El tratamiento térmico de recocido, aunque es beneficioso para mejorar la maquinabilidad, las propiedades mecánicas y la trabajabilidad de los materiales, tiene varias desventajas.Entre ellos, el posible ablandamiento del material, que puede reducir la dureza y la resistencia, lo que lo hace inadecuado para aplicaciones que requieren una gran resistencia al desgaste.El proceso también puede provocar el crecimiento del grano, lo que afecta negativamente a las propiedades mecánicas.Además, el recocido requiere un control preciso de la temperatura y la velocidad de enfriamiento, por lo que requiere mucho tiempo y energía.También puede alterar la microestructura del material de forma no deseada y, en algunos casos, puede introducir oxidación superficial o descarburación, comprometiendo la integridad de la superficie del material.
Explicación de los puntos clave:
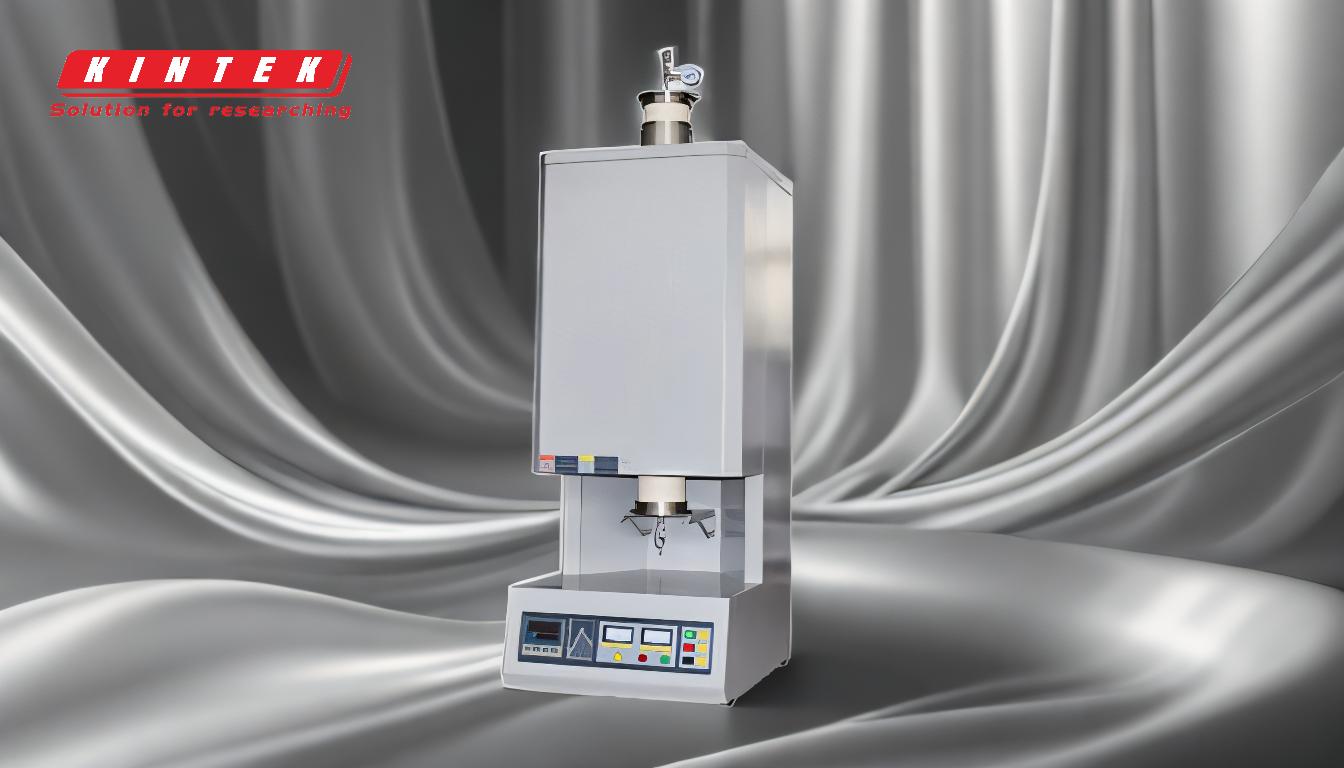
-
Ablandamiento de materiales:
- El recocido reduce la dureza y la resistencia del material al ablandarlo.Esto puede ser una desventaja en aplicaciones en las que se requiera una gran resistencia al desgaste o solidez.Por ejemplo, las herramientas o componentes sometidos a grandes esfuerzos pueden no funcionar bien tras el recocido.
-
Crecimiento del grano:
- Durante el recocido, los granos del material pueden aumentar de tamaño.Este crecimiento de los granos puede afectar negativamente a las propiedades mecánicas, como la tenacidad y la resistencia a la fatiga.Los granos más grandes pueden provocar una reducción del rendimiento general del material bajo carga.
-
Consumo de tiempo y energía:
- El proceso de recocido requiere un control preciso de la temperatura y la velocidad de enfriamiento, por lo que requiere mucho tiempo y energía.Esto puede aumentar los costes de producción y los plazos de entrega, especialmente en la fabricación a gran escala.
-
Cambios microestructurales:
- El recocido puede alterar la microestructura del material de formas que pueden no ser deseables para aplicaciones específicas.Por ejemplo, determinadas fases o estructuras que contribuyen a la resistencia del material u otras propiedades pueden perderse o transformarse durante el proceso de recocido.
-
Oxidación superficial y descarburación:
- Las altas temperaturas del recocido pueden provocar la oxidación o descarburación de la superficie, especialmente en metales como el acero.Esto puede comprometer la integridad de la superficie y las propiedades mecánicas del material, lo que requiere tratamientos superficiales adicionales o mecanizado para restaurar las propiedades deseadas.
-
Aplicabilidad limitada:
- No todos los materiales o aplicaciones se benefician del recocido.Por ejemplo, los materiales que requieren una gran dureza o microestructuras específicas pueden no ser adecuados para el recocido, ya que el proceso puede contrarrestar estos requisitos.
-
Potencial de distorsión:
- Durante las fases de calentamiento y enfriamiento del recocido, existe el riesgo de deformación o alabeo del material, especialmente en componentes complejos o de paredes finas.Esto puede provocar imprecisiones dimensionales y la necesidad de mecanizado adicional o medidas correctoras.
Al comprender estas desventajas, los compradores de equipos y consumibles pueden tomar decisiones informadas sobre si el recocido es el tratamiento térmico adecuado para sus necesidades y aplicaciones específicas.
Tabla resumen:
Desventaja | Impacto |
---|---|
Ablandamiento del material | Reduce la dureza y la resistencia, inadecuado para alta resistencia al desgaste. |
Crecimiento del grano | Afecta negativamente a la tenacidad y a la resistencia a la fatiga. |
Consumo de tiempo y energía | Aumenta los costes de producción y los plazos de entrega. |
Cambios microestructurales | Pueden alterar fases o estructuras deseables en el material. |
Oxidación superficial/Descarburación | Compromete la integridad de la superficie, requiriendo tratamientos adicionales. |
Aplicabilidad limitada | No apto para materiales que requieran gran dureza o microestructuras específicas. |
Potencial de deformación | Riesgo de alabeo, especialmente en componentes complejos o de paredes finas. |
¿Necesita ayuda para decidir si el recocido es adecuado para su aplicación? Póngase en contacto con nuestros expertos para un asesoramiento personalizado.