La temperatura de sinterización de las piezas cerámicas varía considerablemente en función del tipo de material cerámico y de la aplicación prevista.Por lo general, la sinterización se produce entre el 50% y el 75% de la temperatura de fusión de la cerámica, que suele superar los 1000°C.Por ejemplo, el óxido de circonio dental requiere altas temperaturas, entre 1.400 °C y 1.600 °C, para alcanzar una dureza y resistencia óptimas, con un control preciso para evitar el crecimiento del grano y la pérdida de resistencia.Las cerámicas técnicas avanzadas pueden requerir entornos aún más controlados, mientras que las cerámicas más sencillas, como la porcelana, pueden sinterizarse a temperaturas más bajas en hornos básicos.El proceso de sinterización es fundamental para conseguir la densidad, dureza e integridad estructural deseadas de las piezas cerámicas.
Explicación de los puntos clave:
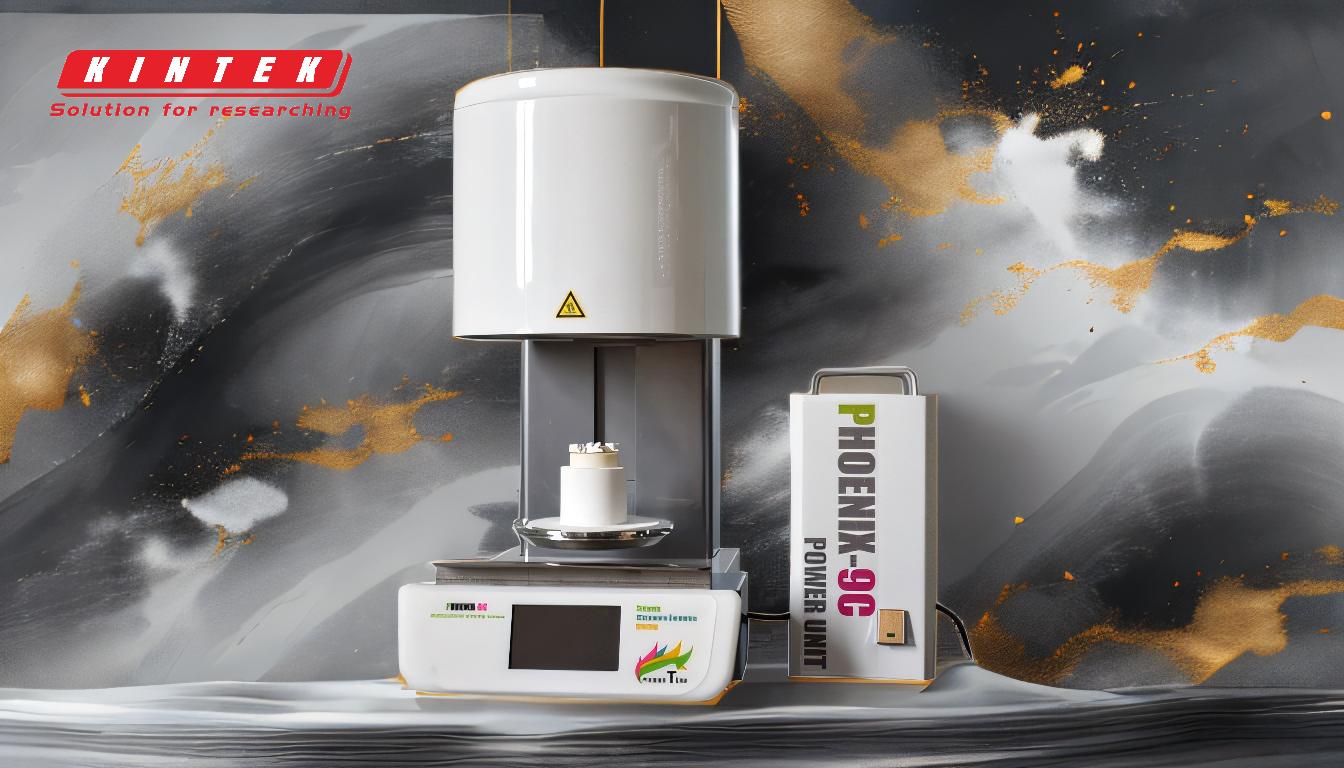
-
Rango general de temperaturas de sinterización:
- Los materiales cerámicos se sinterizan normalmente entre el 50% y el 75% de su temperatura de fusión, que suele ser superior a 1000°C.Este rango garantiza que el material alcance más del 95% de su densidad teórica, lo que es esencial para lograr las propiedades mecánicas deseadas.
-
Sinterización de óxido de circonio dental:
- La zirconia dental requiere una sinterización a altas temperaturas, entre 1400°C y 1600°C.Este intervalo es crítico para conseguir la dureza y resistencia necesarias para las aplicaciones dentales.
- Estudios recientes indican que la cocción de la zirconia entre 1500°C y 1550°C produce la máxima resistencia.Las desviaciones de este intervalo, incluso de sólo 150°C, pueden provocar una pérdida significativa de resistencia debido al crecimiento del grano.
-
Sinterización de compuestos cerámicos:
- Los materiales compuestos cerámicos se sinterizan normalmente a temperaturas comprendidas entre 900°C y 1250°C.Este rango es adecuado para conseguir las propiedades deseadas en los materiales compuestos, que pueden incluir una combinación de diferentes fases cerámicas.
-
Importancia del control de la temperatura:
- El proceso de sinterización es muy sensible al control de la temperatura, especialmente durante las fases de aumento, mantenimiento y enfriamiento.Por ejemplo, la velocidad de rampa desde 900°C hasta la temperatura máxima, la constancia de la temperatura durante el tiempo de mantenimiento y la velocidad de enfriamiento de vuelta a unos 900°C son factores críticos que influyen en las propiedades finales de la cerámica.
-
Variabilidad en función del tipo de cerámica:
- Los distintos tipos de cerámica requieren condiciones de sinterización diferentes.Por ejemplo, la porcelana puede sinterizarse en un horno sencillo de bajo coste, mientras que las cerámicas técnicas avanzadas sin óxido necesitan una sinterización a alta temperatura controlada con precisión en una atmósfera estabilizadora.Esta variabilidad se debe a las diferencias en la composición del material y las propiedades finales deseadas.
-
Impacto de la temperatura en las propiedades del material:
- La temperatura de sinterización afecta directamente a la densidad, dureza y resistencia del material.Por ejemplo, la cocción de la zirconia a 1.500 °C da como resultado una resistencia de unos 1.280 MPa, mientras que la cocción a 1.600 °C reduce la resistencia a unos 980 MPa, y a 1.700 °C, desciende a unos 600 MPa.Esto pone de manifiesto la importancia de un control preciso de la temperatura para conseguir un rendimiento óptimo del material.
-
Consideraciones prácticas para los equipos:
- Al seleccionar el equipo de sinterización, es fundamental tener en cuenta los requisitos específicos de temperatura del material cerámico que se va a procesar.Los hornos de alta temperatura con un control preciso de la temperatura son necesarios para las cerámicas avanzadas, mientras que los hornos más sencillos pueden ser suficientes para cerámicas básicas como la porcelana.
En resumen, la temperatura de sinterización de las piezas cerámicas es un parámetro crítico que varía en función del material y la aplicación.El control preciso de la temperatura es esencial para conseguir las propiedades mecánicas deseadas, y la elección del equipo de sinterización debe ajustarse a los requisitos específicos de la cerámica que se va a procesar.
Tabla resumen:
Tipo de cerámica | Temperatura de sinterización | Consideraciones clave |
---|---|---|
Cerámica en general | 50%-75% de la temperatura de fusión (>1000°C) | Garantiza una densidad teórica >95%, crítica para las propiedades mecánicas. |
Circonio dental | 1400°C - 1600°C | Dureza y resistencia óptimas; las desviaciones provocan crecimiento de grano y pérdida de resistencia. |
Compuestos cerámicos | 900°C - 1250°C | Adecuado para conseguir las propiedades deseadas en materiales multifásicos. |
Porcelana | Temperaturas más bajas en hornos básicos | Proceso de sinterización más sencillo; sin necesidad de equipos avanzados. |
Cerámica técnica avanzada | Altas temperaturas con un control preciso | Requiere atmósferas estabilizadoras y una gestión precisa de la temperatura. |
¿Necesita ayuda para seleccionar el equipo de sinterización adecuado para su cerámica? Póngase en contacto con nuestros expertos hoy mismo ¡!