El recocido es un proceso de tratamiento térmico que implica calentar metales a una temperatura específica, mantenerlos a esa temperatura y luego enfriarlos lentamente. Este proceso ofrece varias ventajas, como mejorar la ductilidad, reducir la dureza, aliviar las tensiones internas y mejorar la maquinabilidad y las propiedades eléctricas. Sin embargo, también tiene desventajas, que incluyen baja productividad, largos tiempos de enfriamiento, calentamiento desigual y sensibilidad a las variaciones de temperatura, que pueden afectar la calidad del material y el rendimiento del equipo. El proceso requiere un manejo cuidadoso después del tratamiento, ya que los materiales se vuelven muy sensibles a los golpes y al estrés.
Puntos clave explicados:
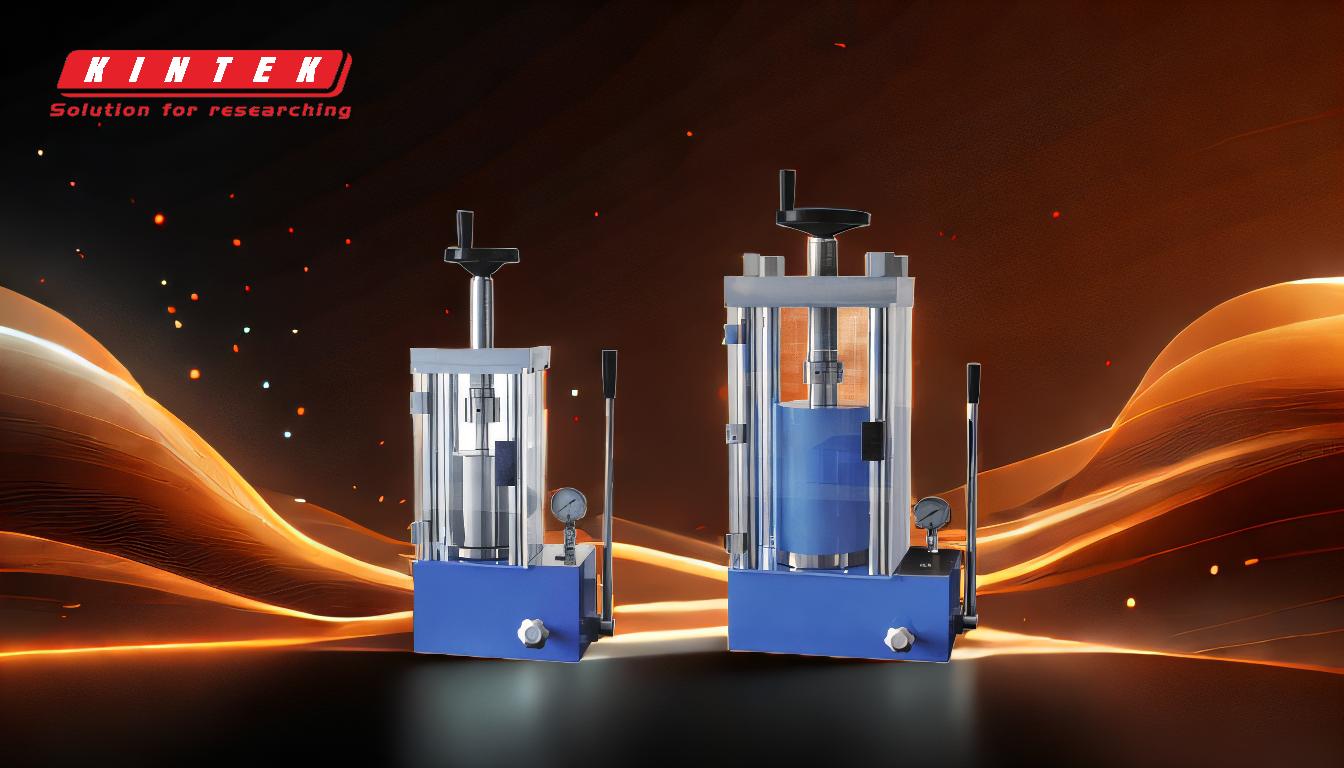
-
Ventajas del recocido:
- Ductilidad y trabajabilidad mejoradas: El recocido hace que los metales sean más dúctiles, lo que permite darles forma sin agrietarse. Esto es particularmente útil en procesos de fabricación en los que es necesario doblar, estirar o darles formas complejas a los metales.
- Reducción de Dureza: Al reducir la dureza, el recocido hace que los metales sean más fáciles de mecanizar, cortar o perforar, lo que resulta beneficioso en industrias que requieren un trabajo de metales preciso.
- Alivio del estrés: Las tensiones internas causadas por procesos de fabricación anteriores, como la soldadura o el trabajo en frío, se alivian durante el recocido. Esto evita la deformación o falla del material durante el uso.
- Propiedades eléctricas mejoradas: El recocido refina la estructura cristalina de los metales, mejorando su conductividad eléctrica. Esto es crucial para los materiales utilizados en aplicaciones eléctricas, como cableado o transformadores.
- Propiedades mecánicas mejoradas: El proceso mejora las propiedades mecánicas como la dureza y la resistencia, lo que hace que los materiales sean más duraderos y resistentes al desgaste.
-
Desventajas del recocido:
- Baja productividad: Los métodos de recocido tradicionales, como el recocido al vacío, suelen tener una baja productividad debido a los largos ciclos de calentamiento y enfriamiento.
- Calentamiento desigual: Los materiales, especialmente las formas grandes o complejas, pueden experimentar un calentamiento desigual, lo que genera propiedades inconsistentes del material y problemas de calidad.
- Sensibilidad a la temperatura: Las variaciones de temperatura durante el proceso de recocido (que oscilan entre 5 y 25 °C) pueden afectar la estabilidad y consistencia del producto final.
- Degradación del equipo: Los ciclos frecuentes entre ambientes de vacío y presión normal pueden causar desgaste en el equipo, reduciendo su vida útil.
- Sensibilidad post-tratamiento: Los materiales recocidos son muy sensibles a los golpes, las vibraciones y la tensión, por lo que requieren un manejo cuidadoso para evitar daños.
-
Aplicaciones y consideraciones:
- Efectos específicos del material: Por ejemplo, en acero para tuberías X80, el recocido a 200 °C durante 12 horas aumenta el límite elástico en un 10 % pero reduce el alargamiento en un 20 %. Esto se debe a la formación de una atmósfera de Cottrell, que fija las dislocaciones y reduce la densidad de dislocaciones móviles.
- Uso de atmósferas inertes: Las mezclas de gas nitrógeno se utilizan a menudo durante el recocido para evitar la oxidación y reacciones químicas no deseadas, asegurando que el material conserve sus propiedades deseadas.
- Proceso de enfriamiento: El enfriamiento lento es fundamental para conseguir la estructura cristalina deseada y evitar reintroducir tensiones o defectos.
-
Desafíos en la implementación industrial:
- Calidad inconsistente: Los métodos tradicionales pueden dar lugar a una mala consistencia de la calidad inherente, lo que dificulta la producción de lotes uniformes de materiales.
- Estrés térmico y problemas de capas: Pueden surgir problemas como tensión térmica, canalización de capas y capas sueltas, particularmente en materiales como rollos de papel de aluminio, lo que afecta su usabilidad y rendimiento.
En resumen, el recocido es un proceso valioso para mejorar las propiedades de los materiales, pero presenta desafíos que requieren un manejo cuidadoso de la temperatura, el equipo y el manejo posterior al tratamiento para lograr resultados consistentes y de alta calidad.
Tabla resumen:
Aspecto | Ventajas | Desventajas |
---|---|---|
Ductilidad | Mejora la ductilidad, haciendo que los metales sean más fáciles de moldear sin agrietarse. | N / A |
Dureza | Reduce la dureza, mejorando la maquinabilidad y la precisión del corte. | N / A |
Alivio del estrés | Alivia tensiones internas, evitando deformaciones o fallos. | N / A |
Propiedades eléctricas | Mejora la conductividad eléctrica, ideal para cableado y transformadores. | N / A |
Propiedades mecánicas | Mejora la tenacidad, la resistencia y la resistencia al desgaste. | N / A |
Productividad | N / A | Baja productividad debido a largos ciclos de calentamiento y enfriamiento. |
Uniformidad de calentamiento | N / A | El calentamiento desigual puede provocar propiedades inconsistentes del material. |
Sensibilidad a la temperatura | N / A | Sensible a las variaciones de temperatura (5-25°C), afectando la estabilidad. |
Vida útil del equipo | N / A | Los ciclos frecuentes provocan desgaste, lo que reduce la vida útil del equipo. |
Manipulación posterior al tratamiento | N / A | Los materiales se vuelven muy sensibles a los golpes y al estrés, por lo que requieren un manejo cuidadoso. |
¿Necesita asesoramiento de expertos sobre procesos de recocido? Contáctanos hoy para optimizar el tratamiento térmico de sus metales!