La mejor frecuencia para el calentamiento por inducción depende de varios factores, como el tipo de material, el tamaño, el grosor y la profundidad de calentamiento deseada.El calentamiento por inducción de frecuencia intermedia oscila entre 500 Hz y 10.000 Hz, mientras que el calentamiento por inducción de alta frecuencia funciona entre 100 kHz y 500 kHz.Las frecuencias más altas son adecuadas para materiales más pequeños y delgados, ya que proporcionan profundidades de calentamiento poco profundas, mientras que las frecuencias más bajas son mejores para materiales más grandes y gruesos, ya que ofrecen una penetración del calor más profunda.La selección de la frecuencia también debe tener en cuenta las propiedades del material de la pieza, los requisitos del proceso y las limitaciones de costes.En última instancia, la frecuencia óptima equilibra la eficacia del calentamiento, las características del material y las necesidades específicas de la aplicación.
Explicación de los puntos clave:
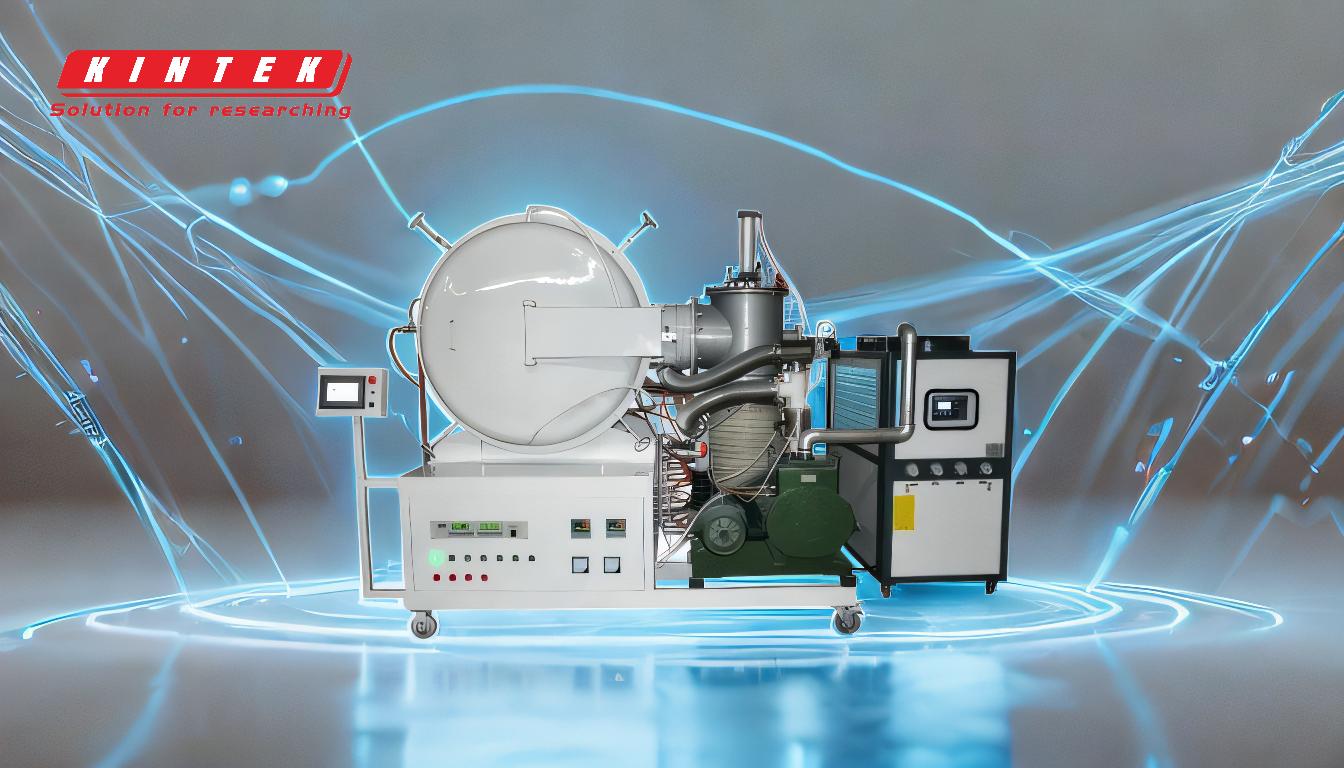
-
Rangos de frecuencia para el calentamiento por inducción:
- Frecuencia intermedia:500 Hz a 10.000 Hz.
- Alta frecuencia:100 kHz a 500 kHz.
- Estos rangos vienen determinados por el tamaño, el grosor y los requisitos de profundidad de calentamiento del material.
-
Impacto de la frecuencia en la profundidad de calentamiento:
- Las frecuencias más altas (por ejemplo, de 100 kHz a 500 kHz) dan lugar a profundidades de calentamiento menos profundas, lo que las hace ideales para materiales pequeños y delgados.
- Las frecuencias más bajas (por ejemplo, de 500 Hz a 10.000 Hz) proporcionan una penetración del calor más profunda, por lo que son adecuadas para materiales más grandes y gruesos.
-
Propiedades del material y selección de frecuencias:
- Tipo de material:En el calentamiento por inducción se suelen utilizar metales y materiales conductores.
- Resistividad:Los materiales con mayor resistividad se calientan más rápidamente.
- Calor específico y masa:Estos factores influyen en la capacidad de alimentación necesaria para el calentamiento.
-
Características de la pieza:
- Tamaño y grosor:Los materiales más pequeños y delgados se calientan más rápido con frecuencias más altas.
- Profundidad de calentamiento deseada:La frecuencia debe coincidir con la profundidad requerida de generación de calor en el material.
-
Requisitos del proceso:
- La selección de la frecuencia debe estar en consonancia con el aumento de temperatura, la pérdida de calor y la eficacia deseados.
- Por ejemplo, las aplicaciones de fusión pueden requerir frecuencias específicas para lograr el efecto de agitación y la eficacia de fusión deseados.
-
Coste y consideraciones prácticas:
- La selección de la banda de frecuencia debe equilibrar el coste de compra del cliente, el material de la pieza de trabajo y los requisitos del proceso.
- Los equipos de alta frecuencia de baja potencia y los equipos de ultraaudio de alta potencia pueden ofrecer efectos de calentamiento similares para determinadas piezas de trabajo, dependiendo de la aplicación.
-
Diseño del inductor y de la fuente de alimentación:
- El diseño de la bobina inductora y la capacidad de la fuente de alimentación deben tener en cuenta el calor específico del material, su masa y el aumento de temperatura requerido.
- La frecuencia de la corriente alterna en la bobina controla la frecuencia de la corriente inducida en la pieza, lo que afecta a la profundidad de calentamiento.
-
Eficacia del calentamiento por inducción:
- La eficacia depende de las características de la pieza, el diseño del inductor, la capacidad de la fuente de alimentación y el cambio de temperatura requerido.
- A menudo se utiliza una mayor potencia de calentamiento por inducción para adaptarse a una amplia gama de variaciones de temperatura.
-
Personalización de la frecuencia:
- La frecuencia de trabajo de las máquinas de fusión por inducción de frecuencia media puede ajustarse cambiando la bobina y el condensador de compensación en función de factores como el material de fusión, la cantidad y el efecto de agitación deseado.
-
Ejemplo práctico:
- Para una chapa fina que requiera un calentamiento superficial, una gama de frecuencias altas (100 kHz a 500 kHz) sería óptima.
- Para un bloque metálico grueso que requiera una penetración profunda del calor, sería más adecuada una gama de frecuencia intermedia (500 Hz a 10.000 Hz).
Teniendo en cuenta estos factores, se puede determinar la mejor frecuencia para el calentamiento por inducción a fin de lograr una eficacia de calentamiento óptima y cumplir los requisitos específicos de la aplicación.
Tabla resumen:
Factor | Detalles |
---|---|
Rangos de frecuencia | Intermedio:500 Hz a 10.000 Hz; Alta: 100 kHz a 500 kHz |
Profundidad de calentamiento | Frecuencias más altas = poca profundidad; Frecuencias más bajas = penetración más profunda |
Propiedades de los materiales | Los metales, la resistividad, el calor específico y la masa influyen en la selección de la frecuencia |
Características de la pieza | El tamaño, el grosor y la profundidad de calentamiento deseada determinan la frecuencia óptima |
Requisitos del proceso | Alinear la frecuencia con el aumento de temperatura, la pérdida de calor y las necesidades de eficiencia |
Consideraciones sobre costes | Equilibre la selección de frecuencia con el coste y los requisitos específicos de la aplicación |
¿Necesita ayuda para seleccionar la frecuencia adecuada para su proceso de calentamiento por inducción? Póngase en contacto hoy mismo con nuestros expertos para obtener soluciones a medida.