Descripción de un horno de fusión por inducción y levitación en vacío
Explore los componentes de un horno de fusión por inducción de levitación en vacío, incluidos el cuerpo del horno, la potencia de media frecuencia, el sistema de vacío, el sistema de refrigeración y el sistema de control eléctrico. Aprenda cómo contribuye cada elemento a la eficacia y precisión de los procesos de fundición de metales.
Los hornos de fusión por inducción en vacío (VIM) han evolucionado desde el procesamiento especializado de aleaciones exóticas hasta un uso más común en diversas industrias, incluida la producción de aceros inoxidables y otros metales. Estos hornos funcionan en condiciones de vacío, ofreciendo un control preciso del proceso de fusión.
¿Cómo funciona un horno de inducción de vacío?
El material se carga en el horno de inducción al vacío, donde se aplica energía para iniciar la fusión. Se añaden cargas adicionales para alcanzar la capacidad de fusión deseada. El metal fundido se somete a refinamiento en condiciones de vacío, con ajustes para lograr una química de fusión precisa.
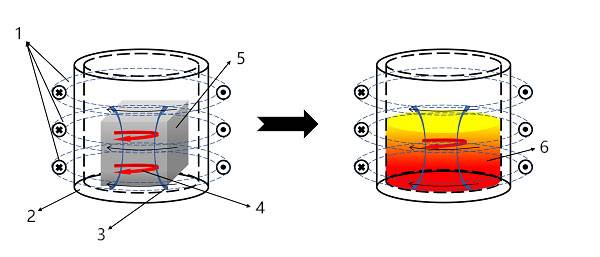
Componentes y funciones clave
Además del cuerpo del horno y del sistema de vacío, un horno de fusión por inducción de vacío está equipado con componentes esenciales como una fuente de alimentación de media frecuencia, un sistema de control eléctrico y un sistema de refrigeración. Estos componentes trabajan conjuntamente para suministrar la energía necesaria para la fusión, al tiempo que evitan el sobrecalentamiento y garantizan la integridad estructural.
Pueden añadirse componentes auxiliares, como carros de transmisión, mecanismos de puerta del horno y ventanas de observación, en función de los requisitos específicos del proceso. Para aplicaciones con altos niveles de impurezas, un sistema de filtrado de gases es esencial para mantener la pureza del metal.
Ventajas de los hornos de fusión por inducción al vacío
La estructura compacta de los hornos VIM, con sólo la parte de fundición encerrada en la cámara de vacío, permite un mejor control de los niveles de vacío y tiempos de evacuación más rápidos. Características como la agitación electromagnética garantizan una mezcla uniforme de los elementos añadidos en todo el baño de fusión, manteniendo una temperatura constante.
La inclusión de deflectores filtrantes y otras medidas mejora la pureza del metal al mitigar el impacto de las impurezas. La detección y reparación de fugas de vacío se simplifican gracias al menor volumen del horno, lo que reduce el tiempo de inactividad por mantenimiento.
Precisión y control
Los hornos de fusión por inducción en vacío ofrecen un control preciso de la temperatura mediante avanzados sistemas de control eléctrico. Los usuarios pueden supervisar el proceso de fusión en tiempo real, garantizando precisión y consistencia. El sistema de refrigeración centralizado regula las temperaturas de fusión, mejorando el control del proceso y la calidad del producto.
Aplicaciones y flexibilidad
Los hornos VIM están disponibles en varios tamaños, desde unidades pequeñas adecuadas para experimentos a escala de gramos hasta modelos más grandes para la producción industrial. Esta versatilidad permite a los usuarios ajustar el tamaño de los lotes en función de sus necesidades específicas.
Eliminación de gases y prevención de la oxidación
Una de las principales ventajas de la fusión por inducción en vacío es la eliminación de gases de los metales fundidos. Este proceso evita la oxidación rápida, garantizando la pureza y calidad del producto final.
En conclusión, los hornos de fusión por inducción al vacío desempeñan un papel vital en los procesos modernos de fundición de metales, ofreciendo un control preciso, una mayor pureza y flexibilidad en la producción.
Eficacia y flexibilidad
Profundice en la gama de hornos de vacío disponibles, desde unidades a pequeña escala adecuadas para lotes de un gramo hasta hornos más grandes con capacidad para lotes de diversos tamaños. Comprenda cómo esta versatilidad permite a los usuarios optimizar los procesos de producción.
Automatización y control avanzados:
Nuestros hornos de vacío están equipados con avanzados sistemas de automatización y control que le permiten gestionar y supervisar con precisión los procesos. Nuestra interfaz de fácil uso le permite programar y ajustar sin esfuerzo diversos parámetros, garantizando un rendimiento y una eficiencia óptimos. Con datos y diagnósticos en tiempo real, puede tomar decisiones informadas, detectar anomalías y optimizar sus procesos de producción para obtener el máximo rendimiento.
Eficiencia energética y sostenibilidad:
Diseños de vacío
Los hornos de vacío para procesado a baja temperatura pueden ser discontinuos o continuos, independientes, integrados en sistemas de hornos de vacío continuos o un "módulo" independiente incorporado a un sistema celular. Por ejemplo, el funcionamiento básico de un horno de vacío discontinuo es el siguiente:
- Bombas de vacío mecánicas, opcionalmente equipadas con soplantes, producen niveles de vacío de hasta 1,3 x 10-3 mbar (0,001 torr), siendo común 6,7 x 10-3 mbar (0,005 torr). Esto se consigue normalmente entre 10 y 30 minutos después del inicio del ciclo, dependiendo del tamaño de los sistemas de bombeo y de la naturaleza de los contaminantes presentes en la carga de trabajo.
- A continuación, la unidad se rellena en el rango de 66,7 x 101 mbar (500 torr) de presión negativa a 0,10 bar (1,5 psig) de presión positiva con un gas inerte como nitrógeno, argón o una mezcla de nitrógeno/hidrógeno (3% como máximo), y comienza el calentamiento.
- Los ciclos de doble bombeo resultan a menudo ventajosos para acelerar la duración total del ciclo. Una vez alcanzado el punto de consigna y empapado a temperatura, se inicia el ciclo de enfriamiento.
Características de los hornos de vacío
Los hornos de vacío KinTek ofrecen un control preciso de la temperatura, una excelente uniformidad de la temperatura y una amplia gama de aplicaciones para laboratorios, universidades y cualquier aplicación de producción a pequeña escala que utilice modelos de hornos industriales.
Cada horno de vacío estándar y personalizado ofrece las siguientes características y ventajas:
- Excelente precisión y uniformidad de la temperatura
- Aislamiento de fibra cerámica energéticamente eficiente
- Función de seguridad de apagado automático
Hornos de vacío personalizados
Obtenga un horno de vacío de alta temperatura construido específicamente para satisfacer las necesidades de su aplicación. Los experimentados y expertos representantes de KinTek pueden ayudarle a diseñar o construir un horno a medida para satisfacer sus especificaciones o necesidades de aplicación exactas.
Esta amplia gama de características y opciones garantiza que nuestros hornos de vacío proporcionen la eficacia y flexibilidad necesarias para una gran variedad de aplicaciones de laboratorio y producción a pequeña escala.
Control de temperatura de precisión
Descubra cómo el sistema de control eléctrico de los hornos de fusión por inducción al vacío garantiza un control preciso de la temperatura durante todo el proceso de fusión. Explore el papel del sistema de refrigeración en el mantenimiento de temperaturas de fusión óptimas y la prevención de la oxidación.
El calentamiento por inducción es un proceso en el que las corrientes inducidas de Foucault calientan materiales conductores. Este calentamiento puede utilizarse para fundir metales y fabricar aleaciones. La fusión por inducción en vacío ofrece una atractiva combinación de atmósfera controlada (vacío o gas inerte) y control preciso del proceso de fusión.
Descripción del horno de sinterización al vacío
Un horno de sinterización al vacío es un tipo de horno en el que los artículos calentados se someten a sinterización en un entorno de vacío. Este horno es crucial en varios procesos industriales, particularmente en la pulvimetalurgia.
El proceso de sinterización es muy sensible a las variaciones de temperatura. Una desviación de unos pocos grados centígrados puede afectar significativamente a la calidad del producto final. Por lo tanto, es imperativo un control estricto de la temperatura de sinterización, con desviaciones que normalmente no superan un rango especificado de ±3℃ a ±5℃.
Ventajas de los equipos de inducción al vacío
En comparación con los métodos de fundición tradicionales, los equipos de inducción al vacío ofrecen ventajas sustanciales en el control del proceso. Con los avances en tecnología informática, los modernos hornos de inducción al vacío integran sistemas de control inteligentes que agilizan las operaciones, reducen los costes de mano de obra y mejoran la precisión.
Los futuros avances en sistemas de control inteligente mejorarán aún más las capacidades de los equipos de inducción al vacío. Estos sistemas permitirán un control preciso de las temperaturas de fundición, facilitarán la adición automática de aleaciones a intervalos predeterminados y agilizarán todo el proceso de fundición. Además, la integración de una completa recopilación de datos y el análisis en tiempo real permitirán a los operarios tomar decisiones informadas y optimizar los parámetros del proceso durante la fundición.
Componentes del horno de fusión por inducción al vacío
El horno de fusión por inducción de vacío consta de varios componentes esenciales, entre los que se incluyen:
- Cuerpo del horno de vacío: Proporciona la cámara donde se produce la fusión en condiciones de vacío o atmósfera controlada.
- Potencia de media frecuencia: Suministra la energía necesaria para el calentamiento por inducción.
- Sistema de vacío: Mantiene el nivel de vacío deseado dentro de la cámara del horno.
- Sistema de refrigeración: Evita el sobrecalentamiento y mantiene temperaturas de fusión óptimas.
- Sistema de control eléctrico: Permite un control preciso de la temperatura y el funcionamiento general del horno.
Principales características y ventajas
- Control preciso de la temperatura: El sistema de control eléctrico garantiza una regulación precisa de las temperaturas de fusión, mejorando la calidad y consistencia del producto final.
- Eliminación de gases: El entorno de vacío elimina los gases de los metales fundidos, evitando una rápida oxidación y preservando la integridad de la aleación.
- Tamaños de lote flexibles: Los hornos de vacío están disponibles en varios tamaños, adaptándose a una amplia gama de tamaños de lote, desde aplicaciones industriales a pequeña escala hasta las más grandes.
- Sistema de enfriamiento centralizado: El sistema de refrigeración disipa eficazmente el calor, manteniendo temperaturas de funcionamiento estables y prolongando la vida útil del equipo.
En conclusión, los hornos de fusión por inducción al vacío ofrecen una precisión y un control inigualables en los procesos de fundición de metales. Al aprovechar tecnologías avanzadas y sistemas de control inteligentes, estos hornos facilitan una producción eficiente, garantizan la calidad del producto y allanan el camino para futuros avances en el procesamiento metalúrgico.
Principio de funcionamiento y significado histórico
Descubra las raíces históricas de la tecnología de fusión por inducción en vacío, remontando sus orígenes a las industrias aeroespacial y metalúrgica. Descubra cómo ha evolucionado esta tecnología hasta convertirse en la piedra angular de la producción de aleaciones de alto rendimiento para diversas aplicaciones.
Fusión por inducción en vacío: Un camino hacia los materiales avanzados
La fusión por inducción en vacío (VIM) es una tecnología fundamental en el ámbito de la metalurgia, especialmente en la producción de aleaciones especializadas y exóticas. Desarrollada inicialmente para el procesamiento de superaleaciones, su espectro de aplicación se ha ampliado hasta abarcar los aceros inoxidables y otros metales. Esta expansión se debe en gran medida a la creciente demanda de materiales avanzados en diversas industrias.
El proceso de fusión por inducción en vacío
La base del proceso VIM es el principio de fusión de metales en condiciones de vacío, con la inducción electromagnética como principal fuente de energía. El proceso implica la generación de corrientes eléctricas parásitas dentro del metal, facilitadas por una bobina de inducción que transporta corriente alterna. Estas corrientes, a su vez, inducen efectos de calentamiento que, en última instancia, conducen a la fusión de la carga metálica.
La rápida evolución de la tecnología VIM tiene sus raíces en la búsqueda de materiales de aleación de alta temperatura por parte de la industria aeroespacial. Estos materiales, esenciales para los equipos aeroespaciales, de misiles, cohetes y energía atómica, requerían innovaciones en los procesos de fundición. Los hornos VIM surgieron como solución, permitiendo la fundición de aleaciones a base de níquel, hierro y cobalto en condiciones de vacío. Este entorno reduce eficazmente la presencia de elementos de vacío como O2, N2 y H2, garantizando la eliminación de inclusiones no metálicas e impurezas nocivas como Pb, Bi, Sb, Cu, Sn y Te.
Aplicaciones de la fusión por inducción en vacío
La versatilidad del VIM se extiende a diversas aplicaciones dentro del panorama metalúrgico:
- Refinado de metales y aleaciones de gran pureza.
- Producción de electrodos para procesos de refundición.
- Fabricación de barras de aleación maestras, vitales en procedimientos como la fundición a la cera perdida.
- Fundición de componentes críticos para motores aeronáuticos.
Evolución histórica
La génesis de la fusión por inducción en vacío se remonta a 1920, cuando surgió el primer prototipo. En esencia, el VIM aprovecha la inducción electromagnética para inducir corrientes de Foucault en el interior de los conductores, calentando y fundiendo así el metal. A lo largo de las décadas, esta tecnología ha encontrado una utilidad indispensable tanto en el sector aeroespacial como en el nuclear, impulsando avances en la ciencia y la ingeniería de materiales.
En resumen, la fusión por inducción en vacío es un testimonio del ingenio humano, ya que facilita la producción de materiales que impulsan las maravillas tecnológicas modernas. Desde sus humildes orígenes hasta su estatus actual como piedra angular de la innovación metalúrgica, el VIM sigue configurando el panorama de la fabricación de materiales avanzados.
Aplicaciones en todas las industrias
Explore el amplio abanico de aplicaciones de la tecnología de fusión por inducción en vacío en los sectores aeroespacial, electrónico y energético, entre otros. Comprenda cómo esta tecnología mejora las propiedades y la calidad de los materiales esenciales para la ingeniería y la fabricación avanzadas.
La tecnología de fusión por inducción en vacío (VIM) ha evolucionado significativamente. Desarrollada originalmente para procesar aleaciones especializadas y exóticas, ahora es cada vez más común a medida que los materiales avanzados encuentran aplicaciones más amplias. Inicialmente utilizada para materiales como las superaleaciones, la VIM ha ampliado su utilidad para incluir aceros inoxidables y otros metales.
El rápido desarrollo de la tecnología VIM está estrechamente ligado a la demanda de materiales de aleación de alta temperatura en industrias como la aeroespacial, la de misiles, cohetes y equipos de energía atómica. Las superaleaciones, cruciales para estas aplicaciones, se benefician enormemente de las capacidades de los hornos VIM.
Funcionamiento de los hornos de inducción al vacío
En un horno de inducción de vacío, el material se carga al vacío y se aplica energía para fundir la carga. Se realizan cargas adicionales para alcanzar la capacidad de fusión deseada, y el metal fundido se refina en condiciones de vacío. Este proceso permite ajustar con precisión la composición química de la masa fundida hasta conseguir la composición deseada.
Ventajas de la fusión por inducción en vacío
-
Alta pureza y calidad: El VIM destaca en la producción de materiales de alta pureza y calidad. El entorno de vacío elimina el riesgo de contaminación por oxígeno, nitrógeno y otros gases presentes en la atmósfera. El resultado es una masa fundida más limpia y homogénea, desprovista de inclusiones nocivas e impurezas que podrían comprometer las propiedades mecánicas.
-
Atmósfera controlada: Dentro de la cámara de vacío, la atmósfera está estrictamente controlada, y sólo se introducen gases específicos a presiones precisas. Este nivel de control permite una gestión precisa de la composición química del material fundido y evita oxidaciones o reacciones no deseadas con los gases ambientales.
Los hornos de fusión por inducción al vacío son fundamentales en el campo de la metalurgia al vacío, ya que desempeñan un papel importante en la producción de aleaciones y aceros especiales cruciales para equipos aeroespaciales, misiles, cohetes, energía atómica y la industria electrónica. Una parte considerable de los productos de estos sectores se fabrica con tecnología VIM.
Varios materiales, como el acero inoxidable, el acero resistente al calor, el acero de ultra alta resistencia, el acero para herramientas, el acero para rodamientos, los materiales magnéticos, las aleaciones elásticas y las aleaciones de expansión, se funden utilizando hornos de fusión por inducción al vacío para garantizar un rendimiento y una calidad óptimos. Estos hornos mejoran la trabajabilidad en caliente y las propiedades mecánicas de las superaleaciones con base de níquel, cobalto y hierro, haciéndolas indispensables en los procesos avanzados de ingeniería y fabricación.
Ventajas sobre los métodos tradicionales
La tecnología de fusión por inducción en vacío destaca como método principal para fundir metales debido a sus numerosas ventajas sobre los métodos tradicionales. Al comparar su eficiencia, sostenibilidad y pureza del material con los métodos convencionales, se hace evidente por qué la fundición por inducción en vacío es cada vez más favorecida en diversas industrias.
Eficiencia energética y sostenibilidad medioambiental
La tecnología de fusión por inducción en vacío (VIM) representa un importante salto adelante en eficiencia energética y sostenibilidad medioambiental en comparación con los métodos de fundición tradicionales. A diferencia de los métodos convencionales, el VIM funciona en un entorno de vacío, lo que minimiza la pérdida de calor y reduce el consumo de energía. Esta utilización eficiente de la energía no sólo disminuye los costes de producción, sino que también contribuye a un proceso de fabricación más ecológico al reducir las emisiones de carbono y el derroche de energía.
Pureza y calidad del material
Una de las principales ventajas del VIM es su capacidad para producir materiales de pureza y calidad excepcionales. El entorno de vacío elimina la presencia de oxígeno, nitrógeno y otros gases que podrían contaminar el metal fundido. Como resultado, el VIM produce fusiones más limpias y homogéneas, desprovistas de impurezas e inclusiones perjudiciales. Esta pureza mejora las propiedades mecánicas y el rendimiento general de los materiales resultantes, haciéndolos muy deseables para diversas aplicaciones.
Atmósfera controlada
En la cámara de vacío de los equipos VIM, la atmósfera se controla meticulosamente, lo que permite regular con precisión la composición y la presión de los gases. Al introducir únicamente gases especificados a presiones exactas, VIM garantiza un control estricto de la composición química del material fundido, minimizando el riesgo de oxidaciones o reacciones no deseadas con los gases ambientales. Este nivel de control es crucial para producir aleaciones con propiedades constantes y minimizar el desperdicio de material.
Eficacia y flexibilidad del proceso
Más allá de sus ventajas medioambientales y de calidad, el VIM ofrece una eficacia y flexibilidad de proceso inigualables. Sus rápidos ciclos de calentamiento y el calentamiento uniforme de las cargas metálicas aumentan significativamente los índices de producción al tiempo que reducen los índices de defectos. Además, la versatilidad del VIM permite fundir diversos metales y aleaciones con facilidad, facilitando el cambio rápido entre materiales y permitiendo la parada inmediata en caso necesario. Esta agilidad en la producción mejora la eficacia operativa y la adaptabilidad a las cambiantes demandas de fabricación.
Aplicación y perspectivas de futuro
La adopción generalizada de la tecnología de fundición por inducción al vacío en todas las industrias pone de manifiesto su inmenso potencial y versatilidad. Desde la investigación experimental a pequeña escala hasta la producción industrial a gran escala, la tecnología VIM ha demostrado su eficacia y fiabilidad. Su sencillo funcionamiento y sus rápidas temperaturas de fusión la convierten en la opción preferida de los fabricantes que buscan precisión y consistencia en sus procesos de producción. A medida que la tecnología siga avanzando, se espera que la aplicación del VIM se expanda aún más, impulsando la innovación y la eficiencia en los procesos de fundición y refinado de metales.
Sinterización por vacío: Mejora de la eficiencia y la calidad
Además de la fusión por inducción en vacío, el sinterizado en vacío se perfila como otro proceso vital para mejorar la eficiencia y la calidad del producto en la fabricación de metales. Al sinterizar polvos metálicos a temperaturas inferiores al punto de fusión en un entorno de vacío, el sinterizado en vacío ofrece varias ventajas. Elimina las reacciones entre metales y gases, mejora la densificación y reduce las temperaturas de sinterización, con lo que se ahorra energía y se prolonga la vida útil de los hornos de sinterización. El resultado es la fabricación de productos metálicos de alta calidad con mejores propiedades mecánicas y menor consumo de energía.
En conclusión, la fusión por inducción en vacío y el sinterizado en vacío representan tecnologías de vanguardia que ofrecen numerosas ventajas sobre los métodos de fundición tradicionales. Desde la eficiencia energética y la pureza de los materiales hasta la flexibilidad de los procesos y la sostenibilidad medioambiental, estas técnicas avanzadas están impulsando la innovación y remodelando el panorama de la fabricación de metales. A medida que las industrias siguen dando prioridad a la sostenibilidad y la calidad, la adopción de procesos basados en el vacío como el VIM y el sinterizado al vacío está a punto de acelerarse, marcando el comienzo de una nueva era de eficiencia y excelencia en la producción de metales.
Características principales de los hornos de fusión por inducción al vacío
Los hornos de fusión por inducción al vacío son fundamentales en los procesos metalúrgicos, ya que ofrecen una amplia gama de características diseñadas para un control preciso y una mayor productividad. A continuación se ofrece un análisis exhaustivo de sus principales componentes y avances:
Componentes estructurales
El horno consta de una camisa hermética de acero refrigerada por agua, diseñada para mantener las condiciones de vacío necesarias durante el proceso. Dentro de este recinto, el metal se funde en un crisol situado dentro de una bobina de inducción refrigerada por agua. Además, el interior del horno suele estar revestido con refractarios adecuados para soportar temperaturas extremas.
Mejoras del proceso
1. Control medioambiental
- La fundición de metal fundido puede ejecutarse en entornos de vacío o gas inerte, lo que garantiza unas condiciones óptimas para la formación de aleaciones y el mantenimiento de la pureza.
2. 2. Características adicionales
- Los hornos pueden integrar mecanismos de inclinación y vertido, cámaras de colada y puertos de muestreo para facilitar las distintas necesidades de producción.
- Las instalaciones de manipulación de moldes permiten el procesamiento automatizado o semiautomatizado, incorporando a veces sistemas de enclavamiento de vacío para un funcionamiento sin fisuras.
Futuras tendencias de desarrollo
La evolución de los equipos de fusión por inducción en vacío refleja una transición hacia estructuras multifuncionales capaces de adaptarse a diversos procesos tecnológicos. Se prevé que predominen las configuraciones modulares, que permiten combinaciones personalizadas de componentes para satisfacer eficazmente los requisitos de procesos específicos.
Control de precisión y automatización
La integración de tecnologías avanzadas, como los sistemas informáticos y la adquisición inteligente de señales, permite un control preciso de los procesos. Las sencillas interfaces hombre-máquina agilizan el funcionamiento, reducen los costes de mano de obra y aumentan la simplicidad operativa.
Sistemas auxiliares
Además de los componentes principales, los sistemas auxiliares, como las fuentes de alimentación, las unidades de control y los sistemas de refrigeración, desempeñan un papel fundamental. Estos sistemas garantizan la entrada de energía para la fusión y evitan el sobrecalentamiento de los componentes críticos.
Consideraciones estructurales
La atención al diseño estructural es primordial para evitar la descarga de vacío. El aislamiento de todos los cuerpos cargados dentro de la carcasa del horno y la eliminación de bordes afilados en el diseño del inductor son cruciales para garantizar un funcionamiento ininterrumpido.
Ventajas clave
- Fusión de determinadas aleaciones de titanio: Las condiciones de vacío permiten la fusión de aleaciones de titanio, ampliando la aplicabilidad del horno.
- Prevención de reacciones químicas: Los entornos de vacío protegen los metales y aleaciones fundidos de reacciones químicas indeseables con inclusiones no metálicas.
- Eliminación de gases nocivos: El estado de vacío facilita la eliminación de gases disueltos nocivos y contaminantes del metal fundido líquido, garantizando la pureza del material.
En conclusión, los hornos de fusión por inducción en vacío encarnan la versatilidad y la precisión, impulsando avances en los procesos metalúrgicos a través de un diseño innovador y la integración tecnológica.
Ventajas medioambientales y de rendimiento
La fusión por inducción en vacío (VIM) ofrece importantes ventajas medioambientales y de rendimiento, lo que la convierte en el método preferido para producir materiales de gran pureza con propiedades superiores.
Alta pureza y calidad
El VIM destaca en la producción de materiales de pureza y calidad excepcionales. Al operar en un entorno de vacío, el VIM elimina el riesgo de contaminación por gases atmosféricos como el oxígeno y el nitrógeno. Esto garantiza una fusión más limpia y homogénea, desprovista de inclusiones nocivas e impurezas que podrían comprometer la integridad mecánica del material. En consecuencia, las aleaciones resultantes presentan mejores propiedades mecánicas y características de rendimiento.
Atmósfera controlada
Dentro de la cámara de vacío, la atmósfera se controla meticulosamente, lo que permite una regulación precisa de la composición y la presión del gas. Este nivel de control es primordial para lograr la composición química deseada del material fundido, evitando al mismo tiempo oxidaciones no deseadas o reacciones con los gases ambientales. Como resultado, el VIM permite la producción de materiales con propiedades químicas consistentes y mínima reactividad, garantizando un rendimiento superior en diversas aplicaciones.
Ventajas resumidas
Las ventajas de utilizar un horno de fusión por inducción al vacío son múltiples:
-
Eliminación de gases: El VIM funciona a presiones extremadamente bajas, normalmente en torno a 0,000001 atmósferas. Este entorno facilita la eliminación de gases indeseables y elementos volátiles de las materias primas durante el proceso de fusión, garantizando la producción de aleaciones de gran pureza.
-
Análisis químico preciso: La ausencia de atmósfera en la cámara de vacío permite un control excepcional y reproducible de la composición química de los materiales fundidos. Esta precisión permite la producción de aleaciones con composiciones a medida y propiedades deseadas, mejorando la eficiencia global del proceso y la calidad del producto.
-
Control superior del proceso: El VIM ofrece un control independiente de la presión, la temperatura y la agitación inductiva, lo que proporciona un control del proceso sin precedentes. Esta flexibilidad permite el desarrollo de prácticas de fusión optimizadas específicas para cada composición de aleación, mejorando aún más el rendimiento y la consistencia de los materiales producidos.
Además de los beneficios medioambientales, las ventajas de un horno de inducción de vacío se extienden al procesamiento de diversos metales y aleaciones:
- Mejora de la pureza: La ausencia de contaminación por aire y escorias en los hornos de inducción al vacío contribuye a la producción de aleaciones relativamente puras con altos niveles de rendimiento.
- Eliminación de gases: El funcionamiento en condiciones de vacío permite reducir el contenido de gas en el acero y las aleaciones fundidos, lo que da lugar a materiales con menores concentraciones de gas y mejores propiedades.
- Prevención de la oxidación: El procesamiento de metales en un entorno de vacío mitiga el riesgo de oxidación, preservando la integridad del material procesado.
- Evaporación de impurezas: Impurezas como el plomo (Pb) y el bismuto (Bi) pueden evaporarse más fácilmente en el vacío, facilitando la purificación del material durante el proceso de fundición.
En conclusión,los hornos de fusión por inducción al vacío ofrecen una solución completa para producir materiales de gran pureza con características de rendimiento superiores, al tiempo que mitigan la contaminación ambiental y garantizan la eficiencia del proceso.
CONTÁCTANOS PARA UNA CONSULTA GRATUITA
Los productos y servicios de KINTEK LAB SOLUTION han sido reconocidos por clientes de todo el mundo. Nuestro personal estará encantado de ayudarle con cualquier consulta que pueda tener. ¡Contáctenos para una consulta gratuita y hable con un especialista del producto para encontrar la solución más adecuada para sus necesidades de aplicación!