Al decidir si soldar o soldar aluminio, es esencial considerar la aplicación específica, los requisitos de resistencia de las uniones y los desafíos asociados con cada método. La soldadura fuerte es particularmente útil para unir aluminio en situaciones en las que mantener la integridad del material base es fundamental, ya que minimiza el riesgo de grietas y cambios metalúrgicos. Sin embargo, las uniones soldadas son generalmente más débiles y menos resistentes al calor que las uniones soldadas. La soldadura, por otro lado, proporciona uniones más fuertes pero requiere un control cuidadoso del aporte de calor para evitar distorsiones y daños al aluminio. La elección depende en última instancia del uso previsto de la junta, de los materiales utilizados y de las propiedades mecánicas deseadas.
Puntos clave explicados:
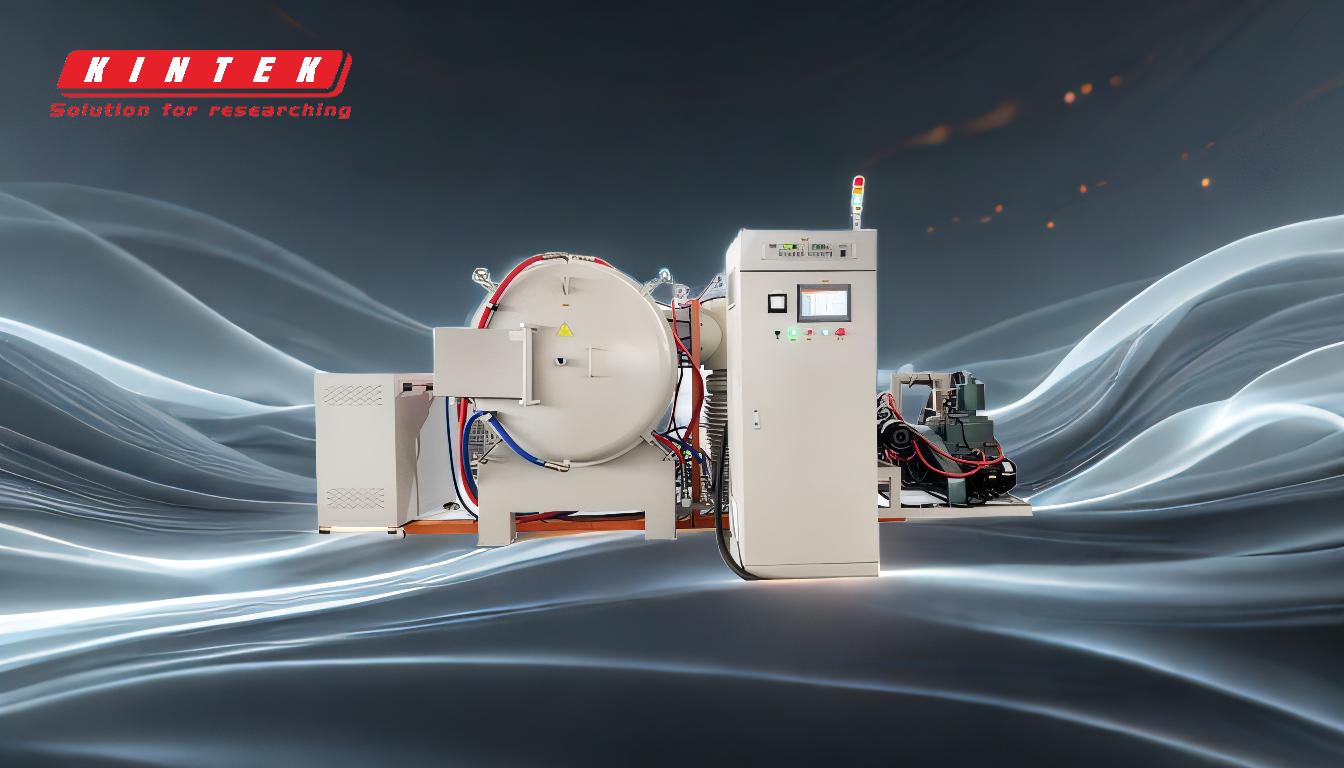
-
Soldadura de aluminio:
- Descripción general del proceso: La soldadura fuerte implica unir piezas de aluminio utilizando un metal de aportación que se funde a una temperatura más baja que el material base. Los dos tipos principales son la soldadura fuerte con fundente y la soldadura fuerte sin fundente (por ejemplo, soldadura fuerte al vacío).
-
Ventajas:
- Reducción del riesgo de agrietamiento y cambios metalúrgicos en la zona afectada por el calor (ZAT).
- Adecuado para reparaciones pequeñas o ensamblajes complejos donde la soldadura puede resultar poco práctica.
- En la soldadura fuerte al vacío, la capa de óxido de aluminio se agrieta con el calor, lo que permite que la aleación de soldadura llegue al material base, y la oxidación se evita manteniendo un alto vacío y utilizando materiales absorbentes.
-
Limitaciones:
- Las uniones soldadas tienen menor resistencia y resistencia al calor en comparación con las uniones soldadas.
- Requiere un control preciso de la uniformidad de la temperatura (±5,5 °C) y los niveles de vacío (10⁻⁵ mbar o mejor) para obtener resultados óptimos.
-
Soldadura de Aluminio:
- Descripción general del proceso: La soldadura implica fundir el material de aluminio base para formar una junta, a menudo con la adición de un metal de aportación. Los métodos comunes incluyen la soldadura TIG (gas inerte de tungsteno) y MIG (gas inerte de metal).
-
Ventajas:
- Produce uniones más fuertes con mayor resistencia al calor, lo que lo hace adecuado para aplicaciones estructurales.
- Puede manejar materiales más gruesos y cargas de tensión más altas en comparación con la soldadura fuerte.
-
Limitaciones:
- Mayor riesgo de agrietamiento y deformación debido al alto aporte de calor requerido.
- Requiere operadores capacitados y un control preciso de los parámetros de soldadura para evitar defectos.
-
Consideraciones de aplicación:
- Fuerza conjunta: Si la unión va a estar sometida a altas tensiones o calor, la soldadura suele ser la mejor opción. Para aplicaciones menos exigentes, la soldadura fuerte puede ser suficiente.
- Espesor del material: La soldadura es más adecuada para materiales más gruesos, mientras que la soldadura fuerte funciona bien para secciones más delgadas o componentes delicados.
- Complejidad del montaje: A menudo se prefiere la soldadura fuerte para ensamblajes complejos o de varias piezas donde la soldadura puede ser un desafío.
-
Requisitos del proceso:
- Soldadura: Requiere un control cuidadoso de la temperatura, los niveles de vacío y los tiempos de ciclo. A menudo se utilizan hornos de temperatura controlada de múltiples zonas para garantizar la uniformidad.
- Soldadura: Requiere operadores capacitados, gases protectores adecuados y un control preciso de la entrada de calor para evitar defectos como porosidad y grietas.
-
Costo y eficiencia:
- Soldadura: Generalmente es más rentable para reparaciones o ensamblajes a pequeña escala debido a los menores costos de equipo y mano de obra. Sin embargo, el proceso puede llevar mucho tiempo, especialmente para la soldadura fuerte al vacío.
- Soldadura: Puede implicar costos iniciales más altos debido a la necesidad de equipos especializados y mano de obra calificada, pero a menudo es más eficiente para aplicaciones a gran escala o de alta resistencia.
En resumen, la decisión de soldar aluminio depende de los requisitos específicos de la aplicación, incluida la resistencia de la unión, el espesor del material y la complejidad del ensamblaje. La soldadura fuerte ofrece ventajas en términos de reducción del riesgo de agrietamiento y idoneidad para diseños complejos, mientras que la soldadura proporciona uniones más fuertes y resistentes al calor para aplicaciones exigentes.
Tabla resumen:
Aspecto | Soldadura de aluminio | Soldadura de Aluminio |
---|---|---|
Descripción general del proceso | Utiliza un metal de aportación con un punto de fusión más bajo que el material base. | Derrite el material base, a menudo con un metal de aportación, para formar una junta. |
Ventajas | - Reducción del riesgo de fisuras y cambios metalúrgicos. | - Uniones más fuertes con mayor resistencia al calor. |
- Adecuado para montajes complejos o pequeñas reparaciones. | - Ideal para aplicaciones estructurales y materiales más gruesos. | |
Limitaciones | - Menor fuerza de unión y resistencia al calor. | - Mayor riesgo de agrietamiento y deformación. |
- Requiere control preciso de temperatura y vacío. | - Requiere operadores capacitados y un control preciso de la entrada de calor. | |
Mejores aplicaciones | - Materiales finos, componentes delicados o ensamblajes complejos. | - Materiales más gruesos, aplicaciones de alto estrés o alto calor. |
Costo y eficiencia | - Rentable para reparaciones a pequeña escala, pero puede llevar mucho tiempo. | - Costos iniciales más altos pero eficientes para aplicaciones a gran escala o de alta resistencia. |
¿Aún no estás seguro de si soldar o soldar tu proyecto de aluminio? Póngase en contacto con nuestros expertos hoy ¡Para orientación personalizada!