Las tolerancias del sinterizado láser son fundamentales para garantizar la precisión y calidad de las piezas impresas en 3D.El proceso consiste en utilizar un láser para fusionar material en polvo capa por capa, y conseguir tolerancias ajustadas es esencial para las aplicaciones que requieren una gran precisión.Según la referencia proporcionada, las técnicas de sinterización adaptadas pueden lograr tolerancias de una micra en cuanto a linealidad y concentricidad.Este nivel de precisión puede alcanzarse mediante un control avanzado de los parámetros del láser, las propiedades del material y la optimización del proceso.
Explicación de los puntos clave:
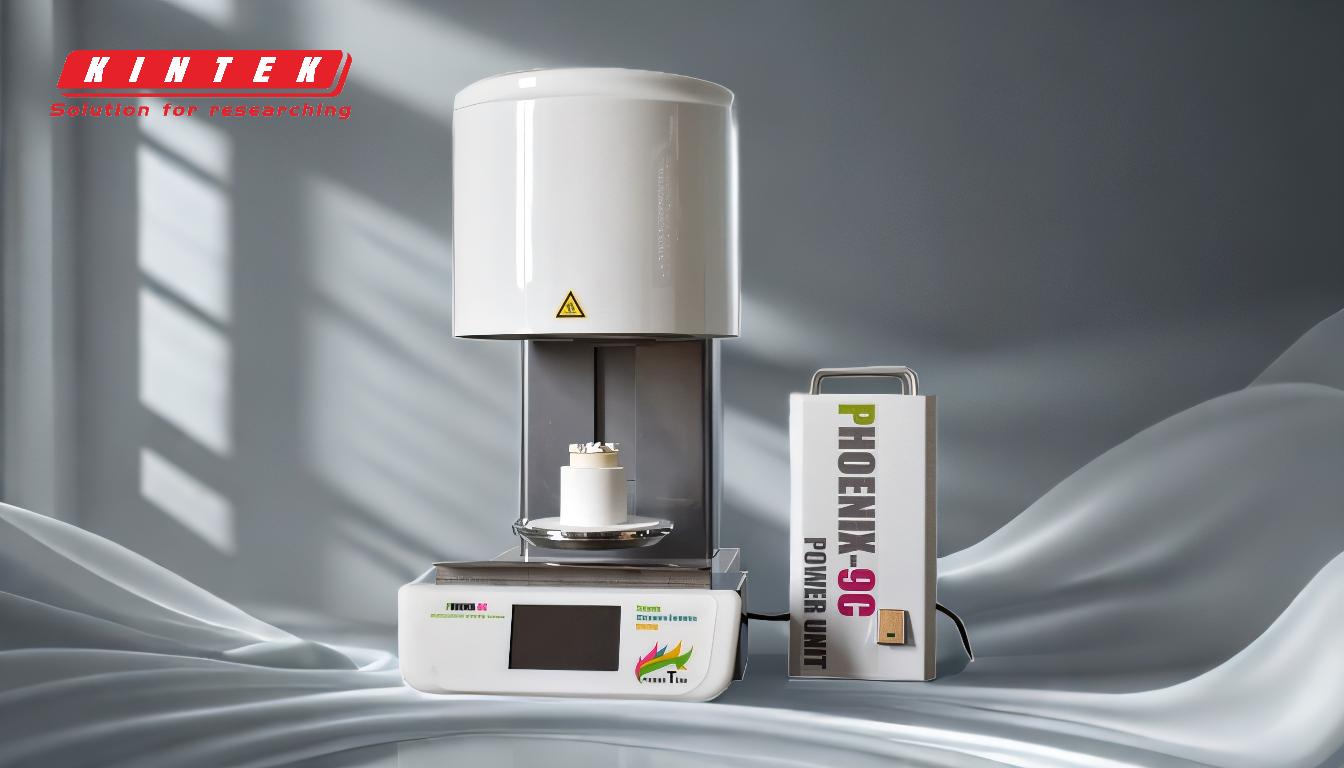
-
Definición de tolerancias en el sinterizado láser:
- Las tolerancias se refieren a la desviación permitida de una dimensión o geometría especificada en una pieza fabricada.
- En el sinterizado láser, las tolerancias se ven influidas por factores como la potencia del láser, la velocidad de escaneado, el grosor de la capa y las propiedades del material.
-
Lograr tolerancias dentro de una micra:
- La referencia afirma que las técnicas de sinterización adaptadas pueden garantizar la linealidad y la concentricidad dentro de una micra.
-
Este nivel de precisión se consigue mediante
- Control láser avanzado:Control preciso de la potencia del láser y de la velocidad de escaneado para minimizar las variaciones.
- Optimización del material:Utilización de materiales con una granulometría y una distribución homogéneas para garantizar una sinterización uniforme.
- Supervisión del proceso:Supervisión y ajuste en tiempo real del proceso de sinterización para mantener tolerancias estrictas.
-
Factores que influyen en las tolerancias:
- Parámetros láser:La intensidad, el enfoque y el patrón de barrido del láser influyen significativamente en la precisión de la pieza sinterizada.
- Espesor de capa:Las capas más finas suelen permitir una mayor precisión, pero pueden aumentar el tiempo de fabricación.
- Propiedades del material:La conductividad térmica, el punto de fusión y el tamaño de las partículas del material afectan a su sinterización y a la precisión dimensional final.
- Calibrado de la máquina:La calibración periódica de la máquina de sinterizado láser es esencial para mantener un rendimiento constante.
-
Aplicaciones que requieren tolerancias estrictas:
- Productos sanitarios:Componentes como implantes y herramientas quirúrgicas requieren una gran precisión para garantizar un ajuste y un funcionamiento adecuados.
- Aeroespacial:Las piezas de aviones y naves espaciales deben cumplir estrictas tolerancias para garantizar la seguridad y el rendimiento.
- Microelectrónica:Los componentes pequeños e intrincados de los dispositivos electrónicos suelen requerir tolerancias de unas pocas micras.
-
Retos para mantener las tolerancias:
- Distorsión térmica:El calor generado durante la sinterización puede hacer que las piezas se alabeen o deformen, afectando a la precisión dimensional.
- Contracción del material:Algunos materiales se encogen al enfriarse, lo que debe tenerse en cuenta en el diseño y el proceso de sinterización.
- Acabado superficial:Conseguir un acabado superficial liso manteniendo unas tolerancias ajustadas puede ser todo un reto.
-
Estrategias para mejorar las tolerancias:
- Optimización de procesos:Ajuste de los parámetros láser y las estrategias de sinterización para minimizar las desviaciones.
- Postprocesado:Pueden utilizarse técnicas como el mecanizado o el pulido para conseguir las tolerancias y el acabado superficial deseados.
- Diseño para la fabricación aditiva (DfAM):Diseño de piezas teniendo en cuenta las tolerancias de sinterización, como la incorporación de márgenes para la contracción o la distorsión.
En conclusión, el sinterizado por láser puede lograr tolerancias de hasta una micra de linealidad y concentricidad mediante técnicas avanzadas y un control minucioso de los parámetros del proceso.Sin embargo, mantener tolerancias tan ajustadas requiere una combinación de materiales optimizados, un control preciso del láser y una supervisión minuciosa del proceso.Estas tolerancias son esenciales para aplicaciones de alta precisión en industrias como la médica, la aeroespacial y la microelectrónica.
Cuadro sinóptico:
Aspecto clave | Detalles |
---|---|
Definición de tolerancia | Desviación admisible de las dimensiones especificadas en piezas sinterizadas por láser. |
Precisión de 1 micra | Control láser avanzado, optimización de materiales y supervisión del proceso en tiempo real. |
Factores que influyen | Los parámetros del láser, el grosor de la capa, las propiedades del material y la calibración de la máquina. |
Aplicaciones | Dispositivos médicos, aeroespacial y microelectrónica. |
Desafíos | Distorsión térmica, contracción del material y acabado superficial. |
Estrategias de mejora | Optimización de procesos, posprocesamiento y diseño para fabricación aditiva (DfAM). |
¿Necesita sinterizado láser de precisión para su proyecto? Póngase en contacto con nuestros expertos para obtener más información.