La pulverización catódica es una técnica de deposición de películas finas muy utilizada y conocida por su gran pureza, control preciso y uniformidad.Sin embargo, presenta varios inconvenientes que pueden afectar a su eficacia, coste y adecuación a la aplicación.Entre los principales inconvenientes se encuentran la menor velocidad de deposición, los elevados costes operativos y de equipos, la sensibilidad al calor, los riesgos de contaminación de la película y las dificultades para conseguir un espesor uniforme de la película.Además, el sputtering se enfrenta a limitaciones en la selección de materiales, el control del proceso y la integración con otras técnicas de fabricación.Estos factores lo hacen menos idóneo para determinadas aplicaciones, en particular las que requieren un alto rendimiento, baja contaminación o combinaciones complejas de materiales.
Explicación de los puntos clave:
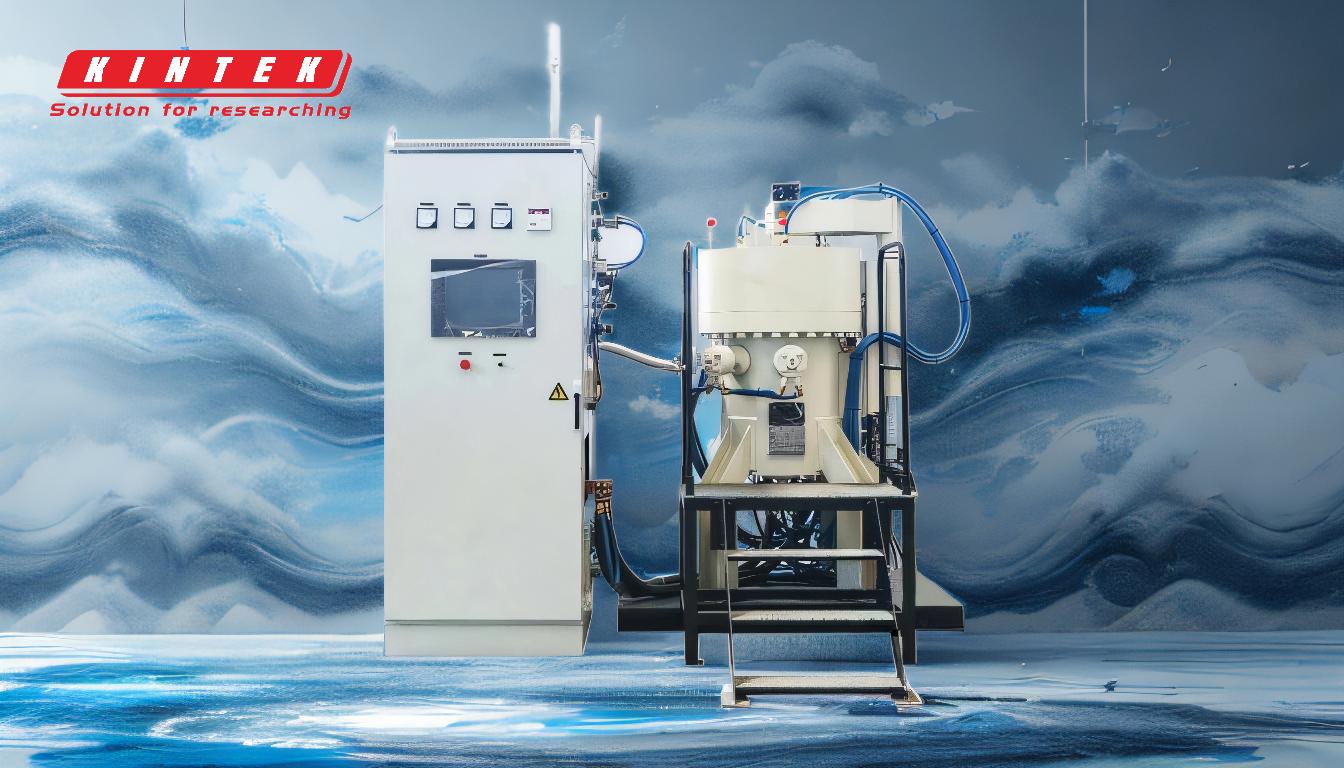
-
Tasas de deposición más lentas
- La velocidad de deposición del sputtering suele ser menor que la de métodos como la evaporación térmica.Esto se debe a la naturaleza física del proceso, en el que los átomos son expulsados de un material objetivo y depositados sobre un sustrato.La lentitud del proceso puede limitar el rendimiento, lo que lo hace menos adecuado para la producción de grandes volúmenes.
-
Costes operativos y de equipo elevados
- Los sistemas de pulverización catódica son caros de adquirir y mantener.La necesidad de sistemas de vacío de alta calidad, fuentes de alimentación de RF o CC y sistemas de refrigeración aumenta el coste total.Además, los cátodos para sputtering suelen ser costosos y el uso de materiales puede ser ineficiente, lo que incrementa aún más los gastos.
-
Sensibilidad al calor y requisitos de refrigeración
- Una parte significativa de la energía utilizada en el sputtering se convierte en calor, que debe eliminarse eficazmente para evitar daños en el sustrato o el blanco.Los sistemas de refrigeración son necesarios, pero pueden reducir los índices de producción y aumentar el consumo de energía, lo que incrementa los costes operativos.
-
Riesgos de contaminación de la película
- El sputtering puede introducir contaminación en la película depositada.Las impurezas del material objetivo o los contaminantes gaseosos del plasma pueden activarse e incorporarse a la película.Esto es particularmente problemático en el sputtering reactivo, donde es necesario un control cuidadoso de la composición del gas para evitar el envenenamiento del blanco.
-
Dificultades para conseguir un espesor de película uniforme
- La distribución del flujo de deposición en el sputtering no suele ser uniforme, especialmente en el caso de sustratos o blancos de gran tamaño.Para conseguir un espesor uniforme pueden ser necesarios dispositivos móviles o complejas configuraciones, lo que añade complejidad y coste al proceso.
-
Limitaciones en la selección de materiales
- El sputtering está limitado por las temperaturas de fusión y las propiedades de los materiales objetivo.Algunos materiales pueden no ser adecuados para el sputtering debido a sus bajos puntos de fusión u otras características físicas, lo que limita la gama de revestimientos que pueden producirse.
-
Dificultad de combinación con procesos de despegado
- El sputtering es difícil de integrar con los procesos lift-off utilizados en la estructuración de películas.El transporte difuso de los átomos pulverizados hace imposible el ensombrecimiento total, lo que provoca contaminación y dificultades para conseguir patrones precisos.
-
Retos del control activo
- En comparación con otros métodos de deposición, como la deposición por láser pulsado, el sputtering ofrece menos control activo sobre el crecimiento capa por capa.Esto puede limitar su uso en aplicaciones que requieren un control preciso a nivel atómico.
-
Altas presiones de funcionamiento y problemas de sellado
- Los procesos de sputtering tradicionales funcionan a presiones relativamente altas, lo que puede provocar la permeación de las juntas de elastómero y otros problemas del sistema de vacío.Estos problemas pueden afectar a la calidad y eficacia del proceso de deposición.
-
Desigualdad de la densidad del plasma
- En el caso de cátodos rectangulares de gran tamaño (por ejemplo, >1 m), puede resultar difícil conseguir una densidad de plasma uniforme, lo que da lugar a una distribución irregular del grosor de la capa.Esto requiere soluciones de ingeniería adicionales.
-
Ineficiencia energética
- La mayor parte de la energía que incide sobre el blanco se convierte en calor en lugar de utilizarse para la deposición, lo que hace que el proceso sea menos eficiente energéticamente en comparación con otras técnicas.
-
Complicaciones del sputtering reactivo
- En el sputtering reactivo, el control preciso de la composición del gas es fundamental para evitar el envenenamiento del blanco, en el que la superficie del blanco se altera químicamente, lo que reduce la eficacia de la deposición y la calidad de la película.
Al conocer estas desventajas, los compradores de equipos y consumibles pueden decidir con conocimiento de causa si el sputtering es la técnica adecuada para sus aplicaciones específicas, teniendo en cuenta factores como el coste, el rendimiento y los requisitos de material.
Tabla resumen:
Desventaja | Detalles clave |
---|---|
Velocidades de deposición más lentas | Menor rendimiento en comparación con métodos como la evaporación térmica. |
Costes operativos y de equipamiento elevados | Sistemas caros, requisitos de vacío y cátodos para sputtering costosos. |
Sensibilidad al calor | Requiere sistemas de refrigeración, lo que reduce el ritmo de producción y aumenta el consumo de energía. |
Riesgos de contaminación de la película | Las impurezas de los objetivos o del plasma pueden afectar a la calidad de la película. |
Desafíos de la uniformidad del espesor de la película | Flujo de deposición no uniforme, especialmente en sustratos grandes. |
Limitaciones en la selección de materiales | Limitada por las propiedades del material objetivo y los puntos de fusión. |
Integración con procesos Lift-Off | Difícil de combinar con técnicas precisas de estructuración de películas. |
Retos del control activo | Crecimiento capa a capa menos preciso que con otros métodos. |
Altas presiones de funcionamiento | Puede provocar problemas en el sistema de vacío y en el sellado. |
Densidad de plasma irregular | Dificultad para conseguir una densidad de plasma uniforme en cátodos grandes. |
Ineficiencia energética | La mayor parte de la energía se convierte en calor, no en deposición. |
Complicaciones del sputtering reactivo | Requiere un control preciso del gas para evitar el envenenamiento del blanco. |
¿Necesita ayuda para decidir si el sputtering es adecuado para su aplicación? Póngase en contacto con nuestros expertos para un asesoramiento personalizado.