La sinterización en pulvimetalurgia es un proceso crítico de tratamiento térmico que transforma los polvos metálicos comprimidos en componentes fuertes y cohesivos. Consiste en calentar el polvo compactado a una temperatura justo por debajo de su punto de fusión, lo que permite que las partículas se unan mediante difusión y crecimiento del grano. Este proceso aumenta la resistencia, densidad e integridad estructural del material, al tiempo que mantiene su forma y propiedades. La sinterización se utiliza mucho en sectores como la automoción y la fabricación de herramientas para producir piezas complejas de alto rendimiento, como engranajes, árboles de levas y herramientas de corte.
Explicación de los puntos clave:
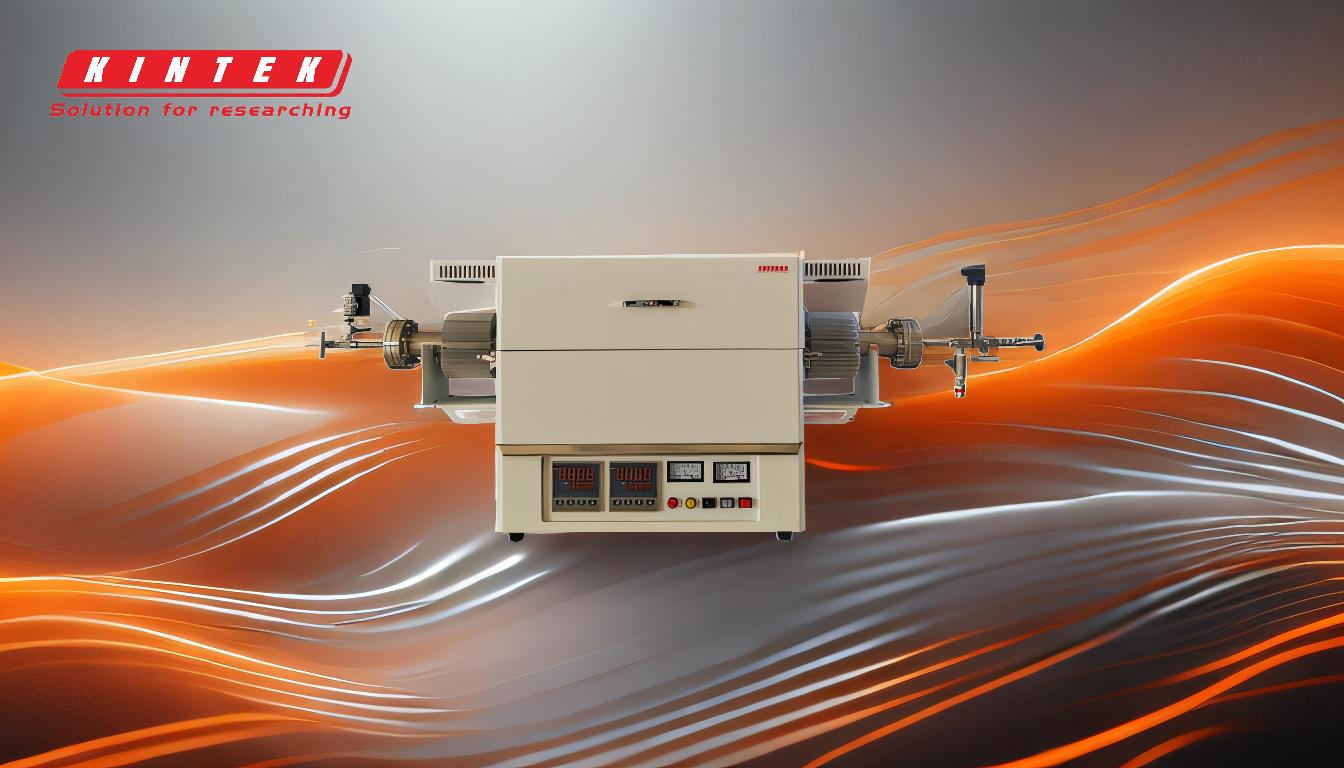
-
Definición y finalidad de la sinterización:
- La sinterización es un proceso de tratamiento térmico en pulvimetalurgia en el que polvos metálicos comprimidos se calientan a una temperatura inferior a su punto de fusión.
- El objetivo principal es unir las partículas metálicas, creando una estructura fuerte y cohesiva al tiempo que se conservan la forma y las propiedades deseadas del material.
-
Control de la temperatura:
- La temperatura de sinterización se controla cuidadosamente para que se mantenga por debajo del punto de fusión del metal primario o de la aleación.
- De este modo se evita la fusión y se garantiza que las partículas se adhieran mediante difusión en estado sólido y no mediante fusión en fase líquida.
-
Mecanismo de unión:
- Durante la sinterización, las partículas metálicas sufren difusión, en la que los átomos migran a través de los límites de las partículas.
- El crecimiento de los granos se produce cuando las partículas más pequeñas se fusionan con las más grandes, lo que reduce la porosidad y aumenta la densidad.
- Este mecanismo de unión refuerza el material y mejora sus propiedades mecánicas.
-
Etapas de la sinterización:
- Fase inicial: Las partículas comienzan a unirse en los puntos de contacto, formando cuellos entre ellas.
- Etapa intermedia: La porosidad disminuye a medida que los cuellos crecen y el material se densifica.
- Fase final: Predomina el crecimiento del grano y el material alcanza su densidad y resistencia finales.
-
Ventajas de la sinterización:
- Mayor resistencia y dureza: La unión de las partículas mejora significativamente las propiedades mecánicas del material.
- Formas complejas: El sinterizado permite fabricar componentes intrincados y precisos que son difíciles de conseguir con otros métodos.
- Eficiencia material: Minimiza los residuos mediante el uso eficiente de los polvos metálicos.
-
Aplicaciones en la industria:
- Automoción: Se utiliza para fabricar engranajes, árboles de levas, asientos de válvulas y otros componentes críticos.
- Fabricación de herramientas: Produce herramientas de corte, brocas y otras piezas resistentes al desgaste.
- Filtros y rodamientos: Crea estructuras porosas para filtros y cojinetes autolubricantes.
-
Comparación con otros procesos:
- A diferencia de la fusión, la sinterización conserva las propiedades originales del material, como la estructura del grano y la composición de la aleación.
- Es más rentable y eficiente energéticamente que la fundición o el mecanizado tradicionales para producir piezas complejas.
-
Factores que influyen en la sinterización:
- Temperatura y tiempo: Las temperaturas más altas y los tiempos de sinterización más largos suelen mejorar la adherencia, pero deben equilibrarse para evitar un crecimiento excesivo del grano.
- Características del polvo: El tamaño, la forma y la distribución de las partículas afectan al proceso de sinterización y a las propiedades finales.
- Atmósfera: Las atmósferas controladas (por ejemplo, hidrógeno, nitrógeno o vacío) evitan la oxidación y garantizan resultados uniformes.
-
Procesos posteriores a la sinterización:
- Tras la sinterización, las piezas pueden someterse a tratamientos adicionales como el tratamiento térmico, el mecanizado o el acabado superficial para conseguir las propiedades y tolerancias deseadas.
-
Ventajas para los fabricantes:
- Rentable: Reduce el desperdicio de material y el consumo de energía en comparación con los métodos de fabricación tradicionales.
- Versatilidad: Compatible con una amplia gama de metales y aleaciones, incluidos el hierro, el cobre, el titanio y las aleaciones a base de níquel.
- Escalabilidad: Adecuada tanto para la creación de prototipos a pequeña escala como para la producción a gran escala.
Al comprender el proceso de sinterización, los fabricantes pueden optimizar sus métodos de producción para crear componentes duraderos y de alta calidad adaptados a aplicaciones específicas. Este proceso, piedra angular de la pulvimetalurgia moderna, permite fabricar piezas complejas con un rendimiento y una eficiencia superiores.
Cuadro recapitulativo:
Aspecto | Detalles |
---|---|
Definición | Proceso de tratamiento térmico que une polvos metálicos por debajo del punto de fusión. |
Mecanismo clave | Difusión en estado sólido y crecimiento de grano. |
Etapas | Inicial (formación del cuello), Intermedio (densificación), Final (crecimiento del grano). |
Beneficios | Mayor resistencia, formas complejas, eficiencia del material. |
Aplicaciones | Piezas de automóvil, herramientas de corte, filtros, rodamientos. |
Factores que influyen | Temperatura, tiempo, características del polvo, atmósfera controlada. |
Ventajas | Rentable, versátil y escalable. |
Optimice su producción con el sinterizado contacte hoy mismo con nuestros expertos para saber más