El endurecimiento por inducción es un proceso de endurecimiento de superficies muy eficaz que se utiliza principalmente para componentes de acero y hierro fundido. Implica el calentamiento localizado de la superficie del metal utilizando un campo magnético alterno generado por una bobina inductora, seguido de un enfriamiento rápido (templado) para lograr el endurecimiento de la superficie. Este proceso mejora la resistencia al desgaste, la resistencia a la fatiga y la tenacidad en áreas específicas de la pieza mientras mantiene la ductilidad del núcleo. El endurecimiento por inducción se utiliza ampliamente en industrias como la fabricación de automóviles para piezas como cigüeñales, árboles de levas y engranajes, donde la durabilidad de la superficie es fundamental. El proceso es versátil y permite controlar la profundidad y la intensidad del endurecimiento ajustando factores como la frecuencia, la densidad de potencia y el tiempo de calentamiento.
Puntos clave explicados:
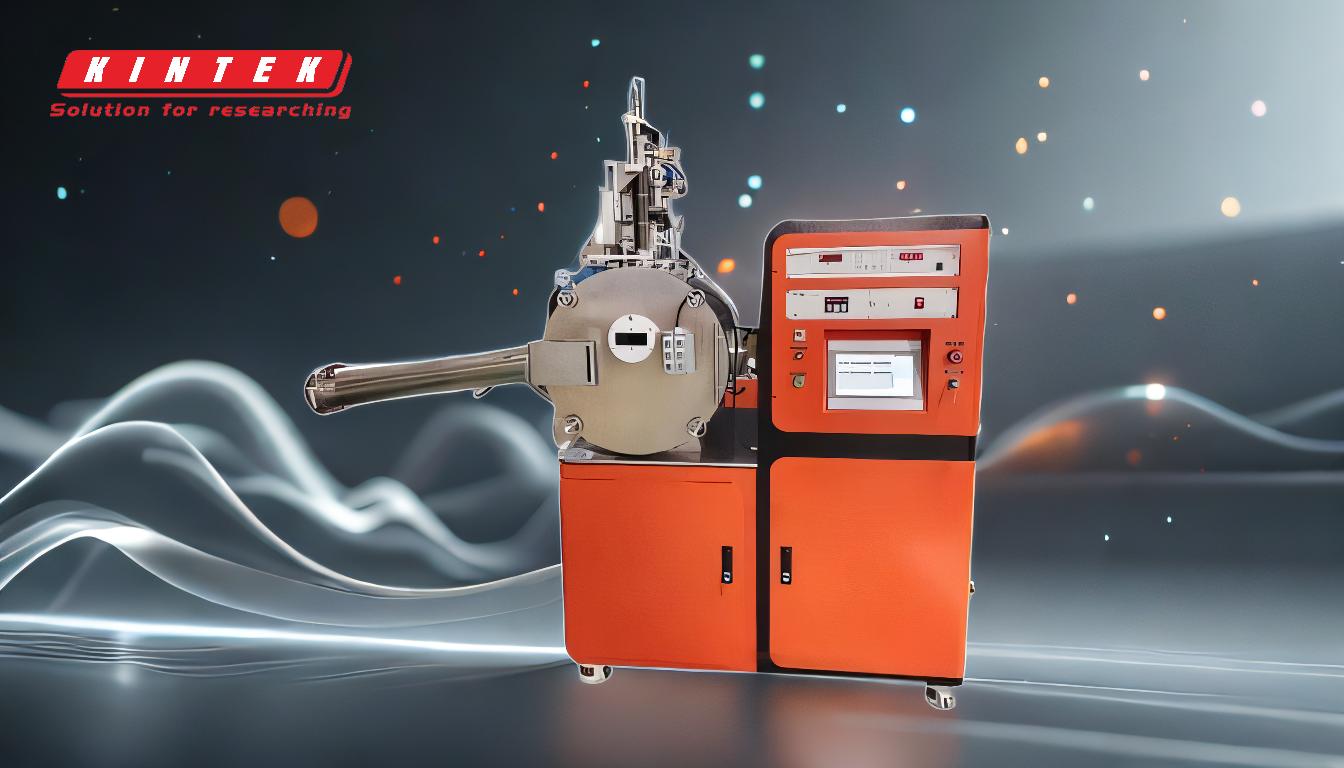
-
Metales aptos para el endurecimiento por inducción:
- Acero: El endurecimiento por inducción se aplica más comúnmente al acero debido a su capacidad de transformarse en martensita (una fase dura y resistente al desgaste) cuando se calienta y se enfría rápidamente. Los ejemplos incluyen aceros al carbono, aceros aleados y aceros para herramientas.
- Hierro fundido: Ciertos tipos de hierro fundido, como el hierro dúctil y el hierro gris, también pueden endurecerse por inducción. El proceso mejora la dureza de su superficie y la resistencia al desgaste, haciéndolos adecuados para aplicaciones exigentes.
- Aplicabilidad limitada a otros metales: El endurecimiento por inducción no se utiliza normalmente para metales no ferrosos (por ejemplo, aluminio, cobre) porque carecen de las propiedades de transformación de fase necesarias para lograr un endurecimiento significativo.
-
Cómo funciona el endurecimiento por inducción:
- La pieza de trabajo se coloca dentro de una bobina inductora, que transporta una corriente alterna de alta frecuencia.
- La corriente alterna genera un campo magnético que induce corrientes parásitas dentro de la pieza de trabajo.
- Debido al efecto piel, las corrientes parásitas se concentran en la superficie, generando calor que eleva la temperatura de la superficie por encima del punto crítico de transformación del material.
- Sigue un enfriamiento rápido (enfriamiento), transformando la capa superficial calentada en martensita, una fase dura y quebradiza.
-
Ventajas del endurecimiento por inducción:
- Endurecimiento localizado: Sólo se endurecen áreas específicas de la pieza, preservando la tenacidad del material del núcleo.
- Profundidad controlada: La profundidad de endurecimiento se puede ajustar variando la frecuencia de la corriente alterna (las frecuencias más altas dan como resultado un endurecimiento menos profundo).
- Eficiencia: El proceso es más rápido y más eficiente energéticamente en comparación con los métodos tradicionales de cementación.
- Propiedades mecánicas mejoradas: Se logra una mayor resistencia al desgaste, resistencia a la fatiga y dureza de la superficie sin comprometer la integridad general de la pieza.
-
Aplicaciones en la industria automotriz:
- El endurecimiento por inducción se utiliza ampliamente en componentes automotrices como cigüeñales, árboles de levas, engranajes y ejes.
- Estas piezas operan en condiciones difíciles y requieren alta resistencia al desgaste, resistencia a la flexión y resistencia a la fatiga.
- El proceso garantiza que las superficies críticas se endurezcan manteniendo al mismo tiempo la ductilidad del núcleo, que es esencial para la durabilidad y el rendimiento.
-
Factores que influyen en el endurecimiento por inducción:
- Composición de materiales: El contenido de carbono y los elementos de aleación del metal determinan su templabilidad.
- Frecuencia: Las frecuencias más altas (por ejemplo, 100-500 kHz) se utilizan para un endurecimiento superficial, mientras que las frecuencias más bajas (por ejemplo, 1-10 kHz) son adecuadas para un endurecimiento más profundo.
- Densidad de potencia y tiempo de calentamiento: Estos parámetros controlan la intensidad y duración del calentamiento, afectando la dureza y profundidad de la capa endurecida.
- Medio de enfriamiento: La elección del medio de enfriamiento (por ejemplo, agua, aceite, polímero) influye en la velocidad de enfriamiento y la dureza final.
-
Limitaciones del endurecimiento por inducción:
- Complejidad de la forma: El proceso es más adecuado para piezas con geometrías simples. Las formas complejas pueden provocar un calentamiento y endurecimiento desiguales.
- Restricciones de materiales: Sólo los metales ferrosos (acero y hierro fundido) pueden endurecerse por inducción de forma eficaz debido a sus propiedades de transformación de fase.
- Costo del equipo: Los sistemas de endurecimiento por inducción de alta frecuencia pueden ser costosos, lo que hace que el proceso sea menos económico para aplicaciones a pequeña escala.
-
Comparación con otros métodos de endurecimiento:
- Endurecimiento: A diferencia del endurecimiento por cementación, que implica la difusión de carbono o nitrógeno en la superficie, el endurecimiento por inducción se basa en calentamiento y enfriamiento localizados.
- Endurecimiento a la llama: El endurecimiento por inducción es más preciso y controlable en comparación con el endurecimiento por llama, que utiliza una llama abierta para calentar.
- Endurecimiento por láser: Si bien el endurecimiento por láser ofrece una precisión aún mayor, el endurecimiento por inducción es más rentable para piezas más grandes y producciones de gran volumen.
En resumen, el endurecimiento por inducción es un proceso versátil y eficiente para mejorar las propiedades superficiales de componentes de acero y hierro fundido. Su capacidad para proporcionar un endurecimiento localizado con profundidad controlada lo hace ideal para aplicaciones en las industrias automotriz y de maquinaria, donde la resistencia al desgaste y la durabilidad son fundamentales. Sin embargo, su idoneidad se limita a metales ferrosos y piezas con geometrías relativamente simples.
Tabla resumen:
Aspecto | Detalles |
---|---|
Metales adecuados | Acero (carbono, aleación, herramientas), Hierro fundido (dúctil, gris) |
Proceso | Calentamiento localizado mediante un campo magnético alterno, seguido de un enfriamiento rápido |
Ventajas clave | Profundidad controlada, eficiencia energética, propiedades mecánicas mejoradas. |
Aplicaciones | Piezas de automoción (cigüeñales, engranajes, árboles de levas, ejes) |
Factores que influyen | Composición del material, frecuencia, densidad de potencia, medio de enfriamiento. |
Limitaciones | Limitado a metales ferrosos, formas complejas y alto coste de equipamiento. |
Descubra cómo el endurecimiento por inducción puede optimizar el rendimiento de sus componentes. contáctenos hoy ¡Para orientación experta!