El revestimiento neutro de un horno de inducción es un componente crítico diseñado para proteger la estructura del horno y mejorar su rendimiento.Está fabricado con materiales refractarios capaces de soportar temperaturas extremas y resistir las reacciones químicas con los metales fundidos.Este revestimiento sirve de barrera entre el metal fundido y la estructura exterior del horno, como la bobina de inducción, garantizando la longevidad y eficacia del horno.También aísla el metal fundido, evitando la contaminación y manteniendo la integridad del metal fundido.El revestimiento neutro es esencial para el funcionamiento seguro y eficaz de los hornos de inducción, por lo que es una consideración clave para los compradores de equipos y consumibles.
Explicación de los puntos clave:
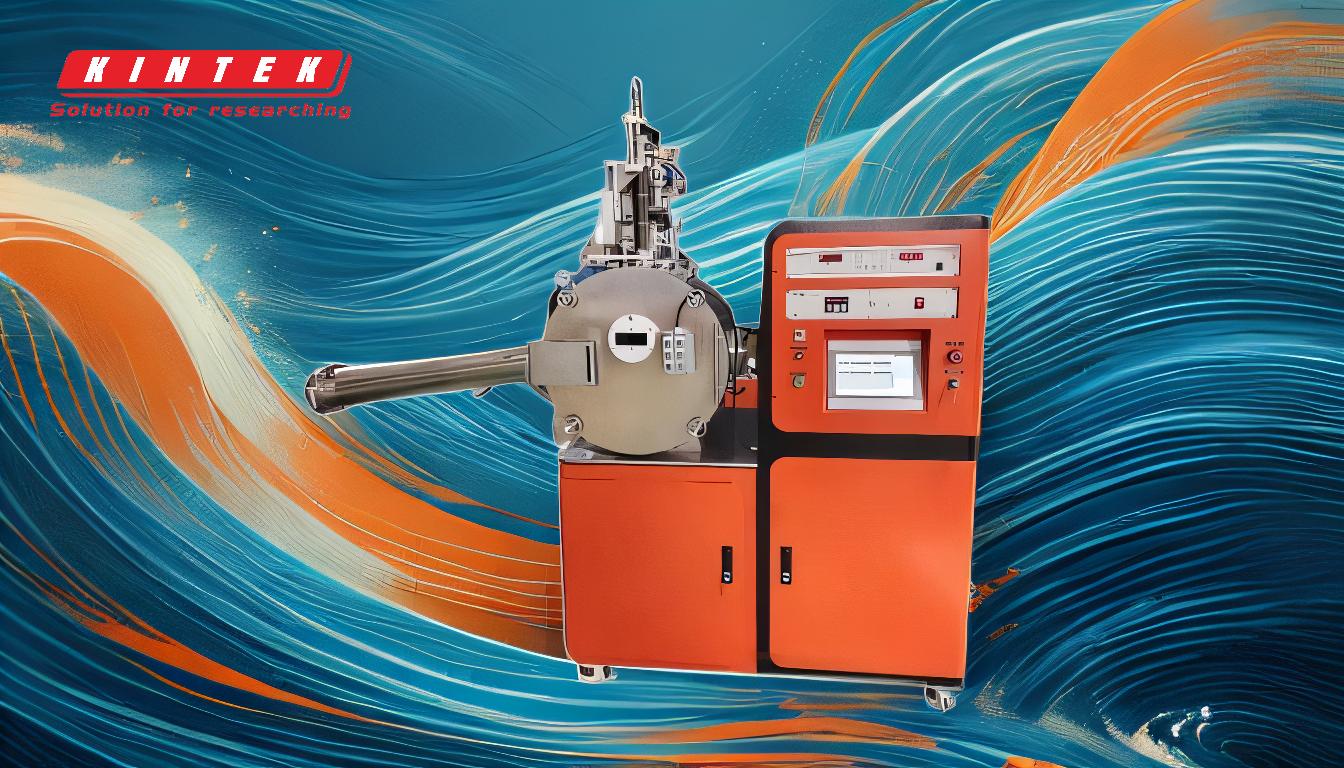
-
Definición y finalidad del revestimiento neutro:
- El revestimiento neutro es una capa protectora en el interior del horno de inducción, fabricada con materiales refractarios.
- Su función principal es contener el metal fundido, aislarlo de la estructura exterior del horno y proteger el cuerpo del horno durante su funcionamiento.
- Garantiza que el horno funcione de forma eficaz y segura al evitar reacciones químicas y daños térmicos.
-
Materiales utilizados en el revestimiento neutro:
- Los materiales refractarios se eligen por su capacidad para soportar altas temperaturas y resistir las reacciones químicas con los metales fundidos.
- Los materiales más comunes son la alúmina, la sílice y la magnesia, que se seleccionan en función del tipo de metal fundido y de las condiciones de funcionamiento del horno.
-
Función de protección de la estructura del horno:
- El revestimiento actúa como barrera entre el metal fundido y la bobina de inducción, evitando el contacto directo y posibles daños.
- También protege el cuerpo del horno del estrés térmico y el desgaste mecánico, alargando la vida útil del horno.
-
Importancia en el mantenimiento de la integridad del metal:
- Al aislar el metal fundido, el revestimiento neutro evita la contaminación de elementos externos, garantizando la pureza y calidad del metal fundido.
- Esto es especialmente importante en aplicaciones que requieren composiciones de aleación precisas, como en las industrias aeroespacial y del automóvil.
-
Impacto en el rendimiento del horno:
- Un revestimiento neutro en buen estado garantiza una transferencia de calor eficaz y una fusión uniforme de la carga metálica.
- Minimiza la pérdida de calor y reduce el consumo de energía, contribuyendo a la rentabilidad global del funcionamiento del horno.
-
Consideraciones para los compradores:
- Al seleccionar un revestimiento neutro, los compradores deben tener en cuenta el tipo de metal que se va a fundir, la temperatura de funcionamiento y la frecuencia de uso del horno.
- La elección del material refractario debe ajustarse a los requisitos específicos de la aplicación para garantizar un rendimiento y una durabilidad óptimos.
-
Mantenimiento y sustitución:
- La inspección y el mantenimiento periódicos del revestimiento neutro son esenciales para evitar grietas, erosión y otras formas de desgaste.
- La sustitución oportuna del revestimiento es necesaria para evitar el tiempo de inactividad del horno y garantizar un rendimiento constante.
En resumen, el revestimiento neutro de un horno de inducción es un componente vital que garantiza el funcionamiento seguro, eficiente y fiable del horno.Protege la estructura del horno, mantiene la integridad del metal fundido y contribuye al rendimiento general del horno.Para los compradores de equipos y consumibles, comprender el papel y la importancia del revestimiento neutro es crucial para tomar decisiones informadas y optimizar el funcionamiento del horno.
Cuadro sinóptico:
Aspecto clave | Detalles |
---|---|
Finalidad | Protege la estructura del horno, aísla el metal fundido y garantiza un funcionamiento seguro. |
Materiales | Alúmina, sílice y magnesia, elegidos por su resistencia a las altas temperaturas. |
Papel en la protección | Actúa como barrera, evita el estrés térmico y el desgaste mecánico. |
Integridad del metal | Evita la contaminación, garantiza la pureza y la calidad del metal fundido. |
Impacto en el rendimiento | Mejora la transferencia de calor, reduce el consumo de energía y mejora la eficiencia. |
Consideraciones de compra | Adecuar los materiales refractarios al tipo de metal, temperatura y frecuencia de uso. |
Mantenimiento | Inspección periódica y sustitución a tiempo para evitar tiempos de inactividad. |
Asegúrese de que su horno de inducción funciona al máximo rendimiento. póngase en contacto con nuestros expertos para saber más sobre los revestimientos neutros.