El proceso de deposición física de vapor (PVD) es un sofisticado método utilizado para depositar películas finas de material sobre un sustrato.Consiste en la transformación de un material sólido en una fase de vapor, que luego se deposita sobre un sustrato para formar un revestimiento fino y uniforme.El proceso suele llevarse a cabo en un entorno de vacío para garantizar la pureza y el control de la deposición.El PVD se utiliza ampliamente en diversas industrias para aplicaciones como mejorar la resistencia al desgaste, aumentar la resistencia a la corrosión y proporcionar acabados decorativos.El proceso implica varios pasos clave, como la vaporización del material de revestimiento, la migración de las partículas vaporizadas y la deposición sobre el sustrato.
Explicación de los puntos clave:
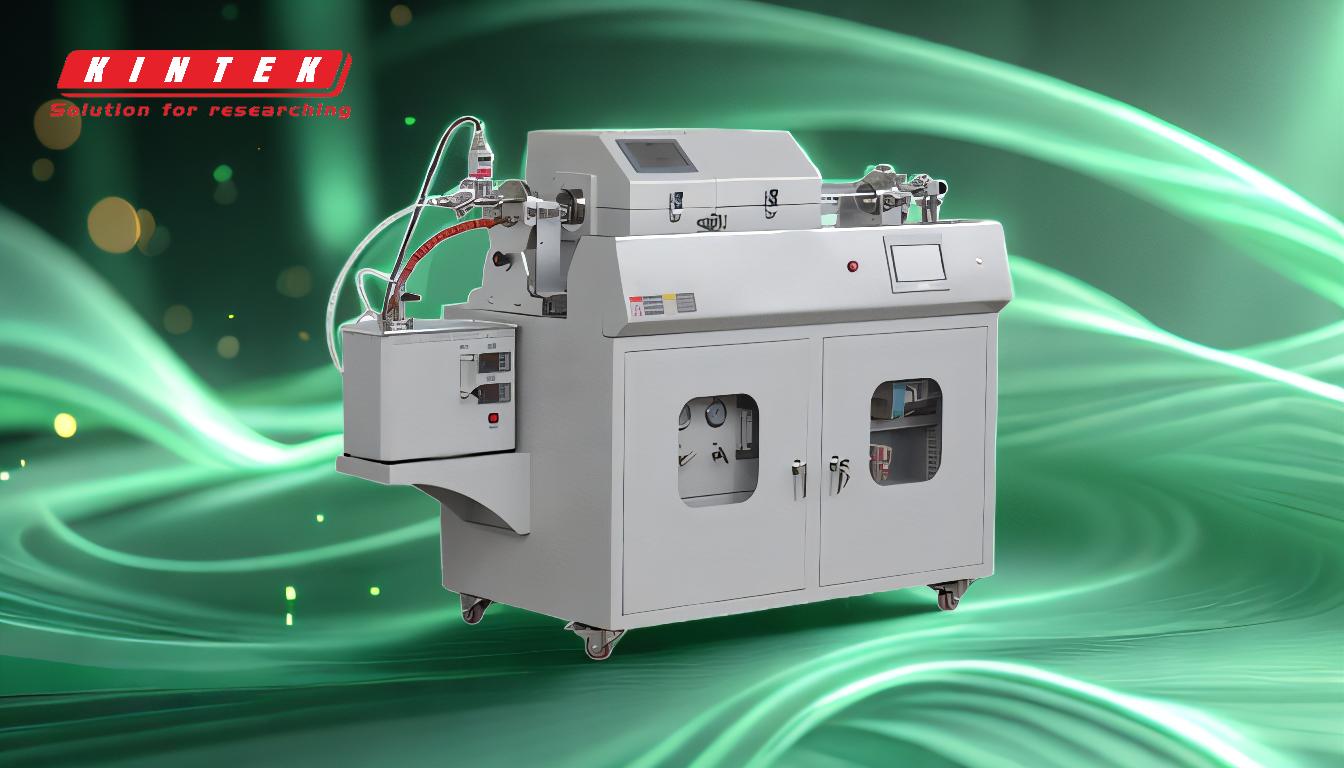
-
Vaporización del material de recubrimiento:
- El primer paso en el proceso de PVD es la vaporización del material de revestimiento.Esto puede conseguirse mediante varios métodos, como la evaporación, el sputtering o la ablación por láser.
- Evaporación:El material se calienta a alta temperatura hasta que se vaporiza.Para ello se suele utilizar un haz de electrones o un calentamiento resistivo.
- Pulverización catódica:Se utilizan iones de alta energía para bombardear el material objetivo, haciendo que los átomos sean expulsados de la superficie y entren en la fase de vapor.
- Ablación por láser:Se utiliza un láser de alta potencia para vaporizar directamente el material.
-
Migración de las partículas vaporizadas:
- Una vez que el material se encuentra en la fase de vapor, las partículas (átomos, moléculas o iones) migran a través de la cámara de vacío.En esta migración influye el entorno de vacío, que minimiza las colisiones con otras partículas y garantiza una deposición limpia.
- Durante esta fase, las partículas vaporizadas pueden sufrir reacciones, especialmente si se introducen gases reactivos (como nitrógeno u oxígeno) en la cámara.Estas reacciones pueden formar compuestos que luego se depositan sobre el sustrato.
-
Deposición sobre el sustrato:
- El último paso es la deposición del material vaporizado sobre el sustrato.Esto ocurre cuando las partículas vaporizadas se condensan en la superficie más fría del sustrato, formando una película fina y uniforme.
- El sustrato suele mantenerse a una temperatura inferior a la del material vaporizado, lo que favorece la condensación y la adherencia del revestimiento.
- El grosor de la película depositada puede controlarse con precisión mediante técnicas como la monitorización de la velocidad de cristal de cuarzo, que mide la velocidad de deposición y la ajusta según sea necesario.
-
Utilización de plasma y gases reactivos:
- En muchos procesos de PVD, el plasma se utiliza para mejorar el proceso de vaporización y deposición.El plasma se crea ionizando un gas, a menudo utilizando una fuente de plasma de acoplamiento inductivo (ICP).
- El plasma de alta energía puede ayudar a disociar las moléculas de gas en especies reactivas, que luego pueden reaccionar con el material vaporizado para formar compuestos.Esto resulta especialmente útil para crear revestimientos duros y resistentes al desgaste, como el nitruro de titanio (TiN) o el nitruro de cromo (CrN).
- La introducción de gases reactivos (por ejemplo, nitrógeno, oxígeno) permite la formación de revestimientos compuestos, que pueden tener propiedades superiores en comparación con los revestimientos de metal puro.
-
Entorno de vacío:
-
Todo el proceso de PVD se lleva a cabo en un entorno de alto vacío.Esto es crucial por varias razones:
- Pureza:El vacío minimiza la presencia de contaminantes, garantizando una deposición limpia.
- Control:La baja presión permite un control preciso del proceso de deposición, incluida la velocidad y la uniformidad del revestimiento.
- Control de la reacción:El entorno de vacío ayuda a controlar las reacciones entre el material vaporizado y cualquier gas reactivo, garantizando propiedades de recubrimiento consistentes.
-
Todo el proceso de PVD se lleva a cabo en un entorno de alto vacío.Esto es crucial por varias razones:
-
Aplicaciones de los revestimientos PVD:
-
Los revestimientos PVD se utilizan en una amplia gama de aplicaciones, entre las que se incluyen:
- Resistencia al desgaste:Recubrimientos como TiN y CrN se utilizan para mejorar la resistencia al desgaste de herramientas de corte, moldes y otros componentes.
- Resistencia a la corrosión:Los revestimientos de PVD pueden proporcionar una barrera contra la corrosión, prolongando la vida útil de los componentes expuestos a entornos agresivos.
- Acabados decorativos:El PVD se utiliza para crear revestimientos decorativos con una amplia gama de colores y acabados, a menudo vistos en electrónica de consumo y joyería.
- Recubrimientos ópticos:El PVD se utiliza para depositar películas finas con propiedades ópticas específicas, como revestimientos antirreflectantes en lentes.
-
Los revestimientos PVD se utilizan en una amplia gama de aplicaciones, entre las que se incluyen:
En resumen, el proceso PVD es un método muy controlado y versátil para depositar películas finas de material sobre un sustrato.Implica la vaporización del material de revestimiento, la migración de las partículas vaporizadas y la deposición sobre el sustrato, todo ello realizado en un entorno de vacío.El uso de plasma y gases reactivos permite crear revestimientos compuestos con propiedades mejoradas, lo que convierte al PVD en una técnica valiosa en diversas aplicaciones industriales.
Cuadro sinóptico:
Pasos clave | Descripción |
---|---|
Vaporización | El material de revestimiento se vaporiza mediante evaporación, pulverización catódica o ablación láser. |
Migración | Las partículas vaporizadas se mueven a través del vacío, minimizando las colisiones. |
Deposición | Las partículas se condensan en el sustrato, formando una película fina y uniforme. |
Plasma y gases reactivos | Mejora las propiedades del revestimiento, por ejemplo, formando TiN o CrN para la resistencia al desgaste. |
Entorno de vacío | Garantiza la pureza, el control y la consistencia de la reacción durante la deposición. |
Aplicaciones | Resistencia al desgaste, protección contra la corrosión, acabados decorativos y revestimientos ópticos. |
Descubra cómo los revestimientos PVD pueden mejorar sus productos. contacte hoy mismo con nuestros expertos ¡!