Para lograr la mayor resistencia de la unión en soldadura fuerte, se deben considerar cuidadosamente varios factores, incluida la selección de materiales, el diseño de la junta, la preparación de la superficie y el proceso de soldadura fuerte en sí. La soldadura fuerte implica unir dos o más piezas metálicas utilizando un metal de aportación con un punto de fusión superior a 450 °C (842 °F) pero inferior al punto de fusión de los metales base. La resistencia de la unión soldada depende de la calidad de la unión, las propiedades del metal de aportación y el diseño de la unión. A continuación se muestra una explicación detallada de cómo maximizar la resistencia de las juntas en soldadura fuerte.
Puntos clave explicados:
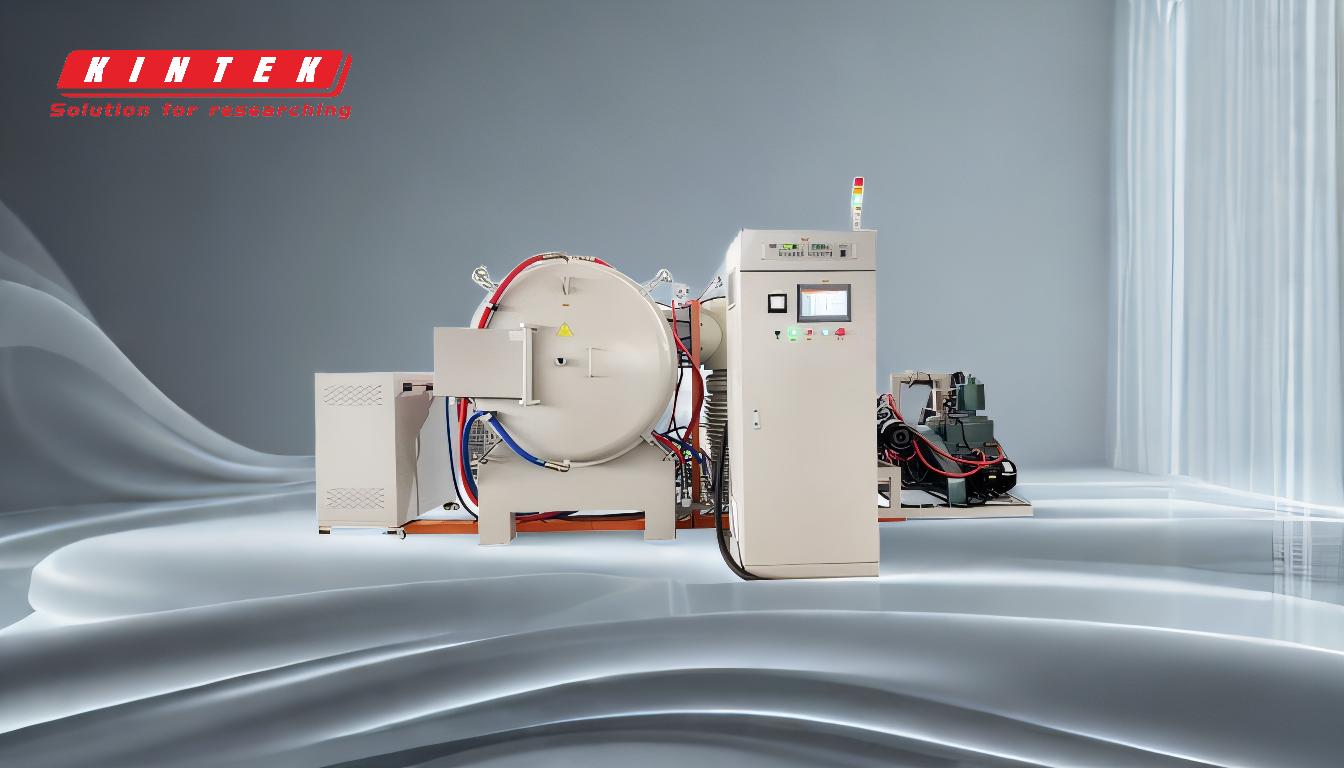
-
Diseño conjunto adecuado:
- El diseño de la unión es fundamental para lograr la máxima resistencia. Una junta bien diseñada garantiza una distribución uniforme de la tensión y un flujo óptimo del metal de aportación.
- Los diseños de juntas comunes incluyen juntas superpuestas, juntas a tope y juntas biseladas. Las juntas traslapadas a menudo se prefieren para la soldadura fuerte porque proporcionan una mayor superficie de unión, lo que mejora la resistencia.
- Se debe controlar cuidadosamente la holgura entre las piezas que se van a unir (espacio de unión). Un espacio de 0,05 a 0,15 mm (0,002 a 0,006 pulgadas) suele ser ideal para que la acción capilar atraiga el metal de aportación hacia la junta.
-
Preparación de la superficie:
- La limpieza es esencial para una unión soldada fuerte. Contaminantes como aceite, grasa, óxidos y suciedad pueden impedir la humectación y unión adecuadas del metal de aportación.
- Las superficies deben limpiarse utilizando métodos mecánicos (p. ej., abrasión) o métodos químicos (p. ej., desengrasado y decapado) antes de soldar.
- La preparación adecuada de la superficie garantiza que el metal de aportación pueda fluir suavemente y formar una unión metalúrgica fuerte con los metales base.
-
Selección de metal de aportación:
- La elección del metal de aportación influye significativamente en la resistencia de la unión. El metal de aportación debe tener buena humectabilidad, compatibilidad con los metales base y propiedades mecánicas apropiadas.
- Los metales de aportación comunes incluyen aleaciones a base de plata, aleaciones a base de cobre y aleaciones a base de níquel. La selección depende de los metales base y de las condiciones de funcionamiento de la junta.
- El metal de aportación también debe tener un rango de fusión adecuado para garantizar que fluya correctamente sin sobrecalentar los metales base.
-
Calefacción y refrigeración controladas:
- El calentamiento uniforme es crucial para lograr una unión soldada fuerte. Un calentamiento desigual puede provocar una unión incompleta o tensiones térmicas.
- El método de calentamiento (p. ej., soplete, horno, inducción) debe seleccionarse en función del tamaño, la forma y los materiales de la junta.
- El enfriamiento controlado es igualmente importante para evitar grietas o distorsiones. Se debe evitar el enfriamiento rápido a menos que los materiales y el proceso lo requieran específicamente.
-
Uso de fundente o atmósfera protectora:
- El fundente se utiliza a menudo para eliminar óxidos y promover la humectación del metal de aportación. También protege la unión de la oxidación durante el proceso de soldadura fuerte.
- En algunos casos, se utiliza una atmósfera protectora (por ejemplo, gas inerte o vacío) en lugar de fundente para evitar la oxidación y la contaminación.
- La elección entre fundente y atmósfera protectora depende de los materiales y del método de soldadura fuerte.
-
Evitar volver a fundir las juntas existentes:
- Al reparar juntas defectuosas, es mejor aplicar una pequeña cantidad de metal de aportación adicional en lugar de volver a fundir la junta existente. La nueva fusión puede alterar la microestructura de la articulación y reducir su resistencia.
- La mayoría de las aleaciones para soldadura fuerte desarrollan una temperatura de refusión más alta después de la soldadura fuerte inicial, lo que puede hacer que la refusión sea menos efectiva y potencialmente dañina para la unión.
-
Inspección y prueba posteriores a la soldadura fuerte:
- Después de soldar, se debe inspeccionar la unión para detectar defectos como huecos, grietas o unión incompleta. Se pueden utilizar métodos de prueba no destructivos (por ejemplo, inspección visual, rayos X, pruebas ultrasónicas) para garantizar la calidad.
- También se pueden realizar pruebas mecánicas (por ejemplo, pruebas de tracción o corte) para verificar la resistencia de la unión.
Al considerar cuidadosamente estos factores, se puede lograr la mayor resistencia de la unión en soldadura fuerte. El diseño adecuado de la junta, la preparación de la superficie, la selección del metal de aportación, el calentamiento y enfriamiento controlados y el uso de fundente o atmósferas protectoras contribuyen a una junta soldada fuerte y confiable. Además, evitar volver a fundir las juntas existentes y realizar inspecciones exhaustivas posteriores a la soldadura fuerte garantiza la integridad de la junta a lo largo del tiempo.
Tabla resumen:
Factor | Consideraciones clave |
---|---|
Diseño conjunto | Utilice juntas traslapadas para áreas de unión más grandes; mantenga un espacio de 0,05 a 0,15 mm para la acción capilar. |
Preparación de la superficie | Limpiar las superficies a fondo para eliminar los contaminantes; Utilice métodos mecánicos o químicos. |
Selección del metal de aportación | Elija aleaciones (por ejemplo, plata, cobre, níquel) con buena humectabilidad y compatibilidad. |
Calefacción y refrigeración | Asegurar un calentamiento uniforme; Evite el enfriamiento rápido para evitar grietas o deformaciones. |
Flujo/atmósfera protectora | Utilice fundente o gas inerte para evitar la oxidación y promover el flujo del metal de aportación. |
Evite volver a derretirse | Agregue metal de aportación nuevo en lugar de volver a fundirlo para preservar la resistencia de la unión. |
Inspección posterior a la soldadura | Inspeccionar en busca de defectos mediante pruebas visuales, de rayos X o ultrasónicas; realizar pruebas mecanicas. |
¿Necesita asesoramiento de expertos para lograr uniones soldadas fuertes? Contáctanos hoy ¡Para soluciones personalizadas!