El grosor del revestimiento de un horno de inducción es un factor crítico que depende de diversas variables, como el tipo de horno, el material que se funde y la temperatura de funcionamiento.Aunque las referencias facilitadas no especifican los espesores exactos del revestimiento, ponen de relieve la importancia de éste para proteger el horno y garantizar un funcionamiento eficaz.El revestimiento debe soportar temperaturas extremas, choques térmicos y reacciones químicas con los metales fundidos.Normalmente, el grosor se diseña para equilibrar el aislamiento térmico, la integridad estructural y la capacidad del horno.Para conocer el espesor exacto del revestimiento, se recomienda consultar las especificaciones del fabricante o las normas del sector.
Explicación de los puntos clave:
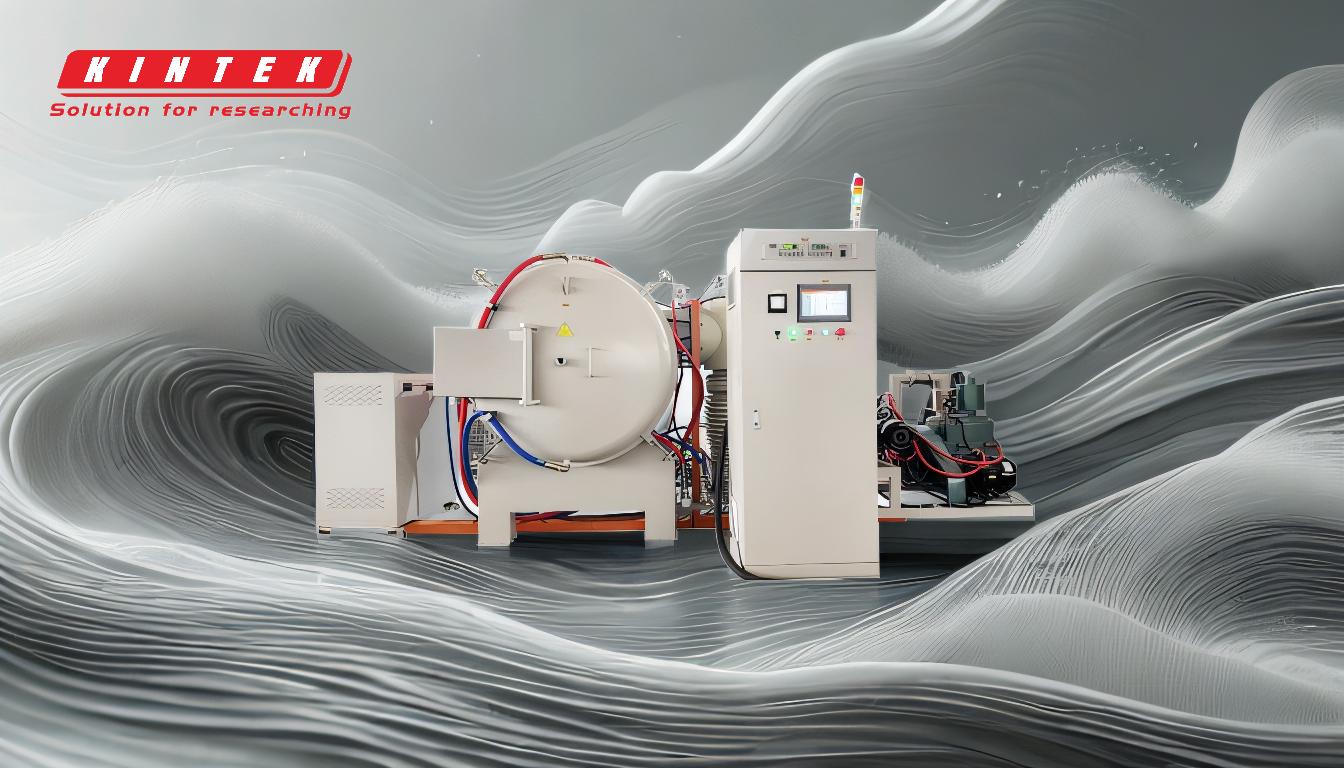
-
Finalidad del horno de inducción Revestimiento:
- El revestimiento de un horno de inducción sirve de barrera entre el metal fundido y los componentes estructurales del horno, como la bobina.Protege el cuerpo del horno de los daños causados por las altas temperaturas y las reacciones químicas.
- Garantiza la contención segura del metal fundido, evitando fugas o contaminaciones.
-
Factores que influyen en el espesor del revestimiento:
- Material que se funde:Los distintos metales y aleaciones requieren revestimientos con propiedades específicas, como la resistencia a las reacciones químicas o al choque térmico.Por ejemplo, fundir acero puede requerir un revestimiento más grueso o robusto que fundir aluminio.
- Temperatura de funcionamiento:Los hornos de inducción pueden alcanzar temperaturas de hasta 1800°C o más.El revestimiento debe ser lo suficientemente grueso para proporcionar un aislamiento adecuado y soportar estas temperaturas extremas.
- Tipo y tamaño del horno:Los hornos más grandes o los diseñados para un funcionamiento continuo pueden requerir revestimientos más gruesos para garantizar su durabilidad y longevidad.
- Estrés térmico y mecánico:El revestimiento debe resistir los ciclos térmicos y las tensiones mecánicas provocadas por la acción de agitación del metal fundido.
-
Materiales típicos de revestimiento:
- Los revestimientos suelen estar hechos de materiales refractarios como alúmina, sílice o magnesia, elegidos por sus altos puntos de fusión y su resistencia al desgaste.
- La elección del material y su espesor se adaptan a la aplicación específica, garantizando un rendimiento y una seguridad óptimos.
-
Consideraciones sobre el diseño:
- El grosor del revestimiento es un equilibrio entre el aislamiento suficiente y el mantenimiento de la capacidad interna del horno.
- Los revestimientos más gruesos ofrecen mejor aislamiento y durabilidad, pero pueden reducir el volumen de trabajo efectivo del horno.
- Los revestimientos más finos pueden aumentar la capacidad, pero requieren un mantenimiento o una sustitución más frecuentes.
-
Implicaciones prácticas para los compradores:
- A la hora de seleccionar un horno de inducción, los compradores deben tener en cuenta el grosor y el material del revestimiento en relación con sus requisitos específicos de fusión.
- Consultar con fabricantes o expertos del sector puede ayudar a determinar las especificaciones óptimas del revestimiento para una aplicación determinada.
- La inspección y el mantenimiento periódicos del revestimiento son esenciales para garantizar un funcionamiento seguro y eficaz del horno.
En conclusión, aunque en las referencias no se especifica el grosor exacto del revestimiento de un horno de inducción, está claro que el diseño del revestimiento se adapta a los requisitos operativos del horno.Factores como el tipo de material, la temperatura de funcionamiento y el tamaño del horno desempeñan un papel importante a la hora de determinar el grosor adecuado del revestimiento.Para obtener detalles precisos, los compradores deben consultar las directrices del fabricante o buscar el asesoramiento de expertos.
Cuadro sinóptico:
Factor | Impacto en el espesor del revestimiento |
---|---|
Material fundido | Revestimientos más gruesos para metales como el acero; más finos para el aluminio debido a su diferente resistencia química. |
Temperatura de funcionamiento | Las temperaturas más altas requieren revestimientos más gruesos para un mejor aislamiento y durabilidad. |
Tipo y tamaño del horno | Los hornos más grandes o de funcionamiento continuo necesitan revestimientos más gruesos para una mayor longevidad. |
Tensión térmica/mecánica | Los revestimientos deben resistir las tensiones provocadas por los ciclos térmicos y la agitación de metal fundido. |
Materiales de revestimiento | La alúmina, la sílice o la magnesia se eligen por sus altos puntos de fusión y su resistencia al desgaste. |
¿Necesita ayuda para determinar el grosor de revestimiento adecuado para su horno de inducción? Póngase en contacto hoy mismo con nuestros expertos para un asesoramiento personalizado.