las que la eficacia y la pureza son fundamentales.
-
Horno de resistencia:
-
Diseño y mantenimiento:
-
Horno de resistencia:
- Diseño más simple con menos componentes, lo que hace que el mantenimiento sea relativamente sencillo.
- Sin embargo, los elementos calefactores pueden requerir una sustitución frecuente debido al desgaste.
-
Horno de inducción:
- Diseño más complejo con componentes como inductores, condensadores y sistemas de control.
- Requiere cuidadosas consideraciones de diseño, como la disposición del yugo y el espaciado entre inductores, para garantizar un rendimiento óptimo.
- El mantenimiento es más sencillo en los modelos avanzados con circuitos integrados y componentes modulares.
-
Horno de resistencia:
-
Idoneidad de los materiales:
-
Horno de resistencia:
- Adecuado para una amplia gama de materiales, incluidos los no metálicos y magnéticos.
- Limitado por la capacidad del material para absorber calor de una fuente externa.
-
Horno de inducción:
- El más adecuado para materiales conductores, especialmente metales.
- Las dificultades surgen con materiales no magnéticos como el aluminio, que requieren diseños de inductores especializados para garantizar un calentamiento eficaz.
-
Horno de resistencia:
En resumen, los hornos de resistencia y los de inducción sirven para fines diferentes en función de sus mecanismos de calentamiento, eficiencia y aplicaciones.Los hornos de resistencia son más adecuados para procesos a temperatura moderada y operaciones por lotes, mientras que los hornos de inducción destacan en procesos a alta temperatura, de gran pureza y continuos.La elección entre uno y otro depende de los requisitos específicos de la aplicación, como la temperatura, el tipo de material y la eficiencia deseada.
Cuadro sinóptico:
Aspecto | Horno de resistencia | Horno de inducción |
---|---|---|
Mecanismo de calentamiento | Los elementos calefactores externos transfieren el calor por conducción, convección o radiación. | Calor generado directamente dentro del material mediante inducción electromagnética. |
Eficacia | Menos eficiente energéticamente debido a la pérdida de calor durante la transferencia. | Más eficiente energéticamente con velocidades de calentamiento más rápidas y menor pérdida de calor. |
Gama de temperaturas | Apto para temperaturas moderadas (por ejemplo, recocido, revenido). | Apto para altas temperaturas (hasta 1650°C) para fusión y forja. |
Riesgo de contaminación | Mayor riesgo debido a los elementos calefactores externos. | Contaminación mínima, ideal para aplicaciones de gran pureza. |
Sistemas de control | Sistemas de control manuales o semiautomatizados. | Automatización avanzada con control preciso de la temperatura y mecanismos de protección. |
Aplicaciones | Procesos de tratamiento térmico (por ejemplo, recocido, temple). | Operaciones de fusión, forja y alta temperatura para metales como el acero y el aluminio. |
Diseño y mantenimiento | Diseño más sencillo, pero los elementos calefactores pueden requerir una sustitución frecuente. | Diseño complejo con mantenimiento más sencillo para los modelos avanzados. |
Adecuación de materiales | Adecuado para materiales no metálicos y magnéticos. | El mejor para materiales conductores, especialmente metales. |
¿Necesita ayuda para elegir el horno adecuado para su aplicación? Póngase en contacto con nuestros expertos para un asesoramiento personalizado.