La sinterización en fase líquida, aunque es beneficiosa para mejorar la densificación y reducir las temperaturas de sinterización, presenta varios inconvenientes.Entre ellas se encuentran los problemas de control de la microestructura, la posibilidad de densificación desigual y las limitaciones en la selección de materiales debido a la necesidad de una fase líquida compatible.Además, el proceso puede dar lugar a problemas como el crecimiento del grano, tensiones residuales y anisotropía de las propiedades.Las altas temperaturas y el consumo de energía asociados a la sinterización en fase líquida también contribuyen a aumentar los costes operativos y los problemas medioambientales.Comprender estos inconvenientes es crucial para optimizar el proceso y seleccionar los materiales y parámetros adecuados para aplicaciones específicas.
Explicación de los puntos clave:
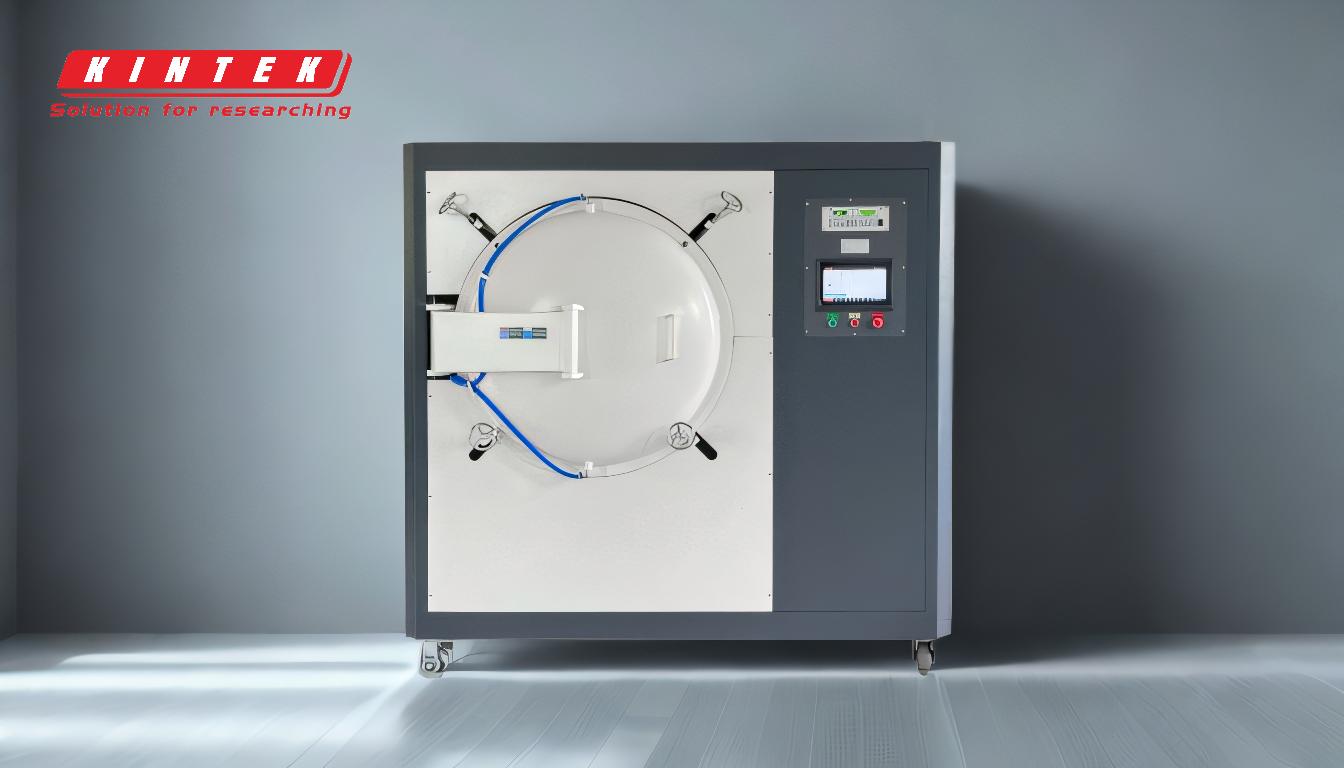
-
Desafíos del control de microestructuras:
- La sinterización en fase líquida puede provocar un crecimiento y un engrosamiento desiguales de los granos, lo que da lugar a una microestructura menos uniforme.
- La presencia de una fase líquida puede provocar una densificación localizada, con las consiguientes variaciones de densidad y propiedades mecánicas en toda la pieza sinterizada.
-
Anisotropía en las propiedades:
- El flujo de la fase líquida durante la sinterización puede provocar la alineación direccional de los granos, lo que da lugar a una anisotropía en las propiedades mecánicas, térmicas y eléctricas.
- Esta anisotropía puede ser problemática para aplicaciones que requieren un comportamiento isótropo.
-
Limitaciones en la selección de materiales:
- La sinterización en fase líquida requiere la formación de una fase líquida compatible, lo que limita la gama de materiales que pueden sinterizarse eficazmente con este método.
- La necesidad de aditivos específicos para formar la fase líquida puede complicar la formulación del material y aumentar los costes.
-
Tensiones residuales y defectos:
- El proceso de enfriamiento tras la sinterización en fase líquida puede inducir tensiones residuales debidas a la contracción diferencial entre las fases sólida y líquida.
- Estas tensiones pueden provocar grietas, alabeos u otros defectos en el producto final.
-
Alto consumo de energía:
- La sinterización en fase líquida suele requerir altas temperaturas para lograr la formación de la fase líquida necesaria, lo que conlleva un mayor consumo de energía.
- Esto contribuye a aumentar los costes operativos y el impacto medioambiental.
-
Crecimiento y engrosamiento del grano:
- La fase líquida puede acelerar el crecimiento del grano, lo que puede degradar las propiedades mecánicas del material sinterizado.
- El control del tamaño de grano se convierte en un reto, que requiere un control preciso de los parámetros de sinterización.
-
Coste y complejidad:
- El equipo y el control del proceso necesarios para la sinterización en fase líquida son más complejos y caros que para la sinterización en estado sólido.
- La necesidad de moldes especializados, aditivos y hornos de alta temperatura aumenta el coste total.
-
Contracción y control dimensional:
- Las piezas sinterizadas con una fase líquida suelen experimentar una mayor contracción, que debe tenerse en cuenta durante el proceso de diseño y producción.
- Esto puede complicar la fabricación de piezas con tolerancias dimensionales ajustadas.
-
Preocupaciones medioambientales y de seguridad:
- Las altas temperaturas y el uso potencial de materiales peligrosos en la sinterización en fase líquida pueden plantear riesgos para la seguridad y problemas medioambientales.
- Para mitigar estos problemas es necesario manipular y eliminar adecuadamente los materiales y subproductos.
Al conocer estas desventajas, los fabricantes pueden evaluar mejor la idoneidad del sinterizado en fase líquida para sus aplicaciones específicas y tomar medidas para mitigar los posibles problemas mediante un diseño cuidadoso del proceso y la selección de materiales.
Tabla resumen:
Desventaja | Detalles clave |
---|---|
Control de la microestructura | Crecimiento desigual del grano, densificación localizada y propiedades no uniformes. |
Anisotropía en las propiedades | Alineación direccional del grano que conduce a un comportamiento mecánico/térmico incoherente. |
Limitaciones en la selección de materiales | Requiere una fase líquida compatible, lo que limita las opciones de materiales y aumenta los costes. |
Tensiones residuales y defectos | La contracción diferencial provoca grietas, alabeos u otros defectos. |
Alto consumo de energía | Las altas temperaturas aumentan el consumo de energía y los costes operativos. |
Crecimiento y endurecimiento del grano | El crecimiento acelerado del grano degrada las propiedades mecánicas. |
Coste y complejidad | Los equipos y aditivos especializados aumentan los costes y la complejidad del proceso. |
Contracción y control dimensional | Una mayor contracción complica la fabricación con tolerancias ajustadas. |
Preocupaciones medioambientales y de seguridad | Las altas temperaturas y los materiales peligrosos plantean riesgos y problemas medioambientales. |
¿Necesita ayuda para optimizar su proceso de sinterización? Póngase en contacto con nuestros expertos para obtener soluciones a medida.