Los hornos de inducción, si bien son muy eficientes para fundir metales, presentan varias desventajas que pueden afectar su idoneidad para determinadas aplicaciones. Uno de los principales inconvenientes es su falta de capacidad de refinado, lo que obliga a que los materiales de carga estén libres de óxidos y sean de composición conocida. Además, algunos elementos de aleación pueden perderse debido a la oxidación, lo que hace necesario volver a agregarlos a la masa fundida. Estas limitaciones pueden afectar la eficiencia general y la rentabilidad del uso de hornos de inducción en procesos de fusión de metales.
Puntos clave explicados:
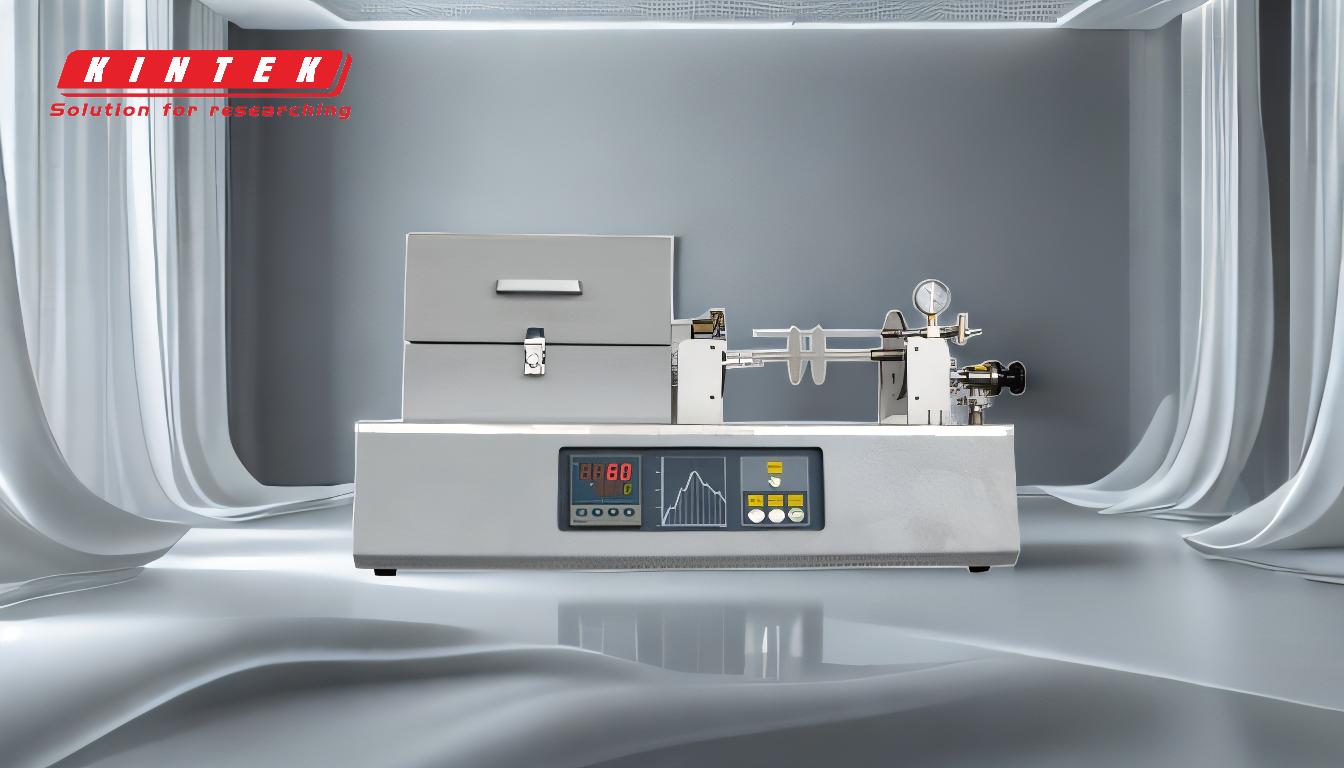
-
Falta de capacidad de refinación:
- Los hornos de inducción no tienen la capacidad de refinar metales. Esto significa que los materiales de carga utilizados ya deben estar libres de óxidos y otras impurezas. Para las industrias que requieren metales de alta pureza, esto puede suponer una limitación importante.
- La ausencia de capacidad de refinación puede llevar a la necesidad de pasos de procesamiento adicionales, aumentando tanto el tiempo como el costo.
-
Requisito de composición conocida:
- Los materiales de carga deben tener una composición conocida para garantizar la calidad deseada del producto final. Este requisito puede complicar el abastecimiento y la preparación de materiales, especialmente cuando se trata de aleaciones complejas.
- Cualquier desviación en la composición de los materiales de carga puede provocar inconsistencias en el producto final, afectando su rendimiento y confiabilidad.
-
Pérdida de elementos de aleación:
- Durante el proceso de fusión, algunos elementos de aleación pueden perderse debido a la oxidación. Esta pérdida puede alterar la composición del producto final, comprometiendo potencialmente sus propiedades.
- Para contrarrestar esto, es necesario volver a añadir estos elementos a la masa fundida, lo que puede aumentar los costes de material y complicar el proceso de fusión.
-
Eficiencia energética y costo:
- Si bien los hornos de inducción son generalmente eficientes energéticamente, la necesidad de materiales de carga de alta calidad y la posible pérdida de elementos de aleación pueden compensar estos ahorros. La rentabilidad general del uso de un horno de inducción debe evaluarse cuidadosamente en función de los requisitos específicos de la aplicación.
- La inversión inicial en un horno de inducción igbt puede ser alto y los costos operativos asociados con el mantenimiento de la calidad del material requerida pueden aumentar el gasto total.
-
Complejidad operativa:
- La necesidad de un control preciso sobre los materiales de carga y el proceso de fusión puede aumentar la complejidad operativa. Se requiere personal calificado para gestionar estos procesos de manera efectiva, lo que aumenta los costos laborales.
- La posibilidad de pérdida de material y la necesidad de volver a agregar elementos de aleación también pueden introducir variabilidad en el proceso de producción, lo que requiere medidas de control de calidad adicionales.
En resumen, si bien los hornos de inducción ofrecen varias ventajas, incluida la eficiencia energética y el control preciso de la temperatura, sus desventajas (como la falta de capacidad de refinación, el requisito de una composición conocida y la posible pérdida de elementos de aleación) deben considerarse cuidadosamente. Estos factores pueden afectar la eficiencia general, el costo y la idoneidad de los hornos de inducción para aplicaciones específicas.
Tabla resumen:
Desventaja | Impacto |
---|---|
Falta de capacidad de refinación | Requiere materiales de carga de alta pureza; aumenta el tiempo y el costo. |
Requisito de composición conocida | Complica el abastecimiento de materiales; las desviaciones afectan la calidad del producto. |
Pérdida de elementos de aleación | La oxidación provoca pérdida de material; la readición aumenta los costos. |
Eficiencia energética y costo | Alta inversión inicial; Los costos operativos pueden compensar los ahorros de energía. |
Complejidad operativa | Requiere personal calificado; la variabilidad puede requerir control de calidad. |
¿Necesita ayuda para elegir el horno adecuado para su aplicación? Póngase en contacto con nuestros expertos hoy !