Introducción
Índice de contenidos
- Introducción
- Visión general del prensado isostático en frío
- Tipos de prensado isostático en frío
- Ventajas del prensado isostático en frío sobre el prensado con matriz uniaxial
- Prensado isostático en frío en la producción de componentes de formas complejas
- Comparación entre el CIP y el moldeo por inyección para la producción de grandes volúmenes
- Resumen histórico del uso del CIP en la fabricación de cerámica de alúmina
- Uso de la CIP en la producción de aislantes para bujías de encendido
- Prensas isostáticas en frío
- Prensado isostático en frío
- DESCRIPCIÓN DEL PRENSADO ISOSTÁTICO EN FRÍO
- Prensado isostático en frío
- Proceso de prensado isostático en frío
- Ventajas del prensado isostático en frío para cerámica de alúmina
- Desventajas del prensado isostático en frío para cerámica
- Aplicaciones del prensado isostático en frío
- Tecnologías de compresión alternativas
- Conclusión
El prensado isostático en frío (CIP)es un proceso de fabricación muy utilizado en diversas industrias, como la cerámica, la metalúrgica y la farmacéutica. Consiste en aplicar la misma presión desde todas las direcciones a un material colocado dentro de un molde o bolsa flexible. Este proceso ayuda a conseguir una densidad uniforme y a dar forma a componentes complejos con geometrías intrincadas. El CIP ofrece varias ventajas sobre el prensado uniaxial tradicional, como la capacidad de dar forma a piezas más complejas y la reducción de distorsiones y grietas debido al empaquetado uniforme de las partículas. En esta entrada del blog, profundizaremos en la aplicación, las ventajas y las limitaciones del prensado isostático en frío.
Visión general del prensado isostático en frío
Explicación del prensado isostático en frío
El prensado isostático en frío (CIP) es una técnica de procesamiento de materiales que consiste en aplicar la misma presión en todas las direcciones a un material en polvo. Este proceso se utiliza para comprimir el polvo y convertirlo en una masa sólida, creando una pieza bruta con la resistencia suficiente para su manipulación y posterior procesamiento.
Diferenciación entre prensado isostático en bolsa húmeda y en bolsa seca
Una variante del prensado isostático en frío es la tecnología de bolsa húmeda. En este proceso, el polvo se introduce en un molde y se sella herméticamente fuera del recipiente de presión. A continuación, el molde se sumerge en un fluido a alta presión dentro del recipiente y se aplica presión isostática para comprimir el polvo y darle forma. La tecnología de bolsa húmeda es ideal para la producción de múltiples formas y de pequeñas a grandes cantidades.
Por otro lado, el prensado isostático en bolsa seca implica la creación de un molde integrado dentro del propio recipiente a presión. El polvo se añade al molde, éste se sella y se aplica presión para comprimirlo. Este proceso elimina la necesidad de sumergir el molde en un fluido separado, lo que facilita la automatización.
Papel de la calidad del polvo y el diseño de las herramientas en el proceso
La calidad del polvo utilizado en el prensado isostático en frío desempeña un papel crucial en el producto final. El polvo debe tener una distribución granulométrica, una fluidez y una densidad adecuadas para garantizar una compresión eficaz y uniforme. Además, el diseño del utillaje, incluido el molde o la bolsa utilizados, debe diseñarse cuidadosamente para adaptarse a los requisitos específicos del material en polvo y la forma deseada.
El diseño adecuado del utillaje y la calidad del polvo son esenciales para conseguir la densidad y resistencia deseadas en el producto final. Esto es especialmente importante en industrias como la aeroespacial, la automovilística y la médica, donde los componentes fiables y de alta calidad son cruciales.
En resumen, el prensado isostático en frío es una técnica versátil de procesamiento de materiales que permite comprimir materiales en polvo para convertirlos en piezas sólidas. La elección entre la tecnología de bolsa húmeda y la de bolsa seca depende de los requisitos específicos de producción. Además, la calidad del polvo y el diseño del utillaje desempeñan un papel importante a la hora de garantizar los resultados deseados en el producto final.
Tipos de prensado isostático en frío
Descripción detallada de la técnica de bolsa húmeda
En la técnica de bolsa húmeda de prensado isostático en frío, el material en polvo se rellena en un molde y se sella herméticamente fuera del recipiente a presión. A continuación, el molde lleno se sumerge en un fluido a presión dentro del recipiente a presión. Se aplica presión isostática a la superficie externa del molde, comprimiendo el polvo hasta convertirlo en una masa sólida.
Este método no es tan común como el otro tipo de prensado isostático en frío, pero hay más de 3000 prensas de bolsas húmedas utilizadas en todo el mundo. Las bolsas húmedas vienen en varios tamaños, desde 50 mm hasta 2000 mm de diámetro.
El procesado de material mediante la tecnología de bolsas húmedas puede durar entre 5 y 30 minutos, lo que lo convierte en un proceso relativamente lento. Sin embargo, el uso de bombas de gran volumen y la mejora de los mecanismos de carga pueden ayudar a acelerar el proceso.
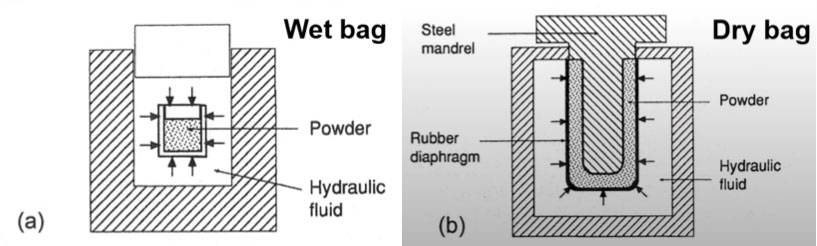
Prensado isostático con bolsa húmeda
Dar forma previa a la muestra, cargarla en una bolsa blanda (vacío) y sumergirla en fluido hidráulico, aplicar alta presión " Se utiliza para formas complejas y muestras de gran tamaño"
Explicación de la técnica de prensado con bolsa seca
La técnica de prensado en bolsa seca, por su parte, implica la creación de un molde integrado en el recipiente a presión. En este proceso, el polvo se añade al molde, que luego se sella. Se aplica presión y se expulsa la pieza resultante.
En comparación con la técnica de la bolsa húmeda, el proceso de la bolsa seca se presta a la automatización y es adecuado para prensar tiradas largas de compactos a altos ritmos de producción. La integración del molde en el recipiente de presión elimina la necesidad del paso de inmersión, lo que lo convierte en un método más eficaz.
Comparación de las aplicaciones de ambas técnicas
La elección entre las técnicas de bolsa húmeda y bolsa seca depende de los requisitos específicos de la aplicación. La tecnología de bolsa húmeda es ideal para la producción de múltiples formas y de pequeñas a grandes cantidades, así como para el prensado de productos de gran tamaño. Permite crear formas intrincadas y consigue una alta densidad de verde.
Por otro lado, el prensado de bolsas secas es más adecuado para la automatización y las altas tasas de producción. Ofrece una integración más fácil en el proceso de fabricación y elimina el paso de inmersión, lo que se traduce en tiempos de producción más rápidos.
En resumen, tanto la técnica de la bolsa húmeda como la de la bolsa seca tienen sus ventajas y se utilizan en distintas aplicaciones. La decisión entre una y otra depende de factores como la forma deseada, la cantidad de producción y el nivel de automatización requerido.
Ventajas del prensado isostático en frío sobre el prensado con matriz uniaxial
Capacidad para conformar formas más complejas
El prensado isostático en frío (CIP) ofrece la ventaja de poder conformar formas más complejas en comparación con el prensado uniaxial. Con el CIP, la presión se aplica uniformemente sobre toda la superficie del molde, lo que permite la compactación de formas intrincadas y detalladas. Esto es especialmente beneficioso cuando se fabrican componentes con geometrías o diseños intrincados que pueden ser difíciles de conseguir con el Prensado Uniaxial.

Reducción de las distorsiones y el agrietamiento gracias al empaquetado uniforme de las partículas
Una de las principales ventajas del Prensado Isostático en Frío sobre el Prensado Uniaxial es la reducción de distorsiones y grietas en el producto final. En el prensado isostático en frío, la presión se aplica uniformemente, lo que da lugar a un empaquetado más uniforme de las partículas y a una reducción de los gradientes de presión. Esto conduce a una distribución más homogénea de la densidad y reduce la probabilidad de distorsiones y grietas en el componente final. Esta ventaja es especialmente crítica cuando se trata de componentes de formas complejas.
Según consideraciones técnicas, la CIP proporciona una densidad mayor y más uniforme a una presión de compactación determinada, lo que la hace especialmente adecuada para polvos quebradizos o finos. Además, la ausencia de fricción en la pared de la matriz en la CIP elimina los problemas asociados a la eliminación de lubricante y permite densidades de prensado más altas.
Por otra parte, el CIP ofrece la ventaja de una contracción más uniforme durante la sinterización debido a la uniformidad de la densidad en verde. Esto es esencial para mantener un buen control de la forma y conseguir propiedades uniformes en el producto final. Además, el CIP no requiere un aglutinante de cera como el Prensado Uniaxial en Matriz, eliminando la necesidad de operaciones de desparafinado.
En resumen, las ventajas del prensado isostático en frío sobre el prensado uniaxial incluyen la capacidad de dar formas más complejas y la reducción de distorsiones y grietas debido al empaquetado uniforme de las partículas. Estas ventajas hacen del CIP el método preferido para fabricar componentes con geometrías intrincadas y conseguir productos homogéneos de alta calidad.
Prensado isostático en frío en la producción de componentes de formas complejas
Comparación entre la CIP y el moldeo por inyección para la producción de grandes volúmenes
Cuando se requieren componentes de formas complejas, que superan las capacidades de prensado uniaxial, y se necesita un gran volumen de producción, las dos opciones principales son el CIP y el moldeo por inyección. El CIP fue el primer método de alta tecnología descrito en la literatura para la fabricación de cerámica de alúmina, por Daubenmeyer en 1934. De hecho, los aislantes de bujías son probablemente el componente cerámico fabricado por CIP de mayor volumen de producción en todo el mundo. Una proporción significativa de los 3.000 millones de aisladores de bujías que se fabrican anualmente se somete a CIP. Como en el caso del prensado uniaxial, la materia prima del CIP suele ser alúmina Bayer simplemente molida, alúmina Bayer molida y secada por atomización o, en raras ocasiones, nanopolvos SolGel de alta tecnología secados por atomización. Sin embargo, en general, el CIP no es tan común industrialmente como el moldeo por inyección. Por lo general, la CIP sólo se utiliza cuando se requieren formas muy complejas y el moldeo por inyección no resulta práctico por el motivo que sea.
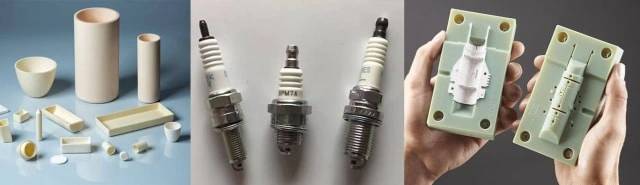
Resumen histórico del uso del CIP en la fabricación de cerámica de alúmina
El prensado isostático en frío (CIP, por sus siglas en inglés) es una tecnología basada en polvos, de forma casi neta, para la producción de componentes metálicos y cerámicos. El CIP se ha utilizado habitualmente para procesar cerámicas, pero no tanto metales. Sin embargo, los recientes avances en capacidad de proceso y pulvimetalurgia han permitido que la CIP se utilice cada vez más en la fabricación de piezas metálicas de alto rendimiento. Ventajas como el procesamiento en estado sólido, la microestructura uniforme, la complejidad de la forma, el bajo coste de las herramientas y la escalabilidad del proceso han hecho de la CIP una ruta de procesamiento viable para los metales. Además, la posibilidad de producir piezas de forma casi neta con un desperdicio mínimo de material ha hecho que el proceso sea más aceptable en aplicaciones especializadas, como la aeroespacial y la automoción.
Uso de la CIP en la producción de aisladores de bujías
Durante décadas, fabricantes de todo el mundo han utilizado con éxito el prensado isostático en frío (CIP). El CIP se utiliza para consolidar polvos metálicos y cerámicos con el fin de obtener una pieza "verde" que pueda someterse a tratamientos posteriores, como el laminado, el mecanizado o la sinterización.
Con presiones típicas de 1.035 a 4.138 bar (15.000 a 60.000 psi) y una temperatura ambiente de hasta 93 °C (200 °F), el CIP puede alcanzar el 95% de la densidad teórica de la cerámica.
Un proceso probado para piezas de alto rendimiento Entre las aplicaciones habituales del prensado isostático en frío se incluyen la consolidación de polvos cerámicos, la compresión de grafito, refractarios y aislantes eléctricos, y otras cerámicas finas para aplicaciones dentales y médicas.
La tecnología se está extendiendo a nuevas aplicaciones, como el prensado de cátodos para sputtering, el revestimiento de piezas de válvulas en un motor para minimizar el desgaste de las culatas, las telecomunicaciones, la electrónica, la industria aeroespacial y la automoción.
Prensas isostáticas en frío
Las prensas isostáticas en frío (CIP) se utilizan para producir componentes de polvo metálico sin sinterizar o compactados con colorante verde en un paso preliminar de densificación previo al laminado, mecanizado o sinterizado. Empresas de todo el mundo utilizan nuestros sistemas CIP para producir eficazmente componentes sin defectos para los sectores aeroespacial, militar, industrial y médico. Los líderes tecnológicos de todo el mundo saben que nuestras prensas isostáticas en frío están diseñadas de tal forma que las piezas pueden retirarse fácilmente con suficiente resistencia en verde para su posterior manipulación y sinterización.
Prensado isostático en frío
El prensado isostático en frío tiene la ventaja de producir piezas en las que no se puede justificar el elevado coste inicial de las matrices de prensado o cuando se necesitan compactos muy grandes o complejos. Es posible prensar isostáticamente una gran variedad de polvos a escala comercial, incluidos metales, cerámicas, plásticos y materiales compuestos. Las presiones necesarias para la compactación oscilan entre menos de 5.000 psi y más de 100.000 psi (34,5 a 690 MPa). Los polvos se compactan en moldes elastoméricos en un proceso de bolsa húmeda o seca.
Al seleccionar los servicios de prensado isostático en frío es importante tener en cuenta las capacidades del material. Aleaciones de aluminio y magnesio, carburos y herramientas de corte, carbono y grafito, cerámica y materiales compuestos son sólo algunos de los materiales y componentes que se producen con CIP. Algunos servicios de prensado isostático en frío están especializados en revestimientos y depósitos de pulverización térmica, aleaciones de cobre o diamantes y materiales similares al diamante. Otros trabajan con materiales electrónicos o eléctricos, explosivos o pirotecnia, o materiales especiales y patentados.
DESCRIPCIÓN DEL PRENSADO ISOSTÁTICO EN FRÍO
El prensado isostático en frío (PIC) es un proceso utilizado para moldear y compactar polvos en componentes de distintos tamaños y formas. En el prensado isostático en frío (CIP) con bolsa húmeda, el material se preforma y luego se sella en una bolsa flexible o molde. La bolsa se coloca dentro de un fluido hidráulico (por ejemplo, aceite o agua) en un recipiente a presión. Se aplica presión al fluido, normalmente entre 10.000 y 60.000 psi, que se distribuye uniformemente por el material. Este método ayuda a reducir la distorsión, mejorar la precisión y reducir el riesgo de atrapamiento de aire y vacíos. Se utiliza mucho en la producción de componentes para aplicaciones médicas, aeroespaciales y de automoción.
Con el CIP hay menos control dimensional que con el prensado uniaxial. Por ejemplo, en el ejemplo anterior, si se necesitan exactamente 5 mm de diámetro, habrá que hacer algunas pruebas, errores y cálculos previos en el molde y el procedimiento de llenado para conseguirlo. Pero una vez conseguido, se trata de un proceso muy repetible que ofrece algunas ventajas claras. Entre ellas, la posibilidad de prensar pastillas con una relación de aspecto muy larga. Las bujías de encendido son un ejemplo de producto común que se prensa isostáticamente en frío a escala industrial.
Prensado isostático en frío
El prensado isostático en frío (CIP) se realiza a temperatura ambiente y utiliza un molde fabricado con un material elastómero como el uretano, el caucho o el cloruro de polivinilo. El fluido en el prensado isostático en frío suele ser aceite o agua. La presión del fluido durante la operación suele ser de 60.000 lbs/pulg2 (400 MPa), a 150.000 lbs/pulg2 (1000 MPa). Una desventaja de este proceso de fabricación es la baja precisión geométrica debido a la flexibilidad del molde. En primer lugar, el polvo se compacta hasta alcanzar una densidad muy uniforme mediante prensado isostático en frío. A continuación, el compacto verde suele sinterizarse de forma convencional, para producir la pieza deseada.
Proceso de prensado isostático en frío
Explicación del proceso CIP
El prensado isostático en frío (CIP) es un método de procesamiento de materiales que consiste en compactar polvos encerrándolos en un molde de elastómero. El molde está hecho de materiales como uretano, caucho o cloruro de polivinilo, que tienen poca resistencia a la deformación. A continuación, se aplica uniformemente presión líquida al molde para comprimirlo. Este proceso se basa en la ley de Pascal, que establece que la presión aplicada en un fluido encerrado se transmite en todas las direcciones sin ningún cambio de magnitud.
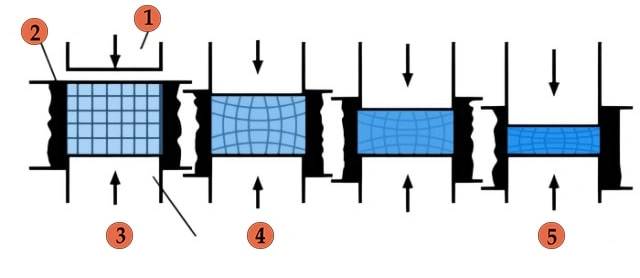
La CIP puede ser utilizada para varios materiales como plásticos, grafito, metalurgia en polvo, cerámica y blancos para sputtering. Suele utilizarse para obtener una pieza "bruta" con la resistencia suficiente para su manipulación y procesamiento, que posteriormente puede sinterizarse para conseguir la resistencia final.
Automatización del proceso CIP
El proceso CIP puede automatizarse utilizando equipos especializados. El material que se va a procesar se sella en un molde de elastómero y se coloca en una cámara de presión. Se bombea un medio líquido, como agua o aceite, a la cámara, y el molde se somete uniformemente a alta presión desde todos los lados. Esta automatización garantiza una aplicación uniforme y precisa de la presión, lo que se traduce en productos acabados de alta calidad.
La automatización del proceso CIP ofrece varias ventajas. Mejora la eficacia al reducir el trabajo manual y aumentar los índices de producción. También garantiza una aplicación uniforme de la presión, lo que mejora la calidad general y la fiabilidad de los productos acabados. Además, la automatización permite controlar y supervisar mejor los parámetros del proceso, lo que se traduce en una mayor optimización del mismo y en un ahorro de costes.
Ciclos de presurización y despresurización en CIP
El proceso CIP implica ciclos de presurización y despresurización para lograr la compactación deseada de los polvos. Durante el ciclo de presurización, el medio líquido se bombea a la cámara de presión, aplicando una presión uniforme al molde de elastómero. Esta presión compacta los polvos y forma un sólido altamente compacto.
Una vez alcanzada la compactación deseada, comienza el ciclo de despresurización. La presión de la cámara se libera gradualmente, lo que permite que el molde se relaje y se extraiga el material compactado. Este ciclo garantiza que el material compactado pueda extraerse fácilmente del molde sin deformaciones ni daños.
Los ciclos de presurización y despresurización se controlan cuidadosamente para lograr la densidad y resistencia deseadas del material compactado. Los parámetros, como la magnitud de la presión, la duración y la velocidad de cambio, pueden ajustarse en función de los requisitos específicos del material procesado.
En conclusión, el prensado isostático en frío (CIP) es un método versátil para compactar polvos y moldear materiales. Al encerrar los polvos en un molde de elastómero y aplicar una presión uniforme, el CIP puede producir sólidos muy compactos con diversas aplicaciones. La automatización del proceso CIP ofrece una mayor eficacia y control, mientras que los ciclos de presurización y despresurización garantizan la densidad y resistencia deseadas del material compactado.
Ventajas del prensado isostático en frío para cerámica de alúmina
Comparación del prensado isostático en frío con el prensado uniaxial y otros métodos de conformado de cerámica
El prensado isostático en frío (CIP) es una tecnología basada en polvo, de forma casi neta, para la producción de componentes metálicos y cerámicos. El CIP se ha utilizado comúnmente para procesar cerámica, pero no tanto para metales. Sin embargo, los recientes avances en capacidad de proceso y pulvimetalurgia han permitido que la CIP se utilice cada vez más en la fabricación de piezas metálicas de alto rendimiento. Ventajas como el procesamiento en estado sólido, la microestructura uniforme, la complejidad de la forma, el bajo coste de las herramientas y la escalabilidad del proceso han hecho de la CIP una ruta de procesamiento viable para los metales.
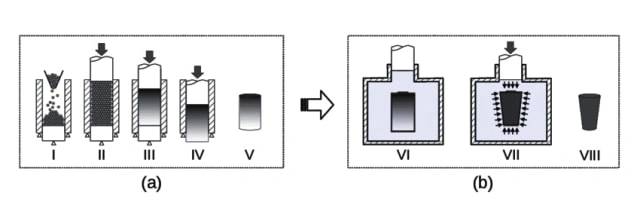
Algunas de las principales ventajas del CIP para la cerámica de alúmina en comparación con el prensado uniaxial son las siguientes:
-
Son posibles formas más complejas: El CIP permite producir formas más complejas que el prensado uniaxial. Esto se debe a que el CIP utiliza moldes flexibles que pueden adaptarse a diseños y formas intrincados.
-
Gradientes de presión de prensado muy reducidos: El CIP reduce significativamente los gradientes de presión de prensado, lo que ayuda a minimizar la distorsión y el agrietamiento durante el proceso de conformado. Esto garantiza que los componentes cerámicos finales tengan una mayor precisión dimensional e integridad estructural.
Ventajas de la CIP para piezas complejas con series de producción pequeñas
La CIP ofrece varias ventajas para la fabricación de piezas complejas con series de producción pequeñas. Estas ventajas incluyen:
-
Bajo coste del molde: La CIP requiere un bajo coste de molde, lo que la hace ideal para producir piezas complejas con series de producción pequeñas. A diferencia de otros métodos de conformado cerámico, el CIP no requiere moldes caros, lo que ayuda a reducir los costes de fabricación.
-
Sin coste de molde para el post-CIP: Además del bajo coste del molde, el CIP también elimina la necesidad de moldes en los procesos post-CIP. Esto reduce aún más los costes de producción y permite una mayor flexibilidad en la fabricación de piezas complejas.
-
Sin limitación de tamaño: El CIP no tiene limitaciones de tamaño, salvo los límites de la cámara de prensado. Esto lo hace adecuado para producir componentes muy grandes, especialmente los de formas complejas. De hecho, se han fabricado con éxito componentes de más de 1 tonelada de peso utilizando la CIP.
-
Tiempos de ciclo de procesamiento cortos: La CIP tiene tiempos de ciclo de procesamiento cortos, ya que no requiere secado ni quemado del aglutinante. Esto significa que los componentes cerámicos formados pueden sinterizarse más rápidamente que con otros métodos, lo que aumenta la eficiencia de la producción.
Aunque la CIP ofrece numerosas ventajas para la cerámica de alúmina, es importante tener en cuenta algunas de sus limitaciones. Entre ellas se incluyen un control dimensional limitado, una complejidad de formas inferior a la del moldeo por inyección de polvo (PIM) y la necesidad de polvos con una excelente fluidez.
En general, el prensado isostático en frío es un método versátil y rentable para producir cerámica de alúmina con formas complejas y pequeñas series de producción. Sus ventajas en términos de complejidad de formas, gradientes de presión reducidos, bajo coste del molde y tiempos de procesamiento más rápidos lo convierten en una opción popular en diversas industrias como la automovilística, aeroespacial y de telecomunicaciones.
Desventajas del prensado isostático en frío para cerámica
Desafíos con el control dimensional y la complejidad de la forma
El prensado isostático en frío (CIP) es un proceso de compactación de polvo que se utiliza para obtener piezas listas para la sinterización. Sin embargo, existen algunos problemas relacionados con el control dimensional y la complejidad de la forma cuando se utiliza el CIP para cerámica.
La menor precisión de las superficies prensadas adyacentes a la bolsa flexible en comparación con el prensado mecánico o la extrusión suele requerir un mecanizado posterior. Esto significa que pueden ser necesarios pasos adicionales para conseguir las dimensiones y la forma deseadas de las piezas cerámicas.
Requisitos de los polvos utilizados en CIP
Una de las desventajas del prensado isostático en frío es que normalmente se requiere un polvo secado por atomización relativamente caro para las prensas de bolsas secas totalmente automáticas. Esto puede aumentar el coste global del proceso, ya que es necesario utilizar polvos especializados.
Además, los índices de producción del CIP son inferiores a los de la extrusión o la compactación por troquel. Esto significa que el proceso puede no ser tan eficiente en términos de volumen de producción.
En resumen, aunque el prensado isostático en frío ofrece ventajas como la capacidad de producir compactos grandes o complejos y el uso de una gran variedad de polvos, también tiene algunas desventajas. Entre ellas se encuentran los retos que plantea el control dimensional y la complejidad de las formas, así como la necesidad de utilizar polvos especializados y unos índices de producción inferiores a los de otros métodos de conformado.
Aplicaciones del prensado isostático en frío
Uso habitual del CIP en la producción en serie de cerámica avanzada
El prensado isostático en frío (CIP) es una tecnología basada en polvo y de forma casi neta que se utiliza habitualmente para procesar cerámica. Tiene la ventaja de poder producir piezas en las que el elevado coste inicial de las matrices de prensado no puede justificarse o cuando se necesitan compactos muy grandes o complejos.
Es posible prensar isostáticamente a escala comercial una gran variedad de polvos, como metales, cerámicas, plásticos y materiales compuestos. Las presiones necesarias para la compactación oscilan entre menos de 5.000 psi y más de 100.000 psi. Los polvos se compactan en moldes elastoméricos en un proceso de bolsa húmeda o seca.
El CIP se ha utilizado ampliamente para la consolidación de polvos cerámicos, grafito, materiales refractarios, aislantes eléctricos y la compresión de cerámica avanzada. Materiales como el nitruro de silicio, el carburo de silicio, el nitruro de boro, el carburo de boro, el boruro de titanio y la espinela pueden procesarse mediante CIP.
Esta tecnología se está extendiendo a nuevas aplicaciones, como la compresión de cátodos para sputtering, el revestimiento de componentes de válvulas para reducir el desgaste de los cilindros de los motores y diversas aplicaciones en los sectores de telecomunicaciones, electrónica, aeroespacial y automoción.
Ejemplos de componentes producidos por CIP
La CIP se utiliza habitualmente para consolidar polvos cerámicos, comprimir grafito, refractarios y aislantes eléctricos, así como otras cerámicas finas para aplicaciones dentales y médicas. También se utiliza para el prensado de blancos de sputtering, el recubrimiento de piezas de válvulas en motores para minimizar el desgaste de las culatas y en diversas aplicaciones en los sectores de telecomunicaciones, electrónica, aeroespacial y automoción.
Los equipos CIP se utilizan para comprimir los costes de producción y son esenciales para fabricar productos acabados a partir de materias primas. El proceso consiste en confinar polvos en un molde de elastómero, colocar el molde en una cámara de presión, bombear un medio líquido y someter uniformemente el molde a alta presión desde todos los lados. El CIP puede utilizarse con metalurgia en polvo, carburos cementados, materiales refractarios, grafito, cerámica, plásticos y otros materiales.

Es importante tener en cuenta las capacidades del material a la hora de seleccionar los servicios de prensado isostático en frío. Las aleaciones de aluminio y magnesio, los carburos y las herramientas de corte, el carbono y el grafito, la cerámica, los compuestos y otros materiales pueden producirse mediante CIP. Algunos servicios de prensado isostático en frío están especializados en revestimientos y depósitos de pulverización térmica, aleaciones de cobre, diamantes y materiales similares al diamante, materiales electrónicos o eléctricos, explosivos o pirotecnia, o materiales especiales y patentados.
El prensado isostático en frío se realiza a temperatura ambiente y utiliza un molde fabricado con un material elastómero como uretano, caucho o cloruro de polivinilo. El fluido utilizado en el prensado isostático en frío suele ser aceite o agua, y la presión del fluido durante la operación suele oscilar entre 60.000 lbs/pulg2 y 150.000 lbs/pulg2. Una desventaja de este proceso de fabricación es la baja precisión geométrica debida al molde flexible.
En resumen, el prensado isostático en frío (CIP) es una técnica valiosa para la producción en masa de cerámica avanzada y otros materiales. Ofrece ventajas como el procesamiento en estado sólido, la microestructura uniforme, la complejidad de la forma, el bajo coste de las herramientas y la escalabilidad del proceso. El CIP se utiliza ampliamente en diversas industrias y continúa expandiéndose hacia nuevas aplicaciones.
Tecnologías de compresión alternativas
Panorama de otras tecnologías de compresión
En el ámbito del procesamiento de materiales, existen varias técnicas de compresión potentes. Dos de ellas, el prensado isostático en frío (CIP) y el prensado isostático en caliente (HIP), se utilizan ampliamente en diversos sectores. Aunque ambos métodos tienen como objetivo mejorar las propiedades de los materiales, difieren en sus condiciones de funcionamiento y ofrecen ventajas únicas.
Introducción de la compactación por ondas de choque como alternativa
Aunque el CIP y el HIP son técnicas de compresión eficaces, se han desarrollado tecnologías alternativas para abordar retos específicos. Una de ellas es la compactación por ondas de choque, también conocida como compresión de choque.
La compactación por ondas de choque implica la generación de una onda de choque corta y de alta presión que puede deformar gravemente las partículas o incluso provocar una fusión local. Este proceso puede dar lugar a que el material se vuelva totalmente denso y compacto sin un crecimiento significativo del grano. Las ondas de choque se caracterizan por presiones muy altas, temperaturas medias, tiempos de reacción muy cortos y velocidades de deformación muy altas.
Diversos métodos, como las pistolas de aire y las ondas de choque explosivas, que antes se utilizaban para comprimir polvos de tamaño micrométrico, se emplean ahora para comprimir nanopolvos. Estas tecnologías de compresión alternativas, con tiempos de calentamiento muy cortos, han demostrado su eficacia para conseguir materiales totalmente densos y compactos sin engrosamiento de los nanogranos.
Un ejemplo de compactación por ondas de choque es el uso de un dispositivo de compactación por ondas de choque planas equipado con una pistola de aire. Este dispositivo genera una onda de choque corta y de alta presión que puede deformar las partículas y lograr una densidad y compactación completas. Estas tecnologías de compresión alternativas ofrecen una forma eficaz de procesar materiales con un crecimiento mínimo del grano y mejores propiedades del material.
En la industria del caucho, las prensas de compresión avanzadas se utilizan para una vulcanización eficaz del caucho. Al aplicar una fuerza de presión controlada sobre los materiales de caucho, estas máquinas comprueban las características físicas de los productos de caucho, como la resistencia, la elasticidad y la durabilidad, garantizando que cumplen las normas ASTM y son de alta calidad.
En general, las tecnologías de compresión alternativas, como la compactación por ondas de choque, ofrecen soluciones innovadoras para conseguir materiales totalmente densos y compactos con propiedades mejoradas. Estas tecnologías ofrecen ventajas únicas y pueden utilizarse en diversas industrias para mejorar la capacidad de procesamiento de materiales.
Conclusión
En conclusión,el prensado isostático en frío (PIC) es una técnica muy versátil y eficaz para fabricar componentes de formas complejas, especialmente en la producción de cerámica avanzada. A diferencia del prensado uniaxial tradicional, el CIP permite la formación de formas más intrincadas y reduce el riesgo de distorsiones y grietas gracias al empaquetado uniforme de las partículas. Aunque el control dimensional y los requisitos de polvo plantean algunos retos, la CIP ofrece ventajas significativas para pequeñas series de producción y se utiliza ampliamente en la producción en masa de cerámica avanzada. Como alternativa a la CIP, también merece la pena considerar la compactación por ondas de choque para determinadas aplicaciones de compresión.
CONTÁCTANOS PARA UNA CONSULTA GRATUITA
Los productos y servicios de KINTEK LAB SOLUTION han sido reconocidos por clientes de todo el mundo. Nuestro personal estará encantado de ayudarle con cualquier consulta que pueda tener. ¡Contáctenos para una consulta gratuita y hable con un especialista del producto para encontrar la solución más adecuada para sus necesidades de aplicación!