El calentamiento por inducción utiliza corriente alterna (CA) para generar calor en materiales conductores mediante inducción electromagnética.La frecuencia de la corriente alterna desempeña un papel fundamental a la hora de determinar la profundidad de calentamiento, la eficacia y la idoneidad para aplicaciones específicas.Las frecuencias de calentamiento por inducción se clasifican en tres rangos: baja frecuencia (50 Hz a 1 kHz), frecuencia intermedia (500 Hz a 10 kHz) y alta frecuencia (100 kHz a 500 kHz).La elección de la frecuencia depende de factores como las propiedades del material, el grosor, la profundidad de calentamiento deseada y los requisitos de la aplicación.Por ejemplo, las frecuencias más bajas son adecuadas para calentar materiales más gruesos, mientras que las frecuencias más altas son ideales para materiales más finos o el calentamiento de superficies.Comprender estas gamas de frecuencias y sus aplicaciones es esencial para diseñar sistemas eficientes de calentamiento por inducción.
Explicación de los puntos clave:
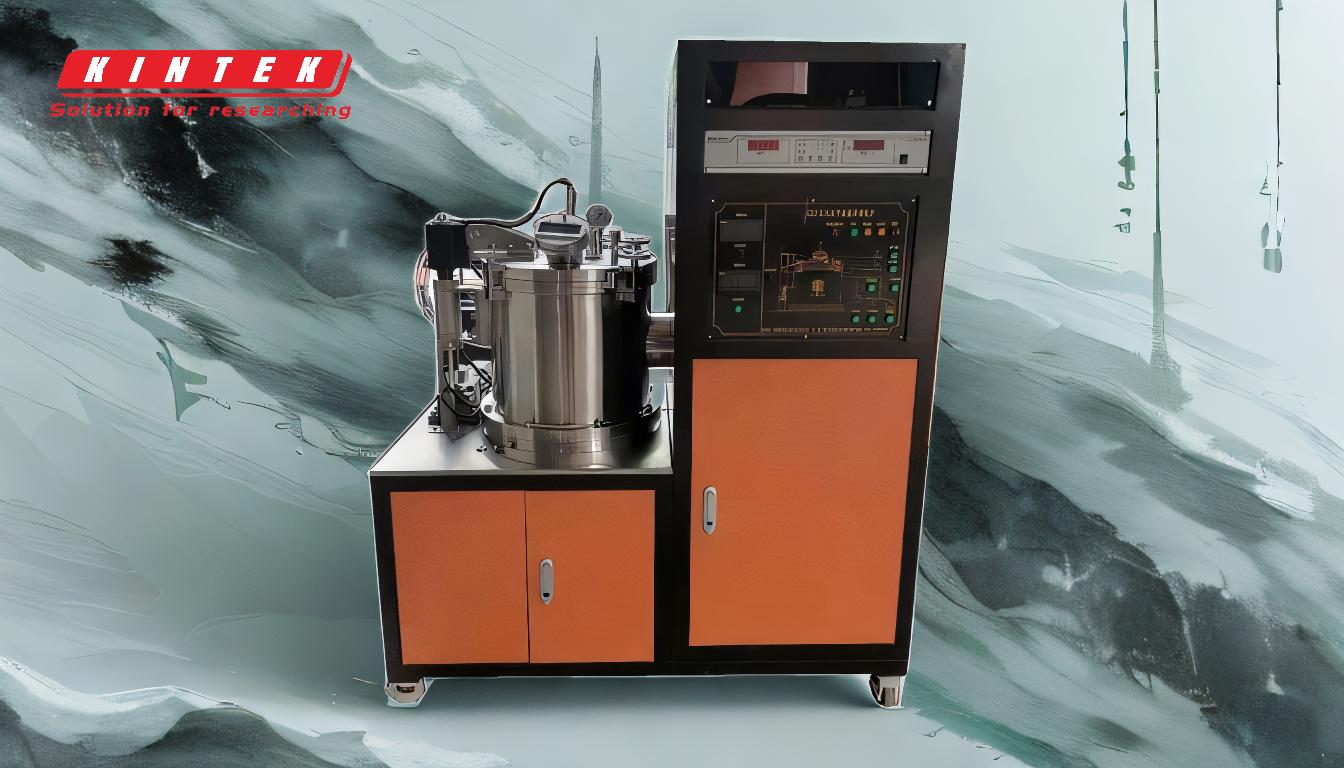
-
Rangos de frecuencia en el calentamiento por inducción:
-
Baja frecuencia (50 Hz a 1 kHz):
- Normalmente se utiliza para calentar materiales grandes o gruesos.
- Proporciona una penetración del calor más profunda, lo que la hace adecuada para aplicaciones como la forja o la fusión de grandes componentes metálicos.
-
Frecuencia intermedia (500 Hz a 10 kHz):
- Comúnmente utilizadas para piezas de tamaño medio y aplicaciones que requieren una profundidad de calentamiento moderada.
- Ideal para procesos como temple, recocido y soldadura fuerte.
-
Alta frecuencia (100 kHz a 500 kHz):
- La más adecuada para materiales finos o aplicaciones de calentamiento de superficies.
- Se utiliza en procesos como el endurecimiento superficial, la soldadura y el calentamiento de componentes pequeños.
-
Baja frecuencia (50 Hz a 1 kHz):
-
Factores que influyen en la selección de la frecuencia:
-
Propiedades de los materiales:
- Los materiales conductores y magnéticos se calientan más eficazmente por inducción.
- Los materiales de mayor resistividad se calientan más rápidamente, mientras que los de menor resistividad pueden requerir frecuencias más altas.
-
Grosor del material:
- Los materiales más gruesos requieren frecuencias más bajas para una penetración más profunda del calor.
- Los materiales más finos o las aplicaciones de calentamiento superficial se benefician de frecuencias más altas.
-
Profundidad de calentamiento:
- Las frecuencias más altas dan lugar a profundidades de calentamiento menores, mientras que las frecuencias más bajas penetran más profundamente en el material.
-
Requisitos de aplicación:
- El aumento de temperatura deseado, la velocidad de calentamiento y el efecto de agitación (en aplicaciones de fusión) influyen en la selección de la frecuencia.
-
Propiedades de los materiales:
-
Frecuencia y eficacia de calentamiento:
- La frecuencia de la corriente alterna controla la velocidad a la que cambia el campo magnético, lo que afecta directamente a la corriente inducida en la pieza.
- Las frecuencias más altas generan más calor en menos tiempo, pero con menor penetración, por lo que son energéticamente eficientes para el calentamiento superficial.
- Las frecuencias más bajas son más eficaces para el calentamiento masivo de materiales más gruesos, ya que proporcionan una distribución uniforme del calor.
-
Aplicaciones prácticas de los rangos de frecuencia:
- Baja Frecuencia:Se utiliza en aplicaciones industriales a gran escala como la fusión de metales, la forja y el calentamiento de componentes pesados.
- Frecuencia intermedia:Se aplica en procesos que requieren un control preciso de la temperatura, como el temple, el recocido y la soldadura fuerte de piezas de tamaño medio.
- Alta frecuencia:Utilizado para tratamientos superficiales, soldadura y calentamiento de componentes pequeños o delgados donde se requiere un calentamiento rápido.
-
Consideraciones sobre el diseño de sistemas de calentamiento por inducción:
- El diseño de la bobina inductora y la capacidad de la fuente de alimentación deben estar en consonancia con la frecuencia elegida para garantizar una generación de calor eficaz.
- El calor específico, la masa y el aumento de temperatura requerido del material influyen en los requisitos de la fuente de alimentación.
- La pérdida de calor por conducción, convección y radiación debe tenerse en cuenta en el diseño del sistema.
Seleccionando cuidadosamente la gama de frecuencias adecuada en función de las propiedades del material, el grosor y los requisitos de la aplicación, los sistemas de calentamiento por inducción pueden alcanzar una eficiencia y un rendimiento óptimos.Comprender estos principios es crucial para que los compradores de equipos y consumibles tomen decisiones informadas a la hora de seleccionar soluciones de calentamiento por inducción.
Tabla resumen:
Gama de frecuencias | Aplicaciones | Profundidad de calentamiento | Idoneidad del material |
---|---|---|---|
Baja (50 Hz - 1 kHz) | Forja, fusión de metales grandes | En profundidad | Materiales gruesos |
Intermedio (500 Hz - 10 kHz) | Endurecimiento, recocido, soldadura fuerte | Moderado | Piezas medianas |
Alta (100 kHz - 500 kHz) | Endurecimiento de superficies, soldadura, componentes pequeños | Poco profundo | Materiales finos |
¿Necesita ayuda para elegir la frecuencia de calentamiento por inducción adecuada para su aplicación? Póngase en contacto con nuestros expertos para obtener soluciones personalizadas.