El ciclo de sinterización es un proceso crítico en la ciencia y la fabricación de materiales, en el que los materiales en polvo se transforman en cuerpos densos y sólidos mediante la aplicación de calor y presión, sin alcanzar el punto de fusión del material. Este proceso se utiliza ampliamente en industrias como la pulvimetalurgia, la cerámica y los plásticos para crear productos duraderos y cohesivos. El ciclo de sinterización suele constar de varias etapas, como la preparación del polvo, la compactación y el calentamiento controlado, seguidos del enfriamiento. Cada etapa desempeña un papel vital para garantizar la integridad estructural del producto final y las propiedades deseadas.
Explicación de los puntos clave:
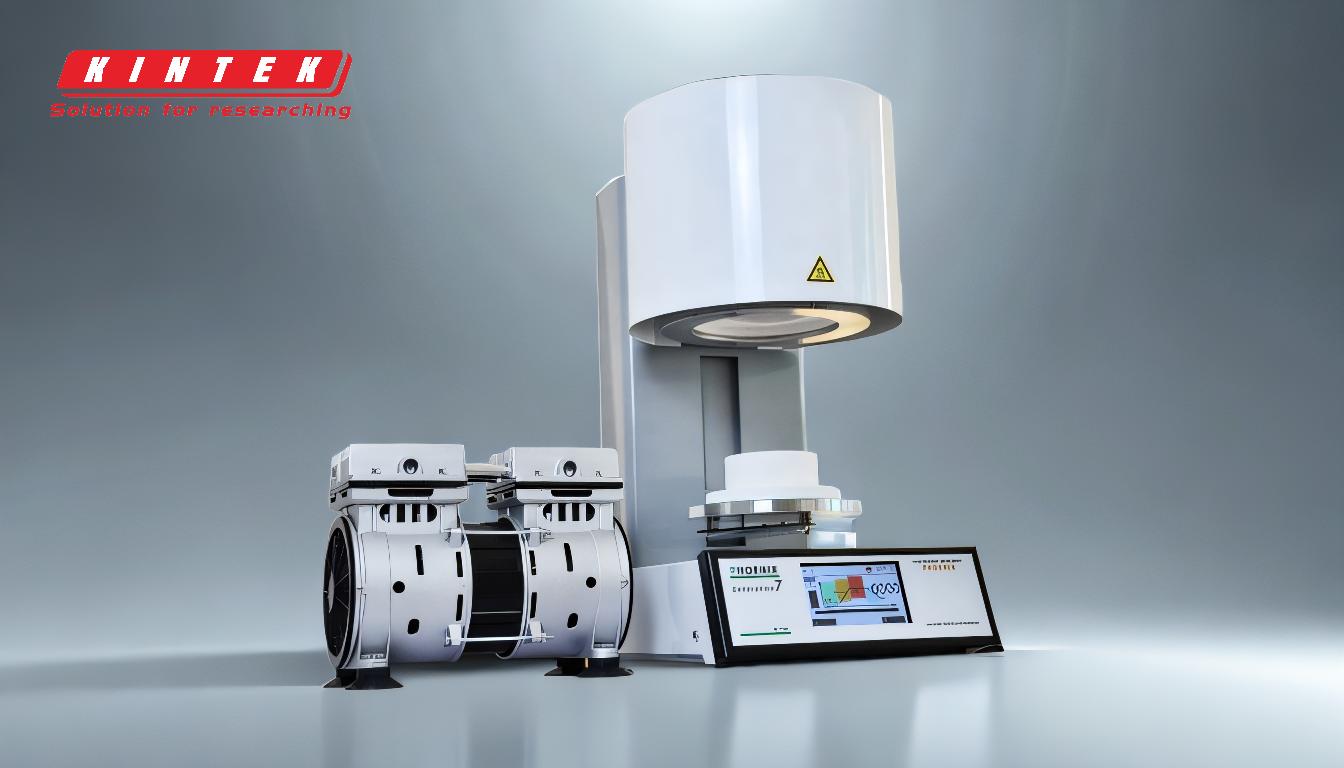
-
Definición y finalidad de la sinterización:
- La sinterización es un proceso que fusiona pequeñas partículas en una masa sólida sin fundir el material. Se utiliza para crear productos densos y duraderos a partir de materiales en polvo como metales, cerámica y plásticos.
- El objetivo principal de la sinterización es unir partículas de polvo adyacentes, lo que da lugar a una estructura cohesiva con propiedades mecánicas mejoradas, como resistencia, dureza y durabilidad.
-
Etapas del ciclo de sinterización:
-
Preparación del polvo:
- El proceso comienza con la preparación de las materias primas en forma de polvo. Esto puede implicar la mezcla de polvos con aditivos como aglutinantes, defloculantes y agua para crear una pasta, que luego se seca por pulverización para formar gránulos.
-
Compactación:
- El polvo preparado se compacta mediante presión mecánica, ya sea por prensado en frío o en caliente, para formar una pieza "verde". Esta etapa garantiza la uniformidad y elimina los huecos en el material.
-
Sinterización (cocción):
- La pieza verde se calienta en un entorno controlado, normalmente en un horno de sinterización. La temperatura se regula cuidadosamente para facilitar la unión de las partículas mediante difusión, lo que conduce a la formación de cuellos y a la densificación. El material no se funde, sino que experimenta una difusión atómica que fusiona las partículas.
-
Enfriamiento:
- Tras la sinterización, el material se enfría gradualmente para permitir que se solidifique en una estructura rígida y cohesiva. Esta etapa es crucial para conseguir las propiedades mecánicas deseadas y evitar defectos.
-
Preparación del polvo:
-
Factores clave que influyen en el proceso de sinterización:
-
Temperatura:
- La temperatura de sinterización debe ser lo suficientemente alta para favorecer la unión de las partículas, pero inferior al punto de fusión del material para evitar la licuefacción.
-
Presión:
- La presión aplicada durante la compactación garantiza una densidad uniforme y reduce la porosidad en la parte verde.
-
Tiempo:
- La duración de la sinterización afecta al grado de unión y densificación de las partículas. Los tiempos de sinterización más largos suelen dar lugar a uniones más fuertes, pero deben equilibrarse con el consumo de energía y la eficiencia de la producción.
-
Atmósfera:
- El entorno de sinterización (por ejemplo, gas inerte, vacío o aire) puede influir en las propiedades finales del material evitando la oxidación o facilitando reacciones químicas específicas.
-
Temperatura:
-
Aplicaciones de la sinterización:
-
Metalurgia de polvos:
- La sinterización se utiliza ampliamente para fabricar componentes metálicos como engranajes, cojinetes y piezas de automoción. Permite crear formas complejas con gran precisión y mínimos residuos.
-
Cerámica:
- En la industria cerámica, el sinterizado se utiliza para fabricar baldosas, aislantes y otros productos de gran estabilidad térmica y mecánica.
-
Plásticos y compuestos:
- El sinterizado se emplea para crear componentes plásticos duraderos y materiales compuestos con propiedades a medida.
-
Metalurgia de polvos:
-
Ventajas de la sinterización:
-
Rentabilidad:
- El sinterizado reduce el desperdicio de material y permite la producción de componentes de forma casi neta, minimizando la necesidad de mecanizado adicional.
-
Versatilidad de materiales:
- El proceso puede aplicarse a una amplia gama de materiales, incluidos metales, cerámicas y polímeros.
-
Propiedades mejoradas:
- Los productos sinterizados presentan una mayor resistencia mecánica, dureza y resistencia al desgaste debido a la densificación y unión de las partículas.
-
Rentabilidad:
-
Retos y consideraciones:
-
Control de los parámetros del proceso:
- Para obtener resultados uniformes es necesario un control preciso de la temperatura, la presión y el tiempo, lo que puede resultar difícil en la producción a gran escala.
-
Limitaciones de los materiales:
- No todos los materiales son adecuados para la sinterización, especialmente los que tienen puntos de fusión bajos o poca estabilidad térmica.
-
Costes del equipo:
- Los hornos y prensas de sinterización pueden ser caros, sobre todo para aplicaciones de alta temperatura o alta presión.
-
Control de los parámetros del proceso:
En resumen, el ciclo de sinterización es un proceso versátil y esencial en la fabricación moderna, que permite la producción de materiales y componentes de alto rendimiento. Al comprender las etapas, los factores que influyen y las aplicaciones del sinterizado, los fabricantes pueden optimizar el proceso para satisfacer los requisitos específicos del producto y lograr resultados superiores.
Tabla resumen:
Aspecto | Detalles |
---|---|
Definición | Fusiona partículas de polvo en una masa sólida sin fundir el material. |
Etapas | Preparación del polvo, compactación, sinterización (cocción), enfriamiento. |
Factores clave | Temperatura, presión, tiempo, atmósfera. |
Aplicaciones | Pulvimetalurgia, cerámica, plásticos y materiales compuestos. |
Ventajas | Rentabilidad, versatilidad de materiales, propiedades mecánicas mejoradas. |
Desafíos | Control preciso de los parámetros, Limitaciones de los materiales, Costes elevados de los equipos. |
Optimice su proceso de sinterización con el asesoramiento de expertos. póngase en contacto con nosotros ¡!