El control de la atmósfera durante la sinterización es esencial para conseguir las propiedades deseadas del material sinterizado.La atmósfera de sinterización influye directamente en los procesos químicos y físicos que tienen lugar durante la sinterización, como la oxidación, la reducción y la difusión.Seleccionando una atmósfera adecuada, ya sea inerte, protectora o reductora, los fabricantes pueden evitar reacciones no deseadas, como la oxidación, y favorecer otras beneficiosas, como la reducción de los óxidos superficiales.Esto garantiza que el producto final tenga las propiedades mecánicas, térmicas y químicas requeridas.Además, la atmósfera afecta a la consistencia de la temperatura durante la sinterización, que es fundamental para controlar la difusión de los límites de grano y la masa, determinando en última instancia la microestructura y el rendimiento del material.
Explicación de los puntos clave:
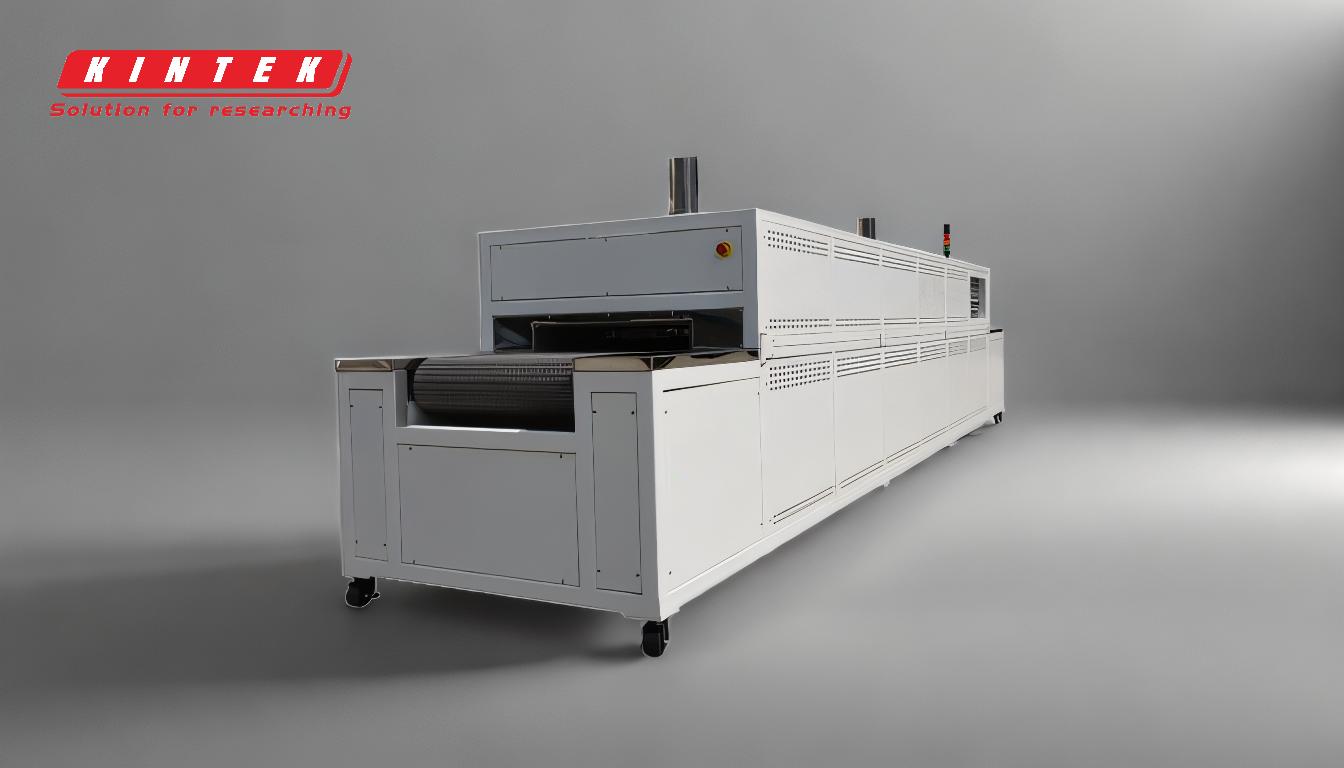
-
Prevención de la oxidación y la contaminación:
- La sinterización a menudo implica compuestos metálicos que son propensos a la oxidación cuando se exponen al aire a altas temperaturas.La oxidación puede degradar las propiedades del material, como la resistencia y la ductilidad.
- Una atmósfera inerte o protectora (por ejemplo, argón, nitrógeno) evita la oxidación al excluir el oxígeno del entorno de sinterización.
- Una atmósfera reductora (por ejemplo, hidrógeno) puede reducir activamente los óxidos superficiales, garantizando una superficie limpia y libre de óxido, lo que es fundamental para lograr una fuerte unión entre partículas.
-
Control de las reacciones químicas:
- La atmósfera de sinterización influye en las reacciones químicas que se producen durante el proceso.Por ejemplo, en una atmósfera reductora, el hidrógeno puede reaccionar con los óxidos de la superficie del polvo, convirtiéndolos de nuevo en metal puro.
- Este control es especialmente importante en materiales como el wolframio, el molibdeno y determinados materiales cerámicos, en los que la formación de óxidos puede alterar significativamente las propiedades del material.
-
Optimización de los procesos de difusión:
- La sinterización se basa en mecanismos de difusión, como la difusión en el límite de grano y la difusión en masa, para lograr la densificación y la unión entre partículas.
- La atmósfera influye en la velocidad y la eficacia de estos procesos de difusión.Por ejemplo, una atmósfera reductora puede mejorar la difusión al eliminar las barreras de óxido, mientras que una atmósfera inerte garantiza una difusión constante sin introducir impurezas.
-
Consistencia y control de la temperatura:
- La atmósfera de sinterización ayuda a mantener perfiles de temperatura constantes, especialmente durante fases críticas como el calentamiento desde 900°C hasta la temperatura máxima, el mantenimiento a la temperatura máxima y el enfriamiento de nuevo a 900°C.
- El control constante de la temperatura es vital para conseguir microestructuras uniformes y evitar defectos como alabeos o grietas.
-
Conseguir las propiedades deseadas del material:
- La elección de la atmósfera de sinterización influye directamente en las propiedades finales del material sinterizado, como la densidad, la resistencia, la dureza y la conductividad térmica.
- Por ejemplo, la sinterización en una atmósfera de hidrógeno puede mejorar la densidad y las propiedades mecánicas de determinados metales al favorecer una mejor unión de las partículas y reducir la porosidad.
-
Rentabilidad y eficiencia:
- Seleccionar la atmósfera adecuada puede optimizar el proceso de sinterización, reduciendo el consumo de energía y el desperdicio de material.
- Por ejemplo, el uso de una atmósfera reductora puede eliminar la necesidad de tratamientos adicionales posteriores a la sinterización para eliminar los óxidos, ahorrando tiempo y recursos.
-
Requisitos específicos de los materiales:
-
Los distintos materiales requieren atmósferas de sinterización específicas.Por ejemplo:
- Las atmósferas inertes son adecuadas para materiales como el titanio y el circonio, que son muy reactivos con el oxígeno.
- Las atmósferas reductoras son ideales para metales como el cobre y el hierro, donde la reducción de óxidos es necesaria para una sinterización óptima.
- Comprender estos requisitos garantiza que el proceso de sinterización se adapte al material y se obtengan los mejores resultados.
-
Los distintos materiales requieren atmósferas de sinterización específicas.Por ejemplo:
En resumen, el control de la atmósfera de sinterización es fundamental para evitar la oxidación, optimizar las reacciones químicas, garantizar perfiles de temperatura uniformes y conseguir las propiedades deseadas del material.También mejora la eficacia del proceso y la rentabilidad, por lo que es un aspecto indispensable de la tecnología de sinterización.
Cuadro sinóptico:
Factor clave | Impacto en la sinterización |
---|---|
Prevención de la oxidación | Las atmósferas inertes o protectoras (por ejemplo, argón, nitrógeno) evitan la oxidación. |
Control de las reacciones químicas | Las atmósferas reductoras (por ejemplo, hidrógeno) convierten los óxidos en metal puro. |
Optimización de la difusión | Mejora la difusión en el límite del grano y en la masa para una mejor densificación. |
Consistencia de la temperatura | Garantiza un calentamiento y enfriamiento uniformes, evitando defectos como el alabeo. |
Propiedades del material | Influye en la densidad, resistencia, dureza y conductividad térmica. |
Rentabilidad | Reduce el consumo de energía y elimina los tratamientos posteriores al sinterizado. |
Requisitos específicos del material | Adapta la atmósfera a materiales como titanio, circonio, cobre y hierro. |
¿Está listo para optimizar su proceso de sinterización? Póngase en contacto con nuestros expertos para obtener soluciones a medida.