El uso de gases inertes en la soldadura, especialmente en procesos como la soldadura por arco de tungsteno con gas (GTAW), ofrece importantes ventajas para evitar la oxidación y garantizar soldaduras de alta calidad.Los gases inertes, como el argón o el helio, crean un escudo protector alrededor de la zona de soldadura, impidiendo que gases reactivos como el oxígeno y el nitrógeno contaminen el metal fundido.Este efecto de protección reduce la formación de defectos como la porosidad, mejora la resistencia de la soldadura y mejora el aspecto general de la soldadura.Al mantener un entorno limpio y estable, los gases inertes también protegen el electrodo de tungsteno de la contaminación, garantizando un rendimiento constante del arco y prolongando la vida útil del equipo de soldadura.
Explicación de los puntos clave:
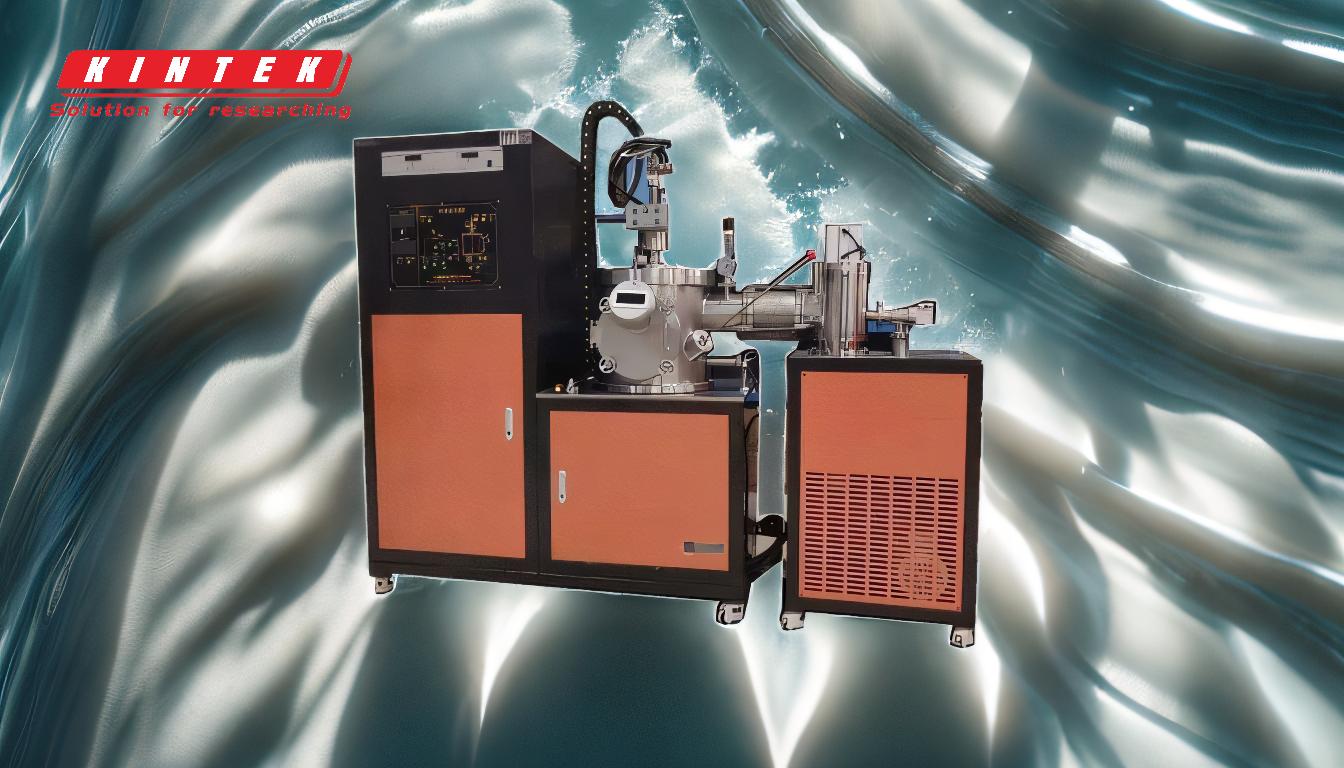
-
Prevención de la oxidación y la contaminación
- Los gases inertes como el argón y el helio son químicamente no reactivos, lo que significa que no reaccionan con el metal fundido ni con el electrodo de tungsteno.
- Cuando se utilizan como gas de protección, desplazan a los gases reactivos como el oxígeno y el nitrógeno del aire circundante, evitando la oxidación y nitruración del baño de soldadura.
- La oxidación puede provocar la formación de óxidos, que debilitan la soldadura y causan defectos como porosidad, grietas y fragilidad.Al eliminar la oxidación, los gases inertes garantizan una soldadura más limpia y resistente.
-
Reducción de la porosidad en las soldaduras
- La porosidad se produce cuando los gases quedan atrapados en el baño de soldadura al solidificarse, creando huecos o burbujas en la soldadura.
- Los gases reactivos, como el oxígeno y el nitrógeno, pueden disolverse en el metal fundido y formar burbujas al enfriarse el metal.
- Los gases inertes evitan que estos gases entren en el baño de soldadura, reduciendo significativamente el riesgo de porosidad y mejorando la integridad estructural de la soldadura.
-
Protección del electrodo de tungsteno
- En GTAW, el electrodo de tungsteno es fundamental para crear un arco estable.Sin embargo, la exposición a gases reactivos puede degradar o contaminar el electrodo.
- Los gases inertes protegen el electrodo de la oxidación y otras reacciones químicas, garantizando un rendimiento constante del arco y reduciendo la necesidad de sustituir el electrodo con frecuencia.
- Esta protección también minimiza las salpicaduras y mejora la precisión del proceso de soldadura.
-
Mejor aspecto y calidad de la soldadura
- Los gases inertes crean un entorno de soldadura estable y limpio, lo que se traduce en soldaduras más lisas y uniformes con menos defectos.
- La ausencia de oxidación y contaminación da lugar a una superficie de soldadura más brillante y limpia, lo que es especialmente importante para aplicaciones estéticas o al soldar materiales como acero inoxidable o aluminio.
- Las soldaduras de alta calidad son esenciales para aplicaciones que requieren uniones fuertes y duraderas, como en las industrias aeroespacial, de automoción y de la construcción.
-
Mayor control del proceso de soldadura
- Los gases inertes proporcionan un entorno de protección constante, lo que permite a los soldadores mantener un mejor control sobre la entrada de calor y la dinámica del baño de soldadura.
- Este control es especialmente importante para soldar materiales finos o realizar soldaduras de precisión, en las que incluso pequeños defectos pueden comprometer el producto final.
- El uso de gases inertes también reduce la probabilidad de salpicaduras de soldadura, lo que puede ahorrar tiempo y recursos durante la limpieza posterior a la soldadura.
-
Compatibilidad con metales reactivos
- Los metales reactivos como el titanio, el magnesio y el aluminio son muy susceptibles a la oxidación y la contaminación durante la soldadura.
- Los gases inertes son esenciales para soldar estos materiales, ya que evitan la formación de óxidos y otros compuestos que pueden debilitar la soldadura.
- Esta compatibilidad hace que los gases inertes sean indispensables para las industrias que dependen de materiales ligeros y resistentes a la corrosión, como la ingeniería aeroespacial y naval.
-
Rentabilidad a largo plazo
- Aunque los gases inertes pueden tener un coste inicial más elevado que los gases reactivos, sus ventajas suelen compensar la inversión inicial.
- Al reducir los defectos, mejorar la calidad de las soldaduras y prolongar la vida útil de los equipos de soldadura, los gases inertes pueden reducir los costes generales de producción.
- Además, la menor necesidad de reparaciones y retoques posteriores a la soldadura ahorra tiempo y mano de obra, lo que convierte a los gases inertes en una opción rentable para aplicaciones de soldadura de alta calidad.
En resumen, el uso de gases inertes en la soldadura proporciona una solución completa para evitar la oxidación, reducir los defectos y mejorar la calidad general de las soldaduras.Su capacidad para crear un entorno estable y libre de contaminación los hace indispensables para aplicaciones de soldadura críticas en diversos sectores.
Tabla resumen:
Beneficios clave | Descripción |
---|---|
Previene la oxidación | Protege la soldadura de los gases reactivos, reduciendo defectos como la porosidad y las grietas. |
Reduce la porosidad | Minimiza los gases atrapados en el baño de soldadura, mejorando la integridad estructural. |
Protege el electrodo de tungsteno | Garantiza un rendimiento constante del arco y prolonga la vida útil del electrodo. |
Mejora el aspecto de la soldadura | Produce soldaduras más limpias y lisas con menos defectos. |
Mejora el control del proceso | Proporciona un entorno estable para la soldadura precisa de materiales finos o delicados. |
Compatible con metales reactivos | Esencial para soldar titanio, aluminio y magnesio sin contaminación. |
Rentable a largo plazo | Reduce las necesidades de reparación y el desgaste de los equipos, disminuyendo los costes generales de producción. |
¿Está preparado para mejorar la calidad de sus soldaduras? Póngase en contacto con nosotros para obtener más información sobre el uso de gases inertes.