La soldadura fuerte y la soldadura blanda son dos métodos de unión de metales, pero difieren significativamente en cuanto a las temperaturas necesarias y las propiedades de los materiales de aportación utilizados.La soldadura fuerte suele requerir temperaturas más elevadas que la soldadura blanda, ya que utiliza metales de aportación que se funden por encima de los 450°C (840°F), mientras que la soldadura blanda emplea metales de aportación que se funden por debajo de este umbral.Esta diferencia de temperatura afecta a la resistencia, durabilidad y aplicaciones de las uniones creadas con cada método.A continuación, analizamos las principales diferencias entre la soldadura fuerte y la soldadura blanda, centrándonos en los requisitos de temperatura, los materiales de aportación y las propiedades de las uniones resultantes.
Explicación de los puntos clave:
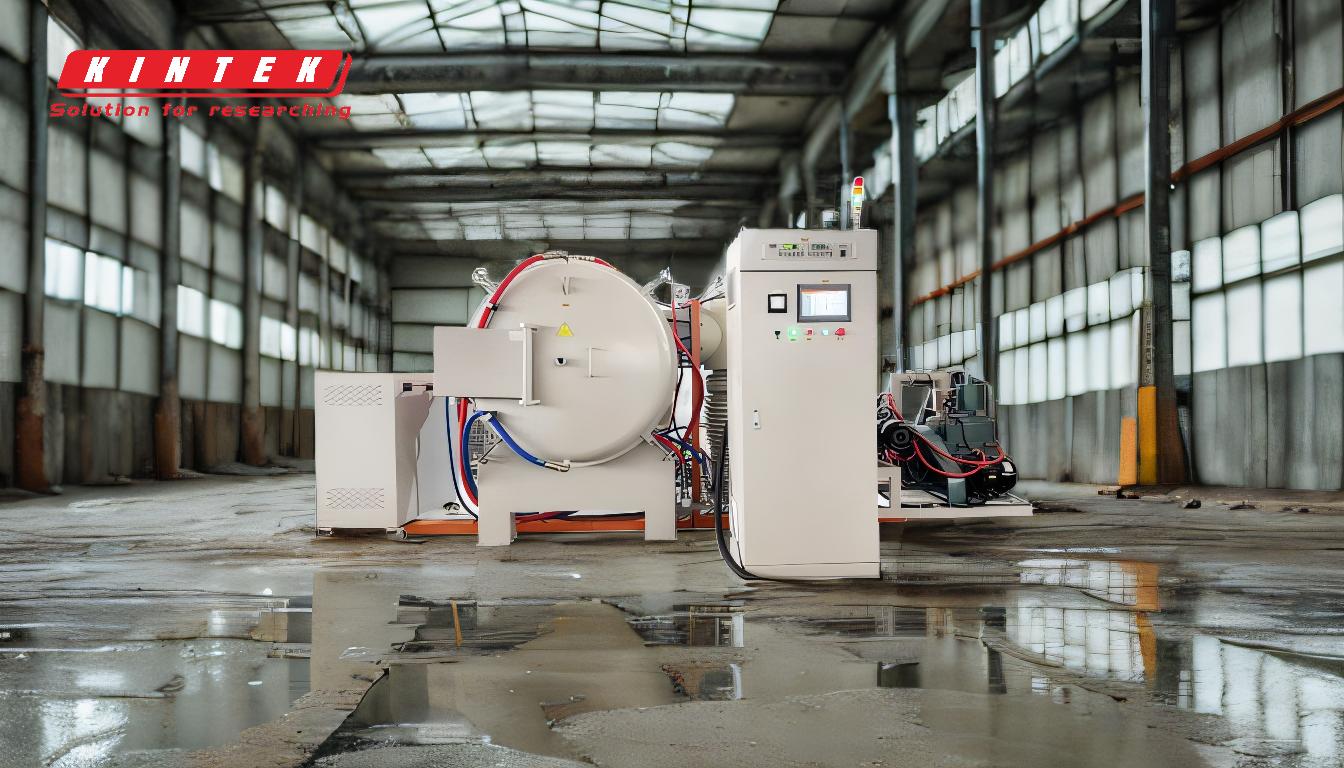
-
Requisitos de temperatura:
- Soldadura fuerte:La soldadura fuerte requiere temperaturas más altas, normalmente superiores a 450°C (840°F).Esto se debe a que los metales de aportación utilizados en la soldadura fuerte tienen puntos de fusión más altos, lo que permite que el proceso cree uniones más fuertes y duraderas.Las altas temperaturas también permiten que el metal de aportación fluya hacia la junta por capilaridad, garantizando una unión fuerte.
- Soldadura:La soldadura, por el contrario, se realiza a temperaturas más bajas, inferiores a 450°C.Los metales de aportación utilizados en la soldadura tienen puntos de fusión más bajos, lo que hace que el proceso sea adecuado para materiales delicados o sensibles al calor.Sin embargo, las uniones resultantes suelen ser menos resistentes que las creadas mediante soldadura fuerte.
-
Materiales de relleno:
- Soldadura fuerte:Los metales de aportación utilizados en la soldadura fuerte suelen ser aleaciones de cobre, plata o níquel.Estos materiales tienen altos puntos de fusión y proporcionan una excelente resistencia a la corrosión.Entre las aleaciones de soldadura fuerte más comunes se encuentran las cargas a base de plata y las aleaciones de cobre-fósforo.
- Soldadura:La soldadura utiliza metales de aportación como aleaciones de estaño-plomo, estaño-plata o estaño-cobre.Estos materiales tienen puntos de fusión más bajos y se eligen por su capacidad para crear conexiones eléctricas o unir componentes finos y delicados sin dañarlos.
-
Resistencia de las uniones y aplicaciones:
- Soldadura fuerte:Debido a las temperaturas más altas y a los materiales de aportación más resistentes, las uniones por soldadura fuerte son más robustas y pueden soportar cargas mecánicas y tensiones térmicas más elevadas.Esto hace que la soldadura fuerte sea adecuada para aplicaciones en industrias como la automoción, la aeroespacial y la de calefacción, ventilación y aire acondicionado, donde son esenciales unas uniones fuertes y estancas.
- Soldadura:Las uniones soldadas son menos resistentes, pero resultan ideales para aplicaciones en las que se requiere conductividad eléctrica, como en electrónica y montaje de placas de circuitos.Las temperaturas más bajas también hacen que la soldadura sea una mejor opción para unir materiales sensibles al calor.
-
Diferencias de proceso:
- Soldadura fuerte:El proceso de soldadura fuerte consiste en calentar los metales base a una temperatura superior al punto de fusión del metal de aportación, pero inferior al punto de fusión de los metales base.A continuación, el metal de aportación se introduce en la unión por capilaridad, formando una fuerte unión al enfriarse.
- Soldadura:La soldadura consiste en calentar los metales base y aplicar el metal de aportación, que se funde y fluye hacia la unión.El proceso suele ser más rápido y requiere menos energía que la soldadura fuerte, por lo que es más adecuado para trabajos a pequeña escala o delicados.
-
Ventajas y limitaciones:
- Soldadura fuerte:La principal ventaja de la soldadura fuerte es la resistencia y durabilidad de las uniones que crea.Sin embargo, las altas temperaturas necesarias pueden limitar su uso con materiales sensibles al calor y requerir equipos especializados.
- Soldadura:La soldadura es ventajosa por sus menores requisitos de temperatura y su idoneidad para las conexiones eléctricas.Sin embargo, las uniones son menos resistentes y pueden no ser adecuadas para aplicaciones sometidas a grandes esfuerzos.
En resumen, la soldadura fuerte requiere temperaturas más altas que la soldadura blanda debido a las diferencias en los puntos de fusión de los metales de aportación utilizados.Esta diferencia influye en la resistencia, durabilidad y aplicaciones de las uniones creadas con cada método.La soldadura fuerte es preferible para aplicaciones de alta resistencia, mientras que la soldadura blanda es ideal para trabajos eléctricos y delicados.Comprender estas diferencias es crucial para seleccionar el método de unión adecuado en función de los requisitos específicos del proyecto.
Cuadro sinóptico:
Aspecto | Soldadura fuerte | Soldadura |
---|---|---|
Temperatura | Por encima de 450°C | Por debajo de 450°C |
Materiales de relleno | Aleaciones de cobre, plata o níquel (por ejemplo, a base de plata, cobre-fósforo) | Aleaciones de estaño-plomo, estaño-plata o estaño-cobre |
Resistencia de la unión | Fuerte, duradera y adecuada para aplicaciones de alta tensión | Menos fuerte, ideal para conexiones eléctricas y componentes delicados |
Aplicaciones | Automoción, aeroespacial, HVAC (juntas estancas) | Electrónica, montaje de placas de circuitos, materiales sensibles al calor |
Proceso | Mayor energía, acción capilar para uniones fuertes | Menor energía, más rápido y adecuado para trabajos a pequeña escala |
¿Necesita ayuda para elegir entre soldadura fuerte y soldadura blanda para su proyecto? Póngase en contacto con nuestros expertos hoy mismo.